LabAdviser/Technology Research: Difference between revisions
No edit summary |
No edit summary |
||
(141 intermediate revisions by 13 users not shown) | |||
Line 1: | Line 1: | ||
'''Feedback to this page''': '''[mailto:labadviser@ | '''Feedback to this page''': '''[mailto:labadviser@nanolab.dtu.dk?Subject=Feed%20back%20from%20page%20http://labadviser.nanolab.dtu.dk/index.php/LabAdviser/Technology_Research click here]''' | ||
<i> Unless otherwise stated, this page is written by <b>DTU Nanolab internal</b></i> | |||
[[image:Final1.jpg|right|500px|thumb|Image: DTU internal]] | |||
Current project descriptions of projects going on at DTU Nanolab can be found on our home page. Overview of research topics can be found here: [https://www.nanolab.dtu.dk/research DTU Nanolab research] and list of Ph.d. students/projects can be found here: [https://www.nanolab.dtu.dk/education/phd-school/phds-at-nanolab PhD's at DTU Nanolab]. | |||
The original aim of this page was to give an overview of the technology research going on in the cleanroom and the other laboratories facilitated by DTU Nanolab. That included a project description and links to other pages in LabAdviser where the process development outcome from these projects can be found. There are a few projects described here but at the moment this is not being fully updated. Please take a look at our home page to get information about current projects. | |||
<!-- [[image:Technology Research.jpg|right|400px]] --> | |||
'''Presentation Form for Presenting Technology Research:''' | |||
*[[/Presentation Form|Presentation Form]] | |||
If you perform technology research in the DTU Nanolab facilities and you would like to contribute to this overview page then please start by contacting [mailto:labadviser@nanolab.dtu.dk?Subject=I%20would%20like%20to%20present%20my%20technology%20research&body=Dear%20Berit,%0A%0DFree%20text...%0A%0DOr%20your%20call%20me:%2045256303 Berit Herstrøm]. | |||
In the bottom of the page some student 3-weeks project reports are listed and uploaded. More project reports are welcome. | |||
<br clear="all"/> | |||
==Projects - Fabrication== | |||
===Advanced Nanomachining=== | |||
*[[/Technology Development of Nanoscale Silicon Plasma Etching Process|Technology Development of Nanoscale Silicon Plasma Etching Process]] - ''initiated November 2017'' - Vy Thi Hoang Nguyen | |||
===Biomaterial Microsystems=== | |||
*[[/Cleanroom fabrication of 3D electrodes with lithography and pyrolysis|Cleanroom fabrication of 3D electrodes with lithography and pyrolysis]] - Jesper Yue Pan | |||
*[[/Direct laser pyrolysis|Direct laser pyrolysis]] - Emil Ludvigsen | |||
*[[/Direct write lithography on MLAs for fabrication of carbon micro tips|Direct write lithography on MLAs for fabrication of carbon micro tips]] - Long Nguyen Quang | |||
*[[/Hot punching and slot die coating|Hot punching and slot die coating]] - Ritika Singh Petersen | |||
===Polymer Microsystems=== | |||
*[[/Fabrication of surfaces for the promotion of bacterial biofilms|Fabrication of surfaces for the promotion of bacterial biofilms]] - initiated 2019 - Ariadni Droumpali | |||
===Silicon Microtechnology=== | |||
*[[/Technology for CZTS-Silicon Tandem Solar Cells|Technology for CZTS-Silicon Tandem Solar Cells]] - initiated June 2017 - Alireza Hajijafarassar | |||
==Projects - Characterization== | |||
===Nanostructure and Functionality=== | |||
*[[/Quantitative electron microscopy of 2D materials|Quantitative electron microscopy of 2D materials]] - ''initiated September 2018'' - Anton Bay Andersen | |||
*[[/High-resolution_TEM_cat-nano-surf|High-resolution transmission electron microscopy of catalytic nanoparticle surfaces]] - ''initiated December 2019'' - William Bang Lomholdt | |||
*[[/Synthesis and nanoscale characterization of ultrathin and ultrasmooth metal films|Synthesis and nanoscale characterization of ultrathin and ultrasmooth metal films]] - ''initiated December 2017'' - Mario Frederik Heinig | |||
===Molecular Windows=== | |||
*[[/Live_TEM_imaging_nanowire_growth|Live TEM imaging of Nanowire growth and device dynamics]] - ''initiated December 2018'' - Christopher Røhl Andersen | |||
===Electron Matter Interactions=== | |||
===Soft Matter=== | |||
==Completed Projects - Fabrication== | |||
