Specific Process Knowledge/Lithography/Development: Difference between revisions
(54 intermediate revisions by 3 users not shown) | |||
Line 1: | Line 1: | ||
{{cc-nanolab}} | |||
[[Category: Equipment |Lithography development]] | '''Feedback to this page''': '''[mailto:labadviser@nanolab.dtu.dk?Subject=Feed%20back%20from%20page%20http://labadviser.nanolab.dtu.dk/index.php?title=Specific_Process_Knowledge/Lithography/Development click here]''' | ||
[[Category: Equipment|Lithography development]] | |||
[[Category: Lithography|Development]] | [[Category: Lithography|Development]] | ||
__TOC__ | |||
==Development Comparison Table== | ==Development Comparison Table== | ||
{| border=" | {|border="1" cellspacing="1" cellpadding="10" style="text-align:left;" | ||
!colspan="2" border="none" style="background:silver; color:black;" align="center"|Equipment | !colspan="2" border="none" style="background:silver; color:black;" align="center"|Equipment | ||
|style="background:WhiteSmoke; color:black"|<b>[[Specific_Process_Knowledge/Lithography/Development#SU8 | |style="background:WhiteSmoke; color:black"|<b>[[Specific_Process_Knowledge/Lithography/Development#Developer: SU8 (Wet Bench)|Developer: SU8 (Wet bench)]]</b> | ||
|style="background:WhiteSmoke; color:black"|<b>[[Specific_Process_Knowledge/Lithography/Development#Developer: E-beam|Developer: E-beam]]</b> | |style="background:WhiteSmoke; color:black"|<b>[[Specific_Process_Knowledge/Lithography/Development#Developer: E-beam 02|Developer: E-beam 02]]</b> | ||
|style="background:WhiteSmoke; color:black"|<b>[[Specific_Process_Knowledge/Lithography/Development#Developer:_TMAH_Manual|Developer: TMAH Manual]]</b> | |style="background:WhiteSmoke; color:black"|<b>[[Specific_Process_Knowledge/Lithography/Development#Developer:_TMAH_Manual 02|Developer: TMAH Manual 02]]</b> | ||
|style="background:WhiteSmoke; color:black"|<b>[[Specific_Process_Knowledge/Lithography/Development#Developer_TMAH_UV-lithography|Developer: TMAH UV-lithography]]</b> | |style="background:WhiteSmoke; color:black"|<b>[[Specific_Process_Knowledge/Lithography/Development#Developer_TMAH_UV-lithography|Developer: TMAH UV-lithography]]</b> | ||
|style="background:WhiteSmoke; color:black"|<b>[[Specific_Process_Knowledge/Lithography/ | |style="background:WhiteSmoke; color:black"|<b>[[Specific_Process_Knowledge/Lithography/Development/DUV_developer#Developer:_TMAH_Stepper|Developer: TMAH Stepper]]</b> | ||
|- | |- | ||
Line 71: | Line 75: | ||
Spray/Puddle | Spray/Puddle | ||
|style="background:WhiteSmoke; color:black"| | |style="background:WhiteSmoke; color:black"| | ||
Puddle | |||
|style="background:WhiteSmoke; color:black"| | |style="background:WhiteSmoke; color:black"| | ||
Puddle | Puddle | ||
Line 79: | Line 83: | ||
|style="background:LightGrey; color:black"|Handling | |style="background:LightGrey; color:black"|Handling | ||
|style="background:WhiteSmoke; color:black"| | |style="background:WhiteSmoke; color:black"| | ||
Single wafer carrier | *Single wafer carrier | ||
*Chip bucket | |||
*100 mm carrier for up to 6 wafers | |||
|style="background:WhiteSmoke; color:black"| | |style="background:WhiteSmoke; color:black"| | ||
*Vacuum chuck for 100 mm & 150 mm substrates | *Vacuum chuck for 100 mm & 150 mm substrates | ||
Line 137: | Line 143: | ||
|style="background:WhiteSmoke; color:black"| | |style="background:WhiteSmoke; color:black"| | ||
*100 mm wafers | * Chips | ||
* 50 mm wafers | |||
* 100 mm wafers | |||
* 150 mm wafers | |||
* 200 mm wafers | |||
|style="background:WhiteSmoke; color:black"| | |style="background:WhiteSmoke; color:black"| | ||
* Chips (5mm to 2") | * Chips (5mm to 2") | ||
Line 373: | Line 383: | ||
--> | --> | ||
==SU8 | ==Developer: SU8 (Wet Bench)== | ||
The SU8 | [[Image:SU8dev.JPG|300x300px|right|thumb|The Developer: SU8(Wet Bench)is located in E-4 room.]] | ||
