Specific Process Knowledge/Lithography/Aligners/Aligner: Maskless 02 processing: Difference between revisions
(86 intermediate revisions by 2 users not shown) | |||
Line 1: | Line 1: | ||
{{:Specific Process Knowledge/Lithography/authors_generic}} | |||
= | '''Feedback to this page''': '''[mailto:labadviser@nanolab.dtu.dk?Subject=Feed%20back%20from%20page%20http://labadviser.nanolab.dtu.dk/index.php?title=Specific_Process_Knowledge/Lithography/Aligners/Aligner:_Maskless_02_processing click here]''' | ||
[[Category: Equipment|Lithography]] | |||
[[Category: Lithography]] | |||
[[Image:DUV_wafers.jpg|500px|frameless|right|]] | |||
__TOC__ | |||
= | =Exposure technology= | ||
Aligner: Maskless 02 is ''not'' a direct writer. In the maskless aligner, the exposure light is passed through a spatial light modulator, much like in a video projector, and projected onto the substrate, exposing a small area of the design at a time. The substrate is fully exposed by scanning the exposure field across the substrate in a succession of exposure stripes. | |||
The | The light source is a laser diode (array) with a wavelength of 375 nm (2.8 W). The spatial light modulator is a digital micro-mirror device. The individual mirrors of the DMD are switched on and off in order to represent the design, and the laser is flashed on and off, in order to give the desired exposure dose. The exposure image is projected onto the substrate through a lens-system. The projected image has a pixel size of 500x500 nm on the substrate surface. The image is scanned across the substrate in stripes in order to expose the entire design. Each stripe is overlapping 2 or 5 times, depending on the chosen [[Specific_Process_Knowledge/Lithography/Aligners/Aligner:_Maskless_02_processing#Exposure_mode|exposure mode]]), in order to reduce light-source non-uniformity effects and stitching errors. The address grid size is 250 nm or 100 nm for Fast and High Quality exposure mode, respectively. | ||
The writing head of the Aligner: Maskless 02 moves only in the z-direction. Using the optical or pneumatic focusing system, the maskless aligner is able to do real-time dynamic autofocus. The defocus process parameter is used to offset the focusing mechanism, to optimize printing quality in different resists and resist thicknesses, as well as reflective or absorbing surfaces, and transparent or non-transparent substrates. | |||
The stage of the Aligner: Maskless 02 moves only in x and y. It has no theta-axis. All rotation during alignment is accomplished by digitally rotating the design to match the physical rotation of the substrate. | |||
=Process Parameters= | |||
The lithographic result of exposure on Aligner: Maskless 02 depends on a lot of factors, including the dose and defocus parameters, and the exposure mode used. The optimal dose and defocus depends on the type and thickness of the resist, as well as the optical properties of the substrate (e.g. reflective/absorbing/transparent). All of these factors influence the obtainable resolution, as well as the writing speed. | |||
The correct way to determine the best dose-defocus settings is to generate a so-called Bossung plot (known from projection lithography), which plots the printed linewidth as a function of dose and defocus. From this, the most stable region of parameter space is chosen, i.e. the region where the linewidth changes the least when dose and defocus changes. Any deviation from the design linewidth may be corrected using the CD bias parameter. This typically involves SEM imaging of resist cross-sections, and quickly becomes time-consuming. However, in most cases, inspection of a dose-defocus matrix (easily generated using the series exposure function) in an optical microscope will get you most of the way. | |||
<br clear="all" /> | |||
==Exposure dose and defocus== | |||
[[Specific Process Knowledge/Lithography/Resist#Aligner:_Maskless_02|Information on UV exposure dose]] | |||
Aligner: Maskless 02 offers two autofocus modes; optical or pneumatic. The autofocus mode is selected via the substrate template. The defocus process parameter is used to compensate for offsets between the autofocus mechanism and the focal point of the exposure light, and simultaneously optimize print quality in different resists and varying thicknesses. | |||
'''Optical:''' | |||
