Specific Process Knowledge/Lithography/Resist/UVresist: Difference between revisions
Line 484: | Line 484: | ||
|-style="background:WhiteSmoke; color:black" | |-style="background:WhiteSmoke; color:black" | ||
!AZ 5214E | !AZ 5214E | ||
| | | 2024-11-29<br>taran | ||
| 1.5 µm | | 1.5 µm | ||
| Fast | | Fast | ||
| | | 105 mJ/cm<sup>2</sup> | ||
| | | 3 | ||
| 1.75 µm | | 1.75 µm | ||
| Dev: SP60s | | Dev: SP60s |
Revision as of 15:50, 9 December 2024
UV resist comparison table
Comparison of specifications and feature space of UV photoresists.
Resist | AZ 5214E | AZ MiR 701 | AZ nLOF 2020 | AZ 4562 | SU-8 | TI Spray |
---|---|---|---|---|---|---|
Resist tone |
|
Positive | Negative | Positive | Negative |
|
Thickness range | 1.5 - 4.2 µm | 1.5 - 4 µm | 1.5 - 4 µm | 5 - 10 µm | 1 - 200 µm | 0.5 - 5 µm |
Coating tool |
Automatic coaters:
Manual coaters:
|
Automatic coaters:
Manual coaters:
|
Automatic coaters:
Manual coaters:
|
Automatic coaters:
Manual coaters:
|
Manual coaters:
or
|
Spray coater |
Spectral sensitivity | 310 - 420 nm | 310 - 445 nm | 310 - 380 nm | 310 - 445 nm | 300 - 375 nm | 310 - 440 nm |
Exposure tool | Mask aligner or Maskless aligner | |||||
Developer |
|
|
AZ 726 MIF | AZ 726 MIF | mr-DEV 600 (PGMEA) | AZ 726 MIF |
Rinse | DIW | DIW | DIW | DIW | IPA | DIW |
Remover |
|
|
|
Remover 1165 |
Cured SU-8 is practically insoluble Plasma ashing can remove crosslinked SU-8 |
|
Comments |
|
High selectivity for dry etch |
Negative sidewalls for lift-off |
For processes with resist thickness between 6 µm and 25 µm |
|
Spray coater specific resist |
Process flow examples |
Mask aligner:
|
Mask aligner:
|
Mask aligner:
|
Mask aligner:
|
Mask aligner:
|
TI spray resist is an image reversal resist, similar to AZ 5214E. The process flow will be similar to the process flows for 5214, except for the coating step. The exposure dose and development will depend on the specific process. |
Other process flows:
Chip on carrier: A procedure for UV lithography on a chip using automatic coater and developer.
Exposure dose
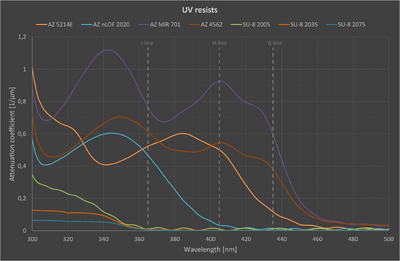
During exposure of the resist, the photoinitiator, or photo-active component, reacts with the exposure light, and starts the reaction which makes the resist develop in the developer.
In a positive resist, it makes the resist become soluble in the developer. In a negative resist, usually assisted by thermal energy in the post-exposure bake (PEB), it makes the resist insoluble in the developer. The amount of light required to fully develop the resist in the development process, is the exposure dose.
The optimal exposure dose is a function of many parameters, including the type of resist, the resist thickness, and the sensitivity of the resist.
Resist sensitivity
The resist sensitivity is a measure of how efficiently it reacts to the exposure light. Spectral sensitivity is the sensitivity of the resist as a function of wavelength. It is usually given simply as the range from the wavelength below which absorption in the resist material makes lithography impractical to the wavelength at which the photoinitiator is no longer efficiently activated.
Within the sensitivity range, the optical absorption is commonly used as a measure of sensitivity. A high absorption coefficient signifies a high sensitivity, as the light is absorbed by the photoinitiator. Because of spectral sensitivity, the optimal dose of a given resist type and thickness is also a function of the spectral distribution of the exposure light, i.e. the equipment used for the exposure. Using a combination of experience, calculation and assumptions, it may be possible to estimate the dose for an exposure equipment, if the exposure dose is already known on another equipment.
