Specific Process Knowledge/Characterization/Profiler
Feedback to this page: click here
Overview of the Nanolab profilers
All the profilers are compared on the topographic measurement page.
The sections below describe each profiler (Dektak stylus profilers and optical profilers) in more detail.
Dektak XTA stylus profiler
The Dektak XTA stylus profiler from Brüker is used for profiling surfaces of samples with structures in the micro- and nanometer range. The size of the structures that can be measured is limited by the tip dimensions.
A profile measurement can be done across a specific structure by using a high magnification camera to locate the structure. It is also possible to program the stylus to measure in several positions, defined with respect to some deskew points. Stress measurements of thin films can be done by measuring the wafer bow.
The user manual, quality control procedure and results, technical information and contact information can be found in LabManager:
Purpose | Profiler for measuring micro structures |
|
---|---|---|
Performance | Scan range x y |
Line scan x: 50 µm to 55 mm in a single scan, up to 200 mm with stiching |
Scan range z |
50 Å to 1 mm | |
Resolution x y |
Down to 0.003 µm | |
Resolution z |
1 Å, 10 Å, 80 Å or 160 Å (for ranges 65 kÅ, 655 kÅ, 5240 kÅ and 1 mm respectively) | |
Height accuracy z (95 % confidence) |
~ 300 Å for the 65 kÅ range, ~ 0.17 µm for the intermediate ranges, and ~0.6 µm for the 1 mm range for well-defined steps that are easy to measure reproducibly (see below) | |
Max scan depth as a function of trench width W |
1.2*(W[µm]-5µm) | |
Hardware settings | Tip radius |
|
Substrates | Substrate size |
|
Substrate materials allowed |
|
Height measurement accuracy for the DektakXT
The accuracy of a height measurement with the profiler depends on the measurement settings, the sample, the instrument calibration and the resolution.
Influence of measurement settings and sample
Both the force setting and the scan speed are important: Too high force may compress a soft material like Al, Au or some polymers, while too low force may lead to the stylus "jumping" over features, especially if the scan speed is high.
If the scan speed is too low and you are measuring a small step <500 nm, you may experience drift in the measurement. Of course you also must make sure the feature you are measuring is wide enough for the stylus tip to reach the bottom (see the DektakXT manual, Figure 3 for details).
If the step is not well defined, you may have significant scatter in the step heights determined.
Influence of calibration standard uncertainty
Nanolab staff check the instrument's measurement accuracy with a standard step height of 9160 Å for the 65 kÅ range and 24.865 µm for the larger ranges. The 95 % confidence intervals for the standards are 300 Å for the 9160 Å standard and 0.15 µm for the 24.865 µm standard. If the control measurement is beyond the limit set in our Quality Control procedure, the instrument is calibrated and the users informed (see LabManager for details on the control instruction and the control measurement data).
The size of the calibration standard confidence intervals mean that the measurement uncertainty is much more significant for very shallow steps below 500-1000 nm than for steps in the micron range: The 95 % confidence interval in the 65 kÅ range is obviously at least ± 300 Å, so measuring a 100-200 nm step will have a huge error percentage-wise. Note that this error (from the calibration standard) is systematic. The random error associated with repeated measurements is usually smaller (perhaps ± 5 nm). Therefore it may still make sense to measure shallow steps to be able to make compare step heights for different samples.
Total uncertainty budget
We can numerically estimate the accuracy of a measurement based on the error of the calibration combined with the error from the limits of the resolution and of the scatter of repeated measurements. You can seean uncertainty budget for the Dektak measurements here (made by Rebecca Ettlinger in 2020): File:uncertainty budget dektaks.xlsx. It is based on the procedure described here.
The error stemming from the uncertainty on the calibration standard dominates for all ranges except the 1 mm range, where the resolution also plays a role. This leads to the 95 % confidence intervals listed above in the table: just over 30 nm for the smallest range, about 0.17 µm for the medium ranges, and about 0.6 µm for the 1 mm range. As noted above, be aware that if you have a step height that is difficult to measure, the scatter of repeated measurements could easily lead to larger confidence intervals.
Dektak 8 stylus profiler
The Dektak 8 stylus profiler is a product of Veeco Instruments. It is used for profiling surfaces of samples with structures in the micro- and nanometer range. The size of the structures that can be measured is limited by the tip dimensions.
It can measure specific structures found with the help of a high magnification video camera or it can be programmed to measure several points defined with respect to some deskew points. It can also be used for stress measurements of thin films by measuring the wafer bow.
The user manual, quality control procedure and results, technical information and contact information can be found in LabManager:
The original user manual can be obtained from the staff.