Works for substrates down to 3x3 mm. | |||
'''Pneumatic:''' | |||
Substrates must be at least 5x5 mm to be successfully loaded. The pneumatic AF freezes at a distance of 3 mm form the substrate edge, which means that in order to have any ''dynamic'' focusing, using the pneumatic AF, the substrate must be larger than 6x6 mm. When using the pneumatic autofocus, we recommend a substrate size of at least 20x20 mm. | |||
==Exposure mode== | ==Exposure mode== | ||
Line 86: | Line 44: | ||
Aligner: Maskless 02 offers two exposure modes. The exposure mode is selected during design conversion. | Aligner: Maskless 02 offers two exposure modes. The exposure mode is selected during design conversion. | ||
'''High quality | '''High quality:''' | ||
In the high quality mode, an area of the pattern is exposed by | High quality mode is used for minimum stitching effects.<br> | ||
In the high quality mode, an area of the pattern is exposed by 5 stripes, each 500 µm wide and exposing a fifth of the dose. At the same time, sub-pixel interpolation is applied, giving an address grid size of 100 nm. | |||
'''Fast''' | '''Fast:''' | ||
In the fast mode, each area of the pattern is exposed by 2 stripes only. This effectively | Fast mode is used for maximum exposure speed.<br> | ||
In the fast mode, each area of the pattern is exposed by 2 stripes only. This effectively reduces the exposure time by 60%, but also increases the size of the address grid in the X-direction to 250 nm. Due to less averaging of non-uniformities, stitching effects will be more prominent in this mode. | |||
==Writing speed== | ==Writing speed== | ||
According to specs, the writing speed of Aligner: Maskless 02 is | (This section was updated 05-09-2023 by taran@nanolab) | ||
According to specs (after being converted to write mode 2), the writing speed of Aligner: Maskless 02 is 500 mm<sup>2</sup>/min in fast mode. Using the high quality exposure mode cuts the expected speed by 2.5, to approximately 200 mm<sup>2</sup>/min. The writing speed of the machine for a 100x100 mm<sup>2</sup> area measured after being modified to write mode 2 (2023-03-21) was ~1200 mm<sup>2</sup>/min at 100 mJ/cm<sup>2</sup>. | |||
When the exposure is started on the maskless aligner, the software starts converting the design to the image files needed for the exposure. When sufficient data has been generated, the hardware starts exposing the sample, while more image data is being generated in the background. This simultaneous data conversion and exposure is called Online conversion. Once a design has been converted (and/or exposed) the data may be reused for repeated exposures. Due to no time lost waiting for data conversion, offline exposure may be several tens of % faster than online. However, the converted data can only be reused if no alignment is needed, including flat alignment ("Expose with substrate angle"/"Expose with Global Angle"). | |||
<br clear="all" /> | |||
[[File:Speed vs area newWritehead.png|640px|thumb|The writing speed of Aligner: Maskless 02 (fast mode, 375nm, 100 mJ/cm<sup>2</sup>) as function of the exposure area. Data and graph by Thomas Anhøj @ DTU Nanolab, 2023.]] | |||
'''Speed vs. area:''' | '''Speed vs. area:''' | ||
During exposure of a stripe the stage moves at a constant speed. Each stripe thus includes a certain movement overhead for acceleration and deceleration. As the stripes get shorter, this overhead becomes more significant, and the normal writing speed is no longer achieved. For samples | During exposure of a stripe the stage moves at a constant speed. Each stripe thus includes a certain movement overhead for acceleration and deceleration. As the stripes get shorter, this overhead becomes more significant, and the normal writing speed is no longer achieved. For smaller samples, the writing speed of Aligner: Maskless 02 drops below the specified writing speed for a full 100 x 100 mm substrate. | ||
<br clear="all" /> | <br clear="all" /> | ||
[[ | [[File:Speed vs dose newWritehead.png|640px|thumb|The writing speed of Aligner: Maskless 02 (fast mode, 375nm) as function of the exposure dose. The exposure speed was measured using a 10 mm x 100 mm exposure area, but should be approximately the same for a full 100 mm wafer exposure. Data and graph by Thomas Anhøj @ DTU Nanolab, 2023.]] | ||
'''Speed vs. dose:''' | '''Speed vs. dose:''' | ||