The SU8-Developer bench is a manually operated wet bench for submersion development of SU-8 photoresist in PGMEA (supplied in the cleanroom as mr-Dev 600). The development process is in two stages; one bath (FIRST) to dissolve the bulk of the resist, and a second, cleaner bath (FINAL) to finish the development. The development time is controlled manually by the user. After development, the substrates are rinsed with IPA in dedicated IPA bath and put for drying in the empty bath. | |||
The user manual, user APV, and contact information can be found in [http://labmanager.dtu.dk/function.php?module=Machine&view=view&mach=509 LabManager: Developer: SU8(Wet Bench)] - '''requires login''' | |||
===Process information=== | ===Process information=== | ||
Several aspects of the outcome of SU-8 processing are affected by the development process. The lithographic resolution is affected by the time between PEB (post-exposure bake) and development, as the cross-linking process continues in the interface between exposed and unexposed regions even at room temperature. Cracks in the structures is affected by two things; the development time, and how much has previously been developed in the developer bath. Cracking is worse with longer development time, and worst in a new developer bath. The effect of the developer use quickly saturates (5-10 wafers). Finally, the stability of fine structures (high aspect ratio) is affected by the rinse after development, as the lower surface tension of IPA compared to PGMEA reduces pattern collapse during drying. | Several aspects of the outcome of SU-8 processing are affected by the development process. The lithographic resolution is affected by the time between PEB (post-exposure bake) and development, as the cross-linking process continues in the interface between exposed and unexposed regions even at room temperature. Cracks in the structures is affected by two things; the development time, and how much has previously been developed in the developer bath. Cracking is worse with longer development time, and worst in a new developer bath. The effect of the developer use quickly saturates (5-10 wafers). Finally, the stability of fine structures (high aspect ratio) is affected by the rinse after development, as the lower surface tension of IPA compared to PGMEA reduces pattern collapse during drying. | ||
Development time is strongly dependent on the SU-8 thickness. | Development time is strongly dependent on the SU-8 thickness. | ||
*Minimum development time: 1 min per | *Minimum development time: 1 min per 20 µm in FIRST | ||
Suggestions: | Suggestions: | ||
*2-5µm: 2 min. in FIRST; 2 min. in FINAL | *2-5µm: 2 min. in FIRST; 2 min. in FINAL | ||
Line 394: | Line 408: | ||
=== Equipment performance and process related parameters === | === Equipment performance and process related parameters === | ||
{| border=" | {|border="1" cellspacing="1" cellpadding="10" style="text-align:left;" | ||
!style="background:silver; color:black;" align="center" width="60"|Purpose | !style="background:silver; color:black;" align="center" width="60"|Purpose | ||
Line 436: | Line 449: | ||
|style="background:WhiteSmoke; color:black"| | |style="background:WhiteSmoke; color:black"| | ||
*100 mm wafers | *100 mm wafers | ||
*150 mm wafer | *150 mm wafers, check the liquid level in the baths | ||
*200 mm wafer, check the liquid level in the baths | |||
|- | |- | ||
| style="background:LightGrey; color:black"|Allowed materials | | style="background:LightGrey; color:black"|Allowed materials | ||
Line 448: | Line 462: | ||
|- | |- | ||
|} | |} | ||
<br clear="all" /> | <br clear="all" /> | ||
==Developer: E-beam== | ==Developer: E-beam 02== | ||
[[Image:IMG 2464.JPG|300×300px|right|thumb|Developer: E-beam is located in E-4]] | [[Image:IMG 2464.JPG|300×300px|right|thumb|Developer: E-beam 02 is located in E-4]] | ||
Developer: E-beam 02 is a manually operated, single substrate puddle developer. It uses the ZED-N50 or AR 600-50 developers and IPA for rinsing. The substrates are loaded manually one by one into the developer. Developer dispense, puddle time, IPA rinse, and drying is then performed automatically by the equipment. | |||