Due to reflection and refraction at the interface between the resist and the substrate, the optimal dose may also be a function of the type of substrate used. Unless otherwise stated, the exposure doses given below are for standard silicon wafers.
Apart from the already mentioned factors, the optimal dose also depends on the developer chemistry and the parameters used in the development process. Finally, the requirements to the lithographic process in terms of resolution, bias (line broadening), etch selectivity, side wall angle, etc. may narrow down, or widen, the process window. The exposure doses given in the sections below should be used as a starting point for individual fabrication process development.
Due to the process of bleaching, where the absorption of the resist changes during exposure, the exposure dose is unfortunately not always constant at different intensities of the exposure light. The exposure time is thus not always a linear function of the exposure intensity.
Calculate exposure time
In the maskless aligners, the dose is set directly as a process parameter in the job. In mask aligners, on the other hand, the parameter that is set is the exposure time, i.e. how long the shutter is open during the exposure.
The exposure dose, D [J/m2], in terms if exposure light intensity I [W/m2] and exposure time t [s], is given by:
Since the intensity is specific to the spectral sensitivity of the sensor used to measure the exposure light, and the exposure time is specific to the spectral distribution of the exposure light (cf. spectral sensitivity), this dose is specific to the combination of exposure source and optical sensor.
Given an exposure dose, the exposure time, t, is calculated as:
It is important to keep in mind that this exposure time is valid only for a specific combination of exposure source and optical sensor, as well as for a specific development process.
Exposure dose for mask aligners
The exposure doses listed below are for generic good exposure results, and can be a compromise between getting good lines, as well as good dots, in both clear field and dark field exposures. The optimal dose for any given specific project, could be different from the listed values.
All doses are for standard silicon wafers, unless otherwise stated. Development is done using 2.38% TMAH (AZ 726 MIF).
Aligner: MA6-1
The Aligner: MA6-1 has an i-line notch filter installed. This results in an exposure light peak around 365 nm with a FWHM of 7 nm.
Date | Thickness | Dose | Development | Comments | |
---|---|---|---|---|---|
AZ 5214E Data from discontinued German version |
Long ago | 1.5 µm | 72 mJ/cm2 | Single puddle, 60 s | Positive process |
Long ago | 2.2 µm | 80 mJ/cm2 | |||
Long ago | 4.2 µm | 160 mJ/cm2 | |||
AZ 4562 Data from discontinued German version |
Long ago | 10 µm | 510 mJ/cm2 | Multiple puddle, 4 x 60 s | Multiple exposure with 10-15 s pauses is recommended. |
AZ MiR 701 Data from discontinued PFOA containing version |
Long ago | 1 µm | 180 mJ/cm2 | Single puddle, 60 s | PEB: 60 s at 110°C |
Long ago | 2 µm | 200 mJ/cm2 | Single puddle, 60 s | ||
Long ago | 4 µm | 400 mJ/cm2 | Single puddle, 60 s | PEB: 90 s at 110°C | |
AZ nLOF 2020 | Long ago | 2 µm | 110 mJ/cm2 | Single puddle, 60 s | PEB: 60 s at 110°C
Side wall angle ~15° For smaller angle (~5°), develop 30 seconds instead |
Aligner: MA6-2
The Aligner: MA6-2 has an i-line notch filter installed. This results in an exposure light peak around 365 nm with a FWHM of 7 nm.
New resists
As of 2023-03-21 we no longer have any of the old versions of the resists: AZ 5214E, AZ 4562, AZ MiR 701. The following table contains only information about the new resist versions.