Purpose | Profiler for measuring micro structures. |
|
---|---|---|
Performance | Scan range x y |
Line scan x: 50 µm to 100 mm |
Scan range z |
50 Å to 1 mm | |
Resolution x y |
Down to 0.067 µm | |
Resolution z |
1 Å, 10 Å, 40 Å or 160 Å (for ranges 65 kÅ, 655 kÅ, 2620 kÅ and 1 mm respectively) | |
Height accuracy z (95 % confidence) |
~ 300 Å for the 65 kÅ range, ~ 0.16 µm for the intermediate ranges, and ~0.6 µm for the 1 mm range for well-defined steps that are easy to measure (see below) | |
Max. scan depth as a function of trench width W |
1.2*(W[µm]-5µm) | |
Hardware settings | Tip radius |
|
Performance | Substrate size |
|
Substrate material allowed |
|
Height measurement accuracy
See above for the DektakXTA as the considerations for the Dektak 8 are the same, though the resolution and measurement repeatability is a tiny bit better for the Dektak 8 than for the DektakXTA.
Optical Profiler (Sensofar)
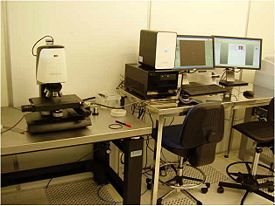
The PLu Neox 3D Optical Profiler (from Sensofar) has a dual-technology sensor head that combines confocal and interferometry techniques as well as thick and thin film measurement capabilities.
The Neox sensor head provides standard microscope imaging, confocal imaging, confocal profiling, PSI (Phase Shift Interferometry), VSI (Vertical Scanning Interferometry) and high resolution thin film thickness measurements on a single instrument.
The main purpose is 3D topographic imaging of surfaces, step height measurements in smaller trenches/holes than can be obtained with standard stylus methods (i.e. with aspect ratios higher that 1:1), roughness measurements with larger FOV (Field Of View) than the AFM, but less horisontal resolution.
For most samples the optical profiler provides fast and easy information without any sample preparation. However, it can be necessary to cover thin transparent layers (< 2 µm) with a thin layer of metal.
The resolution is limited by the objectives and the pixel resolution. Also the depth of focus is limited, especially for higher magnifications.
Analysis software: Free analysis software for visualizing and analyzing AFM and Optical profiler files (Sensofar) Gwyddion
The user manual, technical information and contact information can be found in LabManager:
Optical profiler (Sensofar) info page in LabManager
Process Information
- Results from the Optical Profiler (Sensofar) acceptance test
- Sensofar presentation on how the sensofar works
- Plu neox leaflet including specifications
Equipment | Optical profiler | |
---|---|---|
Purpose | 3D topographic imaging of surfaces. |
|
Posibilities | Confocal and interferometric profiling and reflectometry |
|
Performance | Depending on the objective chosen | |
Substrates | Substrate size |
|
Substrate materials allowed |
|
Optical Profiler (Filmetrics)
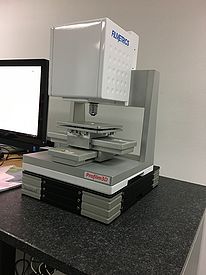
The Profilm3D optical profiler from Filmetrics uses white-light-interferometry (WLI) and phase-shifting-interferometry (PSI) to produce surface profiles and depth-of-field color images.
The main purpose is 3D topographic imaging of surfaces, step height measurements and roughness measurements with larger FOV (Field Of View) than the AFM, but less horisontal resolution.
For most samples the optical profiler provides fast and easy information without any sample preparation. However, it can be necessary to cover thin transparent layers (< 2 µm) with a thin layer of metal.
The resolution is limited by the objective and the sampling resolution.
The user manual, technical information and contact information can be found in LabManager:
Optical profiler (Filmetrics) info page in LabManager
Equipment | Optical profiler | |
---|---|---|
Purpose | 3D topographic imaging of surfaces. |
|
Posibilities | Interferometric profiling |
|
Performance | With the current 10x objective | |
Substrates | Substrate size |
|
Substrate materials allowed |
|
Dektak 3ST
The Dektak 3ST is intended for profile measurements on samples outside the cleanroom.
The user manual, technical information and contact information can be found in LabManager:
Dektak 3ST (Dektak) in LabManager
The computer connected to the Dektak 3ST is pretty old and runs Windows 98 SE. It is not connected to the network but traces can be saved on either USB memory stick or floppy disk. The USB driver is an old universal driver and has been shown to work with small size USB sticks. However it did not work with an 8GB Kingston stick.
Performance | Vertical Range |
|
---|---|---|
Scan length range |
| |
Stylus track force |
| |
Scan speed ranges |
| |
Materials | Allowed substrate materials |
|
Stylus Profiler: Dektak150
The stylus profiler Dektak150 is intended for profile measurements on samples outside the cleanroom.
The user manual, technical information and contact information can be found in LabManager:
Stylus profiler:Dektak150 in LabManager
The computer is not connected to the network but data can be saved on a dedicated USB and transfered to a computer on the network.
Purpose | Profiler for measuring micro structures |
|
---|---|---|
Performance | Scan range x y |
Line scan x: 50 µm to 55 mm in a single scan |
Scan range z |
50 Å to 1 mm | |
Resolution x y |
Down to 0.003µm | |
Resolution z |
1Å (@65kÅ), 10Å (@655 kÅ), 80 Å (@5240 kÅ), 160 Å (@1mm) | |
Maximum sample thickness |
100mm | |
Hardware settings | Tip radius |
|
Substrates | Substrate size |
|
Substrate materials allowed |
|