Specific Process Knowledge/Lithography/UVLithography: Difference between revisions
Line 38: | Line 38: | ||
|[[media:AZ5214E.pdf|AZ5214E.pdf]] | |[[media:AZ5214E.pdf|AZ5214E.pdf]] | ||
|[[Specific_Process_Knowledge/Lithography/Coaters#SSE Spinner|SSE]], [[Specific_Process_Knowledge/Lithography/Coaters#KS Spinner|KS Spinner]], [[Specific_Process_Knowledge/Lithography/Coaters#III-V Spinner|III-V Spinner]] | |[[Specific_Process_Knowledge/Lithography/Coaters#SSE Spinner|SSE]], [[Specific_Process_Knowledge/Lithography/Coaters#KS Spinner|KS Spinner]], [[Specific_Process_Knowledge/Lithography/Coaters#III-V Spinner|III-V Spinner]] | ||
|Positive process: | |'''Positive process:''' | ||
23-33 mJ/cm2 per µm resist for i-line. | 23-33 mJ/cm2 per µm resist for i-line. | ||
½ dose for broadband exposure. | ½ dose (@365nm) for broadband exposure. | ||
Reverse process: | '''Reverse process:''' | ||
10.5 mJ/cm2 per µm resist for i-line, followed by 210 mJ/cm2 flood exposure after reversal bake. | 10.5 mJ/cm2 per µm resist for i-line, followed by 210 mJ/cm2 flood exposure after reversal bake. | ||
½ dose (@365nm) for broadband exposure. | |||
|AZ 351B developer | |AZ 351B developer | ||
|DI water | |DI water | ||
Line 68: | Line 68: | ||
Multiple exposure recommended. | Multiple exposure recommended. | ||
½ dose (@365nm) for broadband exposure. | |||
|AZ 351B developer | |AZ 351B developer | ||
|DI water | |DI water | ||
Line 86: | Line 86: | ||
105 mJ/cm2 per µm resist for i-line. | 105 mJ/cm2 per µm resist for i-line. | ||
1/5 dose for broadband exposure. | 1/5 dose (@365nm) for broadband exposure. | ||
|AZ 726 MIF developer | |AZ 726 MIF developer | ||
|DI water | |DI water |
Revision as of 14:32, 25 March 2014
Feedback to this page: click here
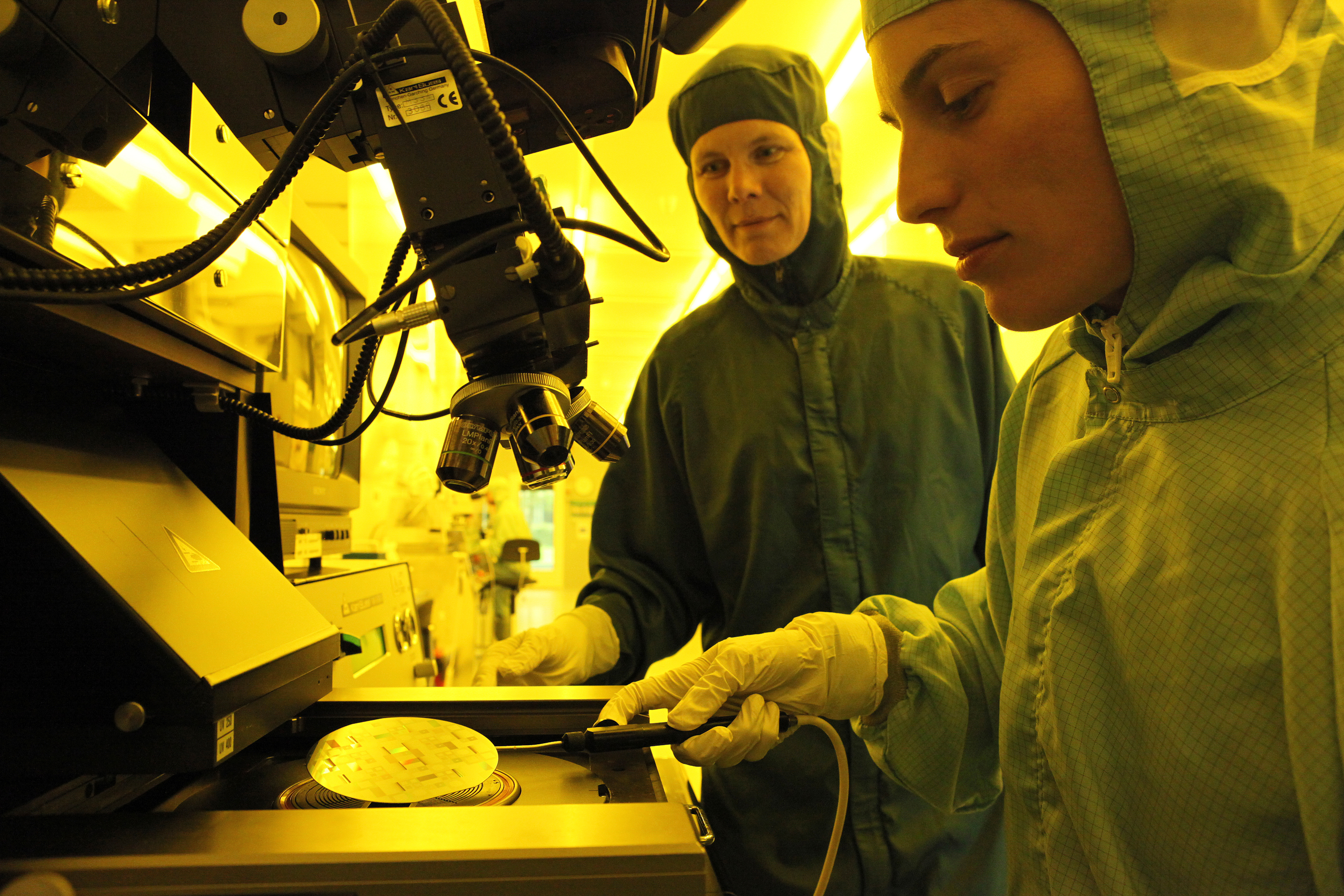
UV Lithography uses ultraviolet light to transfer a pattern from a mask to a wafer coated with photoresist. The photoresist film is spin coated on the wafers and the pattern is transferred to the wafer by using a mask aligner. DTU Danchip houses a number of automatic or semi-automatic coaters and mask aligners.
