Specific Process Knowledge/Lithography/Development
Feedback to this page: click here
THIS PAGE IS UNDER CONSTRUCTION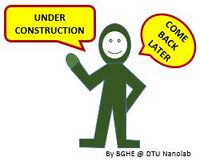
Coaters: Comparison Table
Equipment | Developer 1 and 2 | Developer-6inch | Developer-TMAH | |
---|---|---|---|---|
Purpose |
|
|
| |
Performance | Substrate handling |
|
|
|
Permanent media |
|
|
| |
Manual dispense option |
|
|
| |
Process parameter range | Spindle speed |
|
|
|
Gyrset |
|
|
| |
Substrates | Substrate size |
|
|
|
Batch size |
|
|
| |
Allowed materials |
|
|
|
Developer-1 and Developer-2

Feedback to this section: click here
Developer-1 and Developer-2
The user APV, and contact information can be found in LabManager: Developer-1 Developer-2
Process information
- Before using a one of developer batch's please check the "Litho4_Dev-7up-KOH" logbook to find out when they were used last time. A fresh bath can be reused without problems.
- The main rule is the develop from yesterday must be changed.
- Substrates rinses with with water for 4-5 min. after developing.
- Substrates can been spin-dried or dried with nitrogen gun after the rinse.
The standard developing time AZ resist:
- 1.5µm resist is 60 sec
- 2.2µm resist is 70 sec
- 4.2µm resist is 3 min
- 10µm resist is 5 min
Procedure for making a new developer
1. 800ml "Developer AZ 351B" is mixed with 4000ml water in a special container in the fume hood.
2. Fill the bath with the developer mixture and heat it to 22 °C before use.
Purpose |
| ||
---|---|---|---|
Resist |
| ||
Performance | Coating thickness |
| |
Process parameters | Spin speed |
100 - 5000 rpm | |
Spin acceleration |
100 - 10000 rpm/s | ||
Hotplate temperature |
| ||
Substrates | Substrate size |
| |
Allowed materials |
All cleanroom materials except III-V materials | ||
Batch |
1 - 24 |
Developer-6inch

Feedback to this section: click here
Spin Track 1 + 2 is an SVG 88 series track system from Rite Track. Each track consists of a HMDS priming module, a spin coating module, and a baking module. In fact, the only difference between the two tracks is the resist used in the spin coating module. Spin Track 1 + 2 is capable of handling 150 mm wafers, as well as 100 mm wafers, but is currently set up for 100 mm wafer processing.
The Spin Track 1 + 2 is controlled using the Recipe Manager software via the touchscreen on the arm attached to the lefthand end of the track. Recipes for the individual modules are developed by Danchip and combined into flows. The user selects a flow (specific to track 1 or 2), and the appropriate recipes will be downloaded and executed on the appropriate track. The other track runs an empty process (no wafers needed), and can unfortunately not be used by a second user while the first user is processing.
The user manual, user APV, and contact information can be found in LabManager
Process information
Spin Track | 1 | 2 | |
---|---|---|---|
Purpose |
|
| |
Resist |
AZ MiR 701 (29cps) positive tone |
AZ nLOF 2020 negative tone | |
Performance | Coating thickness |
1 - 3 µm |
1 - 4 µm |
HMDS contact angle |
60° - 90°; standard recipe 82° (on SiO2) | ||
Process parameters | Spin speed |
10 - 9990 rpm | |
Spin acceleration |
1000 - 50000 rpm/s | ||
Hotplate temperature |
90°C |
110°C | |
HMDS priming temperature |
50°C | ||
Substrates | Substrate size |
100 mm wafers | |
Allowed materials |
Silicon and glass wafers Film or pattern of all types | ||
Batch |
1 - 25 |
Developer-TMAH
Feedback to this section: click here
Developer-TMAH is a manually operated, single substrate spray-puddle developer. It uses the TMAH based AZ 726 MIF developer (2.38 % TMAH in water with a small amount of wetting agent).
The user manual, user APV, and contact information can be found in LabManager
Purpose |
Development of
| |
---|---|---|
Developer |
AZ 726 MIF (2.38% TMAH in water) | |
Method |
Puddle | |
Process parameters | Temperature |
Room temperature |
Agitation |
none | |
Substrates | Substrate size |
|
Allowed materials |
All Silicon, glass and polymer substrates | |
Batch |
1 |