Specific Process Knowledge/Characterization/SEM: Scanning Electron Microscopy: Difference between revisions
No edit summary |
No edit summary |
||
Line 1: | Line 1: | ||
== Etching using the dry etch technique RIE (Reactive Ion Etch) == | |||
[[image:Cluster1.jpg|200x200px|right|thumb|RIE1 (part of Cluster1) - positioned in cleanroom2]] | |||
[[image:Cluster2.jpg|200x200px|right|thumb|RIE2 (part of Cluster2)- positioned in cleanroom3]] | |||
At Danchip we have three RIE's. Two (RIE1 and RIE2) for etching silicon based materials, resist and polymers (mainly RIE2) and one (III-V RIE) for etching III-V materials. Here only RIE1 and RIE2 will be described. | |||
The hardware of RIE1 and RIE2 is very similar, but you cannot count on that identical recipes on RIE1 and RIE2 perform exactly the same. In addition to that the main difference between RIE1 and RIE2 is the cleanness of the two equipment. In rough terms RIE1 is the clean system and the RIE2 is the dirty system. This means that in RIE2 opposed to RIE1 it is allowed to have small amounts of metals exposed to the plasma. | |||
'''The user manuals, quality control procedures and results, user APVs, technical information and contact information can be found in LabManager:''' | |||
[http://labmanager.danchip.dtu.dk/function.php?module=Machine&view=view&mach=18 RIE1 info page in LabManager], | |||
[http://labmanager.danchip.dtu.dk/function.php?module=Machine&view=view&mach=19 RIE2 info page in LabManager] | |||
== Process information == | |||
*[[Specific Process Knowledge/Etch/Etching of Silicon/Si etch using RIE1 or RIE2|Etch of silicon using RIE]] | |||
*[[Specific Process Knowledge/Etch/Etching of Silicon Oxide/SiO2 etch using RIE1 or RIE2|Etch of silicon oxide using RIE]] | |||
*[[Specific Process Knowledge/Etch/Etching of Silicon Nitride/Etch of Silicon Nitride using RIE|Etch of silicon nitride using RIE]] | |||
*[[Specific Process Knowledge/Etch/Etching of Polymer/Etch of Photo Resist using RIE|Etch of photo resist using RIE]] | |||
<br clear="all" /> | |||
==Equipment performance and process related parameters== | |||
{| border="2" cellspacing="0" cellpadding="2" | |||
!colspan="2" border="none" style="background:silver; color:black;" align="center"|Equipment | |||
|style="background:WhiteSmoke; color:black"|<b>RIE1</b> | |||
|style="background:WhiteSmoke; color:black"|<b>RIE2</b> | |||
|- | |||
!style="background:silver; color:black;" align="center"|Purpose | |||
|style="background:LightGrey; color:black"|Dry etch of | |||
|style="background:WhiteSmoke; color:black"| | |||
*Silicon | |||
*Silicon oxide | |||
*Silicon (oxy)nitride | |||
*Resist | |||
|style="background:WhiteSmoke; color:black"| | |||
*Silicon | |||
*Silicon oxide | |||
*Silicon (oxy)nitride | |||
*Resist and other polymers | |||
|- | |||
!style="background:silver; color:black" align="center" valign="center" rowspan="2"|Performance | |||
|style="background:LightGrey; color:black"|Etch rates | |||
|style="background:WhiteSmoke; color:black"| | |||
*Silicon: ~0.04-0.8 µm/min | |||
*Silicon oxide: ~0.02-0.15 µm/min | |||
*Silicon (oxy)nitride: ~0.02-? µm/min | |||
|style="background:WhiteSmoke; color:black"| | |||
*Silicon: ~0.04-0.8 µm/min | |||
*Silicon oxide: ~0.02-0.15 µm/min | |||
*Silicon (oxy)nitride: ~0.02-? µm/min | |||
|- | |||
|style="background:LightGrey; color:black"|Anisotropy | |||
|style="background:WhiteSmoke; color:black"| | |||
*Can vary from isotropic to anisotropic with vertical | |||
:sidewalls and on to a physical etch where the sidewalls | |||
:are angled but without etching under the mask. | |||
|style="background:WhiteSmoke; color:black"| | |||