===Plasmonics and Metamaterials=== | |||
*[[/Fabrication of Hyperbolic Metamaterials using Atomic Layer Deposition|Fabrication of Hyperbolic Metamaterials using Atomic Layer Deposition]] - ''initiated November 2013'' - Evgeniy Shkondin | |||
===Advanced Nanomachining=== | |||
*[[/Technology Development of 3D Silicon Plasma Etching process for Novel Devices and Applications|Technology Development of 3D Silicon Plasma Etching process for Novel Devices and Applications]] - ''initiated November 2015'' - Bingdong Chang | |||
===Biomaterial Microsystems=== | |||
===Polymer Microsystems=== | |||
===Silicon Microtechnology=== | |||
*[[/Microfabrication of X-ray optical elements|Microfabrication of X-ray optical elements]] - ''initiated February 2017'' - Chantal Silvestre | |||
*[[/Nanofabrication of Inductive Components for Integrated Power Supply On Chip|Nanofabrication of Inductive Components for Integrated Power Supply On Chip]] - ''initiated November 2014'' Hoà Lê Thanh | |||
*[[/Microfabrication of Hard x-ray Lenses|Microfabrication of Hard x-ray Lenses]] - ''initiated December 2012'' - Frederik Stöhr | |||
==Completed Projects - Characterization== | |||
===Nanostructure and Functionality=== | |||
*[[/Nanoscale characterization of ultra-thin metal films for nanofabrication applications|Nanoscale characterization of ultra-thin metal films for nanofabrication applications]] - ''initiated November 2014'' - Matteo Todeschini | |||
===Molecular Windows=== | |||
===Electron Matter Interactions=== | |||
*[[/Organic Ice Resists for Electron-Beam Lithography - Instrumentation and Processes|Organic Ice Resists for Electron-Beam Lithography - Instrumentation and Processes]] - ''initiated November 2014'' - William Tiddi | |||
===Soft Matter=== | |||
==Completed 3 week projects== | |||
{| border="1" style="text-align: center; height: 200px;" | |||
|- | |||
|colspan="6" style="text-align: center;" style="background: #efefef;" | '''Here you can upload 3-week courses reports that have been carried out at DTU Nanolab. It is up to the supervisors and the students to decide if they want to upload, therefor this list is not a full list of 3-week projects that are going on at DTU Nanolab''' | |||
|- | |||
!scope="row" |Report date | |||
!|Supervisor | |||
!|students | |||
! width="500"|Short abstract | |||
!|File link | |||
!|Keywords | |||
|- | |||
|- | |||
!2018-11 | |||
|jehan@dtu.dk <br> | |||
khara@dtu.dk <br> | |||
flje@dtu.dk | |||
|Jens Hemmingsen s135101 | |||
| | |||
X-ray imaging is a widely used non-invasive imaging technique, with applications in fields such | |||
as materials science, medicine or even food quality control, where the ability to detect foreign | |||
objects can be critical. X-rays have the ability to transmit through many materials with ab- | |||
sorption rates dependent on the material density, which is used to create traditional absorption | |||
x-ray images. | |||
The ability to transmit through materials is, however, a fundamental problem for any application | |||
that requires focusing of the x-rays, since the x-rays will transmit through traditional optical | |||
lenses, without any significant refraction. | |||
Focusing of x-rays is currently done by consecutive stacking of beryllium lenses, in what is known | |||
as a compound lens, but as the x-ray sources have improved over time, the inherent refractive | |||
grain structure in the beryllium lenses have become a source of degradation of the coherence of | |||
the beam. | |||
||[[Media:Diamant2018_v5.pdf]] | |||
|3D laser micro machining, laser milling, diamond, x-ray, lens, CRL | |||
|- | |||
|- | |||
|- | |||
!2018-07 | |||
|jehan@dtu.dk <br> | |||
reet@dtu.dk <br> | |||
|Martin Schjeldrup Jessen s153298 <br> | |||
Christoffer Emil Kurt Tost Jensen s152358 | |||
| | |||
The purpose of the project is to investigate sputter deposition of materials under varying conditions. | |||
It was investigated how the different parameters of Physical Vapor | |||
Deposition affects the rate and quality of the deposition. This was investigated using series of | |||
experiments designed to create a surface response model for each of the materials tested. This | |||
project will also cover what methods are ideal to use for measuring the thickness of a deposition. | |||
