Specific Process Knowledge/Thermal Process/RTP Jipelec 2: Difference between revisions
Line 9: | Line 9: | ||
=RTP2 Jipelec - Rapid Thermal Processor= | =RTP2 Jipelec - Rapid Thermal Processor= | ||
The main purpose of the RTP2 Jipelec is to perform thermal processes, using faster heating rates and shorter process durations when compared to conventional methods. This is called rapid thermal processing (RTP) and can be used to treat different types of samples. | The main purpose of the RTP2 Jipelec is to perform thermal processes, using faster heating rates and shorter process durations when compared to conventional methods. This is called rapid thermal processing (RTP) and can be used to treat different types of samples. |
Revision as of 11:49, 6 November 2023
Feedback to this page: click here
This page is written by DTU Nanolab internal
THIS PAGE IS UNDER CONSTRUCTION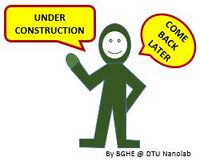
RTP2 Jipelec - Rapid Thermal Processor
The main purpose of the RTP2 Jipelec is to perform thermal processes, using faster heating rates and shorter process durations when compared to conventional methods. This is called rapid thermal processing (RTP) and can be used to treat different types of samples.
Rapid thermal processing typically includes RTA, i.e. Rapid Thermal Annealing, where samples are heated up very rapidly in a nitrogen or argon atmosphere. Contact alloying and RTN, i.e. Rapid Thermal Nitridation, might also be possible for some samples.
The Set-Up
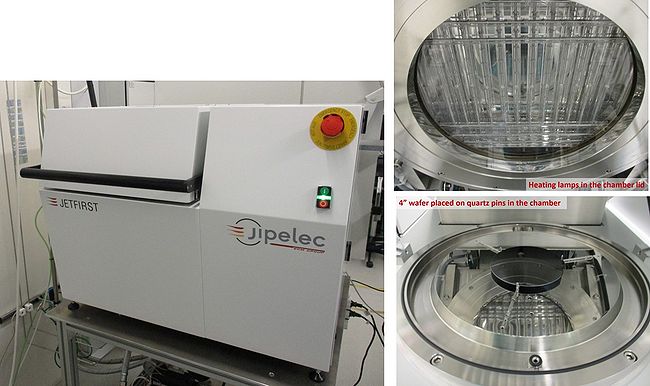
Jipelec JetFIRST 200 RTP (Rapid Thermal Processor/Annealer).
The main purpose of the machine is to anneal different samples very rapidly. Furthermore, the machine can be used for alloying of different materials.
The annealing is done in a process chamber on the machine, in which the samples are heated very rapidly by use of infra red lamps placed in the top of the chamber, directly above the sample(s). The chamber walls are cooled and remains cold during the annealing.
Samples can be wafers (2", 4", 6" and 8") or smaller samples made of different materials. In the process chamber, Si-based samples are normally placed on a 6" graphite susceptor and III-V and metals samples on a Si carrier wafer. Wafers can also be placed directly in the chamber.
The maximum annealing temperature is 1200 C. For temperatures above 700 C the annealing time is limited as can be seen in the table below.
The temperature is measured by either a thermocouple or an optical pyrometer . The temperature is regulated by a PID controller, thus the PID values will have to be optimized for each process and for each each susceptor or wafer size and thickness, annealing temperature, temperature ramping, pressure and gas flow settings etc. The responsible persons will help with the optimization of the PID parameters.
Annealings can be done at atmospheric pressure or in vacuum. It is also possible to apply a flow of either nitrogen or argon during the annealing, and forming gas (4 % H2/96 % N2) will be connected later.
The user manual, user APV, technical information and contact information can be found in LabManager:
Purpose | Rapid thermal processor/annealer | |
---|---|---|
Process parameter range | Process temperature |
Annealing temperature:
Temperature ramp:
|
Process pressure |
| |
Gases on the system |
Process gases:
Purge gas:
| |
Substrates | Batch size |
|
Substrate materials allowed |
|