*Can vary from isotropic to anisotropic with vertical | |||
:sidewalls and on to a physical etch where the sidewalls | |||
:are angled but without etching under the mask. | |||
|- | |||
!style="background:silver; color:black" align="center" valign="center" rowspan="3"|Process parameter range | |||
|style="background:LightGrey; color:black"|Max pressure | |||
|style="background:WhiteSmoke; color:black"| | |||
*800 mTorr | |||
|style="background:WhiteSmoke; color:black"| | |||
*949 mTorr | |||
|- | |||
|style="background:LightGrey; color:black"|Max R.F. power | |||
|style="background:WhiteSmoke; color:black"| | |||
*600 W | |||
|style="background:WhiteSmoke; color:black"| | |||
*600 W | |||
|- | |||
|style="background:LightGrey; color:black"|Gas flows | |||
|style="background:WhiteSmoke; color:black"| | |||
*SF<sub>6</sub>: 0-52 sccm | |||
*O<sub>2</sub>: 0-99 sccm | |||
*CHF<sub>3</sub>: 0-100 sccm | |||
*CF<sub>4</sub>: 0-42 sccm | |||
*Ar: 0-146 sccm | |||
*N<sub>2</sub>: 0-100 sccm | |||
*C<sub>2</sub>F<sub>6</sub>: 0-24 sccm | |||
|style="background:WhiteSmoke; color:black"| | |||
*SF<sub>6</sub>: 0-130 sccm | |||
*O<sub>2</sub>: 0-99 sccm | |||
*CHF<sub>3</sub>: 0-99 sccm | |||
*CF<sub>4</sub>: 0-84 sccm | |||
*Ar: 0-145 sccm | |||
*N<sub>2</sub>: 0-99 sccm | |||
|- | |||
!style="background:silver; color:black" align="center" valign="center" rowspan="3"|Substrates | |||
|style="background:LightGrey; color:black"|Batch size | |||
|style="background:WhiteSmoke; color:black"| | |||
*1 4" wafer | |||
*1 2" wafer (use Al carrier with Si dummy wafer) | |||
*Several smaller samples (use Al carrier with Si dummy wafer) | |||
|style="background:WhiteSmoke; color:black"| | |||
*1 4" wafer (use Al carrier with Si dummy wafer) | |||
*1 2" wafer (use Al carrier with Si dummy wafer) | |||
*1 6" wafer (requires 6" setup) | |||
*Several smaller samples (use Al carrier with Si dummy wafer) | |||
|- | |||
| style="background:LightGrey; color:black"|Allowed materials | |||
|style="background:WhiteSmoke; color:black"| | |||
*Silicon | |||
*Silicon oxide (with boron, phosphorous and germanium) | |||
*Silicon nitrides (with boron, phosphorous and germanium) | |||
*Pure quartz, fused silica (not Pyrex, Tempax and other glasses) | |||
*Resists: AZ resists, e-beam resists, SU8, DUV resists | |||
*Aluminium as thin film layer on your sample | |||
|style="background:WhiteSmoke; color:black"| | |||
*Silicon | |||
*Silicon oxide (with boron, phosphorous and germanium) | |||
*Silicon nitrides (with boron, phosphorous and germanium) | |||
*Pure quartz, fused silica (not Pyrex, Tempax and other glasses) | |||
*Resists: AZ resists, e-beam resists, SU8, DUV resists | |||
*Other olymers (ask the Plasma group for permission) | |||
*Aluminium as thin film layer on your sample | |||
*Other metals (<5% coverage of the wafer) | |||
|- | |||
|} | |||
=The Scanning Electron Microscopes at Danchip = | =The Scanning Electron Microscopes at Danchip = | ||
Revision as of 12:05, 30 November 2012
Etching using the dry etch technique RIE (Reactive Ion Etch)
At Danchip we have three RIE's. Two (RIE1 and RIE2) for etching silicon based materials, resist and polymers (mainly RIE2) and one (III-V RIE) for etching III-V materials. Here only RIE1 and RIE2 will be described.
The hardware of RIE1 and RIE2 is very similar, but you cannot count on that identical recipes on RIE1 and RIE2 perform exactly the same. In addition to that the main difference between RIE1 and RIE2 is the cleanness of the two equipment. In rough terms RIE1 is the clean system and the RIE2 is the dirty system. This means that in RIE2 opposed to RIE1 it is allowed to have small amounts of metals exposed to the plasma.