The writing speed | The writing speed is constant up to a dose of 100 mJ/cm<sup>2</sup>, then drops with increasing dose. At 500 mJ/cm<sup>2</sup>, the writing speed is approximately the nominal speed of 500 mm<sup>2</sup>/min. As a rule of thumb, the writing time doubles every time the dose is doubled. | ||
<br clear="all" /> | <br clear="all" /> | ||
'''Speed vs. design:''' | '''Speed vs. design:''' | ||
<!-- <span style="color:red">New specs after the new writehead has been installed - section will be updated soon.</span> --> | |||
Depending on the complexity and density of the pattern, the conversion process may slow down the exposure significantly. A | Depending on the complexity and density of the pattern, the conversion process may slow down the exposure significantly. A 100 mm wafer exposed with a pattern consisting of 200 million 5 µm circles took more than 16 minutes (600 mm<sup>2</sup>/min), compared to the expected 8-9 minutes (1200 mm<sup>2</sup>/min). It took 6.5 minutes before the first stripe was exposed, and there were several pauses during the print (waiting for data from conversion). Even a simple 100 x 100 mm square takes 1.5 minutes to start printing, lowering the effective writing speed to 1000 mm<sup>2</sup>/min. | ||
The maskless aligner exposes the design in north-south oriented stripes (perpendicular to the flat). The stripes all have the same length, set by the height of the design, and only completely empty stripes are skipped. The writing speed may thus be affected by the layout of the design, as shown below. | The maskless aligner exposes the design in north-south oriented stripes (perpendicular to the flat). The stripes all have the same length, set by the height of the design, and only completely empty stripes are skipped. The writing speed may thus be affected by the layout of the design, as shown below. | ||
{| cellpadding="2" style="border: 2px solid darkgray;" align=" | {| cellpadding="2" style="border: 2px solid darkgray;" align="center" | ||
! width="350" | | ! width="350" | | ||
! width="350" | | ! width="350" | | ||
|+'''Design case: Five | |+'''Design case: Five 100 µm wide, 40 mm long lines, spaced 10 mm apart (40x40 mm<sup>2</sup>). Data and graphics by Thomas Anhøj @ DTU Nanolab, 2019-2023.''' | ||
|- border="0" align="center" | |- border="0" align="center" | ||
|[[Image:MLA150_LongLinesEW.JPG|300px]] | |[[Image:MLA150_LongLinesEW.JPG|300px]] | ||
Line 132: | Line 96: | ||
|- align="center" | |- align="center" | ||
| This design printed in | | This design printed in 2.5 minutes (640 mm<sup>2</sup>/min) || This design printed in less than 1 minute (1780 mm<sup>2</sup>/min) | ||
|} | |} | ||
Line 138: | Line 102: | ||
<br clear="all" /> | <br clear="all" /> | ||
<!-- AFTER THE CONVERSION TO WRITE MODE 2, this data is no longer relevant. No official acceptance test was performed after the write mode conversion. TARAN 5/9-23 | |||
==Acceptance test== | ==Acceptance test== | ||
<span style="color:red">New specs after the new writehead has been installed - section will be updated soon.</span> | |||
Acceptance criteria on a 100 X 100 mm<sup>2</sup> area: Width of smallest resolved line 600±100 nm, alignment error 500 nm, writing speed 285 mm<sup>2</sup>/min. | Acceptance criteria on a 100 X 100 mm<sup>2</sup> area: Width of smallest resolved line 600±100 nm, alignment error 500 nm, writing speed 285 mm<sup>2</sup>/min. | ||
Line 186: | Line 152: | ||
|} | |} | ||
--> | |||
=Features= | =Features= | ||
Line 194: | Line 161: | ||
At the end of substrate detection, the sample is scanned twice along the bottom edge (flat), in order to determine the substrate rotation. This angle will be presented in the exposure panel along with the option to expose the design rotated in order to compensate for this angle, i.e. aligned to the flat/edge of the substrate. | At the end of substrate detection, the sample is scanned twice along the bottom edge (flat), in order to determine the substrate rotation. This angle will be presented in the exposure panel along with the option to expose the design rotated in order to compensate for this angle, i.e. aligned to the flat/edge of the substrate. | ||
'''Result of using "Expose with substrate angle" ("Expose with Global Angle"):''' | '''Result of using "Expose with substrate angle" ("Expose with Global Angle"):''' | ||
