Specific Process Knowledge/Thin film deposition/Deposition of Alumina: Difference between revisions
Line 18: | Line 18: | ||
|-style="background:silver; color:black" | |-style="background:silver; color:black" | ||
! | ! | ||
![[Specific Process Knowledge/Thin film deposition/Lesker|Sputter System Lesker]] | ![[Specific Process Knowledge/Thin film deposition/Lesker|Sputter System Lesker]] | ||
![[Specific Process Knowledge/Thin film deposition/ | ![[Specific Process Knowledge/Thin film deposition/Multisource PVD|Cryofox PVD co-sputter/evaporation]] | ||
![[Specific Process Knowledge/Thin film deposition/ALD Picosun R200|ALD Picosun 200]] | ![[Specific Process Knowledge/Thin film deposition/ALD Picosun R200|ALD Picosun 200]] | ||
|- | |- | ||
Line 28: | Line 27: | ||
!Generel description | !Generel description | ||
| | | | ||
| | | | ||
| | | | ||
*ALD (atomic layer deposition) of Al<sub>2</sub>O<sub>3</sub> | |||
*ALD (atomic layer deposition) of | |||
|- | |- | ||
Line 42: | Line 36: | ||
!Stoichiometry | !Stoichiometry | ||
| | | | ||
| | | | ||
| | | | ||
Al<sub>2</sub>O<sub>3</sub>, very good | |||
|- | |- | ||
Line 55: | Line 45: | ||
!Film Thickness | !Film Thickness | ||
| | | | ||
| | | | ||
| | | | ||
* 0nm - 100nm | * 0nm - 100nm | ||
Line 67: | Line 53: | ||
!Deposition rate | !Deposition rate | ||
| | | | ||
| | | | ||
| | | | ||
* | * (temperature dependent) | ||
|- | |- | ||
Line 81: | Line 62: | ||
!Step coverage | !Step coverage | ||
| | | | ||
| | | | ||
| | | | ||
*Very good. Covers sample everywhere (but long purge time needed for very high aspect ratio structures) | *Very good. Covers sample everywhere (but long purge time needed for very high aspect ratio structures) | ||
Line 93: | Line 70: | ||
!Process Temperature | !Process Temperature | ||
| | | | ||
| | | | ||
| | | | ||
*120<sup>o</sup>C - 150<sup>o</sup>C: | |||
*120<sup>o</sup>C - 150<sup>o</sup>C: | |||
|- | |- | ||
Line 107: | Line 79: | ||
!More info on TiO2 | !More info on TiO2 | ||
| | | | ||
| | | | ||
| | | | ||
*[[Specific Process Knowledge/Thin film deposition/ALD Picosun R200/TiO2 deposition using ALD|TiO2 deposition using ALD]] | *[[Specific Process Knowledge/Thin film deposition/ALD Picosun R200/TiO2 deposition using ALD|TiO2 deposition using ALD]] | ||
Line 121: | Line 89: | ||
!Substrate size | !Substrate size | ||
| | | | ||
| | | | ||
| | | | ||
*1-5 100 mm wafers | *1-5 100 mm wafers | ||
Line 144: | Line 100: | ||
!'''Allowed materials''' | !'''Allowed materials''' | ||
| | | | ||
| | | | ||
| | | |
Revision as of 11:21, 7 September 2015
THIS PAGE IS UNDER CONSTRUCTION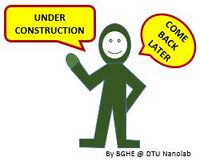
Feedback to this page: click here
Deposition of aluminium oxide
Aluminium oxide (Alumina, Al2O3 ) can be deposited by use of ALD (atomic layer deposition) or by a sputter technique in the Lesker Sputter System or the Cryofox PVD co-sputter/evaporation. During the sputter deposition oxygen is added to the chamber resulting in aluminium oxide on the sample
Comparison of the methods for deposition of Alumium Oxide
Sputter System Lesker | Cryofox PVD co-sputter/evaporation | ALD Picosun 200 | |
---|---|---|---|
Generel description |
| ||
Stoichiometry |
Al2O3, very good | ||
Film Thickness |
| ||
Deposition rate |
| ||
Step coverage |
| ||
Process Temperature |
| ||
More info on TiO2 | |||
Substrate size |
| ||
Allowed materials |
|