The user manuals, quality control procedures and results, user APVs, technical information and contact information can be found in LabManager:
Process information
- Etch of silicon using RIE
- Etch of silicon oxide using RIE
- Etch of silicon nitride using RIE
- Etch of photo resist using RIE
Equipment | RIE1 | RIE2 | |
---|---|---|---|
Purpose | Dry etch of |
|
|
Performance | Etch rates |
|
|
Anisotropy |
|
| |
Process parameter range | Max pressure |
|
|
Max R.F. power |
|
| |
Gas flows |
|
| |
Substrates | Batch size |
|
|
Allowed materials |
|
|
The Scanning Electron Microscopes at Danchip
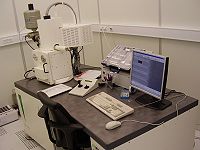
We have four SEM's at Danchip. Together they cover a wide range of needs both in the cleanroom and outside: From the fast in-process verification of different process parameters such as etch rates, step coverages or lift-off quality to the ultra high resolution images on any type of sample intended for publication.
The 'old workhorse' SEM that will cover most users needs is the Leo SEM. It is a very reliable and rugged instrument that provides high quality images of most samples. Due to its robustness new users only need a mandatory two hour training session before they are free to use it by themselves. It is a standard high vacuum instrument equipped with a field emission gun, 3 high vacuum electron detectors (Se2, Inlens and RBSD) and a Röntec EDX system. You can obtain excellent images on a large variety of materials such as semiconductors, semiconductor oxides or nitrides, metals, thin films and some polymers. We prefer that new users that have no prior SEM experience get trained on the Leo SEM before they start using the FEI or Zeiss.
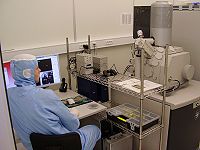
The FEI SEM has been acquired to cope with the growing need for polymer and e-beam related imaging. It is an extremely versatile microscope with two vacuum modes (High Vacuum and Low Vacuum) and 7 different detectors, offering excellent resolution on any type of sample or material. This great performance, however, requires a skilled operator that knows how to achieve it. Also, we have learned that the high degree of sophistication and the great number of detectors make it much less robust compared to the other SEM's. It is therefore the intention that only users with special needs (for instance thick polymers, glass substrates or EDX/micromanipulator experiments) that will be trained. Furthermore, the instrument is equipped with a Oxford Inca EDX system and a Kleindiek micromanipulator with a Capres 4 point probe.
The Zeiss SEM is the newest SEM in the cleanroom.
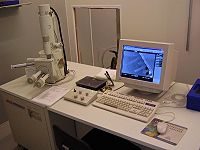
Jeol SEM The less advanced Jeol SEM offers a great alternative for many types of SEM needs. If you have to check the result of an etch process, a lift-off etc. before you proceed with the process sequence, the Jeol SEM is a much better choice. It is simple, faster to use, has a very low sample exchange time and is by far more accessible than any of the other SEMs. There is a very good chance that it is free when you need it. On heavily charging polymers such as SU-8 it even does a better job than the Leo SEM. To use it, a 1-2 hour training session is necessary.
SEM - Zeiss | SEM - FEI | SEM - Leo | SEM - Jeol | |
---|---|---|---|---|
Model | Zeiss Supra 55 VP | FEI Nova 600 NanoSEM | Leo 1550 SEM | Jeol JSM 5500 LV SEM |
Electron emitter type | FEG (Field Emission Gun) | FEG (Field Emission Gun) | FEG (Field Emission Gun) | Tungsten filament |
Vacuum modes | High vacuum (>2*10mbar) and Low vacuum (0.1-1.9 mbar) | High vacuum (>2*10mbar) | High vacuum and Low vacuum | |
Detectors | High and Low vacuum detectors of SE and BSE electrons, HiVac Inlens SE detector and high resolution Low vacuum detector | SE, Inlens SE and BSE detectors | High vacuum SE and BSE detector | |
Substrate size | Up to 6" wafer with full view | Up to 6" wafer with 4" full view | Up to 4" wafer with full view | |
Additional equipment | Kleindiek micromanipulator with Capres 4 point probe | |||
Best obtainable lateral resolution (strongly dependent on user skills and sample type) | Down to 1-2 nm (Limiting factor: Beam) | Down to 10 nm (Limiting factor: Vibrations) | Down to 20-30 nm (Limiting factor: Vibrations) | |
General availability | Good | Poor | Excellent | |
Ease of use | A sophisticated user interface with many features and many different detectors: Complicated | A simple user interface with joystick and a limited number of detectors: Relatively simple | A simple user interface with joystick with one detector: Very simple | |
User level access | Only experienced SEM users, masters/Ph.D students with special needs will be trained | Any cleanroom user | Any cleanroom user | |
Best usage | High resolution imaging of any sample | High resolution imaging of any non-polymer sample | Fast in-process imaging | |
EDX analysis | Oxford Inca system | Röntec system | Not available |