'''[https://www.youtube.com/watch?v=btinNzYnLnY Training video]''' (for Developer: TMAH Manual, but it is the same model) | '''[https://www.youtube.com/watch?v=btinNzYnLnY Training video]''' (for Developer: TMAH Manual, but it is the same model) | ||
The user manual, user APV, and contact information can be found in [http://labmanager.dtu.dk/function.php?module=Machine&view=view&mach=324 LabManager] - '''requires login''' | |||
===Process information=== | ===Process information=== | ||
All recipes use the following structure: | |||
#Pressurize the developer canister | |||
#Dispense puddle while rotating substrate slowly | |||
#Puddle development while not rotating | |||
#Agitate substrate once per 15 seconds by rotating slowly for 1 second | |||
#Spin off developer | |||
#Clean substrate with IPA | |||
#Dry substrate and chamber with nitrogen | |||
Multi-puddle recipes repeat steps 2-5 for the given number of puddles. | |||
''' | '''Process recipes'''<br> | ||
N50 recipes have the letter "N" in them. AR-600-50 recipes have the letter "A" in them. The number is the development time in seconds: | |||
* | *01 Rinse | ||
*02 N 15 | |||
*03 N 30 | |||
*04 N 60 | |||
*05 N 90 | |||
*06 N 120 | |||
*07 N 180 | |||
*08 N 300 | |||
*09 N 600 | |||
*10 N 2x60 | |||
*11 N 5x60 | |||
*12 A 15 | |||
*13 A 30 | |||
*14 A 60 | |||
*15 A 90 | |||
*16 A 120 | |||
*17 A 180 | |||
*18 A 300 | |||
*19 A 600 | |||
*20 A 2x60 | |||
*21 A 5x60 | |||
=== Equipment performance and process related parameters === | === Equipment performance and process related parameters === | ||
{| border=" | {|border="1" cellspacing="1" cellpadding="10" style="text-align:left;" | ||
|- | |- | ||
Line 504: | Line 524: | ||
|- | |- | ||
!style="background:silver; color:black; | !style="background:silver; color:black;" width="60"|Developer | ||
|style="background:LightGrey; color:black"| | |style="background:LightGrey; color:black"| | ||
|style="background:WhiteSmoke; color:black"| | |style="background:WhiteSmoke; color:black"| | ||
*AR 600 - | *AR 600-50 | ||
*ZED N-50 | *ZED N-50 | ||
|- | |- | ||
!style="background:silver; color:black" align="center" valign="center" rowspan="2"|Method | !style="background:silver; color:black" align="center" valign="center" rowspan="2"|Method | ||
|style="background:LightGrey; color:black"|Development | |style="background:LightGrey; color:black"|Development | ||
|style="background:WhiteSmoke; color:black"| | |style="background:WhiteSmoke; color:black"| | ||
Puddle | |||
|- | |- | ||
|style="background:LightGrey; color:black"|Handling | |style="background:LightGrey; color:black"|Handling | ||
|style="background:WhiteSmoke; color:black"| | |style="background:WhiteSmoke; color:black"| | ||
* | *Chip chuck for chips | ||
* | *Non-vacuum chuck for 2" wafers | ||
*Non-vacuum chuck for 100 mm and 150 mm wafers | |||
*Non-vacuum chuck for 200 mm wafers | |||
|- | |- | ||
!style="background:silver; color:black" align="center" valign="center" rowspan="3"|Process parameters | !style="background:silver; color:black" align="center" valign="center" rowspan="3"|Process parameters | ||
Line 527: | Line 549: | ||
|style="background:LightGrey; color:black"|Agitation | |style="background:LightGrey; color:black"|Agitation | ||
|style="background:WhiteSmoke; color:black"| | |style="background:WhiteSmoke; color:black"| | ||
1 second rotational agitation at 30 rpm every 15 seconds | |||
|- | |- | ||
|style="background:LightGrey; color:black"|Rinse | |style="background:LightGrey; color:black"|Rinse | ||
Line 536: | Line 558: | ||
|style="background:LightGrey; color:black"|Substrate size | |style="background:LightGrey; color:black"|Substrate size | ||
|style="background:WhiteSmoke; color:black"| | |style="background:WhiteSmoke; color:black"| | ||
* Chips | *Chips | ||
* 2" wafers | *2" wafers | ||
* 100 mm wafers | *100 mm wafers | ||
* 150 mm wafers | *150 mm wafers | ||
*200 mm wafers | |||
