Specific Process Knowledge/Lithography/SU-8: Difference between revisions
Created page with " SU8 is an epoxy based negative i-line photoresist with a high contrast. More then 10:1 aspect ratio imaging with vertical sidewalls is one of the widely used properties of ..." |
|||
(60 intermediate revisions by 5 users not shown) | |||
Line 1: | Line 1: | ||
{{:Specific Process Knowledge/Lithography/authors_generic}} | |||
'''Feedback to this page''': '''[mailto:labadviser@nanolab.dtu.dk?Subject=Feed%20back%20from%20page%20http://labadviser.nanolab.dtu.dk/index.php/Specific_Process_Knowledge/Lithography/SU-8 click here]''' | |||
[[Category: Lithography|Resist]] | |||
[[Category: Resist|SU-8]] | |||
__TOC__ | |||
==Resist description== | |||
SU-8 is an epoxy based negative i-line photoresist with a high contrast. More then 10:1 aspect ratio imaging with vertical sidewalls is one of the widely used properties of this resist. It also has high chemical, plasma and temperature resistance after curing which makes it well suited for permanent use applications. | |||
<span style="color:red">'''Note:''' Since the SU-8 is epoxy-based, users are required to take the mandatory epoxy safety course "Personlig sikkerhed ved arbejde med epoxy". Registration to this course can be found on [https://www.inside.dtu.dk/en/medarbejder/hr-og-arbejdsmiljoe/kompetenceudvikling/kursusoversigt_overside/kursusoversigt/arbejdsmiljoe-og-beredskabskurser/epoxy-kursus?fs=1 DTU Inside]</span> - '''requires login''' | |||
In the cleanroom the SU-8 2000 product line is widely used, where the '''SU-8 2005''', '''SU-8 2035''', and '''SU-8 2075''' are supplied by Nanolab. Other resist formulations can be used, but has to be ordered by the user. | |||
'''Process recommendations:''' | |||
* A standard process consist of spinning, soft bake, exposure, post-exposure bake and development. Please notice that the entire process must be done continuously, meaning that it is not recommendable to spin the resist and then wait until the next day before exposing | |||
* Exposure using radiation above 350 nm is recommended | |||
* Controlled soft and post-exposure bakes are recommended and must be optimized for the specific application, but baseline parameters which can be used as a starting point will be given | |||
==Pretreatment== | ==Pretreatment== | ||
* To dehydrate the surface, bake in 250C oven at least 30 min | * To dehydrate the surface, bake in 250C oven at least 30 min - the longer the bake, the better. Baking overnight is recommended | ||
* Another dehydration step can be done in the HMDS oven using recipe 9. This does not expose the wafers to HMDS but instead makes a | * Another dehydration step can be done in the HMDS oven using recipe 9. This does not expose the wafers to HMDS but instead makes a bake-out at reduced pressure | ||
==Spinning== | ==Spinning== | ||
SU-8 resist is designed to produce low defect coatings over a very broad range of films thickness. [[Specific Process Knowledge/Lithography/Coaters#Spin_Coater:_RCD8|Spin Coater: RCD8]] is dedicated to spin all SU-8 resist formulations. | |||
'''Safety rules:'''<br> | |||
To keep the cleanroom safe and odor free during the spinning, please follow the following rules: | |||
* Always use point exhaust above the place, where you handle the resist | |||
* When you move the wafers to the dedicated hotplates, always carry them in a closed container | |||
'''Recommenced spin coating conditions:'''<br> | |||
* | * Dispense manually from bottle/syringe for the thin resists or use a syringe dispense system for the thick resists | ||
* | * Use static dispense; approximately 1 ml of SU-8 per inch of substrate diameter | ||
* For | * For SU-8 layers thicker then 100 um use two-step spin coating procedure: | ||
** spread cycle | ** 5 second spread cycle 500 rpm, acceleration 100 rpm/s, following by: | ||
** thickness definition cycle with the final spin speed | ** thickness definition cycle with the final spin speed | ||
** layer uniformity of the thick films can be improved by using a rotation cover(Gyrset), but remember the speed limitation | ** layer uniformity of the thick films can be improved by using a rotation cover (Gyrset), but remember the speed limitation is then 3000 rpm | ||
* For | * For SU-8 layers thinner then 10 um the spread cycle can be omitted to improve the uniformity of the films | ||
* A rotation cover(Gyrset) can be also used in case you | '''Spin curves:''' | ||
** | Spin curves for SU-8 2002 and SU-8 2005 (from the old KS Spinner): | ||
[[File:SU8 spinCurves 2002 2005.png|640px|thumb|right|Spin curves for SU-8 2002 and SU-8 2005.]] | |||
* A rotation cover (Gyrset) can be also used in case you need to spin less than 1 um resist film | |||
** 3000 rpm, 300 rpm/s, 30 sec with gyrset gives approximately 850 nm film thickness, when using SU-8 2002 | |||
* Another way to get a thinner film is to dilute SU-8 2002 in cyclopentanone solution | |||
** 120 nm film: dilute 25 ml SU-8 2002 in 80 ml cyclopentanone, spin at 7000 rpm | |||
** 60-80 nm film: dilute 5 ml SU-8 2002 in 32 ml cyclopentanone, spin at 2000 - 7000 rpm | |||
<br clear="all" /> | |||
==Baking== | |||
SU-8 baking can be divided in 2 steps: | |||
#Soft bake step after spinning | |||
#Post exposure bake after exposure | |||
