Specific Process Knowledge/Thin film deposition/ALD Picosun R200: Difference between revisions
(30 intermediate revisions by 2 users not shown) | |||
Line 2: | Line 2: | ||
'''Feedback to this page''': '''[mailto:labadviser@danchip.dtu.dk?Subject=Feed%20back%20from%20page%20http://labadviser.danchip.dtu.dk/index.php/ALD_Picosun_R200 click here]''' | '''Feedback to this page''': '''[mailto:labadviser@danchip.dtu.dk?Subject=Feed%20back%20from%20page%20http://labadviser.danchip.dtu.dk/index.php/ALD_Picosun_R200 click here]''' | ||
''This page is written by DTU Nanolab internal'' | |||
[[Category: Equipment|Thin film]] | [[Category: Equipment|Thin film]] | ||
Line 9: | Line 11: | ||
[[image:ALD.jpg|300x300px|right|thumb|ALD1, positioned in cleanroom F-2.]] | [[image:ALD.jpg|300x300px|right|thumb|ALD1, positioned in cleanroom F-2.]] | ||
The ALD1 (Picosun R200 ALD) tool is used to deposit a very thin layer of Al<sub>2</sub>O<sub>3</sub>, TiO<sub>2</sub> (amorphous or anatase) | The ALD1 (Picosun R200 ALD) tool is used to deposit a very thin layer of Al<sub>2</sub>O<sub>3</sub>, TiO<sub>2</sub> (amorphous or anatase) and HfO<sub>2</sub> on different samples. Layer can be up to 100 nm thick, see the table below. | ||
Each process is using two | Each process is using two different precursors. The reaction takes place in cycles. During each cycle, a very short pulse of each precursor is introduced into the ALD reaction chamber in turns, and in-between each precursor pulse the chamber is purged with nitrogen. All reactions have to take place on the sample surface, thus it is very important that each precursor is removed from the chamber before the next one is introduced. In that way, materials can be deposited atomic layer by atomic layer by ALD. | ||
In order to ensure that the ALD reactor has the same temperature everywhere, it has a dual chamber structure. The inner chamber is the | In order to ensure that the ALD reactor has the same temperature everywhere, it has a dual chamber structure. The inner chamber is the reactor chamber, and the outer chamber is a vacuum chamber that is isolating the reactor from room air. The space between the two chambers is called an intermediate space (IMS), and this is constantly purged with nitrogen. A sample holder is placed in the reactor chamber. | ||
When the reactor chamber is heated up or cooled down, it will take some time before the sample holder and the sample reaches the desired temperature. Thus, it is important to include a temperature stabilization time in the process recipes. | When the reactor chamber is heated up or cooled down, it will take some time before the sample holder and the sample reaches the desired temperature. Thus, it is important to include a temperature stabilization time in the process recipes. | ||
Line 19: | Line 21: | ||
The ALD deposition takes place in the reactor chamber. All precursor and nitrogen carrier gas lines are connected to the reactor chamber through separate gas lines. The precursor pulse time is controlled using special ALD valves, that allow very short precursors pulses to be introduced into the ALD reactor and at the same time allow a constant nitrogen purge. | The ALD deposition takes place in the reactor chamber. All precursor and nitrogen carrier gas lines are connected to the reactor chamber through separate gas lines. The precursor pulse time is controlled using special ALD valves, that allow very short precursors pulses to be introduced into the ALD reactor and at the same time allow a constant nitrogen purge. | ||
The ALD reaction takes place under vacuum, thus a vacuum pump is connected to the bottom of the ALD reactor. The pump is located in the basement. | The ALD reaction takes place under vacuum, thus a vacuum pump is connected to the bottom of the ALD reactor chamber. The pump is located in the basement. | ||