Date | Thickness | Dose | Development | Comments | |
---|---|---|---|---|---|
AZ MiR 701 | 2023-09-26 taran |
1.5 µm | 150 mJ/cm2
(13.5s @ 11mW/cm2) |
Single puddle, 60 s | PEB: 60 s @ 110°C |
AZ nLOF 2020 | 2023-09-26 taran |
2 µm | 121 mJ/cm2
(11 s @ 11 mW/cm2) |
Single puddle, 60 s | PEB: 60 s @ 110°C 60 s development for lift-off |
AZ 5214E | 2023-01-11 jehem |
1.5 µm | 70 mJ/cm2 | Single puddle, 60 s | |
AZ 5214E Image Reversal |
2023-01-11 jehem |
2.2 µm | 22 mJ/cm2 | Single puddle, 60 s |
Reversal bake: 60 s at 110°C |
AZ 4562 |
2021-12-08 jehem |
10 µm | 550 mJ/cm2 | Multiple puddles, 5 x 60 s |
Priming: HMDS |
Exposure dose for maskless aligners
The exposure doses listed below are for generic good exposure results, and can be a compromise between getting good lines, as well as good dots, in both clear field and dark field exposures. The optimal dose and achievable resolution for any given specific project, could be different from the listed values.
All doses are for standard silicon wafers, unless otherwise stated. Development is done using 2.38% TMAH (AZ 726 MIF).
Aligner: Maskless 01
The Aligner: Maskless 01 has a 365 nm LED light source with a FWHM of 8 nm.
New resists
As of 2023-03-21 we no longer have any of the old versions of the resists: AZ 5214E, AZ 4562, AZ MiR 701. The following table contains only information about the new resist versions.
Date | Thickness | Exposure mode | Dose | Defoc | Resolution | Comments | |
---|---|---|---|---|---|---|---|
AZ MiR 701 | 2023-07-06 jehem |
1.5 µm | Fast | 275 mJ/cm2 | 1 | 1 µm Tested using dehydration reducing measures |
PEB: 60s@110°C Dev: SP60s |
AZ nLOF 2020 | 2023-07-06 jehem |
2.0 µm | Fast | 180 mJ/cm2 | 0 | 1.5 µm | PEB: 60s@110°C Dev: SP60s |
AZ 5214E | 2024-11-29 taran |
1.5 µm | Fast | 105 mJ/cm2 | 3 | 1.75 µm | Dev: SP60s |
AZ 5214E image reversal |
2023-04-05 jehem |
2.2 µm | Fast | possibly obsolete data 20 mJ/cm2 |
possibly obsolete data -2 |
2.0 µm | Reversal bake: 60s@110°C, Flood exposure: 500mJ/cm2 Dev: SP60s |
AZ 4562 | 2023-04-05 jehem |
10 µm | Fast | possibly obsolete data 1050 mJ/cm2 |
possibly obsolete data -1 |
≤5 µm |
Priming: HMDS |
Dehydration reducing measures used for testing AZ MiR 701:
The CDA used for the pneumatic autofocus will dehydrate the resist. To reduce this effect, the writehead is parked far away from the write area while setting up the job for at least a few minutes, before starting the exposure.
Aligner: Maskless 02
The Aligner: Maskless 02 has a 375 nm laser light source with a FWHM of ~1 nm.
New resists
As of 2023-03-21 we no longer have any of the old versions of the resists: AZ 5214E, AZ 4562, AZ MiR 701. The following table contains only information about the new resist versions.
New writehead
As of 2023-03-21 the MLA2 has a new writehead installed, converting it from a write mode 1 tool to a write mode 2 tool. This makes all previous dose/defocus settings obsolete. The following table contains only the dose/defocus values for the new writehead.