*Rotation: 0 | *Rotation: 0 ±0.2° | ||
*Centring: | *Centring: | ||
** '''X''' | ** '''X''' 0 ±100µm | ||
** '''Y''' | ** '''Y''' 0 ±100µm | ||
Taran | Taran Sep 2023, average of 3 4" wafers.<br> | ||
'''Result of loading the same substrate ~10 times without removing it from the stage:''' | '''Result of loading the same substrate ~10 times without removing it from the stage:''' | ||
Line 216: | Line 184: | ||
|- | |- | ||
|-style="background:WhiteSmoke; color:black" | |-style="background:WhiteSmoke; color:black" | ||
|Optical autofocus | |Optical autofocus | ||
| -4.7 mRad | |||
| | |||
| ±1.4 mRad | | ±1.4 mRad | ||
±0.08° | (±0.08°) | ||
|- | |- | ||
|-style="background:WhiteSmoke; color:black" | |-style="background:WhiteSmoke; color:black" | ||
|Pneumatic autofocus | |||
| -2.8 mRad | |||
|Pneumatic autofocus | |||
| - | |||
| ±1.4 mRad | | ±1.4 mRad | ||
±0.08° | (±0.08°) | ||
|} | |} | ||
Measured after conversion to write mode 2 in 2023 by Taran Sep 2023. | |||
<br clear="all" /> | <br clear="all" /> | ||
Line 262: | Line 203: | ||
==Labeling== | ==Labeling== | ||
[[Image:MLA150_label.JPG|400x400px|thumb|An example of wafer ID produced by the labeling function]] | [[Image:MLA150_label.JPG|400x400px|thumb|An example of wafer ID produced by the labeling function. Photograph by Thomas Anhøj @ DTU Nanolab, 2019.]] | ||
The conversion manager software allows for inclusion of labels during the design conversion process. The labels are configured in a .lbl tab-delimited ASCII file with a special header in the first row, which must be located in the 'HIMT\ | The conversion manager software allows for inclusion of labels during the design conversion process. The labels are configured in a .lbl tab-delimited ASCII file with a special header in the first row, which must be located in the 'HIMT\Designs_conversion_PC\Labels' folder. When used, the labels defined in the label file will be merged with the pattern in the source file, and the result can be inspected in the viewer. The X and Y positions of the labels should be given in design coordinates, and will be subject to any offsets/shifts applied to the design. Note, that if the label file is changed, the job file will not update automatically. | ||
'''Example of a label file:''' | '''Example of a label file:''' | ||
Line 272: | Line 213: | ||
-16000 | -46000 | um | 2000 | um | TARAN DTU Nanolab 20190320 | -16000 | -46000 | um | 2000 | um | TARAN DTU Nanolab 20190320 | ||
This produces a | This produces a 2 mm high, approximately 32 mm long, wafer ID at the flat of a 100 mm wafer. Some special characters are not allowed (eg. ';'). | ||
<br clear="all" /> | <br clear="all" /> | ||
Line 278: | Line 219: | ||
==Large defocus range== | ==Large defocus range== | ||
The standard range for the defocus parameter is -10 to 10, but a special feature allows to extend this range to -25 to 25. The large defocus range feature is set in the resist template, and can only be accessed by choosing the ' | The standard range for the defocus parameter is -10 to 10, but a special feature allows to extend this range to -25 to 25. The large defocus range feature is set in the resist template, and can only be accessed by choosing the 'Special - Large defoc range' resist template during the job setup. The dose must be set manually, as this is an otherwise empty resist template. | ||
This feature works with both pneumatic and optical autofocus, in the full range for both. | |||
It is possible to combine this feature with other features, such as high aspect ratio mode. | |||
==High Aspect Ratio (DOF) mode== | ==High Aspect Ratio (DOF) mode== | ||
<span style="color:red">New specs after the new writehead has been installed - section will be updated soon.</span> | |||
