Specific Process Knowledge/Lithography/Development: Difference between revisions
Line 445: | Line 445: | ||
Developer: TMAH Manual is a manually operated, single substrate or chip spray-puddle developer. It uses the TMAH based AZ 726 MIF developer (2.38 % TMAH in water with a small amount of wetting agent). The substrates or chips are loaded manually one by one into the developer. Developer dispense, puddle time, water rinse, and drying is performed automatically by the equipment. | Developer: TMAH Manual is a manually operated, single substrate or chip spray-puddle developer. It uses the TMAH based AZ 726 MIF developer (2.38 % TMAH in water with a small amount of wetting agent). The substrates or chips are loaded manually one by one into the developer. Developer dispense, puddle time, water rinse, and drying is performed automatically by the equipment. | ||
The spray nozzle makes it difficult to build up a perfect puddle on 4" or 6" substrates which affects the uniformity of the development. Pre-wetting during dispense or agitation during development may give better | The spray nozzle makes it difficult to build up a perfect puddle on 4" or 6" substrates which affects the effectiveness and uniformity of the development. Pre-wetting during dispense or agitation during development may give better results. | ||
'''The user manual, user APV, and contact information can be found in [http://labmanager.danchip.dtu.dk/function.php?module=Machine&view=view&mach=324 LabManager]''' | '''The user manual, user APV, and contact information can be found in [http://labmanager.danchip.dtu.dk/function.php?module=Machine&view=view&mach=324 LabManager]''' |
Revision as of 15:35, 11 June 2015
Feedback to this page: click here
Developers: Comparison Table
Equipment | Developer-1 and 2 | Developer: 6inch | SU8-Developer | Developer: TMAH Manual | Developer: TMAH UV-lithography | |
---|---|---|---|---|---|---|
Purpose |
Development of
|
Development of
|
Development of
|
Development of
|
Development of
Post-exposure baking | |
Developer |
AZ 351B diluted 1:5 in water (NaOH and sodium borate salt) |
AZ 351B diluted 1:5 in water (NaOH and sodium borate salt) |
mr-Dev 600 (PGMEA) |
AZ 726 MIF (2.38% TMAH in water) |
AZ 726 MIF (2.38% TMAH in water) | |
Method | Development |
Submersion |
Submersion |
Submersion |
Spray/Puddle |
Puddle |
Handling |
Cassette |
Cassette |
Single wafer holder |
Edge handling chuck or chip "basket" |
Vacuum chuck | |
Process parameters | Temperature |
22°C |
22°C |
Room temperature |
Room temperature |
Room temperature |
Agitation |
Manual |
Circulation and mechanical |
Magnetic stirrer |
Rotation |
Rotation | |
Rinse |
DI water |
DI water |
IPA |
DI water |
DI water | |
Substrates | Substrate size |
|
|
|
|
|
Allowed materials |
Silicon, glass, and polymer substrates Film or pattern of all types |
Silicon, glass, and polymer substrates Film or pattern of all types |
Silicon and glass substrates Film or pattern of all but Type IV |
Silicon, glass, and polymer substrates Film or pattern of all types |
Silicon and glass substrates Film or pattern of all but Type IV | |
Batch |
1-8 |
1-25 |
1-6 |
1 |
1-25 |
Developer-1 and Developer-2
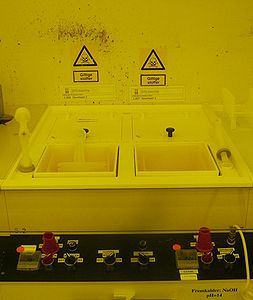
Feedback to this section: click here
Developer-1 and Developer-2 are manual developer baths for submersion development of AZ 5214E and AZ 4562 resists in AZ 351B developer. The developer is mixed 1:5 in water by the user prior to development start, and the wafer cassette is agitated manually by the user during development. The development time is controlled manually by the user. After development, the substrates are rinsed with water in the bench.
The user APV, and contact information can be found in LabManager: Developer-1 Developer-2
Process information
Standard development time using vigorous agitation:
AZ 5214E:
- 1.5µm resist: 60 sec
- 2.2µm resist: 70 sec
- 4.2µm resist: 3 min
AZ 4562:
- 10µm resist: 5 min
Standard development procedure:
- Before using one of developer baths, please check the "Litho4_Dev-7up-KOH" logbook to find out when they were last used. A fresh bath can be reused without problems.
- The main rule is a developer made yesterday must be changed.
- During development, agitate the substrates by moving the carrier up and down.
- Rinse substrates with water for 4-5 min. after development.
- Spin-dry substrates or dry with nitrogen gun after rinsing.
Procedure for making a new developer
1. Switch off the heater, and dump the old developer.
2. 800ml "Developer AZ 351B" is mixed with 4000ml water in a special container in the fume hood.
3. Fill the bath with the developer mixture, and heat it to 22°C before use.
Purpose |
Development of
| |
---|---|---|
Developer |
AZ 351B diluted 1:5 in water (NaOH and sodium borate salt) | |
Method | Development |
Submersion |
Handling |
Cassette | |
Process parameters | Temperature |
22°C |
Agitation |
Manual | |
Rinse |
DI water | |
Substrates | Substrate size |
|
Allowed materials |
Silicon, glass, and polymer substrates Film or pattern of all types | |
Batch |
1-8 |
Developer-6inch
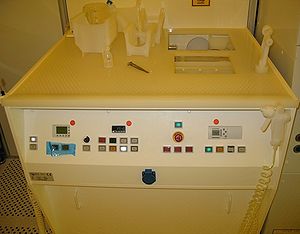
Feedback to this section: click here
The Developer: 6inch bench is an automated developer bath for submersion development of AZ 5214E and AZ 4562 resists in AZ 351B developer. The developer is mixed 1:5 in water by the equipment prior to development start. The developer is circulated during development, and the wafer cassette may be agitated by a mechanical elevator. The development time is controlled manually by the user. After development, the substrates are rinsed with water in the bench.
