Specific Process Knowledge/Lithography/LiftOff: Difference between revisions
No edit summary |
|||
(137 intermediate revisions by 7 users not shown) | |||
Line 1: | Line 1: | ||
{{cc-nanolab}} | |||
'''Feedback to this page''': '''[mailto:labadviser@nanolab.dtu.dk?Subject=Feed%20back%20from%20page%20http://labadviser.nanolab.dtu.dk/index.php?title=Specific_Process_Knowledge/Lithography/LiftOff click here]''' | |||
[[Category: Equipment|Lithography liftoff]] | |||
[[Category: Lithography|Liftoff]] | |||
__TOC__ | |||
=Lift-off Comparison Table= | |||
{|border="1" cellspacing="1" cellpadding="10" style="text-align:left;" | |||
!colspan="2" border="none" style="background:silver; color:black;" align="center"|Equipment | |||
|style="background:WhiteSmoke; color:black" align="center"|<b>[[Specific Process Knowledge/Lithography/LiftOff#Lift-off_wet_bench_07|Lift-off]]</b> | |||
|style="background:WhiteSmoke; color:black" align="center"|<b>[http://labmanager.danchip.dtu.dk/function.php?module=Machine&view=view&mach=370 Fume hood 03: Solvents]</b> - '''requires login''' | |||
|- | |||
!style="background:silver; color:black;" align="center"|Purpose | |||
|style="background:LightGrey; color:black"| | |||
|style="background:WhiteSmoke; color:black"| | |||
Lift-off of e.g. metal using | |||
* UV resists | |||
* e-beam resists | |||
|style="background:WhiteSmoke; color:black"| | |||
General solvent work, including lift-off. | |||
'''DO NOT''' use other fume hoods for lift-off! | |||
* <s>Fume hood 04: Solvents</s> | |||
* <s>Fume hood 08: III-V solvents</s> | |||
* <s>Fume hood 09: UV development</s> | |||
* <s>Fume hood 10: e-beam development</s> | |||
|- | |||
!style="background:silver; color:black;" align="center"|Bath chemical | |||
|style="background:LightGrey; color:black"| | |||
|style="background:WhiteSmoke; color:black"| | |||
NMP (Remover 1165) / Rinse in IPA | |||
|style="background:WhiteSmoke; color:black"| | |||
User defined | |||
|- | |||
!style="background:silver; color:black" align="center" valign="center" rowspan="2"|Process parameters | |||
|style="background:LightGrey; color:black"|Process temperature | |||
|style="background:WhiteSmoke; color:black"| | |||
*Heating of the bath is possible. | |||
*The heating has been limited to 60°C | |||
|style="background:WhiteSmoke; color:black"| | |||
Heating is possible using portable hotplate or portable ultrasonic bath | |||
|- | |||
|style="background:LightGrey; color:black"|Ultrasonic agitation | |||
|style="background:WhiteSmoke; color:black"| | |||
*Continuous or pulsed | |||
*The power may be varied | |||
|style="background:WhiteSmoke; color:black"| | |||
Ultrasonic agitation is possible using portable ultrasonic bath | |||
|- | |||
!style="background:silver; color:black" align="center" valign="center" rowspan="3"|Substrates | |||
|style="background:LightGrey; color:black"|Substrate size | |||
|style="background:WhiteSmoke; color:black"| | |||
* 100 mm wafers | |||
* 150 mm wafers | |||
|style="background:WhiteSmoke; color:black"| | |||
* In principle any, typically chips | |||
|- | |||
| style="background:LightGrey; color:black"|Allowed materials | |||
|style="background:WhiteSmoke; color:black"| | |||
*Silicon or glass wafers | |||
*Film or patterning of all except Type IV (Pb, Te) | |||
|style="background:WhiteSmoke; color:black"| | |||
Any cleanroom material | |||
|- | |||
|style="background:LightGrey; color:black"|Batch | |||
|style="background:WhiteSmoke; color:black" align="center"| | |||
1 - 25 | |||
|style="background:WhiteSmoke; color:black" align="center"| | |||
1 | |||
|- | |||
|} | |||
<br clear="all" /> | |||
=Lift-off process= | |||
[[File:Lift-off process new.png|thumb|Illustration of the lift-off process.]] | |||
The lift-off process is used to pattern a material that can be deposited as a film on a substrate. The material is patterned by depositing the film on top of a patterned masking material, which is then dissolved, thus leaving only parts of the substrate covered in the material. Although this may in theory be done using any combination of mask and material, the most common is using photoresist as a lift-off mask for metal. | |||
The image to the left shows a schematic of the lift off process. | |||
#The substrate is coated with the masking material | |||
#The masking material is patterned. The mask must be a negative image of the desired material pattern | |||
#The material is deposited on top of both mask and substrate. The mask sidewall slope should be negative in order to prevent the material covering the sidewalls during deposition | |||
