Specific Process Knowledge/Etch/DRIE-Pegasus/picoscope
Feedback to this page: click here
Process optimization using the Picoscope
Before going into details on why it makes sense to optimize the processes using the picoscope process monitoring, we need to have a look at how this is usually done.
Standard process parameter monitoring
The original standard recipes on Pegasus 1 differ in many ways. The second step of one of them is listed below:
Process A Step 2 parameters | ||
---|---|---|
Parameter | Etch | Dep |
Gas flow (sccm) | SF6 350 (1.5 s), 550 | C4F8 200 |
Cycle time (secs) | 7.0 | 4.0 |
Pressure (mtorr) | 25 (1.5 s), 150 | 25 |
Coil power (W) | 2800 | 2000 |
Platen power (W) | 140 (1.5) 45 | 0 |
Common | Temperature 20 degs |
When running any recipe on the SPTS Pro software, a set of process parameters are recorded as the process runs. This data can be accessed later by looking up the datalog. Which parameters are recorded is dictated by the socalled logging recipe that is selected for every process recipe. The list of possible parameters to include in a logging recipe is long and is comprised of both input parameters such as 'Coil forward power demand' and 'SF6 flow setpoint', and measured values such as 'Platen temperature' and 'Platen DC Bias'. During the process itself, one can also activate the 'Trace' to monitor the process parameters in real time.
To the left in the figure below, some of the most important process parameters are shown for a process run of the recipe Process A.
- 4 cycles of Process A
-
Left: Recorded with the SPTS software
-
Right: Recorded with the Picoscope
One can see the multiplexing of the Bosch process by alternation of the gas flows of SF6 and C4F8
- 4 cycles of Process D4
-
Left: Recorded with the SPTS software
-
Right: Recorded with the Picoscope


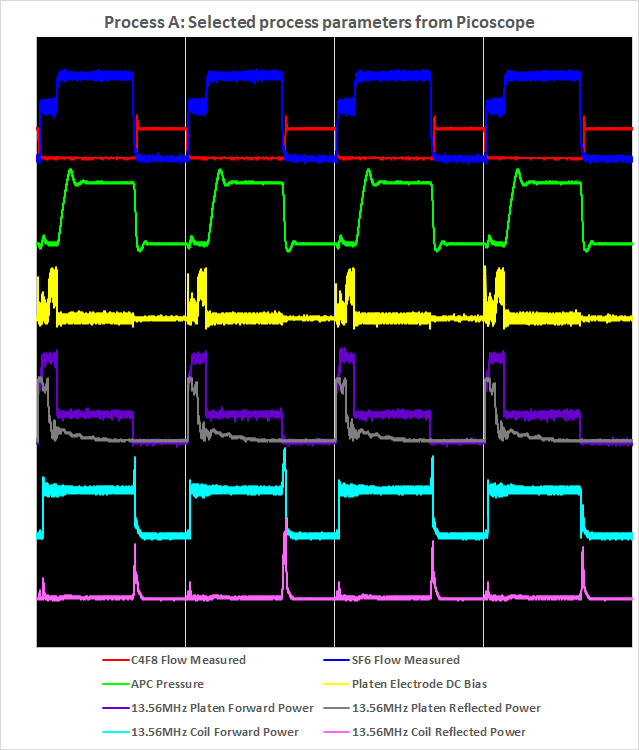
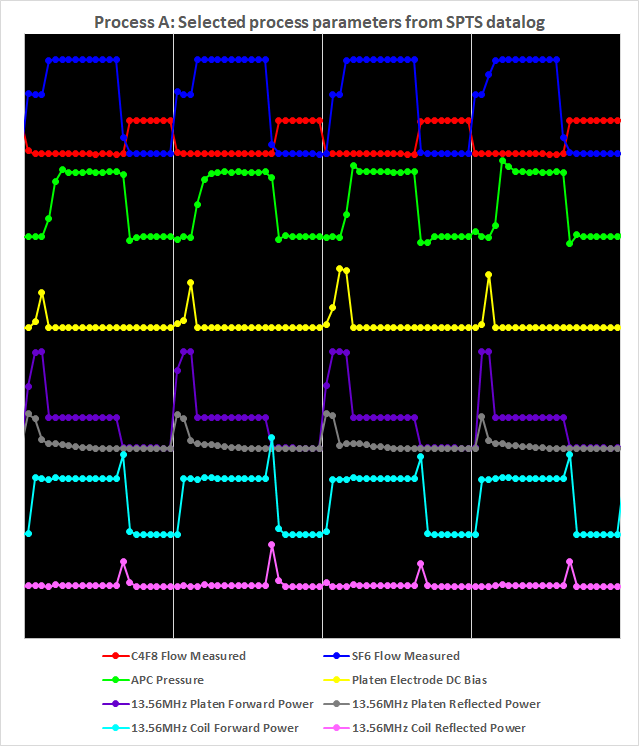