||[[Media:Lesker_rapport_3w_july_2018.pdf ]] | |||
|sputtering, lesker, thin film, characterization, ... | |||
|- | |||
|- | |||
|- | |||
!2018-06-21 | |||
|bghe@danchip.dtu.dk <br> | |||
taran@danchip.dtu.dk <br> | |||
|Martin Riis s181169 <br> | |||
Teitur Hansen s173963 <br> | |||
Nataniel Andresas Olden-Jørgensen s163936 | |||
| | |||
The purpose of the project is optimize the lithography process on Si/SiO2 wafers to obtain straight sidewalls for dry plasma etching. In the project we experience adhesion problems and undercut of the resist at the interface to the sample. Several tests were performed in order to overcome this problem. | |||
||[[Media:New_3_Week_Course.pdf]] | |||
|UV lithography | |||
|- | |||
|- | |||
!2017-06-22 | |||
|pevo@danchip.dtu.dk <br> | |||
mdyma@danchip.dtu.dk <br> | |||
tanamp@dtu.dk | |||
|Asger Sommer s153889 <br> | |||
Christoffer E. K. T. Jensen s152358 <br> | |||
Rikke Bagge s151728 | |||
| | |||
The purpose of the project is develop an optimized recipe for deposition of aluminium nitride (AlN) in the PEALD at Danchip. TMA and NH3 plasma have been used as precursors. | |||
A good quality AlN film should have a decent deposition rate, a high uniformity, a low roughness, a low amount of particles and a small amount of impurities (especially of oxygen and carbon). | |||
The deposited AlN layers have been characterized using a particle scanner, ellipsometry, AFM, SEM and XPS. | |||
AlN has been deposited on wafers, and the best recipe have been chosen for deposition on samples with high aspect ratio trenches. | |||
To limit the amount of depositions the design of experiment (DOE) software JMP has been used to select a number of different recipe parameters. JMP has also been used to evaluate the results. | |||
||[[Media:33470-Mikro3W-Journal.pdf|PEALD deposition of AlN using TMA and NH3]] | |||
|PEALD, AlN, DOE, characterization | |||
|- | |||
!2017-06-22 | |||
|chasil@danchip.dtu.dk | |||
|Andreas R. Stilling-Andersen s163397 <br> | |||
Kristine Børsting s153299 | |||
| | |||
In this 3-weeks course, the student will be working on the micro-fabrication of a Silicon/Gold grating for X-Ray optics. The fabrication of these devices require the usage of standard UV lithography combine with DRIE of silicon and metal thermal evaporation. The optimized DRIE Bosch process creates a fluorocarbon (FC) layer deposited homogeneously along the sidewall of the trench. While the depth of the trench increases with the dry etch number of cycles, an FC layer is accumulating at the top of the trench. This protrusion allows for shadow masking the sidewalls during thermal evaporation of gold, in order to deposit a seed layer at the bottom of the trench allowing for subsequent metallization by electroplating. The student will be designing a simple mask using the software CleWin. The mask will be pattern on a UV resist (5214E) using the Maskless aligner available at DTU Danchip. They will also calculate how deep the trench should be to get a minimum absorption of 92% of the intensity of the X-Ray energy. | |||
||[[Media:Micro_fabrication_of_x_ray_optics_3w_Andreas_Kristin.pdf|Microfabrication of X-Ray optics]] | |||
|DRIE, Lithography, CleWin, Characterization | |||
|- | |||
!2017-06-21 | |||
|Bingdong Chang bincha@dtu.dk | |||
|Benjamin Lundgren Larsen s164006 <br> | |||
Mathias Hoeg Boisen s164000 | |||
|Using the Black Silicon Method to Monitor the Reproducibility of Plasma Etching Processes | |||
|[[Media:Final report_Black silicon.pdf|Black silicon]] | |||
|RIE, Plasma etching, process reproducibility | |||
|- | |||
!2017-01-18 | |||
|Bingdong Chang bincha@dtu.dk | |||
|Keld Fernstrøm s144075 <br> | |||
Asger Steen Nielsen s150369 | |||
|Precise Timing Control in Deep Reactive Ion Etching (DRIE) with Bosch Process | |||
|[[Media:Final report_Etching time control.pdf|Etching time control]] | |||
|DRIE, Plasma Etching | |||
|- | |||
!2016-06-22 | |||
|Bingdong Chang bincha@dtu.dk | |||
|Christian Dam Vedel s153721 <br> | |||
Kitty Steenberg s141812 <br> | |||
Mette Bybjerg Brock s134252 | |||
|High Resolution Pattern Definition with E-beam Lithography | |||
|[[Media:Final report_EBL pattern with HSQ.pdf|EBL pattern with HSQ]] | |||
|E-beam lithography | |||
|- | |||
!2016-01-20 | |||