#The masking material is dissolved, thus lifting part of the deposited material | |||
#The remaining material forms the desired pattern on the substrate | |||
A successful lift-off process is dependent on many factors, including: | |||
*Resist sidewall angle | |||
*Resist thickness relative to the deposited material | |||
*Layout of the design, especially the regions surrounding the device(s) | |||
If the resist sidewall angle is positive, the deposited material will coat the sidewall, thus preventing the solvent from reaching and dissolving the resist. Ultrasonic agitation may be able to pierce the material deposited on top of resist, allowing lift-off. A a positive sidewall angle will typically result in a very slow lift-off process, as well as line edge roughness of the deposited material. A negative, or at least vertical, resist sidewall is usually needed for a successful lift-off process. | |||
If the resist layer used for lift-off is too thin compared to the deposited layer, solvent access to the resist may be limited, due to partial or full coverage of the sidewalls. This would result in a slow lift-off, possibly with line edge roughness of the deposited material. As a rule of thumb, the resist should be 5-10 times thicker than the deposited material. | |||
Small, tightly packed structures result in a very fast lift-off process. It is usually the big, uncovered areas between or around the device(s) that limit the lift-off speed. The less of the deposited material is to remain on the substrate after lift-off, the longer the sample has to spend in the lift-off solvent while resist under the deposited material is being dissolved and transported out. During the design of the pattern used for lift-off, it should be considered to fill any voids between devices with lift-off assisting dummy structures (e.g. hatching or squares/circles), in order to punctuate the open spaces, and allow for multiple, parallel starting points. Consider also if the edge of the substrate (exclusion zone) could be left covered with the deposited material. | |||
'''Please note:''' | |||
At the DTU Nanolab cleanroom facility, it is only allowed to do lift-off in: | |||
*<b>[[Specific Process Knowledge/Lithography/LiftOff#Lift-off_wet_bench_07|Lift-off (Wet bench 07)]]</b> | |||
*<b>[http://labmanager.danchip.dtu.dk/function.php?module=Machine&view=view&mach=370 Fume hood 03: Solvents]</b> - '''requires login''' | |||
Other fume hoods, such as Fume hood 04: Solvents, Fume hood 09: UV development, and Fume hood 10: e-beam development, should not be used for lift-off. For an overview of the fume hoods, click [[Specific_Process_Knowledge/Overview_of_Fume_Hoods|'''here''']]. | |||
<br clear="all" /> | <br clear="all" /> | ||
=Lift-off at Nanolab= | |||
==Lift-off wet bench 07== | |||
[[Image:Lift_off.jpg|300x300px|thumb|Lift-off wet bench in D-3]] | |||
The user manual, and contact information can be found in [http://labmanager.danchip.dtu.dk/function.php?module=Machine&view=view&mach=384 LabManager] - '''requires login''' | |||
{|border="1" cellspacing="1" cellpadding="10" style="text-align:left;" | |||
!colspan="2" border="none" style="background:silver; color:black;" align="center"|Equipment | |||
|style="background:WhiteSmoke; color:black"; align="center";|'''Lift-off''' | |||
|- | |||
!style="background:silver; color:black;"|Purpose | |||
|style="background:LightGrey; color:black"| | |||
|style="background:WhiteSmoke; color:black"| | |||
*Lift-off of UV or E-beam resist | |||
*Resist strip of wafers with metal | |||
|- | |||
!style="background:silver; color:black;"|Bath chemical | |||
|style="background:LightGrey; color:black"| | |||
|style="background:WhiteSmoke; color:black"| | |||
*NMP (Remover 1165) | |||
*Rinse in IPA | |||
|- | |||
!style="background:silver; color:black" valign="center" rowspan="2"|Process parameters | |||
|style="background:LightGrey; color:black"|Process temperature | |||
|style="background:WhiteSmoke; color:black"| | |||
Heating of the bath is possible. | |||
The heating has been limited to 65°C | |||
|- | |||
|style="background:LightGrey; color:black"|Ultrasonic agitation | |||
|style="background:WhiteSmoke; color:black"| | |||
Continuous or pulsed | |||
The power may be varied | |||
|- | |||
!style="background:silver; color:black" valign="center" rowspan="3"|Substrates | |||
|style="background:LightGrey; color:black"|Substrate size | |||
|style="background:WhiteSmoke; color:black"| | |||
* 100 mm wafers | |||
