Specific Process Knowledge/Characterization/Profiler: Difference between revisions
Line 170: | Line 170: | ||
The resolution is limited by the objectives and the pixel resolution. | The resolution is limited by the objectives and the pixel resolution. | ||
[[Image:3D examples.JPG|200px|right|thumb|From the Sensofar | [[Image:3D examples.JPG|200px|right|thumb|From the Sensofar Metrology, used with permission]] | ||
'''Analysis software:''' | '''Analysis software:''' |
Revision as of 17:16, 20 January 2023
Feedback to this page: click here
Overview of the Nanolab profilers
All the profilers are compared on the topographic measurement page.
The sections below describe each profiler (stylus profilers and optical profilers) in more detail.
Dektak XTA stylus profiler
The Dektak XTA stylus profiler from Brüker is used for profiling surfaces of samples with structures in the micro- and nanometer range. The size of the structures that can be measured is limited by the tip dimensions.
A profile measurement can be done across a specific structure by using a high magnification camera to locate the structure. It is also possible to program the stylus to measure in several positions, defined with respect to some deskew points. Stress measurements of thin films can be done by measuring the wafer bow.
The user manual, quality control procedure and results, technical information and contact information can be found in LabManager:
Info about measurement accuracy can be found here.
Purpose | Profiler for measuring micro structures |
|
---|---|---|
Performance | Scan range x y |
Line scan x: 50 µm to 55 mm in a single scan, up to 200 mm with stiching |
Scan range z |
50 Å to 1 mm | |
Resolution x y |
Down to 0.003 µm theoretically, in practice limited by the tip radius | |
Resolution z |
1 Å, 10 Å, 80 Å or 160 Å (for ranges 65 kÅ, 655 kÅ, 5240 kÅ and 1 mm respectively) | |
Height accuracy z (95 % confidence) |
For very well defined steps ~ 2 % for a 1 µm step and ~ 1 % for a 25 µm step (read about reducing and estimating the measurement uncertainty here) | |
Max scan depth as a function of trench width W |
1.2*(W[µm]-5µm) | |
Hardware settings | Tip radius |
|
Substrates | Substrate size |
|
Substrate materials allowed |
|
Stylus Profiler (Tencor P17)
The P17 Stylus Profiler from KLA Tencor is used in a similar manner to the Dektak XTA for profiling surfaces with structures in the micro- and submicrometer range as well as for measuring stress.
Compared to the DektakXT, the P17 has more advanced options for stress measurements: It allows the user to measure a stress map with up to 5° radial resolution. Programming and analyzing a sequence of predefined scans in fixed locations on a wafer is also easier and the manual for doing it much better for the P17 than for the DektakXT. A disadvantage of the P17 is that is can be hard to locate structures as the maximum field of view of the camera is 1x1.5 mm. We recommend having a map of the sample design available so you can easily locate the features of interest. Otherwise the P17 is easy to use, fast, and accurate, just like the DektakXT.
The user manual, quality control procedure and results, technical information and contact information can be found in LabManager:
Process information
- Info about measurement accuracy.
- Using the analysis software from outside the cleanroom: Apex software access & tips
- Info about making 2D stress measurements. This text was removed from the user manual in LabManager as most users make 3D stress measurements. It counts as "3D" even if you just wish to make 2 perpendicular scans. A "2D" stress scan means a single line scan per wafer - the software does not even allow manual rotation of the stage for this type of scan.
Acceptance test
- Acceptance test results on the P17
- Vendor's own conformity test results after installation

Purpose | Profiler for measuring microstructures |
|
---|---|---|
Performance | Scan range X Y |
Line scan X: 20 µm to 200 mm in a single scan. No stitching. Map scan XY: In principle any rectangle that can be inscribed in a 200 mm circle, but resolution is limited to max. 4 million points and scanning is slow. In practice to get good resolution scan a very small area (e.g., 100 x 500 µm) |
Scan range Z |
50 nm to 900 µm. It is possible to measure smaller steps but not recommended as the results may not be accurate. | |
Resolution X Y |
Down to 0.025 µm in theory, but the tip radius is 2 µm, so the meaningful resolution is at the same order of magnitude | |
Resolution Z |
0.01 Å, 0.08 Å, or 0.6 Å according to the manufacturer for ranges 13 µm, 131 µm, and 1 mm. Note the smallest of these values are purely theoretical as they are far below the lab's noise level. | |
Height accuracy z (95 % confidence) |
~ 2 % for the smallest range for a 1 micron step and ~ 1 % for a 25 micron step for well-defined steps that are easy to measure (read about reducing and estimating the measurement uncertainty here) | |
Max scan depth as a function of trench width W |
0.87*(W[µm]-2µm) = tan(60o)/2*(W[µm]-2µm) (empirically validated by Nanolab staff) | |
Hardware settings | Tip radius |
|
Substrates | Substrate size |
|
Substrate materials allowed |
|
Optical Profiler (Sensofar S Neox)
This section is written by Berit Herstrøm @DTU Nanolab if nothing else is stated
The Sensofar S Neox 3D Optical Profiler has a sensor head that combines confocal, interferometry and focus variation techniques as well as thick and thin film measurement capabilities.