|mattod@danchip.dtu.dk<br> pevo@danchip.dtu.dk pewin@danchip.dtu.dk | |||
|Gustav Juhl Johansen s134266<br> | |||
William Band Lomholt s4269 | |||
|In-situ imaging of the ALD film growth mechanism can be done in an environmental TEM (eTEM), but it is very important to understand if the gas phase reactions can contaminate the microscope. For this reason a small ALD system with a chamber size corresponding to the specimen area of the eTEM has been build. With this chamber ALD depositions of platinum can be studied and optimized. In this project the software LabView has been used to program a Virtual Intstument (VI) that can control the different components of the hardware on the ALD system. With the software it is also possible to define the parameters for an ALD deposition process. The different programming steps are described in details in the report. Furhermore, the ALD deposition principle is described in the report. | |||
|[[:media:3week_Jan2016_Gustav_William.pdf|Programming the Control Software of an Atomic Layer Deposition System]] | |||
|ALD, LabView | |||
|- | |||
|- | |||
!2015-06-25 | |||
|pevo@danchip.dtu.dk<br> mdyma@danchip.dtu.dk | |||
|Daniel Anyaogu s134258<br> | |||
Emil Ludvigsen s134254 | |||
| | |||
DRIE etching of deep structures in silicon samples results in rough sidewalls with scallops that for many applications are very undesirable. | |||
It has been shown that scallops can be removed by use of hydrogen annealing as the surface mobility of the silicon atoms then enhances. | |||
In this project silicon samples with DRIE etched micro trenches have then been annealed in the ATV Furnace and the Black Magic PECVD. The annealing has been done at high temperatures and both at atmospheric pressure and vacuum. Prior to the annealing some of the sample have been RCA cleaned. | |||
To evaluate the effect of the annealing the samples have been inspected using SEM. | |||
|[[:media:Hydrogen Annealing for Removal of Scallops after DRIE.pdf|Hydrogen Annealing for Removal of Scallops after DRIE]] | |||
|DRIE, scallops, hydrogen annealing | |||
|- | |||
|- | |||
!2015-06-24 | |||
|jehan@danchip.dtu.dk | |||
|Zakaria Abachri (s134237) <br> Rune Sixten Grass (s134243) | |||
|The purpose of this project and following journal is to characterise the material thickness produced using parameters such as pressure, power and ratio of source materials used in magnetron sputtering of silicon wafers on the sputter system in DTU Danschips cleanroom. We want to investigate and optimize the sputter deposition process and map how the parameters affects the thickness of different types of metals, dielectrics or semiconductors on silicon wafers. The thickness will be measured in-situ by an ellipsometer layer by layer by fitting different types of material models to the data, which in turn predict the growth rate for each layer. An ex-situ measurement of the total multilayer thickness will also be carried out as a comparison to the model fit. | |||
|[[Media:3_weeks_course_Zakaria_Abachri_(s134237)_Rune_Sixten_Grass_(s134243).pdf |Optimization of thin film deposition using in-situ ellipsometry]] | |||
|ellipsometry, thin film, in-situ, sputtering, lesker | |||
|- | |||
!2015-08-05 | |||
|jehan@danchip.dtu.dk<br> rkc@danchip.dtu.dk | |||
|Jens Hemmingsen s135101 | |||
|Laser ablation is a method used to remove material from a solid surface, by irradiating it with a laser beam. The material directly underneath the beam is heated and then evaporates. The process can be compared to old fashioned machine milling, in which a rotary tool is used to remove material from a solid surface, and indeed laser ablation is also known as laser micromachining. There are a lot of different, sometimes interdependent, process parameters used in the milling process, which means that the ablation removal rate often depends on the specific design pattern used in a particular job. The goal of this project is to reduce the need for design-specific process optimization or to find ways to simplify the process optimization. | |||
|[[:media:3-weeks_course_-_Jens_Hemmingsen_-_micro-3W_laser_micromachining.pdf|Laser micromachining of silicon microstructures]] | |||
|laser micro machining, silicon, dicing | |||
|- | |||
|} |
Latest revision as of 12:53, 4 January 2024