The user manual, user APV, and contact information can be found in LabManager
Process information
Standard development time:
AZ 5214E:
- 1.5µm resist: 60 sec
- 2.2µm resist: 70 sec
- 4.2µm resist: 3 min
AZ 4562:
- 10µm resist: 5 min
Purpose |
Development of
| |
---|---|---|
Developer |
AZ 351B diluted 1:5 in water (NaOH and sodium borate salt) | |
Method | Development |
Submersion |
Handling |
Cassette | |
Process parameters | Temperature |
22°C |
Agitation |
Circulation and mechanical | |
Rinse |
DI water | |
Substrates | Substrate size |
|
Allowed materials |
Silicon, glass, and polymer substrates Film or pattern of all types | |
Batch |
1-25 |
SU8-Developer
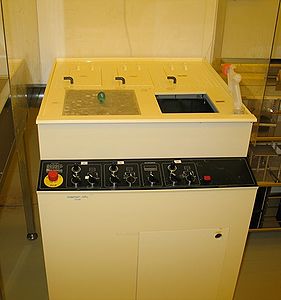
Feedback to this section: click here
The SU8-Developer bench is a manually operated chemical bench for submersion development of SU-8 photoresist in PGMEA (supplied in the cleanroom as mr-Dev 600). The development process is in two stages; one bath (FIRST) to dissolve the bulk of the resist, and a second, cleaner bath (FINAL) to finish the development. The development time is controlled manually by the user. After development, the substrates are rinsed with IPA and dried in the bench.
The user manual, user APV, and contact information can be found in LabManager
Process information
Several aspects of the outcome of SU-8 processing are affected by the development process. The lithographic resolution is affected by the time between PEB (post-exposure bake) and development, as the cross-linking process continues in the interface between exposed and unexposed regions even at room temperature. Cracks in the structures is affected by two things; the development time, and how much has previously been developed in the developer bath. Cracking is worse with longer development time, and worst in a new developer bath. The effect of the developer use quickly saturates (5-10 wafers). Finally, the stability of fine structures (high aspect ratio) is affected by the rinse after development, as the lower surface tension of IPA compared to PGMEA reduces pattern collapse during drying.
Development time is strongly dependent on the SU-8 thickness. Here are some suggestions:
- 2-5µm: 2 min. in FIRST; 2 min. in FINAL
- 40µm: 5 min. in FIRST; 5 min. in FINAL (however, 3 min. in FIRST and 2 min. in FINAL is sufficient)
- 180-250µm: 15 min. in FIRST; 15 min. in FINAL
Purpose |
Development of
| |
---|---|---|
Developer |
mr-Dev 600 (PGMEA) | |
Method | Development |
Submersion |
Handling |
Single wafer holder | |
Process parameters | Temperature |
Room temperature |
Agitation |
Magnetic stirrer | |
Rinse |
IPA | |
Substrates | Substrate size |
|
Allowed materials |
Silicon and glass substrates Film or pattern of all but Type IV | |
Batch |
1-6 |
Developer: TMAH Manual
Feedback to this section: click here
Developer: TMAH Manual is a manually operated, single substrate or chip spray-puddle developer. It uses the TMAH based AZ 726 MIF developer (2.38 % TMAH in water with a small amount of wetting agent). The substrates or chips are loaded manually one by one into the developer. Developer dispense, puddle time, water rinse, and drying is performed automatically by the equipment.
The spray nozzle makes it difficult to build up a perfect puddle on 4" or 6" substrates which affects the effectiveness and uniformity of the development. Pre-wetting during dispense or agitation during development may give better results.
The user manual, user APV, and contact information can be found in LabManager
Process information
Process recipes
- SP 60s: Single puddle, 60s. Rinse and dry.
- SP 60s agi: Single puddle, 60s. 15 cycles per minute agitation during development. Rinse and dry.
- SP 60s prw: Single puddle, 60s. Pre-wetting step during developer dispense. Rinse and dry.
Utility recipes
- UTIL-DR: Dome rinse.
- UTIL-BE: Bottle empty. Danchip use only.
Purpose |
Development of
| |
---|---|---|
Developer |
AZ 726 MIF (2.38% TMAH in water) | |
Method | Development |
Spray/Puddle |
Handling |
Edge handling chuck or chip "basket" | |
Process parameters | Temperature |
Room temperature |
Agitation |
none | |
Rinse |
DI water | |
Substrates | Substrate size |
|
Allowed materials |
Silicon, glass, and polymer substrates Film or pattern of all types | |
Batch |
1 |
Developer TMAH UV-lithography
Feedback to this section: click here
Developer TMAH UV-lithography was released Q4 2014.
The user manual, user APV, and contact information can be found in LabManager
Process information
Purpose |
Development of
| |
---|---|---|
Developer |
AZ 726 MIF (2.38% TMAH in water) | |
Method | Development |
Puddle |
Handling |
Vacuum chuck | |
Process parameters | Temperature |
Room temperature |
Agitation |
Rotation | |
Rinse |
DI water | |
Substrates | Substrate size |
|
Allowed materials |
Silicon and glass substrates Film or pattern of all except Type IV | |
Batch |
1-25 |