Specific Process Knowledge/Doping: Difference between revisions
Line 10: | Line 10: | ||
*[[Specific Process Knowledge/Thermal Process/Dope with Phosphorus|Dope with Phosphorous]] - Doping Silicon wafers with phosphorous by thermal predeposition and drive-in | *[[Specific Process Knowledge/Thermal Process/Dope with Phosphorus|Dope with Phosphorous]] - Doping Silicon wafers with phosphorous by thermal predeposition and drive-in | ||
*[[Specific Process Knowledge/Thermal Process/Dope with Boron|Dope with Boron]] - Doping Silicon wafers with boron by thermal predeposition and drive-in | *[[Specific Process Knowledge/Thermal Process/Dope with Boron|Dope with Boron]] - Doping Silicon wafers with boron by thermal predeposition and drive-in | ||
*[[Specific Process Knowledge/Thin film deposition/Furnace LPCVD PolySilicon|Furnace LPCVD PolySilicon]] - Deposition of PolySi doped with B or P | *[[Specific Process Knowledge/Thin film deposition/Furnace LPCVD PolySilicon/Boron doped poly-Si and a-Si |Furnace LPCVD PolySilicon]] - Deposition of PolySi doped with B or P | ||
*[[Specific Process Knowledge/Thin film deposition/PECVD|PECVD]] - Making boron glass (BSG), phosphorus glass (PSG), boron-phosphorous glass PBSG or germanium doped glass | *[[Specific Process Knowledge/Thin film deposition/PECVD|PECVD]] - Making boron glass (BSG), phosphorus glass (PSG), boron-phosphorous glass PBSG or germanium doped glass | ||
*Ion implantation | *Ion implantation |
Revision as of 10:54, 24 November 2015
Feedback to this page: click here
Doping your wafer
This page is about doping your wafer or making a thin film layer doped with boron, phosphorous or Germanium.
- Dope with Phosphorous - Doping Silicon wafers with phosphorous by thermal predeposition and drive-in
- Dope with Boron - Doping Silicon wafers with boron by thermal predeposition and drive-in
- Furnace LPCVD PolySilicon - Deposition of PolySi doped with B or P
- PECVD - Making boron glass (BSG), phosphorus glass (PSG), boron-phosphorous glass PBSG or germanium doped glass
- Ion implantation
- Doping results - achieved by different processes
Comparison of different doping processes
Phosphorous predep | Boron predep | PECVD doped thin film | Doped Poly Si | Ion implantation | |
---|---|---|---|---|---|
Generel description | Dopants introduced by diffusion from gas-phase (POCl3). A thin phosphorous glass is formed on the substrate and phosphorous atoms are driven in. The phosphorous glass is afterward removed by a short BHF etch. Often further annealing is desired in order to redistribute the dopants in the material. This is done at 800°C - 1150°C in either high temperature annealing furnaces or by rapid thermal annealing. | Dopants introduced by diffusion from solid source wafers containing B2O3. A boron glass is formed on the substrate and boron atoms are driven in. The boron glass is afterward removed by a low temperature oxidation process (1 hour at 800°C-900°C) in the boron drive in furnace (A1) followed by a BHF etch. Often further annealing is desired in order to redistribute the dopants in the material. This is done at 800°C - 1150°C in either high temperature annealing furnaces or by rapid thermal annealing. | Deposition of doped thin film (oxides or nitrides). A high temperature step to drive in and redistribute the dopants in the material is required. This is typically done at 800°C - 1150°C in either high temperature annealing furnaces (C1 or C3) or by rapid thermal annealing. The doped glass can afterwards be removed in a BHF etch. | Dopants introduced by in-situ doping of poly/amorphous Si. In some cases you need a high temperature step to redistribute the dopants in the material and alter the crystallinity. This is typically done at 800°C - 1150°C in either high temperature annealing furnaces (C1 or C3) or by rapid thermal annealing. | Dopant ions are implanted into the substrate by a high-energy ion beam. Contrary the other doping techniques the doping concentration has a peak inside the substrate when introduced by ion-implantation. Ion implantation cannot be done at Danchip but IBS (Ion Beam Services) offers ion-beam implantation as a service. See more at the homepage of IBS: http://www.ion-beam-services.com/about_us.htm. When wafers return from Ion implantation they need a clean before entering the cleanroom. Activation and redistribution of the dopants is required and is done by a high temperature anneal (600°C-1000°C) in the high temperature furnaces or by rapid thermal anneal. |
Process Temperature |
|
|
|
|
|
Dopant |
|
|
|
|
|
Substrate size |
|
|
|
|
|
Allowed materials |
|
|
|
|
|
THIS PAGE IS UNDER CONSTRUCTION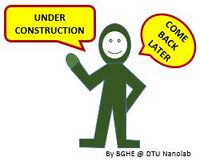
Doping results
Below is shown doping results achieved by the use of different processes and heat treatments