* 150 mm wafers | |||
|- | |||
| style="background:LightGrey; color:black"|Allowed materials | |||
|style="background:WhiteSmoke; color:black"| | |||
Silicon or glass wafers | |||
Film or patterning of all but Type IV (Pb, Te) | |||
|- | |||
|style="background:LightGrey; color:black"|Batch | |||
|style="background:WhiteSmoke; color:black"| | |||
1 - 25 | |||
|- | |||
|} | |||
<br clear="all" /> | |||
== Process information == | |||
Lift-off is used for lift-off using resists that are soluble in NMP (''N''-Methyl-Pyrrolidone), supplied in the cleanroom as "Remover 1165". Both AZ 5214E and AZ nLOF are soluble in NMP. | |||
For information on processing of AZ nLOF, or image reversal of AZ 5214E, see here: [[Specific_Process_Knowledge/Lithography/Resist/UVresist|Resist Overview]]. | |||
<br clear="all" /> | |||
==Poor metal (TiPt) adhesion/ Metal delaminating after lift-off== | |||
''This experiment was done by Gustav E. Skands(ges@sbtinstruments.com) in May 2024'' | |||
This entry details an observed issue with metal adhesion during a Ti/Pt deposition (10/160 nm) and lift-off process within DTU Nanolab. The employed photoresist was TI Spray from MicroChemicals, which is believed (but not confirmed) to share many properties with AZ5214E. The thickness of the resist was approximately 5 µm, and it was spray coated onto the substrate using the Spray Coater. | |||
'''Root cause:''' | |||
The core of the adhesion challenge was linked to the choice of photoresist developer. 2.08% TMAH facilitated excellent resist pattern development, but subsequent metal adhesion during the deposition process was consistently poor, observed across both Wordentec and both Temescal systems. This occurred despite the absence of any visible residues on the substrate surface. Attempts to enhance adhesion, including a descum procedure using 70 mL/min O2 and 70 mL/min N2, 150W, 5 minutes, prior to deposition, were unsuccessful. | |||
'''Solution:''' | |||
Changing the developer to AZ351B (2 minutes development time in beaker) in the process provided significant improvements. Although AZ351B exhibited reduced selectivity in dissolving the soluble vs. insoluble resist, thereby compromising the precision of the resist pattern, it considerably improved the adhesion properties of the deposited metal. | |||
A dual developer approach—using TMAH (3x 60s development in Developer: TMAH UV-lithography followed by a 30 second development step in AZ351B—was therefore implemented. This approach leveraged the high-resolution patterning capability of TMAH and the superior adhesion characteristics provided by AZ351B. | |||
The different adhesion properties observed with the two developers suggest underlying molecular interactions that may inhibit or promote metal-substrate bonding. It is hypothesized that TMAH may leave molecular residues that, although not detectable through optical inspection, could create a barrier to adhesion at the molecular level. Conversely, AZ351B appears to modify or clear these residues, thereby enhancing adhesion. | |||
A descum step of 70 mL/min O2 and 70 mL/min N2, 150W, 5 minutes, was still performed immediately before deposition. However, it is unknown if this has an effect. | |||
Process temperature considerations | |||
The process incorporated a deposition temperature of 50°C, which was maintained without further comparative analysis against room temperature deposition due to the successful outcomes achieved and considerations of operational cost efficiency. | |||
==Poor metal (TiAu) adhesion/ Metal delaminating after lift-off== | |||
''This experiment was done by Mathias Zambach (zambach@fysik.dtu.dk) in June 2024'' | |||
'''Problem:''' Mathias experienced the delamination of TiAu after the lift-off process, see the image. | |||
'''Solution:''' Adding a descum step (70 ml/min O2, 70 ml/min N2, 150W, 5 min) right before metal depositions. | |||
[[File:Delamination of TiAu.jpg|thumb]] | |||
The process flow: | |||
1.) 2 um nLOF coating | |||
2.) Exposure | |||
3.) Development of nLOF | |||
'''4.) 5 min descum (70 ml/min O2, 70 ml/min N2, 150W, 5 min) was done right before TiAu deposition''' | |||
5.) 10 nm Ti depositing with 2 A/s by Temescal | |||
6.) 200 nm Au depositing with 2 A/s by Temescal | |||
7.) Lift-off (approx. 45 min) | |||
By adding step 4.) 5 min Descum, the problem with the delamination of metals was solved. |
Latest revision as of 14:48, 30 July 2024
The contents on this page, including all images and pictures, was created by DTU Nanolab staff unless otherwise stated.
