Specific Process Knowledge/Lithography/Pretreatment
Feedback to this page: click here
Pretreatment
Pretreatment is done before spin coating in order to ensure the best conditions for adhesion between the substrate surface and the resist. Pretreatment ranges from a simple dehydration bake over etching the native oxide to vapor phase deposition of an adhesion promoter.
All surfaces can be divided to hydrophilic or hydrophobic surfaces. Oxidized surfaces such as SiO2 or surfaces with native oxide (e.g. Si or Al substrates) are considered to be hydrophilic and have very bad wetting with hydrophobic resist. The adhesion of most resists on hydrophilic surfaces is deteriorated if moisture is present on the surface.
Therefore it is very important to do the pretreatment step before the spinning. Here we will give an overview of treatments available at DTU Nanolab to promote photoresist adhesion.
Comparing pretreatment methods
HMDS | Buffered HF-Clean | Oven 250C | |
---|---|---|---|
Generel description |
Vapor priming |
Native oxide strip |
Dehydration |
Chemical |
hexamethyldisilazane (HMDS) |
12%HF with Ammoniumflouride |
none |
Substrate size |
|
|
|
Allowed materials |
Silicon, glass, and polymer substrates (Tg > 150°C) Film or pattern of all types, except type IV and resist/polymer |
|
|
Restrictions | Type IV and resist/polymer on polymer substrate
i.e. no resist coated wafers or crystalbonded chips! |
Wafers with metal is not allowed | Resist is not allowed |
Pretreatment of different surfaces
This section is under construction
Dehydration | BHF dip | HMDS | Dip/spin-on adhesion promoter | Comment | |
Silicon with native oxide | (x) | x | x | (x) | |
Silicon oxide | (x) | x | (x) | ||
Silicon nitride | (x) | x | (x) | ||
Glass (borofloat/pyrex) | x | x | (x) | Dehydration before HMDS for best result | |
Fused silica | x | x | (x) | Dehydration before HMDS for best result |
HMDS
Feedback to this section: click here
The chemical treatment with hexamethyldisilazane (HMDS) before the spin coating can be used to promote the adhesion for photoresist. Vapor priming with HMDS leaves a mono-layer of TMS (trimethylsilyl) on the Si or SiO2 surface. The process dehydrates the substrate surface, and lowers the surface tension.
The molecular formula for hexamethyldisilazane, or bis(trimethylsilyl)amine, is C6H19NSi2. Here is a schematic overview of HMDS treatment of silicon-oxide surface.
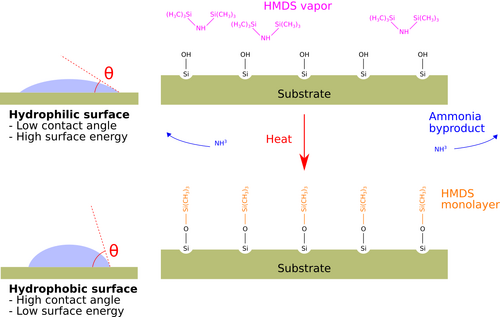
Comparing HMDS priming
Equipment | Oven: HMDS 2 | Gamma UV/ Gamma e-beam and UV | |||
---|---|---|---|---|---|
Purpose |
|
| |||
Priming chemical |
hexamethyldisilazane (HMDS) | ||||
Performance | Contact angle |
|
Fast recipe [standard recipe]:
| ||
Process parameters | Process temperature |
150°C |
120°C | ||
Process time |
25 minutes |
1 min / wafer | |||
Substrates | Substrate size |
|
| ||
Allowed materials |
Silicon, glass, and polymer substrates III-V materials on silicon carrier Film or pattern of all but types, except type IV and resist/polymer (incl. Crystalbond) |
Silicon and glass wafers Film or pattern of all but types, except type IV and resist/polymer (incl. Crystalbond) | |||
Batch |
1 - 25, multiple batches possible |
1 - 25 |
Oven: HMDS 2
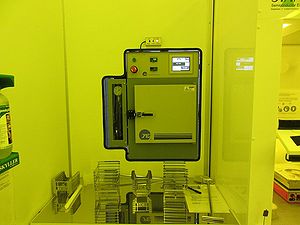
The user manual, user APV, and contact information can be found in LabManager:
Process information
- Recipe 1: baseline prime process with 5 min HMDS priming time
Spin Coater: Gamma UV

The user manual, user APV, and contact information can be found in LabManager:
Spincoater: Gamma UV labmanager page
Additional information about the spin coater and processes can be found in Labadviser:
Spincoater: Gamma UV labadviser page
Spin Coater: Gamma e-beam & UV
The user manual, user APV, and contact information can be found in LabManager:
Spin Coater: Gamma e-beam & UV labmanager page
Additional information about the spin coater and processes can be found in Labadviser:
Spin Coater: Gamma e-beam & UV labadviser page
Buffered HF-Clean
Feedback to this section: click here
Another commonly used method to render the surface of silicon wafers hydrophobic is the dilute HF dip.
BHF is mostly used to do pretreatment step for new Si wafers. The native dioxide layer will be removed during 30 sec etching and in this way we will promote the resist adhesion on the Si substrates. We recommend to spin resist asap after the procedure.
The user manual, user APV, and contact information can be found in LabManager:
Buffered HF-Clean in LabManager
Process information
For more information on this BHF bath take a look here: Wet Silicon Oxide Etch (BHF)
Oven 250C
Feedback to this section: click here
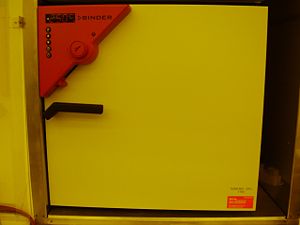
The oven is typically used for pretreatment (dehydration) of Si and glass substrates to promote the resist adhesion. We recommend to place the wafers in metal carrier in the oven at least for 4 hours, better during the night, and spin the resist on them asap.
The user manual, and contact information can be found in LabManager: Oven 250C