Feedback to this page: click here
Unless otherwise stated, this page is written by DTU Nanolab internal
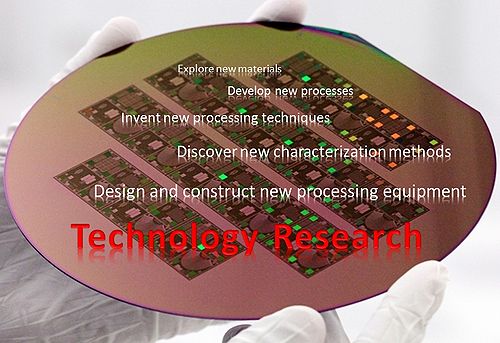
Current project descriptions of projects going on at DTU Nanolab can be found on our home page. Overview of research topics can be found here: DTU Nanolab research and list of Ph.d. students/projects can be found here: PhD's at DTU Nanolab.
The original aim of this page was to give an overview of the technology research going on in the cleanroom and the other laboratories facilitated by DTU Nanolab. That included a project description and links to other pages in LabAdviser where the process development outcome from these projects can be found. There are a few projects described here but at the moment this is not being fully updated. Please take a look at our home page to get information about current projects.
Presentation Form for Presenting Technology Research:
If you perform technology research in the DTU Nanolab facilities and you would like to contribute to this overview page then please start by contacting Berit Herstrøm.
In the bottom of the page some student 3-weeks project reports are listed and uploaded. More project reports are welcome.
Projects - Fabrication
Advanced Nanomachining
- Technology Development of Nanoscale Silicon Plasma Etching Process - initiated November 2017 - Vy Thi Hoang Nguyen
Biomaterial Microsystems
- Cleanroom fabrication of 3D electrodes with lithography and pyrolysis - Jesper Yue Pan
- Direct laser pyrolysis - Emil Ludvigsen
- Direct write lithography on MLAs for fabrication of carbon micro tips - Long Nguyen Quang
- Hot punching and slot die coating - Ritika Singh Petersen
Polymer Microsystems
- Fabrication of surfaces for the promotion of bacterial biofilms - initiated 2019 - Ariadni Droumpali
Silicon Microtechnology
- Technology for CZTS-Silicon Tandem Solar Cells - initiated June 2017 - Alireza Hajijafarassar
Projects - Characterization
Nanostructure and Functionality
- Quantitative electron microscopy of 2D materials - initiated September 2018 - Anton Bay Andersen
- High-resolution transmission electron microscopy of catalytic nanoparticle surfaces - initiated December 2019 - William Bang Lomholdt
- Synthesis and nanoscale characterization of ultrathin and ultrasmooth metal films - initiated December 2017 - Mario Frederik Heinig
Molecular Windows
- Live TEM imaging of Nanowire growth and device dynamics - initiated December 2018 - Christopher Røhl Andersen
Electron Matter Interactions
Soft Matter
Completed Projects - Fabrication
Plasmonics and Metamaterials
- Fabrication of Hyperbolic Metamaterials using Atomic Layer Deposition - initiated November 2013 - Evgeniy Shkondin
Advanced Nanomachining
- Technology Development of 3D Silicon Plasma Etching process for Novel Devices and Applications - initiated November 2015 - Bingdong Chang
Biomaterial Microsystems
Polymer Microsystems
Silicon Microtechnology
- Microfabrication of X-ray optical elements - initiated February 2017 - Chantal Silvestre
- Nanofabrication of Inductive Components for Integrated Power Supply On Chip - initiated November 2014 Hoà Lê Thanh
- Microfabrication of Hard x-ray Lenses - initiated December 2012 - Frederik Stöhr
Completed Projects - Characterization
Nanostructure and Functionality
- Nanoscale characterization of ultra-thin metal films for nanofabrication applications - initiated November 2014 - Matteo Todeschini
Molecular Windows
Electron Matter Interactions
- Organic Ice Resists for Electron-Beam Lithography - Instrumentation and Processes - initiated November 2014 - William Tiddi
Soft Matter
Completed 3 week projects
Here you can upload 3-week courses reports that have been carried out at DTU Nanolab. It is up to the supervisors and the students to decide if they want to upload, therefor this list is not a full list of 3-week projects that are going on at DTU Nanolab
| |||||
Report date | Supervisor | students | Short abstract | File link | Keywords |
---|---|---|---|---|---|
2018-11 | jehan@dtu.dk khara@dtu.dk |
Jens Hemmingsen s135101 |