|- | |- | ||
| style="background:LightGrey; color:black"|Allowed materials | | style="background:LightGrey; color:black"|Allowed materials | ||
Line 546: | Line 569: | ||
*Film, or pattern, of all materials except Type IV | *Film, or pattern, of all materials except Type IV | ||
|- | |- | ||
|style="background:LightGrey; color:black"|Batch | |style="background:LightGrey; color:black"|Batch size | ||
|style="background:WhiteSmoke; color:black"| | |style="background:WhiteSmoke; color:black"| | ||
1 | 1 | ||
Line 554: | Line 577: | ||
<br clear="all" /> | <br clear="all" /> | ||
==Developer: TMAH Manual== | ==Developer: TMAH Manual 02== | ||
[[Image:IMG 2464.JPG|300×300px|right|thumb|Developer: TMAH Manual is located in E-4]] | [[Image:IMG 2464.JPG|300×300px|right|thumb|Developer: TMAH Manual 02 is located in E-4]] | ||
Developer: TMAH Manual 02 is a manually operated, single substrate or chip puddle developer. It uses the TMAH based AZ 726 MIF developer (2.38 % TMAH in water with a small amount of wetting agent). The substrates or chips are loaded manually one by one into the developer. Developer dispense, puddle time, water rinse, and drying is performed automatically by the equipment. | |||
'''[https://www.youtube.com/watch?v=btinNzYnLnY Training video]''' | |||
The user manual, user APV, and contact information can be found in [http://labmanager.dtu.dk/function.php?module=Machine&view=view&mach=324 LabManager] - '''requires login''' | |||
===Process information=== | ===Process information=== | ||
All recipes use the following structure: | |||
#Pressurize the TMAH canister | |||
#Dispense puddle while rotating substrate slowly | |||
#Puddle development while not rotating | |||
#Agitate substrate once per 15 seconds by rotating slowly for 1 second | |||
#Spin off developer | |||
#Clean substrate and chamber with DI water | |||
#Dry substrate and chamber with nitrogen | |||
Multi-puddle recipes repeat steps 2-5 for the given number of puddles. | |||
''' | |||
'''Process recipes'''<br> | |||
* | SP: Single-puddle<br> | ||
MP: Multi-puddle | |||
*01 Rinse | |||
*02 SP 15 | |||
*03 SP 30 | |||
*04 SP 60 | |||
*05 SP 90 | |||
*06 SP 120 | |||
*07 SP 300 | |||
*08 MP 2x60 | |||
*09 MP 5x60 | |||
*91 SP test | |||
*92 MP test | |||
=== Equipment performance and process related parameters === | === Equipment performance and process related parameters === | ||
{| border=" | {|border="1" cellspacing="1" cellpadding="10" style="text-align:left;" | ||
Line 589: | Line 625: | ||
|style="background:LightGrey; color:black"| | |style="background:LightGrey; color:black"| | ||
|style="background:WhiteSmoke; color:black"| | |style="background:WhiteSmoke; color:black"| | ||
Development of: | Development of UV resists: | ||
*AZ nLOF | *AZ nLOF | ||
*AZ MiR 701 | *AZ MiR 701 | ||
*AZ 5214E | *AZ 5214E | ||
*AZ 4562 | *AZ 4562 | ||
Development of DUV resists: | |||
*KRF M230Y | |||
*KRF M35G | |||
|- | |- | ||
!style="background:silver; color:black;" align="center" width="60"|Developer | !style="background:silver; color:black;" align="center" width="60"|Developer | ||
|style="background:LightGrey; color:black"| | |style="background:LightGrey; color:black"| | ||
|style="background:WhiteSmoke; color:black"| | |style="background:WhiteSmoke; color:black"| | ||
AZ 726 MIF | AZ 726 MIF<br> | ||
(2.38% TMAH in water) | (2.38% TMAH in water) | ||
|- | |- | ||
Line 606: | Line 643: | ||
|style="background:LightGrey; color:black"|Development | |style="background:LightGrey; color:black"|Development | ||
|style="background:WhiteSmoke; color:black"| | |style="background:WhiteSmoke; color:black"| | ||
Puddle | |||
|- | |- | ||
|style="background:LightGrey; color:black"|Handling | |style="background:LightGrey; color:black"|Handling | ||
|style="background:WhiteSmoke; color:black"| | |style="background:WhiteSmoke; color:black"| | ||
*Chip chuck for chips and 2" wafers | *Chip chuck for chips and 2" wafers | ||
*Non-vacuum chuck for 100 mm and 150 mm wafers | |||