The goal of the soft bake step is to reduce the amount of solvent in the photoresist layer. The applied heat evaporates the solvent from the resist film. The soft bake step is be done on dedicated SU-8 hotplates, and is usually done in one or two steps with a 5-8 deg/min temperature ramp between the steps.<br> | |||
The soft bake temperature is typically between 20°C and 110°C, and the soft bake time depends on the film thickness. After soft bake the resist should be firm to the touch (not sticky), in order to be used in the exposure tools. | |||
The goal of the | The goal of the post exposure bake is to increase the polymerization reaction (the cross-linking). The post exposure step can be done on the same hotplates as the soft bake step, with the temperature range between 20°C and 120°C, and with temperature ramping of 5-8 deg/min. | ||
'''NB:''' It is important to do the post exposure bake immediately after exposure, to limit photoinitiator diffusion into unexposed areas. | |||
It is important to do the post exposure bake immediately after exposure to limit photoinitiator diffusion into | |||
==Exposure== | ==Exposure== | ||
Exposing SU-8 is done using light sources at 375 nm or lower. SU-8 is not (practically) sensitive to 405 nm light and above. | |||
Duration of the UV-exposure depends of resist thickness, | '''Exposure in mask aligner:'''<br> | ||
Duration of the UV-exposure depends of resist thickness, and if the UV exposure becomes too long, the heating at the interface between the mask and resist can cause formation of "hard skin" at the surface of the SU-8; the so-called T-topping phenomena. The rule of thumb is, that if the exposure dose exceeds 250-300 mJ/cm<sup>2</sup>, it is recommended to do multiple exposures instead, with a waiting time of 15 - 20 s between the exposure steps, to allow the resist cool down. | |||
==Developing== | ==Developing== | ||
'''Development speed:''' | |||
*Puddle development in mr DEV 600 (PGMEA): ~20 µm/min | |||
*Immersion development in mr DEV 600 (PGMEA): ~20 µm/min | |||
'''Puddle development:'''<br> | |||
Puddle development can be done in the Spin coater: gamma ebeam & UV using one of the predefined development sequences. The development is a puddle development, and it requires that the substrate does not have any through holes - if the substrate has holes, you need to use immersion development instead. | |||
After | '''Immersion development:'''<br> | ||
Immersion development can be done in the [[Specific_Process_Knowledge/Lithography/Development#SU8-Developer|Developer:_SU8_(Wet_Bench)]]: | |||
#The development time is dependent on the layer thickness. Minimum development time in "First" bath is 1 min per 20 µm resist film thickness | |||
#After development the substrate must be rinsed with IPA on both sides for ~30 sec. White traces during rinsing indicates incomplete development of SU-8 | |||
#Finally the substrates are dried in air in the drying bath or with a nitrogen gun | |||
==Phd. work on the topic== | |||
==PhD dissertations== | |||
PhD Thesis by Thomas Anhøj (February 2007) on process optimization of 40 µm thick SU-8 25 for lab-on-a-chip. | |||
*[https://orbit.dtu.dk/en/publications/fabrication-of-high-aspect-ratio-su-8-structures-for-integrated-s Fabrication of high aspect ratio SU-8 structures for integrated spectrometers] | |||
*[https://labmanager.dtu.dk/view_binary.php?class=MiscDocument&id=4&name=TAA_Defense_070420.pdf Slides from defence] - '''requires login''' |
Latest revision as of 12:08, 1 February 2024
This section, including all images and pictures, is created by DTU Nanolab staff unless otherwise stated.
Feedback to this page: click here
Resist description
SU-8 is an epoxy based negative i-line photoresist with a high contrast. More then 10:1 aspect ratio imaging with vertical sidewalls is one of the widely used properties of this resist. It also has high chemical, plasma and temperature resistance after curing which makes it well suited for permanent use applications.
Note: Since the SU-8 is epoxy-based, users are required to take the mandatory epoxy safety course "Personlig sikkerhed ved arbejde med epoxy". Registration to this course can be found on DTU Inside - requires login
In the cleanroom the SU-8 2000 product line is widely used, where the SU-8 2005, SU-8 2035, and SU-8 2075 are supplied by Nanolab. Other resist formulations can be used, but has to be ordered by the user.
Process recommendations:
- A standard process consist of spinning, soft bake, exposure, post-exposure bake and development. Please notice that the entire process must be done continuously, meaning that it is not recommendable to spin the resist and then wait until the next day before exposing
- Exposure using radiation above 350 nm is recommended
- Controlled soft and post-exposure bakes are recommended and must be optimized for the specific application, but baseline parameters which can be used as a starting point will be given
Pretreatment
- To dehydrate the surface, bake in 250C oven at least 30 min - the longer the bake, the better. Baking overnight is recommended
- Another dehydration step can be done in the HMDS oven using recipe 9. This does not expose the wafers to HMDS but instead makes a bake-out at reduced pressure
Spinning
SU-8 resist is designed to produce low defect coatings over a very broad range of films thickness. Spin Coater: RCD8 is dedicated to spin all SU-8 resist formulations.
