Specific Process Knowledge/Back-end processing/Polymer Injection Molder: Difference between revisions
No edit summary |
|||
(63 intermediate revisions by 5 users not shown) | |||
Line 1: | Line 1: | ||
= | '''Feedback to this page''': '''[mailto:wetchemistry@nanolab.dtu.dk?Subject=Feed%20back%20from%20page%20http://labadviser.nanolab.dtu.dk/index.php/Specific_Process_Knowledge/Back-end_processing/Polymer_Injection_Molder click here]''' | ||
== Polymer injection molding == | |||
'''The Polymer Injection Molder is no more an open access tool has been moved to DTU Construct''' | |||
[[image:Imm.jpg|200x200px|right|thumb|Injection molding machine in the basement under the cleanroom]] | |||
The injection molder at DTU Nanolab is an Engel Victory Tech 80/45 which is a hydraulic machine with single motor. The machine is also equipped with a robot which can pick up finished samples and place them on a conveyor belt. See the table below for key capabilities of this machine. '''The user manual, user APV, technical information and contact information can be found in LabManager:''' | |||
The | |||
[http://www.labmanager.dtu.dk/function.php?module=Machine&view=view&mach=278 Polymer injection molding Info on LabManager] (Click 'Documents' tab to go to documents). | |||
==Equipment performance== | |||
The polymer injection molding machine at DTU Nanolab is a hydraulic system with the following capabilities: | |||
{| border="2" cellspacing="0" cellpadding="2" | {| border="2" cellspacing="0" cellpadding="2" | ||
Line 43: | Line 20: | ||
|style="background:WhiteSmoke; color:black"|<b>Value</b> | |style="background:WhiteSmoke; color:black"|<b>Value</b> | ||
|- | |- | ||
!style="background:silver; color:black" align="center" valign="center" rowspan="2"| | !style="background:silver; color:black" align="center" valign="center" rowspan="2"|General | ||
|style="background:LightGrey; color:black"| | |style="background:LightGrey; color:black"|Tools | ||
|style="background:WhiteSmoke; color:black"| | |style="background:WhiteSmoke; color:black"| | ||
Flat disc, Disc with Luer connectors, Microscope slide | |||
|- | |- | ||
|style="background:LightGrey; color:black"| | |style="background:LightGrey; color:black"|Clamping force | ||
|style="background:WhiteSmoke; color:black"| | |style="background:WhiteSmoke; color:black"| | ||
Up to 450 kN | |||
|- | |- | ||
!style="background:silver; color:black" align="center" valign="center" rowspan="2"| | !style="background:silver; color:black" align="center" valign="center" rowspan="2"|Processing temperatures | ||
|style="background:LightGrey; color:black"| | |style="background:LightGrey; color:black"|Mold temperature | ||
|style="background:WhiteSmoke; color:black"| | |style="background:WhiteSmoke; color:black"| | ||
~15°C to 140°C | |||
|- | |- | ||
|style="background:LightGrey; color:black"| | |style="background:LightGrey; color:black"|Heating cylinder | ||
|style="background:WhiteSmoke; color:black"| | |style="background:WhiteSmoke; color:black"| | ||
Absolute max: 350°C | |||
|- | |- | ||
!style="background:silver; color:black" align="center" valign="center" rowspan="3"| | !style="background:silver; color:black" align="center" valign="center" rowspan="3"|Molding parameters | ||
|style="background:LightGrey; color:black"| | |style="background:LightGrey; color:black"|Injection speed | ||
|style="background:WhiteSmoke; color:black"| | |style="background:WhiteSmoke; color:black"| | ||
Up to 53 cm<sup>3</sup>/s | |||
|- | |- | ||
| style="background:LightGrey; color:black"| | | style="background:LightGrey; color:black"|Injection pressure | ||
|style="background:WhiteSmoke; color:black"| | |style="background:WhiteSmoke; color:black"| | ||
Up to 2200 bar | |||
|- | |- | ||
| style="background:LightGrey; color:black"| | | style="background:LightGrey; color:black"|Process types | ||
|style="background:WhiteSmoke; color:black"| | |style="background:WhiteSmoke; color:black"| | ||
Constant or variable mold temperature | |||
|} | |} | ||
<br clear="all" /> | <br clear="all" /> | ||
== Polymers == | |||
At DTU Nanolab the following polymers are used routinely: | |||
*Topas 5013L-10<br> | |||
*Topas 8007S-04<br> | |||
*PP<br> | |||
*PMMA<br> | |||
Topas polymers are supplied by Nanolab. All other polymers are purchased by the users themselves. All polymers (and each individual grade of each polymer) must be approved for use at DTU Nanolab. If you would like to use a new polymer or a new grade of a certain polymer, please fill out the application form which can be found in LabManager by going to the 'Documents' tab of the 'Info' page for the Polymer Injection Molding machine. You can also click this direct link: [http://labmanager.dtu.dk/view_binary.php?fileId=2857 New_polymer_application.dotx]. | |||
When the polymer has been approved you will receive labels which must be used to label your polymer. All polymers left in the injection molding room must be marked with this official DTU Nanolab label. '''Polymers not labelled appropriately may be thrown out at any time'''. | |||
The easiest way to get an overview of polymers and processes used on the polymer injection molding machine is to go to LabManager and consult the [http://labmanager.dtu.dk/function.php?module=Processlog&view=editlog&machid=278 Process Log for the injection molding machine]. If you would like use a non-Nanolab polymer for a test, please contact the owner of the polymer and ask if you can have a sample. A complete list of all polymers in use at DTU Nanolab and who owns them can be found in LabManager on the Info page for the polymer injection molding machine on the 'Documents' tab. You can also click this direct link: [http://labmanager.dtu.dk/view_binary.php?fileId=3723 Approved_polymers_list.pdf]. | |||
==Process parameters and optimization== | |||