The liquid precursors (H<sub>2</sub>O, TMA, TiCl<sub>4</sub> and | The liquid precursors (H<sub>2</sub>O, TMA, TiCl<sub>4</sub> and TEMAHf) are located in the cabinet below the ALD chamber. When these precursors are not in use, the manual valves have to be closed. Only four of the precursors (normally <sub>2</sub>O, TMA, TEMAHf and TiCl<sub>4</sub>) can be connected at the same time. Ozone is generated by use of an ozone generator that is located on the side of the machine. | ||
It is possible to change the sample holder, so that ALD deposition can take place on different samples, e.g. a small wafer batch or a number of smaller samples. Samples are loaded manually into the sample holder by use of a tweezer. However, for some materials the uniformity will only be good for the top sample(s) in a minibatch holder. | It is possible to change the sample holder, so that ALD deposition can take place on different samples, e.g. a small wafer batch (up to five wafers at a time) or a number of smaller samples. Samples are loaded manually into the sample holder by use of a tweezer. However, for some materials the uniformity will only be good for the top sample(s) in a minibatch holder. | ||
A short presentation with some information about the ALD tool can be found [[Media:ProcessMeeting ALD 2013-12-06_1.pdf|here]]. | A short presentation with some information about the ALD tool can be found [[Media:ProcessMeeting ALD 2013-12-06_1.pdf|here]]. | ||
Line 38: | Line 40: | ||
*[[/Al2O3 deposition using ALD|Al<sub>2</sub>O<sub>3</sub> deposition using ALD 1]] | *[[/Al2O3 deposition using ALD|Al<sub>2</sub>O<sub>3</sub> deposition using ALD 1]] | ||
*[[/TiO2 deposition using ALD|TiO<sub>2</sub> deposition using ALD 1]] | *[[/TiO2 deposition using ALD|TiO<sub>2</sub> deposition using ALD 1]] | ||
*[[/ZnO deposition using ALD|ZnO deposition using ALD 1]] | *[[/ZnO deposition using ALD|ZnO deposition using ALD 1. ''Obsolete - ZnO should now be deposited in ALD2'']] | ||
*[[/AZO deposition using ALD|Al-doped ZnO (AZO) deposition using ALD 1]] | *[[/AZO deposition using ALD|Al-doped ZnO (AZO) deposition using ALD 1. ''Obsolete - AZO should now be deposited in ALD2'']] | ||
*[[/HfO2 deposition using ALD|HfO<sub>2</sub> deposition using ALD 1]] | <!--*[[/HfO2 deposition using ALD|HfO<sub>2</sub> deposition using ALD 1]]--> | ||
*[[/HfO2 deposition using ALD new page|HfO<sub>2</sub> deposition using ALD 1 | *[[/HfO2 deposition using ALD new page|HfO<sub>2</sub> deposition using ALD 1]] | ||
==Equipment performance and process related parameters== | ==Equipment performance and process related parameters== | ||
Line 53: | Line 55: | ||
|style="background:LightGrey; color:black"|ALD (atomic layer deposition) of | |style="background:LightGrey; color:black"|ALD (atomic layer deposition) of | ||
|style="background:WhiteSmoke; color:black"| | |style="background:WhiteSmoke; color:black"| | ||
*Al<sub>2</sub>O<sub>3</sub> | *Al<sub>2</sub>O<sub>3</sub> (amorphous) | ||
*TiO<sub>2</sub> (amorphous or anatase) | *TiO<sub>2</sub> (amorphous or anatase) | ||
*HfO<sub>2</sub> | *HfO<sub>2</sub> (polycrystalline) | ||
|- | |- | ||
!style="background:silver; color:black" align="center" valign="center" rowspan="2"|Performance | !style="background:silver; color:black" align="center" valign="center" rowspan="2"|Performance | ||
Line 64: | Line 64: | ||
*Al<sub>2</sub>O<sub>3</sub>: ~ 0.075 - 0.097 nm/cycle (Using the "Al2O3" recipe, depending on temperature) | *Al<sub>2</sub>O<sub>3</sub>: ~ 0.075 - 0.097 nm/cycle (Using the "Al2O3" recipe, depending on temperature) | ||
*TiO<sub>2</sub>: 0.041 - 0.061 nm/cycle (Using the "TiO2" recipe, depending on temperature) | *TiO<sub>2</sub>: 0.041 - 0.061 nm/cycle (Using the "TiO2" recipe, depending on temperature) | ||
*HfO<sub>2</sub>: 0.0827 nm/cycle | |||