Safety rules:
To keep the cleanroom safe and odor free during the spinning, please follow the following rules:
- Always use point exhaust above the place, where you handle the resist
- When you move the wafers to the dedicated hotplates, always carry them in a closed container
Recommenced spin coating conditions:
- Dispense manually from bottle/syringe for the thin resists or use a syringe dispense system for the thick resists
- Use static dispense; approximately 1 ml of SU-8 per inch of substrate diameter
- For SU-8 layers thicker then 100 um use two-step spin coating procedure:
- 5 second spread cycle 500 rpm, acceleration 100 rpm/s, following by:
- thickness definition cycle with the final spin speed
- layer uniformity of the thick films can be improved by using a rotation cover (Gyrset), but remember the speed limitation is then 3000 rpm
- For SU-8 layers thinner then 10 um the spread cycle can be omitted to improve the uniformity of the films
Spin curves:
Spin curves for SU-8 2002 and SU-8 2005 (from the old KS Spinner):
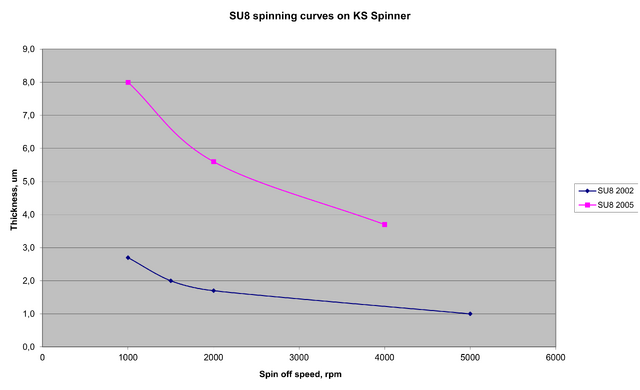
- A rotation cover (Gyrset) can be also used in case you need to spin less than 1 um resist film
- 3000 rpm, 300 rpm/s, 30 sec with gyrset gives approximately 850 nm film thickness, when using SU-8 2002
- Another way to get a thinner film is to dilute SU-8 2002 in cyclopentanone solution
- 120 nm film: dilute 25 ml SU-8 2002 in 80 ml cyclopentanone, spin at 7000 rpm
- 60-80 nm film: dilute 5 ml SU-8 2002 in 32 ml cyclopentanone, spin at 2000 - 7000 rpm
Baking
SU-8 baking can be divided in 2 steps:
- Soft bake step after spinning
- Post exposure bake after exposure
The goal of the soft bake step is to reduce the amount of solvent in the photoresist layer. The applied heat evaporates the solvent from the resist film. The soft bake step is be done on dedicated SU-8 hotplates, and is usually done in one or two steps with a 5-8 deg/min temperature ramp between the steps.
The soft bake temperature is typically between 20°C and 110°C, and the soft bake time depends on the film thickness. After soft bake the resist should be firm to the touch (not sticky), in order to be used in the exposure tools.
The goal of the post exposure bake is to increase the polymerization reaction (the cross-linking). The post exposure step can be done on the same hotplates as the soft bake step, with the temperature range between 20°C and 120°C, and with temperature ramping of 5-8 deg/min.
NB: It is important to do the post exposure bake immediately after exposure, to limit photoinitiator diffusion into unexposed areas.
Exposure
Exposing SU-8 is done using light sources at 375 nm or lower. SU-8 is not (practically) sensitive to 405 nm light and above.
Exposure in mask aligner:
Duration of the UV-exposure depends of resist thickness, and if the UV exposure becomes too long, the heating at the interface between the mask and resist can cause formation of "hard skin" at the surface of the SU-8; the so-called T-topping phenomena. The rule of thumb is, that if the exposure dose exceeds 250-300 mJ/cm2, it is recommended to do multiple exposures instead, with a waiting time of 15 - 20 s between the exposure steps, to allow the resist cool down.
Developing
Development speed:
- Puddle development in mr DEV 600 (PGMEA): ~20 µm/min
- Immersion development in mr DEV 600 (PGMEA): ~20 µm/min
Puddle development:
Puddle development can be done in the Spin coater: gamma ebeam & UV using one of the predefined development sequences. The development is a puddle development, and it requires that the substrate does not have any through holes - if the substrate has holes, you need to use immersion development instead.
Immersion development:
Immersion development can be done in the Developer:_SU8_(Wet_Bench):
- The development time is dependent on the layer thickness. Minimum development time in "First" bath is 1 min per 20 µm resist film thickness
- After development the substrate must be rinsed with IPA on both sides for ~30 sec. White traces during rinsing indicates incomplete development of SU-8
- Finally the substrates are dried in air in the drying bath or with a nitrogen gun
Phd. work on the topic
PhD dissertations
PhD Thesis by Thomas Anhøj (February 2007) on process optimization of 40 µm thick SU-8 25 for lab-on-a-chip.