|- | |- | ||
!style="background:silver; color:black" align="center" valign="center" rowspan="3"|Process parameters | !style="background:silver; color:black" align="center" valign="center" rowspan="3"|Process parameters | ||
Line 621: | Line 657: | ||
|style="background:LightGrey; color:black"|Agitation | |style="background:LightGrey; color:black"|Agitation | ||
|style="background:WhiteSmoke; color:black"| | |style="background:WhiteSmoke; color:black"| | ||
1 second rotational agitation at 30 rpm every 15 seconds | |||
|- | |- | ||
|style="background:LightGrey; color:black"|Rinse | |style="background:LightGrey; color:black"|Rinse | ||
Line 630: | Line 666: | ||
|style="background:LightGrey; color:black"|Substrate size | |style="background:LightGrey; color:black"|Substrate size | ||
|style="background:WhiteSmoke; color:black"| | |style="background:WhiteSmoke; color:black"| | ||
* Chips (6-60 mm) | *Chips (6-60 mm) | ||
* 100 mm wafers | *100 mm wafers | ||
* 150 mm wafers | *150 mm wafers | ||
|- | |- | ||
| style="background:LightGrey; color:black"|Allowed materials | | style="background:LightGrey; color:black"|Allowed materials | ||
Line 639: | Line 675: | ||
*Film, or pattern, of all materials except Type IV | *Film, or pattern, of all materials except Type IV | ||
|- | |- | ||
|style="background:LightGrey; color:black"|Batch | |style="background:LightGrey; color:black"|Batch size | ||
|style="background:WhiteSmoke; color:black"| | |style="background:WhiteSmoke; color:black"| | ||
1 | 1 | ||
|- | |- | ||
|} | |} | ||
Line 650: | Line 686: | ||
[[Image:SUSS DEV.JPG|300x300px|right|thumb|Developer: TMAH UV-lithography is located in E-4]] | [[Image:SUSS DEV.JPG|300x300px|right|thumb|Developer: TMAH UV-lithography is located in E-4]] | ||
Developer TMAH UV-lithography was released Q4 2014. | |||
'''[https://www.youtube.com/watch?v=fs9DRH0Eo3k Training video]''' | '''[https://www.youtube.com/watch?v=fs9DRH0Eo3k Training video]''' | ||
The user manual, user APV, and contact information can be found in [http://labmanager.dtu.dk/function.php?module=Machine&view=view&mach=329 LabManager] - '''requires login''' | |||
===[[Specific Process Knowledge/Lithography/Development/Developer TMAH UV-lithography processing|Process Information]]=== | ===[[Specific Process Knowledge/Lithography/Development/Developer TMAH UV-lithography processing|Process Information]]=== | ||
Line 665: | Line 701: | ||
=== Equipment performance and process related parameters === | === Equipment performance and process related parameters === | ||
{| border=" | {|border="1" cellspacing="1" cellpadding="10" style="text-align:left;" | ||
!style="background:silver; color:black; | !style="background:silver; color:black;" width="60"|Purpose | ||
|style="background:LightGrey; color:black"| | |style="background:LightGrey; color:black"| | ||
|style="background:WhiteSmoke; color:black | |style="background:WhiteSmoke; color:black"| | ||
Development of | Development of | ||
*AZ nLOF | *AZ nLOF | ||
Line 677: | Line 713: | ||
*DUV resists | *DUV resists | ||
|- | |- | ||
!style="background:silver; color:black; | !style="background:silver; color:black;" width="60"|Developer | ||
|style="background:LightGrey; color:black"| | |style="background:LightGrey; color:black"| | ||
|style="background:WhiteSmoke; color:black | |style="background:WhiteSmoke; color:black" | | ||
AZ 726 MIF | AZ 726 MIF | ||
Line 686: | Line 722: | ||
!style="background:silver; color:black" align="center" valign="center" rowspan="2"|Method | !style="background:silver; color:black" align="center" valign="center" rowspan="2"|Method | ||
|style="background:LightGrey; color:black"|Development | |style="background:LightGrey; color:black"|Development | ||
|style="background:WhiteSmoke; color:black | |style="background:WhiteSmoke; color:black"| | ||
Puddle | Puddle | ||
|- | |- | ||
|style="background:LightGrey; color:black"|Handling | |style="background:LightGrey; color:black"|Handling | ||