Aligner: Maskless 02 is configured with the so-called "Write Mode I", which uses a higher demagnification, higher NA lens system to achieve higher resolution. This reduces the depth of focus (technically ''depth of field''), making it more difficult to achieve good lithographic results in thicker resist coatings. The theoretical DOF of Aligner: Maskless 02 is 0.3µm, compared to 1µm for Aligner: Maskless 01 and Aligner: Maskless 03. In order to improve processing of thick resists, the Aligner: Maskless 02 has been configured with the High Aspect Ratio Mode, which uses a variable aperture in the optical path to decrease the (illumination) NA of the system, thus increasing the DOF at the expense of intensity and resolution limit. | Aligner: Maskless 02 is configured with the so-called "Write Mode I", which uses a higher demagnification, higher NA lens system to achieve higher resolution. This reduces the depth of focus (technically ''depth of field''), making it more difficult to achieve good lithographic results in thicker resist coatings. The theoretical DOF of Aligner: Maskless 02 is 0.3µm, compared to 1µm for Aligner: Maskless 01 and Aligner: Maskless 03. In order to improve processing of thick resists, the Aligner: Maskless 02 has been configured with the High Aspect Ratio Mode, which uses a variable aperture in the optical path to decrease the (illumination) NA of the system, thus increasing the DOF at the expense of intensity and resolution limit. | ||
[[Image:MLA150_intensityVSaperture.JPG|400x400px|thumb|The exposure intensity of Aligner: Maskless 02 as a function of the high AR mode aperture setting]] | [[Image:MLA150_intensityVSaperture.JPG|400x400px|thumb|The exposure intensity of Aligner: Maskless 02 as a function of the high AR mode aperture setting. Data and graph by Thomas Anhøj @ DTU Nanolab, 2019.]] | ||
The aperture size is controlled via a parameter in the resist template. The high AR parameter can be Standard (aperture fully open; 800 motor steps), Large (100 steps), or X-Large (60 steps). | The aperture size is controlled via a parameter in the resist template. The high AR parameter can be Standard (aperture fully open; 800 motor steps), Large (100 steps), or X-Large (60 steps). | ||
Line 398: | Line 341: | ||
After alignment to the specified alignment marks, the Aligner: Maskless 02 will automatically compensate for the translation (shift) and rotation detected during the alignment. However, the translation is set using only the first alignment mark. This means that if there is any run-out (gain) in the wafer, the alignment will be perfect at the first alignment position, while the second alignment position will be off by the run-out error. The central part of the print will be misaligned by half the run-out error. This is different compared to alignment in a mask aligner, where the user usually splits the run-out error between the two sides, resulting in good alignment in the center. In Aligner: Maskless 02, run-out may be compensated by activating the scaling function, which only becomes available when using 3 or more alignment positions. To help assess whether the measured scaling or shearing is significant, 10 ppm (scaling = 1.000010 or 0.999990; shearing = ±0.010 mRad) corresponds to a difference of 1µm from one edge to the other on a 4" wafer. | After alignment to the specified alignment marks, the Aligner: Maskless 02 will automatically compensate for the translation (shift) and rotation detected during the alignment. However, the translation is set using only the first alignment mark. This means that if there is any run-out (gain) in the wafer, the alignment will be perfect at the first alignment position, while the second alignment position will be off by the run-out error. The central part of the print will be misaligned by half the run-out error. This is different compared to alignment in a mask aligner, where the user usually splits the run-out error between the two sides, resulting in good alignment in the center. In Aligner: Maskless 02, run-out may be compensated by activating the scaling function, which only becomes available when using 3 or more alignment positions. To help assess whether the measured scaling or shearing is significant, 10 ppm (scaling = 1.000010 or 0.999990; shearing = ±0.010 mRad) corresponds to a difference of 1µm from one edge to the other on a 4" wafer. | ||
In order to get good alignment, it is advised to use four alignment marks for alignment, and to activate scaling (possibly also shearing) before starting the exposure. Optical or pneumatic auto-focus should not affect the result, but it is recommended to use the "High Res" camera for the final alignment of each mark in order to achieve the best overlay accuracy. | In order to get good alignment, it is advised to use four alignment marks for alignment, and to activate scaling (possibly also shearing) before starting the exposure. Optical or pneumatic auto-focus should not affect the result, but it is recommended to use the "High Res" camera for the final alignment of each mark in order to achieve the best overlay accuracy. Exposure using the fast mode decreases the overlay accuracy, since the address grid size is increased to 250 nm. | ||
