Specific Process Knowledge/Lithography: Difference between revisions
No edit summary |
|||
(21 intermediate revisions by the same user not shown) | |||
Line 7: | Line 7: | ||
__TOC__ | __TOC__ | ||
Lithography is a method used for transferring a pattern from a physical or digital mask onto the substrate. At DTU Nanolab we have four different types of lithography | Lithography is a method used for transferring a pattern from a physical or digital mask onto the substrate. At DTU Nanolab we have four different types of lithography available: | ||
*[[Specific Process Knowledge/Lithography/UVLithography|UV Lithography]]: UV lithography is used for making features as small as about 1 micrometer | *[[Specific Process Knowledge/Lithography/UVLithography|UV Lithography]]: UV lithography is used for making features as small as about 1 micrometer | ||
*[[Specific Process Knowledge/Lithography/DUVStepperLithography|DUV Stepper Lithography]]: DUV lithography is used for features as small as | *[[Specific Process Knowledge/Lithography/DUVStepperLithography|DUV Stepper Lithography]]: DUV lithography is used for features as small as 200 nm | ||
*[[Specific Process Knowledge/Lithography/EBeamLithography|E-beam Lithography]]: The smallest features can be made in our e-beam writers - about 10 nm | *[[Specific Process Knowledge/Lithography/EBeamLithography|E-beam Lithography]]: The smallest features can be made in our e-beam writers - about 10 nm | ||
*[[Specific_Process_Knowledge/Imprinting|Nano Imprint Lithography]]: for stamping without irradiation | *[[Specific_Process_Knowledge/Imprinting|Nano Imprint Lithography]]: for stamping without irradiation | ||
Line 16: | Line 16: | ||
=Comparing lithography methods at DTU Nanolab= | =Comparing lithography methods at DTU Nanolab= | ||
{| | {| class="wikitable" width="100%" | ||
|- | |- | ||
! !! [[Specific Process Knowledge/Lithography/UVLithography|UV Lithography]] !! [[Specific Process Knowledge/Lithography/DUVStepperLithography|DUV Stepper Lithography]] !! [[Specific Process Knowledge/Lithography/EBeamLithography|E-beam Lithography]] !! [[Specific_Process_Knowledge/Imprinting|Nano Imprint Lithography]] | |||
|- | |- | ||
! scope=row style="text-align: left;" | Generel description | |||
| Pattern transfer via ultraviolet (UV) light || Pattern transfer via deep ultraviolet (DUV) light || Patterning by electron beam || Pattern transfer via hot embossing (HE) | |||
|- | |- | ||
! scope=row style="text-align: left;" | Pattern size range | |||
| ~1 µm and up<br>(resist type, thickness, and pattern dependent) || ~200 nm and up<br>(pattern type, shape and pitch dependent) || ~10-1000 nm<br>(and larger at high currents) || ~20 nm and up | |||
|- | |- | ||
! scope=row style="text-align: left;" | Resist type | |||
| | |||
| | |||
| | |||
UV sensitive: | UV sensitive: | ||
*AZ 5214E, AZ 4562, AZ MiR 701 (positive) | *AZ 5214E, AZ 4562, AZ MiR 701 (positive) | ||
*AZ 5214E, AZ nLOF 2020, SU-8 (negative) | *AZ 5214E, AZ nLOF 2020, SU-8 (negative) | ||
| | | | ||
DUV sensitive | DUV sensitive: | ||
*JSR KRF M230Y, JSR KRF M35G (positive) | *JSR KRF M230Y, JSR KRF M35G (positive) | ||
*UVN2300-0.8 (negative) | *UVN2300-0.8 (negative) | ||
| | | | ||
E-beam sensitive | E-beam sensitive: | ||
