Specific Process Knowledge/Back-end processing/Polymer Injection Molder/Process: Difference between revisions
Line 12: | Line 12: | ||
<br> | <br> | ||
*'''Total time''': In the bottom of the screen a progress bar will indicate progress for the currently running cycle. Please note that the time axis of the progress bars do NOT autoscale. Min and max time scale values have to entered manually (but since the total cycle time for both the current and last cycle is shown right above, it's very easy to enter a sensible value). | *'''Total time''': In the bottom of the screen a progress bar will indicate progress for the currently running cycle. Please note that the time axis of the progress bars do NOT autoscale. Min and max time scale values have to entered manually (but since the total cycle time for both the current and last cycle is shown right above, it's very easy to enter a sensible value). | ||
<br><br><br><br><br><br><br><br><br><br> | |||
The injection molding machine also has tool for monitoring process parameters during the injection phase. To ensure reproducible results it can be beneficial to monitor parameters that are tightly linked to sample quality/properties. This can be done using the 'Micrograph' tool: | The injection molding machine also has tool for monitoring process parameters during the injection phase. To ensure reproducible results it can be beneficial to monitor parameters that are tightly linked to sample quality/properties. This can be done using the 'Micrograph' tool: | ||
<br> | <br> |
Revision as of 11:51, 12 February 2018
Process overview
Once a process is running satisfactory, the machine also has tool that can be used for monitoring a running process. These tools can be help to ensure desired sample quality and reproducibility.
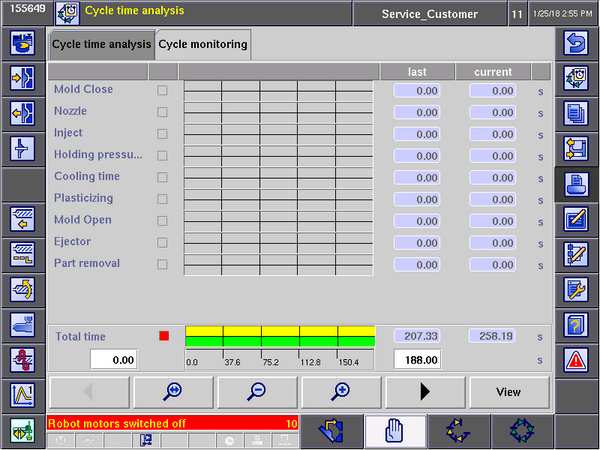
- Mold Close to Part removal: In the left part of the screen the individual phases of the injection molding cycle is listed. In the center of the screen, progress bars will indicate which phases are currently active. Note that the 'Part removal' step of Variotherm processes often takes quite a long time. This is because the 'Mold pause time' delay (mentioned in section '9. Ejection') used for reheating the mold is included in this step.
- Retract profile: This parameter controls the speed profile as the tower moves backwards and retracts the nozzle from the mold inlet port. Again, the default settings will work fine for most applications.
- Last and Current columns: In this column it's possible to see how long time each phase takes in the currently active cycle. For comparison the corresponding time during the last cycle is also listed.
- Total time: In the bottom of the screen a progress bar will indicate progress for the currently running cycle. Please note that the time axis of the progress bars do NOT autoscale. Min and max time scale values have to entered manually (but since the total cycle time for both the current and last cycle is shown right above, it's very easy to enter a sensible value).
The injection molding machine also has tool for monitoring process parameters during the injection phase. To ensure reproducible results it can be beneficial to monitor parameters that are tightly linked to sample quality/properties. This can be done using the 'Micrograph' tool:
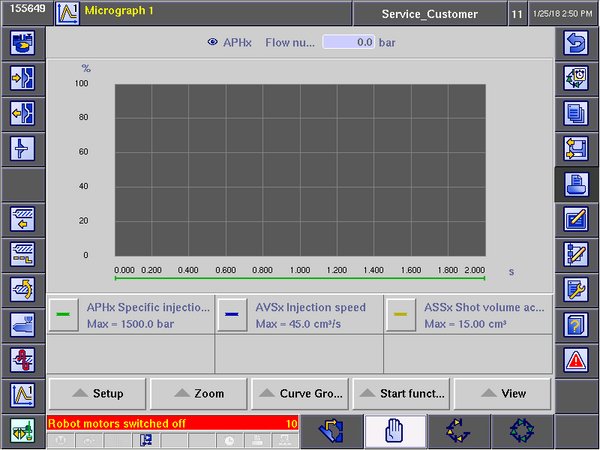
- Force build-up time: This setting defines how long time the machine has to build up the nozzle contact force. A value of 0,2-0,5 sec works fine for most applications
- Contact force: This parameter defines how hard the nozzle presses against the inlet port during injection and after/holding pressure. Please do not increase this value above 15 kN without contacting DTU Danchip as this may damage the nozzle tip or the mold inlet port! For polymers that undergo significant shear thinning (such as PP and PE) contact forces around 14 kN can be required (depends on injection speed) while lower contact forces (10 - 12 kN) will be sufficient for most other polymers.
- Delay time retraction: In some cases it may be desirable to maintain the inlet port at high temperature after injection and holdin/after pressure. In this case a delay can be entered here (usually 5 - 10 seconds is fine). Keep in mind that if the sum of 'Plasticizing delay time' described earlier and the 'Delay time retraction' on this page exceeds the cooling time, this will cause a delay in the injection molding cycle (thus increasing the effective cooling time).
There are also other possibilities for documenting and monitoring injection molding processes.