<!-- AFTER THE CONVERSION TO WRITE MODE 2, this data is no longer relevant. TARAN 6/9-23 | |||
'''Alignment accuracy:''' | '''Alignment accuracy:''' | ||
Line 471: | Line 415: | ||
The result shows significant misalignment between the two layers, higher than what is seen in true overlay tests. This is believed to be an effect of drift during the first, long print (most likely heating of the stage), as the misalignment is seen to be biggest between parts printed furthest apart in time (i.e. on the left side of the wafer). In a normal overlay print, this error can be at least partially compensated using the scaling and shearing function available for three or more alignment marks/positions. | The result shows significant misalignment between the two layers, higher than what is seen in true overlay tests. This is believed to be an effect of drift during the first, long print (most likely heating of the stage), as the misalignment is seen to be biggest between parts printed furthest apart in time (i.e. on the left side of the wafer). In a normal overlay print, this error can be at least partially compensated using the scaling and shearing function available for three or more alignment marks/positions. | ||
--> | |||
<br clear="all" /> | <br clear="all" /> | ||
==Top Side Alignment== | ==Top Side Alignment== | ||
<!-- | |||
<span style="color:red">New specs after the new writehead has been installed - section will be updated soon.</span> | |||
--> | |||
'''Overlay accuracy (spec):''' | '''Overlay accuracy (spec):''' ±0.5 µm | ||
'''Camera field of view (W x H):''' <br> | '''Camera field of view (W x H):''' <br> | ||
'''High Res''' | '''High Res''' 190 µm x 140 µm <br> | ||
'''Low Res''' | '''Low Res''' 640 µm x 480 µm <br> | ||
'''Overview''' | '''Overview''' 12 mm x 9 mm | ||
'''Accessible stage coordinates:''' <br> | '''Accessible stage coordinates:''' <br> | ||
Line 488: | Line 435: | ||
In order to be sure the Overview camera can be used to locate the first alignment mark, it is advised to use a mark in the bottom left portion (3<sup>rd</sup> quadrant) of the design as mark 1. <br> | In order to be sure the Overview camera can be used to locate the first alignment mark, it is advised to use a mark in the bottom left portion (3<sup>rd</sup> quadrant) of the design as mark 1. <br> | ||
{| cellpadding="2" style="border: 2px solid darkgray;" align=" | {| cellpadding="2" style="border: 2px solid darkgray;" align="center" | ||
! width="320" | | ! width="320" | | ||
! width="320" | | ! width="320" | | ||
! width="320" | | ! width="320" | | ||
|+'''Camera views during alignment on Aligner: Maskless 02''' | |+'''Camera views during alignment on Aligner: Maskless 02. Screenshots by Thomas Anhøj @ DTU Nanolab, 2019.''' | ||
|- border="0" align="center" | |- border="0" align="center" | ||
|[[Image:MLA150 TSA Overview.JPG|300px]] | |[[Image:MLA150 TSA Overview.JPG|300px]] | ||
|[[Image:MLA150_BSA_Backside.JPG|300px]] | |||
|[[Image:MLA150_TSA_Low_Res.JPG|300px]] | |[[Image:MLA150_TSA_Low_Res.JPG|300px]] | ||
|- align="center" | |- align="center" | ||
| Overview camera image of a TSA alignment mark during alignment.<br/> The circle is | | Overview camera image of a TSA alignment mark during alignment.<br/> The circle is 3 mm in diameter, the alignment mark is 300 µm. The blue cross-hair is ~400 µm. || Low Res camera image of a TSA alignment mark during alignment.<br/> The mark is 300 µm wide. The blue cross-hair is ~18 µm. || High Res camera image of a TSA alignment mark during alignment.<br/> The lines of the cross are 20 µm wide. The blue cross-hair is ~7 µm. | ||
|} | |} | ||
'''Alignment test | <br clear="all" /> | ||
'''Alignment test''' (unless otherwise stated, these tests use 375nm laser, High Res camera, and Quality exposure) | |||
{|border="1" cellspacing="0" cellpadding="3" style="text-align:center;" | {|border="1" cellspacing="0" cellpadding="3" style="text-align:center;" | ||
|- | |- | ||
Line 514: | Line 464: | ||
!Shearing [mRad] | !Shearing [mRad] | ||