|style="background:WhiteSmoke; color:black | |style="background:WhiteSmoke; color:black"| | ||
Vacuum chuck | Vacuum chuck | ||
|- | |- | ||
!style="background:silver; color:black" align="center" valign="center" rowspan="3"|Process parameters | !style="background:silver; color:black" align="center" valign="center" rowspan="3"|Process parameters | ||
|style="background:LightGrey; color:black"|Temperature | |style="background:LightGrey; color:black"|Temperature | ||
|style="background:WhiteSmoke; color:black | |style="background:WhiteSmoke; color:black"| | ||
Room temperature | Room temperature | ||
|- | |- | ||
|style="background:LightGrey; color:black"|Agitation | |style="background:LightGrey; color:black"|Agitation | ||
|style="background:WhiteSmoke; color:black | |style="background:WhiteSmoke; color:black"| | ||
Rotation | Rotation | ||
|- | |- | ||
|style="background:LightGrey; color:black"|Rinse | |style="background:LightGrey; color:black"|Rinse | ||
|style="background:WhiteSmoke; color:black | |style="background:WhiteSmoke; color:black"| | ||
DI water | DI water | ||
|- | |- | ||
!style="background:silver; color:black" align="center" valign="center" rowspan="3"|Substrates | !style="background:silver; color:black" align="center" valign="center" rowspan="3"|Substrates | ||
|style="background:LightGrey; color:black"|Substrate size | |style="background:LightGrey; color:black"|Substrate size | ||
|style="background:WhiteSmoke; color:black | |style="background:WhiteSmoke; color:black"| | ||
* 100 mm wafers | * 100 mm wafers | ||
* 150 mm wafers | * 150 mm wafers | ||
|- | |- | ||
| style="background:LightGrey; color:black"|Allowed materials | | style="background:LightGrey; color:black"|Allowed materials | ||
|style="background:WhiteSmoke; color:black | |style="background:WhiteSmoke; color:black"| | ||
Silicon and glass substrates | Silicon and glass substrates | ||
Line 719: | Line 755: | ||
|- | |- | ||
|style="background:LightGrey; color:black"|Batch | |style="background:LightGrey; color:black"|Batch | ||
|style="background:WhiteSmoke; color:black | |style="background:WhiteSmoke; color:black"| | ||
1-25 | 1-25 | ||
|- | |- | ||
|} | |} | ||
<br clear="all" /> | |||
{{:Specific Process Knowledge/Lithography/Development/DUV_developer}} |
Latest revision as of 13:15, 10 October 2024
The contents on this page, including all images and pictures, was created by DTU Nanolab staff unless otherwise stated.
Feedback to this page: click here
Development Comparison Table
Equipment | Developer: SU8 (Wet bench) | Developer: E-beam 02 | Developer: TMAH Manual 02 | Developer: TMAH UV-lithography | Developer: TMAH Stepper | |
---|---|---|---|---|---|---|
Purpose |
|
Development of:
|
Development of:
|
Development of:
|
Development of:
Post-exposure baking |
Development of:
Post-exposure baking |
Developer |
mr-Dev 600 (PGMEA) |
|
AZ 726 MIF (2.38% TMAH in water) |
AZ 726 MIF (2.38% TMAH in water) |
AZ 726 MIF (2.38% TMAH in water) | |
Method | Development |
Submersion |
Spray/Puddle |
Puddle |
Puddle |
Puddle |
Handling |
|
|
|
Vacuum chuck |
Vacuum chuck | |
Process parameters | Temperature |
Room temperature |
Room temperature |
Room temperature |
Room temperature |
Room temperature |
Agitation |
Magnetic stirrer |
Rotation |
Rotation |
Rotation |
Rotation | |
Rinse |
IPA |
IPA |
DI water |
DI water |
DI water | |
Substrates | Substrate size |
|
|
|
|
|
Allowed materials |
|
All cleanroom approved materials |
|
|
| |
Batch |
1 - 6 |
1 |
1 |
1 - 25 |
1 - 25 |
Developer: SU8 (Wet Bench)
The SU8-Developer bench is a manually operated wet bench for submersion development of SU-8 photoresist in PGMEA (supplied in the cleanroom as mr-Dev 600). The development process is in two stages; one bath (FIRST) to dissolve the bulk of the resist, and a second, cleaner bath (FINAL) to finish the development. The development time is controlled manually by the user. After development, the substrates are rinsed with IPA in dedicated IPA bath and put for drying in the empty bath.