Feedback to this page: click here
Lift-off Comparison Table
Equipment | Lift-off | Fume hood 03: Solvents - requires login | |
---|---|---|---|
Purpose |
Lift-off of e.g. metal using
|
General solvent work, including lift-off. DO NOT use other fume hoods for lift-off!
| |
Bath chemical |
NMP (Remover 1165) / Rinse in IPA |
User defined | |
Process parameters | Process temperature |
|
Heating is possible using portable hotplate or portable ultrasonic bath |
Ultrasonic agitation |
|
Ultrasonic agitation is possible using portable ultrasonic bath | |
Substrates | Substrate size |
|
|
Allowed materials |
|
Any cleanroom material | |
Batch |
1 - 25 |
1 |
Lift-off process
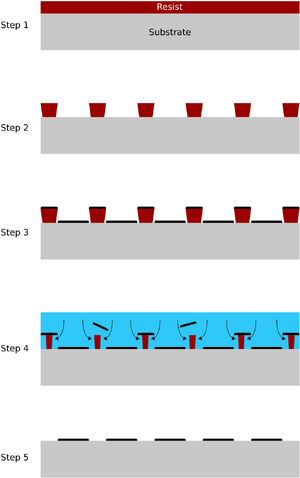
The lift-off process is used to pattern a material that can be deposited as a film on a substrate. The material is patterned by depositing the film on top of a patterned masking material, which is then dissolved, thus leaving only parts of the substrate covered in the material. Although this may in theory be done using any combination of mask and material, the most common is using photoresist as a lift-off mask for metal.
The image to the left shows a schematic of the lift off process.
- The substrate is coated with the masking material
- The masking material is patterned. The mask must be a negative image of the desired material pattern
- The material is deposited on top of both mask and substrate. The mask sidewall slope should be negative in order to prevent the material covering the sidewalls during deposition
- The masking material is dissolved, thus lifting part of the deposited material
- The remaining material forms the desired pattern on the substrate
A successful lift-off process is dependent on many factors, including:
- Resist sidewall angle
- Resist thickness relative to the deposited material
- Layout of the design, especially the regions surrounding the device(s)
If the resist sidewall angle is positive, the deposited material will coat the sidewall, thus preventing the solvent from reaching and dissolving the resist. Ultrasonic agitation may be able to pierce the material deposited on top of resist, allowing lift-off. A a positive sidewall angle will typically result in a very slow lift-off process, as well as line edge roughness of the deposited material. A negative, or at least vertical, resist sidewall is usually needed for a successful lift-off process.
If the resist layer used for lift-off is too thin compared to the deposited layer, solvent access to the resist may be limited, due to partial or full coverage of the sidewalls. This would result in a slow lift-off, possibly with line edge roughness of the deposited material. As a rule of thumb, the resist should be 5-10 times thicker than the deposited material.
Small, tightly packed structures result in a very fast lift-off process. It is usually the big, uncovered areas between or around the device(s) that limit the lift-off speed. The less of the deposited material is to remain on the substrate after lift-off, the longer the sample has to spend in the lift-off solvent while resist under the deposited material is being dissolved and transported out. During the design of the pattern used for lift-off, it should be considered to fill any voids between devices with lift-off assisting dummy structures (e.g. hatching or squares/circles), in order to punctuate the open spaces, and allow for multiple, parallel starting points. Consider also if the edge of the substrate (exclusion zone) could be left covered with the deposited material.
Please note:
At the DTU Nanolab cleanroom facility, it is only allowed to do lift-off in:
- Lift-off (Wet bench 07)
- Fume hood 03: Solvents - requires login
Other fume hoods, such as Fume hood 04: Solvents, Fume hood 09: UV development, and Fume hood 10: e-beam development, should not be used for lift-off. For an overview of the fume hoods, click here.
