Specific Process Knowledge/Lithography/Development
Feedback to this page: click here
Development Comparison Table
Equipment | SU8-Developer | Developer: E-beam | Developer: TMAH Manual | Developer: TMAH UV-lithography | Developer: TMAH Stepper | |
---|---|---|---|---|---|---|
Purpose |
|
Development of
|
Development of
|
Development of
|
Development of
Post-exposure baking |
Development of
Post-exposure baking |
Developer |
mr-Dev 600 (PGMEA) |
N-50 AR600-546 |
AZ 726 MIF (2.38% TMAH in water) |
AZ 726 MIF (2.38% TMAH in water) |
AZ 726 MIF (2.38% TMAH in water) | |
Method | Development |
Submersion |
Spray/Puddle |
Spray/Puddle |
Puddle |
Puddle |
Handling |
Single wafer holder |
Vacuum chuck for 2",4" and 6" (the same) or chip "basket" |
Edge handling chuck or chip "basket" |
Vacuum chuck |
Vacuum chuck | |
Process parameters | Temperature |
Room temperature |
Room temperature |
Room temperature |
Room temperature |
Room temperature |
Agitation |
Magnetic stirrer |
Rotation |
Rotation |
Rotation |
Rotation | |
Rinse |
IPA |
IPA |
DI water |
DI water |
DI water | |
Substrates | Substrate size |
|
|
|
|
|
Allowed materials |
Silicon and glass substrates Film or pattern of all but Type IV |
All cleanroom approved materials |
All cleanroom approved materials Film or pattern of all types |
Silicon and glass substrates Film or pattern of all but Type IV |
Silicon, III-V, and glass substrates Film or pattern of all but Type IV | |
Batch |
1-6 |
1 |
1 |
1-25 |
1-25 |
SU8-Developer
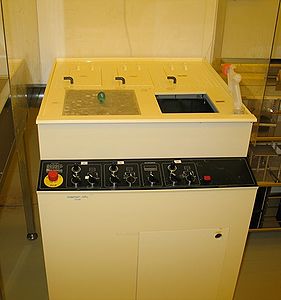
Feedback to this section: click here
The SU8-Developer bench is a manually operated chemical bench for submersion development of SU-8 photoresist in PGMEA (supplied in the cleanroom as mr-Dev 600). The development process is in two stages; one bath (FIRST) to dissolve the bulk of the resist, and a second, cleaner bath (FINAL) to finish the development. The development time is controlled manually by the user. After development, the substrates are rinsed with IPA and dried in the bench.
The user manual, user APV, and contact information can be found in LabManager
Process information
Several aspects of the outcome of SU-8 processing are affected by the development process. The lithographic resolution is affected by the time between PEB (post-exposure bake) and development, as the cross-linking process continues in the interface between exposed and unexposed regions even at room temperature. Cracks in the structures is affected by two things; the development time, and how much has previously been developed in the developer bath. Cracking is worse with longer development time, and worst in a new developer bath. The effect of the developer use quickly saturates (5-10 wafers). Finally, the stability of fine structures (high aspect ratio) is affected by the rinse after development, as the lower surface tension of IPA compared to PGMEA reduces pattern collapse during drying.
Development time is strongly dependent on the SU-8 thickness.
- Minimum development time: 1 min per 20µm in FIRST
Suggestions:
- 2-5µm: 2 min. in FIRST; 2 min. in FINAL
- 40µm: 5 min. in FIRST; 5 min. in FINAL (however, 3 min. in FIRST and 2 min. in FINAL is sufficient)
- 180-250µm: 15 min. in FIRST; 15 min. in FINAL
Purpose |
Development of
| |
---|---|---|
Developer |
mr-Dev 600 (PGMEA) | |
Method | Development |
Submersion |
Handling |
Single wafer holder | |
Process parameters | Temperature |
Room temperature |
Agitation |
Magnetic stirrer | |
Rinse |
IPA | |
Substrates | Substrate size |
150 mm wafer is possible if the level is high enough |
Allowed materials |
Silicon and glass substrates Film or pattern of all but Type IV | |
Batch |
1-6 |
Developer: E-beam
Feedback to this section: click here
Developer: E-beam is a manually operated, single substrate or chip spray-puddle developer. It uses the N50 or AR 600-546 developers and IPA for rinsing. The substrates or chips are loaded manually one by one into the developer. Developer dispense, puddle time, IPA rinse, and drying is performed automatically by the equipment.
