Specific Process Knowledge/Thermal Process/C4 Aluminium Anneal furnace
Feedback to this page: click here
This page is written by DTU Nanolab internal
Aluminium Anneal furnace (C4)
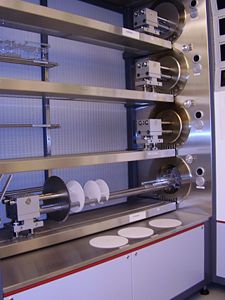
The Aluminium Anneal or Al-Anneal furnace (C4) is a Tempress horizontal furnace for annealing and oxidation of different samples.
The samples can for instance be silicon and quartz wafers or small samples with aluminium or ALD deposited Al2O3 and TiO2. Other materials might be allowed in the furnace, but this requires a permision from the Thin Film group. Also please check the cross contamination information in LabManager, before you use the furnace.
The furnace is the lowest of the C-stack furnaces positioned in cleanroom B-1. .
The user manual, technical information and contact information can be found in LabManager:
Process knowledge
Purpose |
| |
---|---|---|
Process parameter range | Process Temperature |
|
Process pressure |
| |
Gas flows |
| |
Substrates | Batch size |
|
Substrate materials allowed |
|
Oxidation uniformity for 6" wafers
In November 2023 an oxygen (O2) mass flow controller was connected to the furnace, so that it became possible to oxidize different wafers and samples in the furnace.
The C4 furnace is made for processing of 4" wafers placed vertically in a quartz boat. However, it is possible to process 6" wafers (or small samples placed on a 6" wafer), if they are placed horizontally on the boat.
Normally only one 6" wafer is being processed, because the temperature flat zone, i.e. the area inside the furnace where the temperature is uniform, is only a little longer than one quartz boat. But because there are two quartz boats available for the furnace, it has also been tried to place a 6" wafer on each boat and oxidize them at the same time as explained here.
Sample loading:
One 6" wafer was placed on each of the two quartz boats. The wafer flats were pointing towards each other, and the boats were centered above the arrow on the cantilever. The loading procedure is explained in the user manual for the furnace, but users should not do this without training, as the wafers might collide with the furnace tube, when the door closes (the tube diameter is 160 mm, and the wafer diameter is 150 mm). In order improve the temperature uniformity over the two 6" wafers, two 4" dummy wafers were placed in the end of each boat.
The 6" wafer closest to the furnace door/cleanroom is numbered "w1", and the wafer closest to the furnace/service room is numbered "w2". See the image below.
Process parameters:
For the oxidation, the following process parameters were used:
- Recipe: "DRY1050"
- Oxidation temperature: 1050 oC
- Oxidation time: 1 h 40 min
Results:
After the oxidation, the thickness of the oxide layer grown on the 6" wafers was measured in five points on each wafer using the Ellipsometer VASE.
The measurement results are shown below.
Pernille Voss Larsen, DTU Nanolab, November 2023