Resist Overview
Resist | Polarity | Manufacturer | Comments | Technical reports | Spin Coating | Exposure dose | Developer | Rinse | Remover | Process flows (in docx-format) |
AZ 5214E | Positive but can be reversed | AZ Electronic Materials | Can be used for both positive and reverse processes with resist thickness between 1 to 4um. | AZ5214E.pdf | SSE, KS Spinner, III-V Spinner | Positive process:
23-33 mJ/cm2 per µm resist for i-line. ½ dose (@365nm) for broadband exposure. Reverse process: 10.5 mJ/cm2 per µm resist for i-line, followed by 210 mJ/cm2 flood exposure after reversal bake. ½ dose (@365nm) for broadband exposure. |
AZ 351B developer | DI water | Acetone | |
AZ 4562 | Positive | AZ Electronic Materials | For process with resist thickness between 6 and 25um. | AZ4500.pdf | SSE, KS Spinner | 28 mJ/cm2 per µm resist for i-line, probably increasing with increasing thickness.
Multiple exposure recommended. ½ dose (@365nm) for broadband exposure. |
AZ 351B developer | DI water | Acetone | Process_Flow_thick_AZ4562.docx |
AZ MiR 701 | Positive | AZ Electronic Materials | High selectivity for dry etch. | AZ_MiR_701.pdf | Spin Track 1 + 2 | Preliminary results:
105 mJ/cm2 per µm resist for i-line. 1/5 dose (@365nm) for broadband exposure. |
AZ 726 MIF developer | DI water | Remover 1165 | Process_Flow_AZ_MiR701.docx |
AZ nLOF 2020 | Negative | AZ Electronic Materials | AZ_nLOF_2020.pdf | Spin Track 1 + 2 | <30 mJ/cm2 per µm resist for i-line, decreasing with increasing thickness.
Same dose for broadband exposure. |
AZ 726 MIF developer | DI water | Remover 1165 | Process_Flow_AZ_nLOF_2020.docx
| |
SU-8 | Negative | Microchem | SU-8_DataSheet_2005.pdf, SU-8_DataSheet_2075.pdf | KS Spinner | Thickness and process dependent. | PGMEA, mr-Dev 600 developer | IPA | Plasma ashing can remove crosslinked SU8. | Process_Flow_SU8_70um.docx
|