The machine is setup to agitate and be stationary to enhance the development uniformity - this is a ongoing process.
Training video (for Developer: TMAH Manual, but it is the same model)
The user manual, user APV, and contact information can be found in LabManager
Process information
All recipes are single puddle. N50 and 546 denotes the developer used (546 is short for AR 600- 546). The first step is pressurizing the canister so nothing will happen visually. Please watch if the developer and rinsing starts. If not try to restart the machine by pressing the EMO and turning it on again. The spray is 8-10 s and will start the development process hence the short recipes (10s and 30s.) have been adjusted according to this.
Process recipes
- 546 10s: 10s. Development Rinse and dry.
- 546 30s: 60s. Development Rinse and dry.
- 546 60s: 60s. Development Rinse and dry.
- 546 180s: 180s. Development Rinse and dry.
- N50 10s: 10s. Development Rinse and dry.
- N50 30s: 30s. Development Rinse and dry.
- N50 60s: 60s. Development Rinse and dry.
- N50 90s: 90s. Development Rinse and dry.
- N50 120s: 120s. Development Rinse and dry.
- N50 180s: 180s. Development Rinse and dry.
- N50 300s: 300s. Development Rinse and dry.
- N50 180s6": Test for changing the agitation for 6" uniformity 180s. Development Rinse and dry.
- Testdev: The time can be modified 60s. Development Rinse and dry on AR 600-546.
- Rinse: Rinse and dry.
Utility recipes
- UTIL-DR: Dome rinse.
- UTIL-BE: Bottle empty. Nanolab use only.
Purpose |
Development of
| |
---|---|---|
Developer |
| |
Method | Development |
Spray/Puddle |
Handling |
Vacuum chuck for 2",4" or 6" wafers and chip "basket" | |
Process parameters | Temperature |
Room temperature |
Agitation |
Yes 15rpm back and forth | |
Rinse |
IPA - Isopropanol | |
Substrates | Substrate size |
|
Allowed materials |
All cleanroom approved materials Film or pattern of all types | |
Batch |
1 |
Developer: TMAH Manual
Feedback to this section: click here
Developer: TMAH Manual is a manually operated, single substrate or chip spray-puddle developer. It uses the TMAH based AZ 726 MIF developer (2.38 % TMAH in water with a small amount of wetting agent). The substrates or chips are loaded manually one by one into the developer. Developer dispense, puddle time, water rinse, and drying is performed automatically by the equipment.
The spray nozzle makes it difficult to build up a perfect puddle on 4" or 6" substrates which affects the effectiveness and uniformity of the development. Pre-wetting during dispense or agitation during development may give better results.
The user manual, user APV, and contact information can be found in LabManager
Process information
Process recipes
- DP 2x60s: Double puddle, 2 times 60s. Rinse and dry.
- MP 4x60s: Multiple puddle, 4 times 60s. Rinse and dry.
- SP 120s: Single puddle, 120s. Rinse and dry.
- SP 15s: Single puddle, 15s. Rinse and dry.
- SP 30s: Single puddle, 30s. Rinse and dry.
- SP 60s: Single puddle, 60s. Rinse and dry.
Utility recipes
- UTIL-DR: Dome rinse.
- UTIL-BE: Bottle empty. Nanolab use only.
Purpose |
Development of
| |
---|---|---|
Developer |
AZ 726 MIF (2.38% TMAH in water) | |
Method | Development |
Spray/Puddle |
Handling |
Edge handling chuck or chip "basket" | |
Process parameters | Temperature |
Room temperature |
Agitation |
none | |
Rinse |
DI water | |
Substrates | Substrate size |
|
Allowed materials |
All cleanroom approved materials Film or pattern of all types | |
Batch |
1 |
Developer TMAH UV-lithography
Feedback to this section: click here
Developer TMAH UV-lithography was released Q4 2014.
The user manual, user APV, and contact information can be found in LabManager
Process information
Purpose |
Development of
| |
---|---|---|
Developer |
AZ 726 MIF (2.38% TMAH in water) | |
Method | Development |
Puddle |
Handling |
Vacuum chuck | |
Process parameters | Temperature |
Room temperature |
Agitation |
Rotation | |
Rinse |
DI water | |
Substrates | Substrate size |
|
Allowed materials |
Silicon and glass substrates Film or pattern of all except Type IV | |
Batch |
1-25 |