*HfO<sub>2</sub>: 0. | |||
|- | |- | ||
|style="background:LightGrey; color:black"|Thickness | |style="background:LightGrey; color:black"|Thickness | ||
Line 71: | Line 70: | ||
*Al<sub>2</sub>O<sub>3</sub>: 0 - 100 nm | *Al<sub>2</sub>O<sub>3</sub>: 0 - 100 nm | ||
*TiO<sub>2</sub>: 0 - 100 nm | *TiO<sub>2</sub>: 0 - 100 nm | ||
*HfO<sub>2</sub>: 0 - 100 nm | |||
*HfO<sub>2</sub>: 0 - | <i>As the purpose of ALD 1 is to deposit very thin and uniform layers, the allowed deposition thickness is limited to 100 nm, and it is not allowed to do more depositions on the same sample(s) to deposit thicker layers than 100 nm. Deposition of thicker layers is not allowed, because this will occupy the machine for long time and thus make it available for less users. Long depositions also cause issues and with flakes and particles, which means that the chamber and the pump line will have to be cleaned or changed quite often. Furthermore, the delivery time on precursors is usually quite long. So when you make a sample design, you should avoid steps, where you need to deposit thicker layers than 100 nm with ALD, or you can consider, if the same material can be deposited using other machines in the cleanroom.</i> | ||
|- | |- | ||
!style="background:silver; color:black" align="center" valign="center" rowspan="2"|Process parameter range | !style="background:silver; color:black" align="center" valign="center" rowspan="2"|Process parameter range | ||
|style="background:LightGrey; color:black"|Temperature | |style="background:LightGrey; color:black"|Temperature window | ||
|style="background:WhiteSmoke; color:black"| | |style="background:WhiteSmoke; color:black"| | ||
*Al<sub>2</sub>O<sub>3</sub>: 150 - 300 <sup>o</sup>C | *Al<sub>2</sub>O<sub>3</sub>: 150 - 300 <sup>o</sup>C | ||
*Amorphous TiO<sub>2</sub>: 100-150 <sup>o</sup>C | *Amorphous TiO<sub>2</sub>: 100 - 150 <sup>o</sup>C | ||
*Anatase TiO<sub>2</sub>: 300-350 | *Anatase TiO<sub>2</sub>: 300 - 350 <sup>o</sup>C | ||
*HfO<sub>2</sub>: 150 - 350 <sup>o</sup>C | |||
*HfO<sub>2</sub>: 150- | |||
|- | |- | ||
|style="background:LightGrey; color:black"|Precursors | |style="background:LightGrey; color:black"|Precursors | ||
|style="background:WhiteSmoke; color:black"| | |style="background:WhiteSmoke; color:black"| | ||
*TMA | *TMA | ||
*TiCl<sub>4</sub> | *TiCl<sub>4</sub> | ||
*H<sub>2</sub>O | *H<sub>2</sub>O | ||
*O<sub>3</sub> | *O<sub>3</sub> | ||
*O<sub>2</sub> | *O<sub>2</sub> - Not available at the moment | ||
* | *TEMAHf | ||
|- | |- | ||
!style="background:silver; color:black" align="center" valign="center" rowspan="3"|Substrates | !style="background:silver; color:black" align="center" valign="center" rowspan="3"|Substrates | ||
Line 99: | Line 96: | ||
*1-5 100 mm wafers | *1-5 100 mm wafers | ||
*1-5 150 mm wafers | *1-5 150 mm wafers | ||
*1-3 200 mm wafers | |||
*Several smaller samples | *Several smaller samples | ||
|- | |- | ||
Line 108: | Line 106: | ||
*Al, Al<sub>2</sub>O<sub>3</sub> | *Al, Al<sub>2</sub>O<sub>3</sub> | ||
*Ti, TiO<sub>2</sub> | *Ti, TiO<sub>2</sub> | ||
*Other metals (use dedicated carrier | *Other metals (use dedicated carrier wafers) | ||
*III-V materials (use dedicated carrier | *III-V materials (use dedicated carrier wafers) | ||
*Polymers (depending on the melting point/deposition temperature, use carrier | *Polymers (depending on the melting point/deposition temperature, use carrier wafers) | ||
|- | |- | ||
|} | |} |
Latest revision as of 09:57, 30 April 2024
ALD1
Feedback to this page: click here
This page is written by DTU Nanolab internal
ALD - Atomic layer deposition
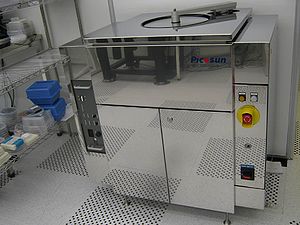
The ALD1 (Picosun R200 ALD) tool is used to deposit a very thin layer of Al2O3, TiO2 (amorphous or anatase) and HfO2 on different samples. Layer can be up to 100 nm thick, see the table below.