!Misalignment [µm] | !Misalignment [µm] | ||
!Run-out [ppm] | !Run-out [ppm] | ||
!Rotation [ppm] | !Rotation [ppm] | ||
|- | |- | ||
|- | |||
|-style="background:WhiteSmoke; color:black" | |||
|rowspan="2"|4 alignment marks | |||
(Taran Apr 2023) | |||
|'''X''' | |||
| 6 | |||
|rowspan="2" align="center"|0.004 | |||
| -0.5±0.08 | |||
| -0.3±1.7 | |||
| 0.6±1.2 | |||
|- | |||
|-style="background:WhiteSmoke; color:black" | |||
|'''Y''' | |||
| 9 | |||
| -0.3±0.08 | |||
| 1.1±1.7 | |||
| -1.1±1.2 | |||
|- | |||
|-style="background:WhiteSmoke; color:black" | |||
|rowspan="2"|4 alignment marks | |||
'''Low Res camera''' | |||
(Taran Apr 2023) | |||
|'''X''' | |||
| 5 | |||
|rowspan="2" align="center"|0.004 | |||
| -0.95±0.13 | |||
| -1.1±2.5 | |||
| -0.8±1.3 | |||
|- | |||
|-style="background:WhiteSmoke; color:black" | |||
|'''Y''' | |||
| 7 | |||
| 0.1±0.1 | |||
| -1.1±1.7 | |||
| -0.8±2.5 | |||
|- | |||
|-style="background:WhiteSmoke; color:black" | |||
|rowspan="2"|4 alignment marks | |||
'''Fast exposure''' | |||
(Taran Apr 2023) | |||
|'''X''' | |||
| 7 | |||
|rowspan="2" align="center"|0.003 | |||
| -0.65±0.05 | |||
| -0.6±1.7 | |||
| 0.3±1.2 | |||
|- | |||
|-style="background:WhiteSmoke; color:black" | |||
|'''Y''' | |||
| 8 | |||
| -0.25±0.05 | |||
| 0.3±1.7 | |||
| -0.3±1.2 | |||
|- | |||
|-style="background:WhiteSmoke; color:black" | |||
|rowspan="2"|'''2''' alignment marks | |||
(Taran Apr 2023) | |||
|'''X''' | |||
|NA | |||
|rowspan="2"|NA | |||
| -0.75±0.3 | |||
| -8.9±1.7 | |||
| -1.4±2.5 | |||
|- | |||
|-style="background:WhiteSmoke; color:black" | |||
|'''Y''' | |||
| NA | |||
| -0.55±0.28 | |||
| -6.1±2.5 | |||
| -0.8±1.2 | |||
<!-- | |||
|- | |- | ||
|-style="background:WhiteSmoke; color:black" | |-style="background:WhiteSmoke; color:black" | ||
|rowspan="2"|2 alignment marks | |rowspan="2"|2 alignment marks | ||
(Taran Apr 2019) | (Taran Apr 2019) | ||
Line 529: | Line 561: | ||
|rowspan="2"|NA | |rowspan="2"|NA | ||
| 0.25±0.15 | | 0.25±0.15 | ||
| 1.7±1.7 | | 1.7±1.7 | ||
| 2.2±1.3 | | 2.2±1.3 | ||
Line 538: | Line 569: | ||
| NA | | NA | ||
| 0.3±0.13 | | 0.3±0.13 | ||
| 0.8±1.7 | | 0.8±1.7 | ||
| 0.0±1.7 | | 0.0±1.7 | ||
Line 545: | Line 575: | ||
|-style="background:WhiteSmoke; color:black" | |-style="background:WhiteSmoke; color:black" | ||
|rowspan="2"|4 alignment marks | |rowspan="2"|4 alignment marks | ||
(Taran Apr 2019) | (Taran Apr 2019) | ||
Line 552: | Line 581: | ||
|rowspan="2" align="center"|0.001 | |rowspan="2" align="center"|0.001 | ||
| 0.2±0.05 | | 0.2±0.05 | ||
| -0.6±1.7 | | -0.6±1.7 | ||
| 0.3±1.2 | | 0.3±1.2 | ||
Line 561: | Line 589: | ||
| -1 | | -1 | ||
| 0.4±0.05 | | 0.4±0.05 | ||
| 0.6±1.7 | | 0.6±1.7 | ||
| 0.6±1.2 | | 0.6±1.2 | ||
Line 568: | Line 595: | ||
|-style="background:WhiteSmoke; color:black" | |-style="background:WhiteSmoke; color:black" | ||
|rowspan="2"|4 alignment marks | |rowspan="2"|4 alignment marks | ||
Low Res camera | |||
(Taran Apr 2019) | (Taran Apr 2019) | ||
Line 575: | Line 602: | ||
|rowspan="2" align="center"|0.002 | |rowspan="2" align="center"|0.002 | ||
| -0.05±0.13 | | -0.05±0.13 | ||
| -1.9±1.7 | | -1.9±1.7 | ||
| 0.8±1.3 | | 0.8±1.3 | ||
Line 583: | Line 609: | ||
|'''Y''' | |'''Y''' | ||
| -2 | | -2 | ||
| 0.3±0.05 | | 0.3±0.05 | ||
| -0.6±1.7 | | -0.6±1.7 | ||
| 1.1±1.7 | | 1.1±1.7 | ||
--> | |||
|} | |} | ||
'''Alignment test with scaled first print | <!-- | ||
'''Alignment test with scaled first print''' | |||
{|border="1" cellspacing="0" cellpadding="3" style="text-align:center;" | {|border="1" cellspacing="0" cellpadding="3" style="text-align:center;" | ||
|- | |- | ||
Line 652: | Line 679: | ||
|} | |} | ||
--> | |||
==Back Side Alignment== | ==Back Side Alignment== | ||
'''Overlay accuracy (spec):''' ±1 µm | |||
'''BSA windows:''' along the X and Y axes, 10 mm wide x 46 mm long, starting 14.5 mm from the center. | |||
''' | '''Camera field of view (W x H):''' 640 µm x 480 µm | ||
[[Image:MLA150_BSA_Backside.JPG|center|300px|thumb|Image of a BSA alignment mark during alignment. The mark is 300 µm wide. The blue cross-hair is ~18 µm. Screenshot by Thomas Anhøj @ DTU Nanolab, 2019.]] | |||
The alignment marks must be placed within the BSA windows. The Overview camera only shows the top side of the substrate, and cannot be used to locate the BSA marks. | The alignment marks must be placed within the BSA windows. The Overview camera only shows the top side of the substrate, and cannot be used to locate the BSA marks. | ||
