Specific Process Knowledge/Lithography/UVExposure Dose: Difference between revisions
Line 413: | Line 413: | ||
|rowspan="1"|PEB: 60 s at 110°C | |rowspan="1"|PEB: 60 s at 110°C | ||
Process | Process adopted from process logs. | ||
|- | |- | ||
Revision as of 09:58, 8 May 2017
Feedback to this page: click here
Exposure dose
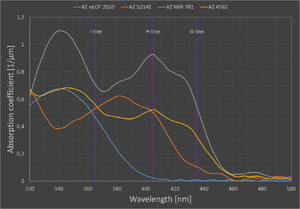
During exposure of the resist, the photoinitiator, or photo-active component, reacts with the exposure light, and starts the reaction that makes the resist develop in the developer. In a positive resist, it makes the resist become soluble in the developer. In a negative resist, usually assisted by thermal energy in the post-exposure bake, it makes the resist insoluble in the developer. The amount of light required to fully develop the resist in the development process, is the exposure dose. The optimal exposure dose is a function of many parameters, including the type of resist, the resist thickness, and the sensitivity of the resist.
The resist sensitivity is a measure of how efficiently it reacts to the exposure light. Spectral sensitivity is the sensitivity of the resist as a function of wavelength. It is usually given simply as the range from the wavelength below which absorption in the resist material makes lithography impractical to the wavelength at which the photoinitiator is no longer efficiently activated. The spectral sensitivity is listed in the Resist Overview. Within this range, the optical absorption is commonly used as a measure of sensitivity. A high absorption coefficient signifies a high sensitivity, as the light is absorbed by the photoinitiator. Because of spectral sensitivity, the optimal dose of a given resist type and thickness is also a function of the spectral distribution of the exposure light, i.e. the equipment used for the exposure, see table below. Made using a combination of experience, calculation, and assumption, the values given in the Relative exposure dose table may be used to estimate the dose for one equipment from the known dose on another equipment.
Due to reflection and refraction at the interface between the resist and the substrate, the optimal dose may also be a function of the type of substrate used. Unless otherwise stated, the exposure doses given here are for standard silicon wafers.
Apart from the already mentioned factors, the optimal dose also depends on the developer chemistry and the parameters used in the development process. Finally, the requirements to the lithographic process in terms of resolution, bias (line broadening), etch selectivity, side wall angle, etc. may narrow down, or widen, the process window. The exposure doses given in the sections below should be used as a starting point for individual fabrication process development.
Due to the process of bleaching, where the absorption of the resist changes during exposure, the exposure dose is unfortunately not always constant at different intensities of the exposure light. The exposure time is thus not always a linear function of the exposure intensity.
Lamp | Installed filter | Adjusted intensity | Filter options | |
---|---|---|---|---|
KS Aligner | 350 W Hg | i-line notch filter
365nm (FWHM = 7 nm) |
7 mW/cm2 @ 365 nm (Constant Intensity) |
|
Aligner: MA6 - 2 | 500 W Hg-Xe | i-line notch filter
365nm (FWHM = ? nm) |
The intensity is set by the user
~13 mW/cm2 @ 365 nm |
|
Aligner-6inch | 350 W Hg | SU-8 long-pass filter (50% i-line)
Broadband i-, h-, and g-line |
7 mW/cm2 @ 365 nm (Constant Power) |
|
The most powerful UV lines in the Hg spectrum are the i-, h-, and g-lines at 356 nm, 405 nm, and 435 nm wavelength, respectively. While the Hg lamp produces little or no intensity in the deep-UV (UV-C) range, the Hg-Xe lamp has increased output below 300 nm.
Calculating exposure time
The exposure dose, D [J/m2], is given by:
D = I x t ,
where I [W/m2] is the intensity of the exposure light, and t [s] is the exposure time. As the intensity is specific to the spectral sensitivity of the sensor used to measure the exposure light, and the exposure time is specific to the spectral distribution of the exposure light (cf. spectral sensitivity), this dose is specific to the combination of exposure source and optical sensor.
Given the optimum exposure dose, the exposure time is calculated as:
t = D / I .
It is important to keep in mind that this exposure time is valid only for a specific combination of exposure source and optical sensor, as well as for a specific development process.
Comparison: Relative exposure dose
KS Aligner | Aligner: MA6 - 2 | Aligner-6inch | |
---|---|---|---|
AZ 5214E | 1 | 1.15 1) | 0.5 |
AZ 4562 | 1 | 1.15 1) | 0.5 |
AZ MiR 701 | 1 | 1.15 1) | 0.2 |
AZ nLOF 2020 | 1 | 1.15 1) | 1 |
SU-8 | 1 | 1.15 1) | 0.6 - 1 |
1) Due to a difference in the sensitivity of the sensor used in calibration.
Exposure dose when using AZ 351B developer (NaOH)
KS Aligner (351B)
The KS Aligner has an i-line notch filter installed. This results in an exposure light peak around 365 nm with a FWHM of 7 nm. Dependent on the spectral sensitivity of the resist, the optimal dose may be increased compared to broadband exposure on the Aligner-6inch. Unless otherwise stated, the exposure doses given here are for standard silicon wafers.
Thickness | Dose | Development | Comments | |
---|---|---|---|---|
AZ 5214E | 1.5 µm | 35-49 mJ/cm2 | 60 s | Positive process |
2.2 µm | 56-70 mJ/cm2 | 70 s | ||
4.2 µm | ~140 mJ/cm2 | 3 minutes | ||
AZ 5214E | 1.5 µm | 21 mJ/cm2 | 60 s | Image reversal process.