Lift-off at Nanolab
Lift-off wet bench 07
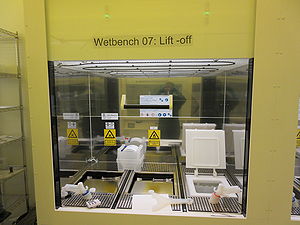
The user manual, and contact information can be found in LabManager - requires login
Equipment | Lift-off | |
---|---|---|
Purpose |
| |
Bath chemical |
| |
Process parameters | Process temperature |
Heating of the bath is possible. The heating has been limited to 65°C |
Ultrasonic agitation |
Continuous or pulsed The power may be varied | |
Substrates | Substrate size |
|
Allowed materials |
Silicon or glass wafers Film or patterning of all but Type IV (Pb, Te) | |
Batch |
1 - 25 |
Process information
Lift-off is used for lift-off using resists that are soluble in NMP (N-Methyl-Pyrrolidone), supplied in the cleanroom as "Remover 1165". Both AZ 5214E and AZ nLOF are soluble in NMP.
For information on processing of AZ nLOF, or image reversal of AZ 5214E, see here: Resist Overview.
Poor metal (TiPt) adhesion/ Metal delaminating after lift-off
This experiment was done by Gustav E. Skands(ges@sbtinstruments.com) in May 2024
This entry details an observed issue with metal adhesion during a Ti/Pt deposition (10/160 nm) and lift-off process within DTU Nanolab. The employed photoresist was TI Spray from MicroChemicals, which is believed (but not confirmed) to share many properties with AZ5214E. The thickness of the resist was approximately 5 µm, and it was spray coated onto the substrate using the Spray Coater.
Root cause: The core of the adhesion challenge was linked to the choice of photoresist developer. 2.08% TMAH facilitated excellent resist pattern development, but subsequent metal adhesion during the deposition process was consistently poor, observed across both Wordentec and both Temescal systems. This occurred despite the absence of any visible residues on the substrate surface. Attempts to enhance adhesion, including a descum procedure using 70 mL/min O2 and 70 mL/min N2, 150W, 5 minutes, prior to deposition, were unsuccessful.
Solution: Changing the developer to AZ351B (2 minutes development time in beaker) in the process provided significant improvements. Although AZ351B exhibited reduced selectivity in dissolving the soluble vs. insoluble resist, thereby compromising the precision of the resist pattern, it considerably improved the adhesion properties of the deposited metal.
A dual developer approach—using TMAH (3x 60s development in Developer: TMAH UV-lithography followed by a 30 second development step in AZ351B—was therefore implemented. This approach leveraged the high-resolution patterning capability of TMAH and the superior adhesion characteristics provided by AZ351B.
The different adhesion properties observed with the two developers suggest underlying molecular interactions that may inhibit or promote metal-substrate bonding. It is hypothesized that TMAH may leave molecular residues that, although not detectable through optical inspection, could create a barrier to adhesion at the molecular level. Conversely, AZ351B appears to modify or clear these residues, thereby enhancing adhesion.
A descum step of 70 mL/min O2 and 70 mL/min N2, 150W, 5 minutes, was still performed immediately before deposition. However, it is unknown if this has an effect.
Process temperature considerations The process incorporated a deposition temperature of 50°C, which was maintained without further comparative analysis against room temperature deposition due to the successful outcomes achieved and considerations of operational cost efficiency.
Poor metal (TiAu) adhesion/ Metal delaminating after lift-off
This experiment was done by Mathias Zambach (zambach@fysik.dtu.dk) in June 2024
Problem: Mathias experienced the delamination of TiAu after the lift-off process, see the image.
Solution: Adding a descum step (70 ml/min O2, 70 ml/min N2, 150W, 5 min) right before metal depositions.
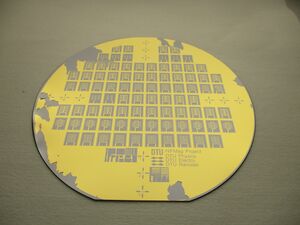
The process flow:
1.) 2 um nLOF coating
2.) Exposure
3.) Development of nLOF
4.) 5 min descum (70 ml/min O2, 70 ml/min N2, 150W, 5 min) was done right before TiAu deposition
5.) 10 nm Ti depositing with 2 A/s by Temescal
6.) 200 nm Au depositing with 2 A/s by Temescal
7.) Lift-off (approx. 45 min)
By adding step 4.) 5 min Descum, the problem with the delamination of metals was solved.