The user manual, user APV, and contact information can be found in LabManager: Developer: SU8(Wet Bench) - requires login
Process information
Several aspects of the outcome of SU-8 processing are affected by the development process. The lithographic resolution is affected by the time between PEB (post-exposure bake) and development, as the cross-linking process continues in the interface between exposed and unexposed regions even at room temperature. Cracks in the structures is affected by two things; the development time, and how much has previously been developed in the developer bath. Cracking is worse with longer development time, and worst in a new developer bath. The effect of the developer use quickly saturates (5-10 wafers). Finally, the stability of fine structures (high aspect ratio) is affected by the rinse after development, as the lower surface tension of IPA compared to PGMEA reduces pattern collapse during drying.
Development time is strongly dependent on the SU-8 thickness.
- Minimum development time: 1 min per 20 µm in FIRST
Suggestions:
- 2-5µm: 2 min. in FIRST; 2 min. in FINAL
- 40µm: 5 min. in FIRST; 5 min. in FINAL (however, 3 min. in FIRST and 2 min. in FINAL is sufficient)
- 180-250µm: 15 min. in FIRST; 15 min. in FINAL
Purpose |
Development of:
| |
---|---|---|
Developer |
mr-Dev 600 (PGMEA) | |
Method | Development |
Submersion |
Handling |
Single wafer holder | |
Process parameters | Temperature |
Room temperature |
Agitation |
Magnetic stirrer | |
Rinse |
IPA | |
Substrates | Substrate size |
|
Allowed materials |
| |
Batch |
1-6 |
Developer: E-beam 02
Developer: E-beam 02 is a manually operated, single substrate puddle developer. It uses the ZED-N50 or AR 600-50 developers and IPA for rinsing. The substrates are loaded manually one by one into the developer. Developer dispense, puddle time, IPA rinse, and drying is then performed automatically by the equipment.
Training video (for Developer: TMAH Manual, but it is the same model)
The user manual, user APV, and contact information can be found in LabManager - requires login
Process information
All recipes use the following structure:
- Pressurize the developer canister
- Dispense puddle while rotating substrate slowly
- Puddle development while not rotating
- Agitate substrate once per 15 seconds by rotating slowly for 1 second
- Spin off developer
- Clean substrate with IPA
- Dry substrate and chamber with nitrogen
Multi-puddle recipes repeat steps 2-5 for the given number of puddles.
Process recipes
N50 recipes have the letter "N" in them. AR-600-50 recipes have the letter "A" in them. The number is the development time in seconds:
- 01 Rinse
- 02 N 15
- 03 N 30
- 04 N 60
- 05 N 90
- 06 N 120
- 07 N 180
- 08 N 300
- 09 N 600
- 10 N 2x60
- 11 N 5x60
- 12 A 15
- 13 A 30
- 14 A 60
- 15 A 90
- 16 A 120
- 17 A 180
- 18 A 300
- 19 A 600
- 20 A 2x60
- 21 A 5x60
Purpose |
Development of:
| |
---|---|---|
Developer |
| |
Method | Development |
Puddle |
Handling |
| |
Process parameters | Temperature |
Room temperature |
Agitation |
1 second rotational agitation at 30 rpm every 15 seconds | |
Rinse |
IPA | |
Substrates | Substrate size |
|
Allowed materials |
| |
Batch size |
1 |
Developer: TMAH Manual 02
Developer: TMAH Manual 02 is a manually operated, single substrate or chip puddle developer. It uses the TMAH based AZ 726 MIF developer (2.38 % TMAH in water with a small amount of wetting agent). The substrates or chips are loaded manually one by one into the developer. Developer dispense, puddle time, water rinse, and drying is performed automatically by the equipment.