X-ray imaging is a widely used non-invasive imaging technique, with applications in fields such as materials science, medicine or even food quality control, where the ability to detect foreign objects can be critical. X-rays have the ability to transmit through many materials with ab- sorption rates dependent on the material density, which is used to create traditional absorption x-ray images. The ability to transmit through materials is, however, a fundamental problem for any application that requires focusing of the x-rays, since the x-rays will transmit through traditional optical lenses, without any significant refraction. Focusing of x-rays is currently done by consecutive stacking of beryllium lenses, in what is known as a compound lens, but as the x-ray sources have improved over time, the inherent refractive grain structure in the beryllium lenses have become a source of degradation of the coherence of the beam. |
Media:Diamant2018_v5.pdf | 3D laser micro machining, laser milling, diamond, x-ray, lens, CRL |
2018-07 | jehan@dtu.dk reet@dtu.dk |
Martin Schjeldrup Jessen s153298 Christoffer Emil Kurt Tost Jensen s152358 |
The purpose of the project is to investigate sputter deposition of materials under varying conditions. It was investigated how the different parameters of Physical Vapor Deposition affects the rate and quality of the deposition. This was investigated using series of experiments designed to create a surface response model for each of the materials tested. This project will also cover what methods are ideal to use for measuring the thickness of a deposition. |
Media:Lesker_rapport_3w_july_2018.pdf | sputtering, lesker, thin film, characterization, ... |
2018-06-21 | bghe@danchip.dtu.dk taran@danchip.dtu.dk |
Martin Riis s181169 Teitur Hansen s173963 |
The purpose of the project is optimize the lithography process on Si/SiO2 wafers to obtain straight sidewalls for dry plasma etching. In the project we experience adhesion problems and undercut of the resist at the interface to the sample. Several tests were performed in order to overcome this problem. |
Media:New_3_Week_Course.pdf | UV lithography |
2017-06-22 | pevo@danchip.dtu.dk mdyma@danchip.dtu.dk |
Asger Sommer s153889 Christoffer E. K. T. Jensen s152358 |
The purpose of the project is develop an optimized recipe for deposition of aluminium nitride (AlN) in the PEALD at Danchip. TMA and NH3 plasma have been used as precursors. A good quality AlN film should have a decent deposition rate, a high uniformity, a low roughness, a low amount of particles and a small amount of impurities (especially of oxygen and carbon). The deposited AlN layers have been characterized using a particle scanner, ellipsometry, AFM, SEM and XPS. AlN has been deposited on wafers, and the best recipe have been chosen for deposition on samples with high aspect ratio trenches. To limit the amount of depositions the design of experiment (DOE) software JMP has been used to select a number of different recipe parameters. JMP has also been used to evaluate the results. |
PEALD deposition of AlN using TMA and NH3 | PEALD, AlN, DOE, characterization |
2017-06-22 | chasil@danchip.dtu.dk | Andreas R. Stilling-Andersen s163397 Kristine Børsting s153299 |
In this 3-weeks course, the student will be working on the micro-fabrication of a Silicon/Gold grating for X-Ray optics. The fabrication of these devices require the usage of standard UV lithography combine with DRIE of silicon and metal thermal evaporation. The optimized DRIE Bosch process creates a fluorocarbon (FC) layer deposited homogeneously along the sidewall of the trench. While the depth of the trench increases with the dry etch number of cycles, an FC layer is accumulating at the top of the trench. This protrusion allows for shadow masking the sidewalls during thermal evaporation of gold, in order to deposit a seed layer at the bottom of the trench allowing for subsequent metallization by electroplating. The student will be designing a simple mask using the software CleWin. The mask will be pattern on a UV resist (5214E) using the Maskless aligner available at DTU Danchip. They will also calculate how deep the trench should be to get a minimum absorption of 92% of the intensity of the X-Ray energy. |
Microfabrication of X-Ray optics | DRIE, Lithography, CleWin, Characterization |
2017-06-21 | Bingdong Chang bincha@dtu.dk | Benjamin Lundgren Larsen s164006 Mathias Hoeg Boisen s164000 |