Date | Thickness | Laser | Autofocus | Exposure mode | Dose | Defoc | Resolution | Comments | |
---|---|---|---|---|---|---|---|---|---|
AZ MiR 701 | 2023-08-21 taran |
1.5 µm | 375 | Optical | Quality | 325 mJ/cm2 | 1 | 1 µm Tested using dehydration reducing measures (design elongated +40mm in y). |
PEB: 60s @ 110°C |
Pneumatic | ? | ||||||||
AZ nLOF 2020 | 2023-08-21 taran |
2.0 µm | 375 | Optical | Quality | 450 mJ/cm2 | 0 | 1.5 µm |
PEB: 60s @ 110°C |
Pneumatic | ? | ||||||||
AZ 5214E | 2024-12-09 taran |
1.5 µm | 375 | Optical | Quality | 100 mJ/cm2 | 2 | 1.5 µm | Dev: SP60s |
Pneumatic | -2 (?) | ||||||||
AZ 5214E image reversal |
2023-04-17 jehem |
2.2 µm | 375 | Optical | Quality | 35 mJ/cm2 | 0 | 1.5 µm |
Reversal bake: 60s @ 110°C |
Pneumatic | ? | ||||||||
AZ 4562 | 2023-04-19 jehem |
10 µm | 375 | Optical | Quality | 1150 mJ/cm2 | 0 | ≤5 µm |
Priming: HMDS |
Pneumatic | ? |
Dehydration reducing measures used for testing AZ MiR 701:
The CDA used for the pneumatic autofocus will dehydrate the resist. To reduce this effect, the writehead is parked far away from the write area while setting up the job for at least a few minutes, before starting the exposure.
Aligner: Maskless 03
The Aligner: Maskless 03 has a 405 nm laser light source with a FWHM of ~1 nm.
New resists
As of 2023-03-21 we no longer have any of the old versions of the resists: AZ 5214E, AZ 4562, AZ MiR 701. The following table contains only information about the new resist versions.
Date | Thickness | Laser | Autofocus | Exposure mode | Dose | Defoc | Resolution | Comments | |
---|---|---|---|---|---|---|---|---|---|
AZ MiR 701 | 2023-06-30 jehem |
1.5 µm | 405 | Pneumatic | Quality | 175 mJ/cm2 | 0 | 1 µm Tested using dehydration reducing measures |
PEB: 60s@110°C Dev: SP60s |
AZ 5214E | 2023-06-30 jehem |
1.5 µm | 405 | Pneumatic | Quality | 75 mJ/cm2 | 0 | 1 µm | Dev: SP60s |
AZ 5214E Image reversal |
2023-06-30 jehem |
2.2 µm | 405 | Pneumatic | Quality | 50 mJ/cm2 | 0 | 1 µm |
Reversal bake: 60s@110°C |
AZ nLOF 2020 | 2023-06-30 jehem |
2.0 µm | 405 | Pneumatic | Quality | 9000 mJ/cm2 | 2 | 1 µm |
PEB: 60s @ 100°C |
AZ 4562 | 2023-06-30 jehem |
10 µm | 405 | Pneumatic | Quality | 550 mJ/cm2 | 3 | ≤5 µm |
Priming: HMDS |
Dehydration reducing measures used for testing AZ MiR 701:
The CDA used for the pneumatic autofocus will dehydrate the resist. To reduce this effect, the writehead is parked far away from the write area while setting up the job for at least a few minutes, before starting the exposure.
Exposure dose when using AZ 351B developer (NaOH)
The exposure doses listed below are for generic good exposure results, and can be a compromise between getting good lines, as well as good dots, in both clear field and dark field exposures. The optimal dose for any given specific project, could be different from the listed values.
All doses are for standard silicon wafers, unless otherwise stated. Development is done using AZ 351B developer (NaOH) diluted 1:5.
KS Aligner (351B)
The KS Aligner has an i-line notch filter installed. This results in an exposure light peak around 365 nm with a FWHM of 7 nm.
Date | Thickness | Dose | Development] | Comments | |
---|---|---|---|---|---|
AZ 5214E Data from discontinued German version |
Long ago | 1.5 µm | 70mJ/cm2 | 60 s | Positive process |
Long ago | 2.2 µm | 72 mJ/cm2 | 70 s | ||
Long ago | 4.2 µm | 160 mJ/cm2 | 180 s | ||
AZ 5214E Data from discontinued German version |
Long ago | 1.5 µm | 30 mJ/cm2 | 60 s | Image reversal process.
Reversal bake: 100s at 110°C. |
Long ago | 2.2 µm | 35 mJ/cm2 | 70 s | ||
AZ 4562 Data from discontinued German version |
Long ago | 10 µm | 320 mJ/cm2 | 5 minutes | Multiple exposure with 10-15 s pauses is recommended. |