The user manual, user APV, and contact information can be found in LabManager - requires login
Process information
All recipes use the following structure:
- Pressurize the TMAH canister
- Dispense puddle while rotating substrate slowly
- Puddle development while not rotating
- Agitate substrate once per 15 seconds by rotating slowly for 1 second
- Spin off developer
- Clean substrate and chamber with DI water
- Dry substrate and chamber with nitrogen
Multi-puddle recipes repeat steps 2-5 for the given number of puddles.
Process recipes
SP: Single-puddle
MP: Multi-puddle
- 01 Rinse
- 02 SP 15
- 03 SP 30
- 04 SP 60
- 05 SP 90
- 06 SP 120
- 07 SP 300
- 08 MP 2x60
- 09 MP 5x60
- 91 SP test
- 92 MP test
Purpose |
Development of UV resists:
Development of DUV resists:
| |
---|---|---|
Developer |
AZ 726 MIF | |
Method | Development |
Puddle |
Handling |
| |
Process parameters | Temperature |
Room temperature |
Agitation |
1 second rotational agitation at 30 rpm every 15 seconds | |
Rinse |
DI water | |
Substrates | Substrate size |
|
Allowed materials |
| |
Batch size |
1 |
Developer TMAH UV-lithography
Developer TMAH UV-lithography was released Q4 2014.
The user manual, user APV, and contact information can be found in LabManager - requires login
Process Information
Purpose |
Development of
| |
---|---|---|
Developer |
AZ 726 MIF (2.38% TMAH in water) | |
Method | Development |
Puddle |
Handling |
Vacuum chuck | |
Process parameters | Temperature |
Room temperature |
Agitation |
Rotation | |
Rinse |
DI water | |
Substrates | Substrate size |
|
Allowed materials |
Silicon and glass substrates Film or pattern of all except Type IV | |
Batch |
1-25 |
Developer: TMAH Stepper
This developer is dedicated for development of DUV resists. The developer is fully automatic and can run up to 25 substrates in a batch 4", 6", and 8" size (8" requires tool change). The machine is equipped with 1 developer line, in our case 2,38% TMAH in water (AZ 726 MIF), 1 topside rinse line with water, 1 backside rinse line with water and 1 N2 line for drying.
The user manual and contact information can be found in LabManager - requires login
Process information
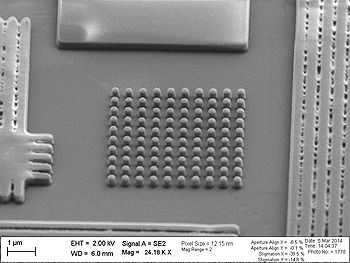
The development process will be performed by the customer together with the Photolith group of DTU Nanolab. In case you would like to do DUV lithography please contact Lithography team, who will consult you and run your wafers together with you.
Here you can find a chart demonstrating a dependence between 250 nm line width/pillars diameter and exposure dose.
Standard processes
Post-exposure bake sequences:
- (1000) DCH PEB 130C 60s 60s baking at 130°C; 20s cooling
- (1001) DCH PEB 130C 90s 90s baking at 130°C; 20s cooling
Development sequences:
- (1004) DCH DEV 60s 60s single puddle development
Combined PEB and development sequences:
- (1002) DCH PEB_60s and DEV_60s 60s baking at 130°C followed by 60s single puddle development
- (1003) DCH PEB_90s and DEV_60s 90s baking at 130°C followed by 60s single puddle development
The standard developer process consists of:
- pre-wetting with water (2.5s @ 1000rpm)
- developer dispense (2.5s @ 40rpm, corresponding to ~9ml)
- development (60s @ 0rpm)
- water rinse with BSR (5s @ 3000rpm)
- nitrogen drying (7s @ 4000rpm)
and has a cycle time of ~2 minutes
Purpose |
Development of DUV resist: KRF M230Y and KRF M35G | ||
---|---|---|---|
Developer |
2,38% water based TMAH | ||
Process parameters | Spin speed |
10 - 5000 rpm | |
Spin acceleration |
100 - 10000 rpm/s | ||
Hotplate temperature |
130°C for post exposure baking | ||
Substrates | Substrate size |
| |
Allowed materials |
| ||
Batch |
1 - 25 |