Each process is using two different precursors. The reaction takes place in cycles. During each cycle, a very short pulse of each precursor is introduced into the ALD reaction chamber in turns, and in-between each precursor pulse the chamber is purged with nitrogen. All reactions have to take place on the sample surface, thus it is very important that each precursor is removed from the chamber before the next one is introduced. In that way, materials can be deposited atomic layer by atomic layer by ALD.
In order to ensure that the ALD reactor has the same temperature everywhere, it has a dual chamber structure. The inner chamber is the reactor chamber, and the outer chamber is a vacuum chamber that is isolating the reactor from room air. The space between the two chambers is called an intermediate space (IMS), and this is constantly purged with nitrogen. A sample holder is placed in the reactor chamber.
When the reactor chamber is heated up or cooled down, it will take some time before the sample holder and the sample reaches the desired temperature. Thus, it is important to include a temperature stabilization time in the process recipes.
The ALD deposition takes place in the reactor chamber. All precursor and nitrogen carrier gas lines are connected to the reactor chamber through separate gas lines. The precursor pulse time is controlled using special ALD valves, that allow very short precursors pulses to be introduced into the ALD reactor and at the same time allow a constant nitrogen purge.
The ALD reaction takes place under vacuum, thus a vacuum pump is connected to the bottom of the ALD reactor chamber. The pump is located in the basement.
The liquid precursors (H2O, TMA, TiCl4 and TEMAHf) are located in the cabinet below the ALD chamber. When these precursors are not in use, the manual valves have to be closed. Only four of the precursors (normally 2O, TMA, TEMAHf and TiCl4) can be connected at the same time. Ozone is generated by use of an ozone generator that is located on the side of the machine.
It is possible to change the sample holder, so that ALD deposition can take place on different samples, e.g. a small wafer batch (up to five wafers at a time) or a number of smaller samples. Samples are loaded manually into the sample holder by use of a tweezer. However, for some materials the uniformity will only be good for the top sample(s) in a minibatch holder.
A short presentation with some information about the ALD tool can be found here.
The user manual, the user APV and contact information can be found in LabManager:
Process information
- Standard recipes on the ALD 1 tool
- Advanced recipes involving fabrication of multilayers
- Al2O3 deposition using ALD 1
- TiO2 deposition using ALD 1
- ZnO deposition using ALD 1. Obsolete - ZnO should now be deposited in ALD2
- Al-doped ZnO (AZO) deposition using ALD 1. Obsolete - AZO should now be deposited in ALD2
- HfO2 deposition using ALD 1
Equipment | ALD1 | |
---|---|---|
Purpose | ALD (atomic layer deposition) of |
|
Performance | Deposition rates |
|
Thickness |
As the purpose of ALD 1 is to deposit very thin and uniform layers, the allowed deposition thickness is limited to 100 nm, and it is not allowed to do more depositions on the same sample(s) to deposit thicker layers than 100 nm. Deposition of thicker layers is not allowed, because this will occupy the machine for long time and thus make it available for less users. Long depositions also cause issues and with flakes and particles, which means that the chamber and the pump line will have to be cleaned or changed quite often. Furthermore, the delivery time on precursors is usually quite long. So when you make a sample design, you should avoid steps, where you need to deposit thicker layers than 100 nm with ALD, or you can consider, if the same material can be deposited using other machines in the cleanroom. | |
Process parameter range | Temperature window |
|
Precursors |
| |
Substrates | Batch size |
|
Allowed materials |
|