Specific Process Knowledge/Etch/DRIE-Pegasus: Difference between revisions
Line 45: | Line 45: | ||
*[[Specific Process Knowledge/Etch/DRIE-Pegasus/nanoetch|Nanostructure etches including nano1.42]] | *[[Specific Process Knowledge/Etch/DRIE-Pegasus/nanoetch|Nanostructure etches including nano1.42]] | ||
*[[Specific Process Knowledge/Etch/DRIE-Pegasus/ | *[[Specific Process Knowledge/Etch/DRIE-Pegasus/DUVetch|Etch processes with DUV masks]] | ||
*[[Specific Process Knowledge/Etch/DRIE-Pegasus/Barc|BARC etches]] | *[[Specific Process Knowledge/Etch/DRIE-Pegasus/Barc|BARC etches]] |
Revision as of 11:01, 2 June 2016
Feedback to this page: click here
The DRIE Pegasus at Danchip
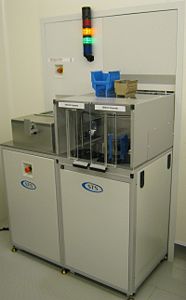
The Bosch process
The DRIE Pegasus is a state-of-art silicon dry etcher that offers outstanding performance in terms of etch rate, uniformity etc. It uses the so-called Bosch process to achieve excellent control of the etched features. Click HERE for more fundamental information of the system.
The user manual(s), quality control procedure(s) and results, user APV(s), technical information and contact information can be found in LabManager:
Equipment info in LabManager
Process information
Process notation
Describing a process recipe on the Pegasus may sometimes be difficult because of the great flexibility of the instrument. A compact and precise notation is therefore required for the recipes. Click here to find a short description of the official SPTS notation.
Hardware changes
A few hardware modifications have been made on the Pegasus since it was installed in 2010. The changes are listed below.
Other etch processes
More processes, such as for DUV resist, are currently being developed, but they are not quite 'ready for publication' at LabAdviser so please contact Jonas (mailto:jml@danchip.dtu.dk) for more information.
Advanced Processing - Henri Jansen style
Wafer bonding
To find information on how to bond wafers or chips to a carrier wafer, click here.
Acceptance test
The instrument was opened for users in April 2010 when the acceptance test was signed. This was based on the performance of five standard recipes (A, B, C, D and SOI) that are further examined below. The acceptance test report is found here.
Characterisation of etched trenches
Comparing differences in etched trenches requires a set of common parameters for each trench. Click here to find more information about the parameters used on the DRIE-Pegasus process development.
Material from SPTS
Internal Danchip Process log
Process log at Danchip [1]
Equipment | DRIE-Pegasus | |
---|---|---|
Purpose | Dry etch of |
|
Performance | Etch rates |
|
Uniformity |
| |
Process parameter range | RF powers |
|
Gas flows |
| |
Pressure and temperature |
| |
Process options |
| |
Substrates | Batch size |
|
Allowed materials |
| |
Possible masking materials |
|