Using the Black Silicon Method to Monitor the Reproducibility of Plasma Etching Processes | Black silicon | RIE, Plasma etching, process reproducibility |
2017-01-18 | Bingdong Chang bincha@dtu.dk | Keld Fernstrøm s144075 Asger Steen Nielsen s150369 |
Precise Timing Control in Deep Reactive Ion Etching (DRIE) with Bosch Process | Etching time control | DRIE, Plasma Etching |
2016-06-22 | Bingdong Chang bincha@dtu.dk | Christian Dam Vedel s153721 Kitty Steenberg s141812 |
High Resolution Pattern Definition with E-beam Lithography | EBL pattern with HSQ | E-beam lithography |
2016-01-20 | mattod@danchip.dtu.dk pevo@danchip.dtu.dk pewin@danchip.dtu.dk |
Gustav Juhl Johansen s134266 William Band Lomholt s4269 |
In-situ imaging of the ALD film growth mechanism can be done in an environmental TEM (eTEM), but it is very important to understand if the gas phase reactions can contaminate the microscope. For this reason a small ALD system with a chamber size corresponding to the specimen area of the eTEM has been build. With this chamber ALD depositions of platinum can be studied and optimized. In this project the software LabView has been used to program a Virtual Intstument (VI) that can control the different components of the hardware on the ALD system. With the software it is also possible to define the parameters for an ALD deposition process. The different programming steps are described in details in the report. Furhermore, the ALD deposition principle is described in the report. | Programming the Control Software of an Atomic Layer Deposition System | ALD, LabView |
2015-06-25 | pevo@danchip.dtu.dk mdyma@danchip.dtu.dk |
Daniel Anyaogu s134258 Emil Ludvigsen s134254 |
DRIE etching of deep structures in silicon samples results in rough sidewalls with scallops that for many applications are very undesirable. It has been shown that scallops can be removed by use of hydrogen annealing as the surface mobility of the silicon atoms then enhances. In this project silicon samples with DRIE etched micro trenches have then been annealed in the ATV Furnace and the Black Magic PECVD. The annealing has been done at high temperatures and both at atmospheric pressure and vacuum. Prior to the annealing some of the sample have been RCA cleaned. To evaluate the effect of the annealing the samples have been inspected using SEM. |
Hydrogen Annealing for Removal of Scallops after DRIE | DRIE, scallops, hydrogen annealing |
2015-06-24 | jehan@danchip.dtu.dk | Zakaria Abachri (s134237) Rune Sixten Grass (s134243) |
The purpose of this project and following journal is to characterise the material thickness produced using parameters such as pressure, power and ratio of source materials used in magnetron sputtering of silicon wafers on the sputter system in DTU Danschips cleanroom. We want to investigate and optimize the sputter deposition process and map how the parameters affects the thickness of different types of metals, dielectrics or semiconductors on silicon wafers. The thickness will be measured in-situ by an ellipsometer layer by layer by fitting different types of material models to the data, which in turn predict the growth rate for each layer. An ex-situ measurement of the total multilayer thickness will also be carried out as a comparison to the model fit. | Optimization of thin film deposition using in-situ ellipsometry | ellipsometry, thin film, in-situ, sputtering, lesker |
2015-08-05 | jehan@danchip.dtu.dk rkc@danchip.dtu.dk |
Jens Hemmingsen s135101 | Laser ablation is a method used to remove material from a solid surface, by irradiating it with a laser beam. The material directly underneath the beam is heated and then evaporates. The process can be compared to old fashioned machine milling, in which a rotary tool is used to remove material from a solid surface, and indeed laser ablation is also known as laser micromachining. There are a lot of different, sometimes interdependent, process parameters used in the milling process, which means that the ablation removal rate often depends on the specific design pattern used in a particular job. The goal of this project is to reduce the need for design-specific process optimization or to find ways to simplify the process optimization. | Laser micromachining of silicon microstructures | laser micro machining, silicon, dicing |