Specific Process Knowledge/Doping: Difference between revisions
Line 37: | Line 37: | ||
|-style="background:WhiteSmoke; color:black" | |-style="background:WhiteSmoke; color:black" | ||
!Generel description | !Generel description | ||
|Dopants introduced by diffusion from gas-phase ( | |Dopants introduced by diffusion from gas-phase (POCl<sub>3</sub>) | ||
|Dopants introduced by diffusion from solid source wafers | |Dopants introduced by diffusion from solid source wafers | ||
|Deposition of doped thin film (oxides or nitrides) | |Deposition of doped thin film (oxides or nitrides) | ||
Line 64: | Line 64: | ||
!Dopant | !Dopant | ||
| | | | ||
*Phosporous ( | *Phosporous (POCl<sub>3</sub>) | ||
| | | | ||
*Boron (solid source wafers containing B<sub>2</sub>O<sub>3</sub>) | *Boron (solid source wafers containing B<sub>2</sub>O<sub>3</sub>) | ||
Line 70: | Line 70: | ||
*Phosphorous (PH<sub>3</sub>) | *Phosphorous (PH<sub>3</sub>) | ||
*Boron (B<sub>2</sub>H<sub>6</sub>) | *Boron (B<sub>2</sub>H<sub>6</sub>) | ||
* | *Germanium (GeH<sub>4</sub>) | ||
| | | | ||
*Phosphorous (PH<sub>3</sub>) | *Phosphorous (PH<sub>3</sub>) |
Revision as of 17:06, 30 October 2014
THIS PAGE IS UNDER CONSTRUCTION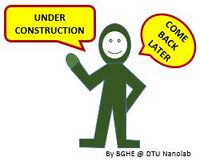
Feedback to this page: click here
Doping your wafer
This page is about doping your wafer or making a thin film layer doped with boron, phosphorous or Germanium.
- Dope with Phosphorous - Doping Silicon wafers with phosphorous by thermal predeposition and drive-in
- Dope with Boron - Doping Silicon wafers with boron by thermal predeposition and drive-in
- Furnace LPCVD PolySilicon - Deposition of PolySi doped with B or P
- PECVD - Making boron glass (BSG), phosphorus glass (PSG), boron-phosphorous glass PBSG or germanium doped glass
- Ion implantation
Comparison of different doping processes
Phosphorous predep | Boron predep | PECVD doped thin film | Doped Poly Si | |
---|---|---|---|---|
Generel description | Dopants introduced by diffusion from gas-phase (POCl3) | Dopants introduced by diffusion from solid source wafers | Deposition of doped thin film (oxides or nitrides) | Dopants introduced by in-situ doping of poly/amorphous Si |
Process Temperature |
|
|
|
|
Dopant |
|
|
|
|
Substrate size |
|
|
|
|
Allowed materials |
|
|
|
|
Ion implantation
Ion implantation cannot be done at Danchip. IBS offers ion-beam implantation as a service. See more at the homepage of IBS: http://www.ion-beam-services.com/about_us.htm