*AR-P6200 CSAR, ZEP502A , PMMA (positive) | *AR-P6200 CSAR, ZEP502A , PMMA (positive) | ||
*HSQ, mr-EBL, AR-N 7520 (negative) | *HSQ, mr-EBL, AR-N 7520 (negative) | ||
| | | | ||
Imprint polymers: | Imprint polymers: | ||
*Topas | *Topas | ||
Line 76: | Line 45: | ||
*mr-I 7030R | *mr-I 7030R | ||
|- | |- | ||
! scope=row style="text-align: left;" | Resist thickness range | |||
| ~0.5 µm to 200 µm || ~50 nm to 2 µm || ~30 nm to 1 µm || ~100 nm to 2 µm | |||
| | |||
~0.5 µm to 200 µm | |||
| | |||
~50 nm to 2 µm | |||
| | |||
~30 nm to 1 µm | |||
| | |||
~ 100 nm to 2 µm | |||
|- | |- | ||
! scope=row style="text-align: left;" | Typical exposure time | |||
| Mask aligner: 10-180 s per wafer<br>Maskless aligner: 5-60 minutes per wafer | |||
| | | | ||
10 s | |||
| | |||
Process dependent: | Process dependent: | ||
*Pattern | *Pattern | ||
Line 103: | Line 57: | ||
Throughput is up to 60 wafers/hour | Throughput is up to 60 wafers/hour | ||
| | | | ||
Process dependent: | Process dependent: | ||
*Dose | *Dose [µC/cm<sup>2</sup>]: <math>Q</math> | ||
*Beam current | *Beam current [A]: <math>I</math> | ||
*Pattern area | *Pattern area [cm<sup>2</sup>]: <math>a</math> | ||
Process time [s]: <math>t = \frac{Q \sdot a}{I}</math> | |||
| Process dependent, including heating/cooling rates | |||
|- | |- | ||
! scope=row style="text-align: left;" | Substrate size | |||
| | |||
| | |||
*chips down to 3 mm x 3 mm | *chips down to 3 mm x 3 mm | ||
*50 mm wafers | *50 mm wafers | ||
*100 mm wafers | *100 mm wafers | ||
*150 mm wafers | *150 mm wafers | ||
*200 mm wafers | *200 mm wafers | ||
| | | | ||
*100 mm wafers | *100 mm wafers | ||
*150 mm wafers | *150 mm wafers | ||
*200 mm wafers | *200 mm wafers | ||
| | | | ||
We have cassettes fitting: | We have cassettes fitting: | ||
*4 small samples (slit openings: 20mm, 12mm, 8mm, 4mm) | *4 small samples (slit openings: 20mm, 12mm, 8mm, 4mm) | ||
Line 136: | Line 85: | ||
*1 wafer of 200 mm in size | *1 wafer of 200 mm in size | ||
Only one cassette can be loaded at a time | Only one cassette can be loaded at a time | ||
| | | | ||
*small samples | *small samples | ||
*50 mm wafers | *50 mm wafers | ||
*100 mm wafers | *100 mm wafers | ||
*150 mm wafers | *150 mm wafers | ||
|- | |- | ||
! scope=row style="text-align: left;" | Allowed materials | |||
| Any standard cleanroom material | |||
| Any standard cleanroom material | |||
| | | | ||
Any standard cleanroom material | |||
| | |||
Any standard cleanroom material | |||
| | |||
Any standard cleanroom material, except: | Any standard cleanroom material, except: | ||
*Materials that will degas | *Materials that will degas | ||
*Graphene requires special treatment | *Graphene requires special treatment | ||
| | | Any standard cleanroom material | ||
Any standard cleanroom material | |||
|- | |- | ||
|} | |} | ||
<br clear="all" /> | <br clear="all" /> | ||
=Equipment Pages= | =Equipment and Process Pages= | ||
{ | {{:Specific Process Knowledge/Lithography/UVlithographyProcessPages}} | ||
=Lithography Tool Package Training= | =Lithography Tool Package Training= |
Latest revision as of 17:06, 2 April 2025
The contents on this page, including all images and pictures, was created by DTU Nanolab staff unless otherwise stated.
