Specific Process Knowledge/Thermal Process/C4 Aluminium Anneal furnace: Difference between revisions
No edit summary |
|||
Line 66: | Line 66: | ||
|} | |} | ||
==Oxidation uniformity== | |||
==Oxidation uniformity for 6" wafers== | |||
In November 2023 an oxygen (O<sub>2</sub>) mass flow controller was connected to the furnace, so that it became possible to oxidize different wafers and samples in the furnace. | |||
The C4 furnace is made for processing of 4" wafers placed vertically in a quartz boat. However, it is possible to process 6" wafers (or small sample placed on a 6" wafer), if they are placed horizontally on the boat. | |||
Normally only one 6" wafer is be processed, because the temperature flat zone, i.e. the area where the temperature is uniform, it only a little longer than one quartz boat. The teh | |||
It was tried to oxidize two 6" wafers at the same time in the furnace. | |||
<b>Process parameters:</b> | |||
* Recipe: "DRY1050" | |||
* Oxidation temperature: 1050 <sup>o</sup>C | |||
* Oxidation time: 1 h 40 min | |||
[[image:Oxidation test 1.jpg|600x600px|left|thumb|Two 6" wafer loaded in the C4 furnace. Two 4" dummy wafers are placed in the end of each boat. ]] | |||
[[image:Oxidation test 2.jpg |700x700px|left|thumb|Oxide thickness measured on the two 6" wafers]] |
Revision as of 13:22, 15 December 2023
Feedback to this page: click here
This page is written by DTU Nanolab internal
Aluminium Anneal furnace (C4)
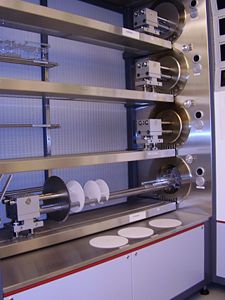
The Aluminium Anneal or Al-Anneal furnace (C4) is a Tempress horizontal furnace for annealing and oxidation of different samples.
The samples can for instance be silicon and quartz wafers or small samples with aluminium or ALD deposited Al2O3 and TiO2. Other materials might be allowed in the furnace, but this requires a permision from the Thin Film group. Also please check the cross contamination information in LabManager, before you use the furnace.
The furnace is the lowest of the C-stack furnaces positioned in cleanroom B-1. .
The user manual, technical information and contact information can be found in LabManager:
Process knowledge
Purpose |
| |
---|---|---|
Process parameter range | Process Temperature |
|
Process pressure |
| |
Gas flows |
| |
Substrates | Batch size |
|
Substrate materials allowed |
|
Oxidation uniformity for 6" wafers
In November 2023 an oxygen (O2) mass flow controller was connected to the furnace, so that it became possible to oxidize different wafers and samples in the furnace.
The C4 furnace is made for processing of 4" wafers placed vertically in a quartz boat. However, it is possible to process 6" wafers (or small sample placed on a 6" wafer), if they are placed horizontally on the boat.
Normally only one 6" wafer is be processed, because the temperature flat zone, i.e. the area where the temperature is uniform, it only a little longer than one quartz boat. The teh
It was tried to oxidize two 6" wafers at the same time in the furnace.
Process parameters:
- Recipe: "DRY1050"
- Oxidation temperature: 1050 oC
- Oxidation time: 1 h 40 min