There are no standard injection molding processes because it varies significantly how users prefer to optimize their process and how they prioritize parameters such as polymer type, replication fidelity, dimensional accuracy, optical properties, residual stress and cycle time. However, browsing through the [http://labmanager.dtu.dk/function.php?module=Processlog&view=editlog&machid=278 Process Log] it's usually not a problem to find a program made for the polymer and tool at hand which can be used as a starting point. | |||
The injection moulding cycle consists of the steps outlined below. Click on each step to get a description of the most important process parameters for each step: | |||
#[[/MoldTemp|Mold heating setup]]<br> | |||
#[[/MoldClose|Closing mold]]<br> | |||
#[[/Injection|Injection]]<br> | |||
#[[/SwitchOver|Switch-over type]]<br> | |||
#[[/AfterPressure|After (holding) pressure]]<br> | |||
#[[/Cooling|Cooling]]<br> | |||
#[[/Dosing|Dosing (plastizising)]]<br> | |||
#[[/Demolding|Demolding]]<br> | |||
#[[/Eject|Ejection]]<br> | |||
#[[/Robot|Robot sample pickup]]<br> | |||
#[[/Nozzle|Nozzle settings]] | |||
#[[/Process|Process overview]] | |||
==Advanced process parameter optimization and features== | |||
This LabAdviser page is just a quick overview of the most important parameters and features. For a full description of parameters and machine features, please refer to the full operating manual from Engel. It can be found in LabManager under Equipment Info -> Polymer Injection Molding -> Documents -> Technical Documents -> EN-VC_Standard_dtu or by clicking this direct link: [http://labmanager.dtu.dk/view_binary.php?fileId=4388 EN-VC_Standard_dtu.pdf]. Please note that this manual refers to a slightly larger machine and some features that are not all available on DTU Nanolab's machine, but all general guidelines and descriptions of the user interface are valid. |
Latest revision as of 09:50, 26 January 2024
Feedback to this page: click here
Polymer injection molding
The Polymer Injection Molder is no more an open access tool has been moved to DTU Construct
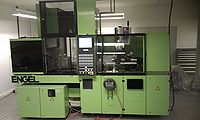
The injection molder at DTU Nanolab is an Engel Victory Tech 80/45 which is a hydraulic machine with single motor. The machine is also equipped with a robot which can pick up finished samples and place them on a conveyor belt. See the table below for key capabilities of this machine. The user manual, user APV, technical information and contact information can be found in LabManager:
Polymer injection molding Info on LabManager (Click 'Documents' tab to go to documents).
Equipment performance
The polymer injection molding machine at DTU Nanolab is a hydraulic system with the following capabilities:
Parameter | Value | |
---|---|---|
General | Tools |
Flat disc, Disc with Luer connectors, Microscope slide |
Clamping force |
Up to 450 kN | |
Processing temperatures | Mold temperature |
~15°C to 140°C |
Heating cylinder |
Absolute max: 350°C | |
Molding parameters | Injection speed |
Up to 53 cm3/s |
Injection pressure |
Up to 2200 bar | |
Process types |
Constant or variable mold temperature |
Polymers
At DTU Nanolab the following polymers are used routinely:
- Topas 5013L-10
- Topas 8007S-04
- PP
- PMMA
Topas polymers are supplied by Nanolab. All other polymers are purchased by the users themselves. All polymers (and each individual grade of each polymer) must be approved for use at DTU Nanolab. If you would like to use a new polymer or a new grade of a certain polymer, please fill out the application form which can be found in LabManager by going to the 'Documents' tab of the 'Info' page for the Polymer Injection Molding machine. You can also click this direct link: New_polymer_application.dotx.
When the polymer has been approved you will receive labels which must be used to label your polymer. All polymers left in the injection molding room must be marked with this official DTU Nanolab label. Polymers not labelled appropriately may be thrown out at any time.
The easiest way to get an overview of polymers and processes used on the polymer injection molding machine is to go to LabManager and consult the Process Log for the injection molding machine. If you would like use a non-Nanolab polymer for a test, please contact the owner of the polymer and ask if you can have a sample. A complete list of all polymers in use at DTU Nanolab and who owns them can be found in LabManager on the Info page for the polymer injection molding machine on the 'Documents' tab. You can also click this direct link: Approved_polymers_list.pdf.
Process parameters and optimization
There are no standard injection molding processes because it varies significantly how users prefer to optimize their process and how they prioritize parameters such as polymer type, replication fidelity, dimensional accuracy, optical properties, residual stress and cycle time. However, browsing through the Process Log it's usually not a problem to find a program made for the polymer and tool at hand which can be used as a starting point.
The injection moulding cycle consists of the steps outlined below. Click on each step to get a description of the most important process parameters for each step:
- Mold heating setup
- Closing mold
- Injection
- Switch-over type
- After (holding) pressure
- Cooling
- Dosing (plastizising)
- Demolding
- Ejection
- Robot sample pickup
- Nozzle settings
- Process overview
Advanced process parameter optimization and features
This LabAdviser page is just a quick overview of the most important parameters and features. For a full description of parameters and machine features, please refer to the full operating manual from Engel. It can be found in LabManager under Equipment Info -> Polymer Injection Molding -> Documents -> Technical Documents -> EN-VC_Standard_dtu or by clicking this direct link: EN-VC_Standard_dtu.pdf. Please note that this manual refers to a slightly larger machine and some features that are not all available on DTU Nanolab's machine, but all general guidelines and descriptions of the user interface are valid.