The Neox sensor head provides standard microscope imaging, confocal imaging, confocal profiling, PSI (Phase Shift Interferometry), CSI (Coherence Scanning Interferometry), Active illumination (Ai) Focus Variation and high resolution thin film thickness measurements on a single instrument.
The main purpose is 3D topographic imaging of surfaces, step height measurements in smaller trenches/holes than can be obtained with standard stylus methods (i.e. with aspect ratios higher that 1:1), roughness measurements with larger FOV (Field Of View) than the AFM, but less horisontal resolution.
For most samples the optical profiler provides fast and easy information without any sample preparation. However, it can be necessary to cover thin transparent layers (< 2 µm) with a thin layer of metal.
The resolution is limited by the objectives and the pixel resolution.
Analysis software:
- Free analysis software for visualizing and analyzing AFM and Optical profiler files (Sensofar) Gwyddion
- SensoView software from Sensfar want also be downloaded for all users: U:\Nlab\CleanroomDrive\_Equipment\Optical profiler Sensofar\SensoVIEW 1.6.0
The user manual, technical information (SensoSCAN and SensoVIEW manuals) and contact information can be found in LabManager:
Optical profiler (Sensofar S Neox) info page in LabManager
Process Information
- Sensofar presentation on how the sensofar works (for the previous system but the techniques are the same)
- Neox leaflet including specifications
- Acceptance measurements on the S Neox Sensofar: Media:Acceptance measurements on Nanolab samples.pdf, measured at the acceptances test by Sensofar and Berit Herstrøm@ DTU Nanolab
- Results from the Optical Profiler (Sensofar) acceptance test - for the previous system - expired!!
Optical Profiler (Filmetrics)
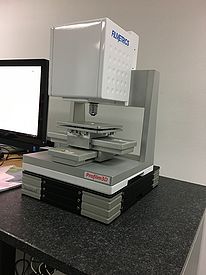
The Profilm3D optical profiler from Filmetrics uses white-light-interferometry (WLI) and phase-shifting-interferometry (PSI) to produce surface profiles and depth-of-field color images.
The main purpose is 3D topographic imaging of surfaces, step height measurements and roughness measurements with larger FOV (Field Of View) than the AFM, but less horisontal resolution.
For most samples the optical profiler provides fast and easy information without any sample preparation. However, it can be necessary to cover thin transparent layers (< 2 µm) with a thin layer of metal.
The resolution is limited by the objective and the sampling resolution.
The user manual, technical information and contact information can be found in LabManager:
Optical profiler (Filmetrics) info page in LabManager
Equipment | Optical profiler | |
---|---|---|
Purpose | 3D topographic imaging of surfaces. |
|
Posibilities | Interferometric profiling |
|
Performance | With the current 10x objective | |
Substrates | Substrate size |
|
Substrate materials allowed |
|
Dektak 3ST
The Dektak 3ST is intended for profile measurements on samples outside the cleanroom. It is located in the basement, building 346, room 904.
The user manual, technical information and contact information can be found in LabManager:
Dektak 3ST (Dektak) in LabManager
The computer connected to the Dektak 3ST is pretty old and runs Windows 98 SE. It is not connected to the network but traces can be saved on either USB memory stick or floppy disk. The USB driver is an old universal driver and has been shown to work with small size USB sticks. However it did not work with an 8GB Kingston stick.
Performance | Vertical Range |
|
---|---|---|
Scan length range |
| |
Stylus track force |
| |
Scan speed ranges |
| |
Materials | Allowed substrate materials |
|
Stylus Profiler: Dektak150
The stylus profiler Dektak150 is intended for profile measurements on samples outside the cleanroom. It is located in Packlab in building 347. Packlab is a low-class cleanroom. The Dekta150 is especially well suited for measuring soft samples as it can be adjusted to apply lower force than the other stylus profilers at Nanolab.
The user manual, technical information and contact information can be found in LabManager:
Stylus profiler:Dektak150 in LabManager
The computer is not connected to the network but data can be saved on a dedicated USB and transfered to a computer on the network.
Info about measurement accuracy can be found here.
Purpose | Profiler for measuring micro structures |
|
---|---|---|
Performance | Scan range x y |
Line scan x: 50 µm to 55 mm in a single scan |
Scan range z |
50 Å to 1 mm | |
Resolution x y |
Theoretically down to 0.003 µm (in practice the resolution is limited by the tip size) | |
Resolution z |
1Å (@65kÅ), 10Å (@655 kÅ), 80 Å (@5240 kÅ), 160 Å (@1mm) | |
Maximum sample thickness |
100 mm | |
Hardware settings | Tip radius |
|
Substrates | Substrate size |
|
Substrate materials allowed |
|