Reversal bake: 100s at 110°C. |
2.2 µm | 24 mJ/cm2 | 70 s | ||
AZ 4562 | 10 µm | ~280 mJ/cm2 | 5 minutes | Multiple exposure with 10 s pauses is recommended. |
Additional information:
AZ 5214E image reversal
- 1.5 µm resist on boron glass: around 49 mJ/cm2 (supplied March 2013 by Morten Bo Lindholm Mikkelsen, DTU Nanotech).
Aligner-6inch (351B)
The Aligner-6inch has a long pass filter designed for SU-8 exposure installed. The SU-8 filter has no transmission in the 250-330 nm range, and close to full transmission in the 400-500 nm range. In the 350-370 nm range, the transmission is approximately 0.5. This results in a broadband exposure light consisting of the i-line (365 nm), the h-line (405 nm), and the g-line (435 nm) from the Hg spectrum. Dependent on the spectral sensitivity of the resist, the optimal dose may be decreased compared to i-line exposure on the KS-Aligner. Unless otherwise stated, the exposure doses given here are for standard silicon wafers.
Thickness | Dose | Development | Comments | |
---|---|---|---|---|
AZ 5214E | 1.5 µm | 17-25 mJ/cm2 | 60 s | Positive process |
AZ 5214E | 1.5 µm | 10.5 mJ/cm2 | 60 s | Image reversal process.
Reversal bake: 100s at 110°C. |
2.2 µm | 12 mJ/cm2 | 70 s | ||
AZ 4562 | 10 µm | ~140 mJ/cm2 | 5 minutes | Multiple exposure with 10s pauses is recommended. |
Exposure dose when using AZ 726 MIF developer (TMAH)
KS Aligner (726)
The KS Aligner has an i-line notch filter installed. This results in an exposure light peak around 365 nm with a FWHM of 7 nm. Dependent on the spectral sensitivity of the resist, the optimal dose may be increased compared to broadband exposure on the Aligner-6inch. Unless otherwise stated, the exposure doses given here are for standard silicon wafers.
Thickness | Dose | Development | Comments | |
---|---|---|---|---|
AZ 5214E | 1.5 µm | 60 mJ/cm2 | Single puddle, 60 s | Positive process |
2.2 µm | 75 mJ/cm2 | |||
4.2 µm | 140 mJ/cm2 | |||
AZ 4562 | 10 µm | 420-450 mJ/cm2 | Multiple puddle, 4 x 60 s | Multiple exposure with 10-15 s pauses is recommended. |
AZ MiR 701 | 1 µm | ~150 mJ/cm2 | Single puddle, 60 s | PEB: 60 s at 110°C
Preliminary results |
2 µm | ~175 mJ/cm2 | Single puddle, 60 s | ||
4 µm | ~200 mJ/cm2 | Single puddle, 60 s | PEB: 90 s at 110°C
Preliminary results | |
AZ nLOF 2020 | 2 µm | 84-112 mJ/cm2 | Single puddle, 60 s | PEB: 60 s at 110°C
Side wall angle ~15°. For lover angle, develop 30 s (~5°) |
Aligner: MA6 - 2 (726)
Unless otherwise stated, the exposure doses given here are for standard silicon wafers.
Not all thicknesses tested yet. Use Relative exposure dose table to estimate dose.
Thickness | Dose | Development | Comments | |
---|---|---|---|---|
AZ 5214E | 1.5 µm | 72 mJ/cm2 | Single puddle, 60 s | Positive process |
2.2 µm | 90 mJ/cm2 | Single puddle, 60 s | ||
AZ 5214E | 1.5 µm | 22? mJ/cm2 | Single puddle, 60 s | Image reversal process.
Reversal bake: 120s at 110°C. |
2.2 µm | 25 mJ/cm2 | Single puddle, 60 s | ||
AZ 4562 | 10 µm | 520-?? mJ/cm2 | Multiple puddle, 4 x 60 s | Multiple exposure with 10 s pauses is recommended.
Process not yet established. |
AZ MiR 701 | 1.5 µm | 169 mJ/cm2 | Single puddle, 60 s | PEB: 60 s at 110°C |
2 µm | ~200 mJ/cm2 | Single puddle, 60 s | ||
4 µm | ~280 mJ/cm2 | Single puddle, 60 s | PEB: 60 s at 110°C
Process adopted from process logs. | |
AZ nLOF 2020 | 1.5 µm | 104 mJ/cm2 | Single puddle, 30 s | PEB: 60 s at 110°C
Use 60 s development for lift-off |
Aligner-6inch (726)
The Aligner-6inch has a long pass filter designed for SU-8 exposure installed. The SU-8 filter has no transmission in the 250-330 nm range, and close to full transmission in the 400-500 nm range. In the 350-370 nm range, the transmission is approximately 0.5. This results in a broadband exposure light consisting of the i-line (365 nm), the h-line (405 nm), and the g-line (435 nm) from the Hg spectrum. Dependent on the spectral sensitivity of the resist, the optimal dose may be decreased compared to i-line exposure on the KS-Aligner. Unless otherwise stated, the exposure doses given here are for standard silicon wafers.
No process results. Use Relative exposure dose table to estimate dose.