Feedback to this page: click here
Lithography
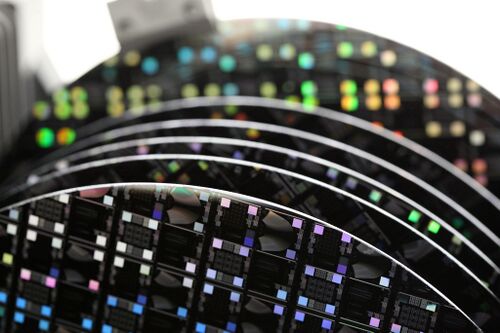
Lithography is a method used for transferring a pattern from a physical or digital mask onto the substrate. At DTU Nanolab we have four different types of lithography available:
- UV Lithography: UV lithography is used for making features as small as about 1 micrometer
- DUV Stepper Lithography: DUV lithography is used for features as small as 200 nm
- E-beam Lithography: The smallest features can be made in our e-beam writers - about 10 nm
- Nano Imprint Lithography: for stamping without irradiation
Comparing lithography methods at DTU Nanolab
UV Lithography | DUV Stepper Lithography | E-beam Lithography | Nano Imprint Lithography | |
---|---|---|---|---|
Generel description | Pattern transfer via ultraviolet (UV) light | Pattern transfer via deep ultraviolet (DUV) light | Patterning by electron beam | Pattern transfer via hot embossing (HE) |
Pattern size range | ~1 µm and up (resist type, thickness, and pattern dependent) |
~200 nm and up (pattern type, shape and pitch dependent) |
~10-1000 nm (and larger at high currents) |
~20 nm and up |
Resist type |
UV sensitive:
|
DUV sensitive:
|
E-beam sensitive:
|
Imprint polymers:
|
Resist thickness range | ~0.5 µm to 200 µm | ~50 nm to 2 µm | ~30 nm to 1 µm | ~100 nm to 2 µm |
Typical exposure time | Mask aligner: 10-180 s per wafer Maskless aligner: 5-60 minutes per wafer |
Process dependent:
Throughput is up to 60 wafers/hour |
Process dependent:
Process time [s]: |
Process dependent, including heating/cooling rates |
Substrate size |
|
|
We have cassettes fitting:
Only one cassette can be loaded at a time |
|
Allowed materials | Any standard cleanroom material | Any standard cleanroom material |
Any standard cleanroom material, except:
|
Any standard cleanroom material |
Equipment and Process Pages
Pre-lithography
|
Coating
|
Exposure/design transfer
|
Development
|
Post-lithography
|
Lithography Tool Package Training
DTU Nanolab offers a Tool Package Training for Lithography (TPT Lithography). You are required to pass this course, in order to get access to the lithography equipment inside the DTU Nanolabs cleanroom facility. The course includes theory on lithographic processes and training videos for equipment operation. The theory part consists of lecture videos followed by quizzes for each section. Once completed successfully, you can do the online training that explains the operation for the specific lithography equipment you want to use in more detail. After completing the online training, you can request hands-on training for the equipment inside the cleanroom via training@nanolab.dtu.dk.
The course is available via DTU Learn. You sign up for the course by enrolling yourself in the course here.
Course Layout
- Online lecture videos (theory)
- Quizzes for each section
- Online training videos (equipment operation)
- Individual hands-on training
Individual hands-on training can be requested via training@nanolab.dtu.dk.
Learning objectives
- Coating
- Exposure
- Development
- Resist, substrates and pre-treatment
- Post-lithography steps
Qualifying Prerequisites
- Cleanroom safety course at DTU Nanolab
- Admission to the cleanroom must be obtained before the group training session
Course Responsible
- Jens Hindborg Hemmingsen
- Thomas Aarøe Anhøj
If you have questions you can contact us via lithography@nanolab.dtu.dk.
Knowledge and Information about Lithography