Specific Process Knowledge/Etch/ICP Metal Etcher: Difference between revisions
No edit summary |
No edit summary |
||
(One intermediate revision by the same user not shown) | |||
Line 32: | Line 32: | ||
*[[Specific Process Knowledge/Etch/Titanium Oxide/ICP metal|Etch of Titanium Oxide]] | *[[Specific Process Knowledge/Etch/Titanium Oxide/ICP metal|Etch of Titanium Oxide]] | ||
*[[Specific Process Knowledge/Etch/Aluminum Oxide/Al2O3 Etch with ICP Metal|Al<sub>2</sub>O<sub>3</sub> Etch]] | *[[Specific Process Knowledge/Etch/Aluminum Oxide/Al2O3 Etch with ICP Metal|Al<sub>2</sub>O<sub>3</sub> Etch]] | ||
'''End point detection''' | |||
*[[/Examples of End point detection|Examples of End point detection]] | |||
==An overview of the performance of the ICP Metal Etcher and some process related parameters== | ==An overview of the performance of the ICP Metal Etcher and some process related parameters== |
Latest revision as of 09:37, 24 April 2023
Feedback to this page: click here
The ICP Metal Etcher
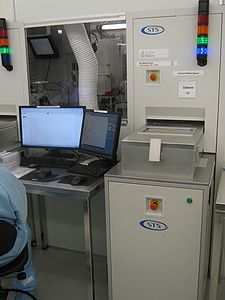
Name: PRO ICP
Vendor: STS (now SPTS)
The ICP Metal Etcher allows you to dry etch a small set of metals that includes aluminium, titanium, chromium, titanium tungsten and molybdenum (along with the related oxides and nitrides). It is, despite its name, strictly forbidden to etch (or expose to plasma) other metals. In order to do so use the IBE/IBSD Ionfab 300.
The user manual, user APV and contact information can be found in LabManager:
Equipment info in LabManager
Process information
Standard recipes
Other etch recipes
- Barc Etch
- Etch of silicon
- Etch of silicon oxide
- Etch of silicon nitride
- Etch of Titanium Oxide
- Al2O3 Etch
End point detection
Purpose | Dry etch of |
| |||||||||
---|---|---|---|---|---|---|---|---|---|---|---|
Performance | Etch rates |
| |||||||||
Anisotropy |
| ||||||||||
Process parameter range | Process pressure |
| |||||||||
Gas flows |
| ||||||||||
Substrates | Batch size |
| |||||||||
Substrate material allowed |
| ||||||||||
Possible masking material |
|