{| cellpadding="2" style="border: 2px solid darkgray;" align=" | {| cellpadding="2" style="border: 2px solid darkgray;" align="center" | ||
! width="320" | | ! width="320" | | ||
! width="320" | | ! width="320" | | ||
Line 671: | Line 700: | ||
! width="320" | | ! width="320" | | ||
|+'''Substrate view during backside alignment''' | |+'''Substrate view during backside alignment. Screenshots by Thomas Anhøj @ DTU Nanolab, 2019.''' | ||
|- border="0" align="center" | |- border="0" align="center" | ||
|[[Image:MLA150 BSA 2inch.JPG|300px]] | |[[Image:MLA150 BSA 2inch.JPG|300px]] | ||
Line 682: | Line 711: | ||
|} | |} | ||
<br clear="all" /> | |||
'''Backside alignment test:''' | '''Backside alignment test:''' | ||
Line 696: | Line 727: | ||
|- | |- | ||
|-style="background:WhiteSmoke; color:black" | |-style="background:WhiteSmoke; color:black" | ||
|rowspan="2" align="center"|Align- | |rowspan="2" align="center"|Align - flip 180° - align<br>3 point average | ||
|'''X''' | |'''X''' | ||
| -0. | | -0.625 ±0.125 | ||
|rowspan="2" align="center"|0. | |rowspan="2" align="center"|0.5 µm verniers | ||
Taran May 2019 | Taran May 2019 | ||
Line 705: | Line 736: | ||
|-style="background:WhiteSmoke; color:black" | |-style="background:WhiteSmoke; color:black" | ||
|'''Y''' | |'''Y''' | ||
| -0. | | -0.75 ±0.125 | ||
<!-- | |||
|- | |- | ||
|-style="background:WhiteSmoke; color:black" | |-style="background:WhiteSmoke; color:black" | ||
|rowspan="2" align="center"|Align-flip180-align, 3 points <br/> | |rowspan="2" align="center"|Align-flip180-align, 3 points <br/> 405 nm | ||
|'''X''' | |'''X''' | ||
| -0. | | -0.625 ±0.125 | ||
|rowspan="2" align="center"|0. | |rowspan="2" align="center"|0.5 µm verniers | ||
Taran May 2019 | Taran May 2019 | ||
Line 718: | Line 750: | ||
|-style="background:WhiteSmoke; color:black" | |-style="background:WhiteSmoke; color:black" | ||
|'''Y''' | |'''Y''' | ||
| -0. | | -0.375 ±0.125 | ||
|- | |- | ||
Line 724: | Line 756: | ||
|rowspan="2" align="center"|KOH-window, ? points | |rowspan="2" align="center"|KOH-window, ? points | ||
|'''X''' | |'''X''' | ||
| 0. | | 0.0 ±0.0 | ||
|rowspan="2" align="center"|Not performed yet | |rowspan="2" align="center"|Not performed yet | ||
|- | |- | ||
|-style="background:WhiteSmoke; color:black" | |-style="background:WhiteSmoke; color:black" | ||
|'''Y''' | |'''Y''' | ||
| 0. | | 0.0 ±0.0 | ||
--> | |||
|} | |} | ||
Line 737: | Line 769: | ||
==Advanced Field alignment (TSA)== | ==Advanced Field alignment (TSA)== | ||
'''Overlay accuracy (spec):''' 0. | '''Overlay accuracy (spec):''' 0.25 µm (5x5 mm<sup>2</sup> area) | ||
Shift, rotation, scaling, and shearing is determined and set by global alignment marks. The shift is corrected locally by automatic alignment to one mark in each field (chip). | Shift, rotation, scaling, and shearing is determined and set by global alignment marks. The shift is corrected locally by automatic alignment to one mark in each field (chip). | ||
Line 755: | Line 787: | ||
|-style="background:WhiteSmoke; color:black" | |-style="background:WhiteSmoke; color:black" | ||
|rowspan="2" align="center"|25 fields | |rowspan="2" align="center"|25 fields | ||
375 nm, high res camera | |||
(Taran Sept 2023) | |||
|'''X''' | |||
| -450 ±75 | |||
| -438 ±75 | |||
|- | |||
|-style="background:WhiteSmoke; color:black" | |||
|'''Y''' | |||
| -200 ±50 | |||
| -212 ±50 | |||
|- | |||
|-style="background:WhiteSmoke; color:black" | |||
|rowspan="2" align="center"|25 fields | |||
375 nm, high res camera | |||
(Taran Mar 2019) | (Taran Mar 2019) | ||
|'''X''' | |'''X''' | ||
| | | 50 ±75 | ||
| | | 70 ±75 | ||
|- | |- | ||
|-style="background:WhiteSmoke; color:black" | |-style="background:WhiteSmoke; color:black" | ||
|'''Y''' | |'''Y''' | ||
| | | 150 ±50 | ||
| | | 128 ±50 | ||
<!-- | |||
|- | |- | ||
|-style="background:WhiteSmoke; color:black" | |-style="background:WhiteSmoke; color:black" | ||
|rowspan="2" align="center"|Scaled first print, 10 fields | |rowspan="2" align="center"|Scaled first print, 10 fields | ||
375 nm, high res camera | |||
(Taran Mar 2019) | (Taran Mar 2019) | ||
|'''X''' | |'''X''' | ||
| - | | -25 ±50 | ||
| - | | -5 ±50 | ||
|- | |- | ||
|-style="background:WhiteSmoke; color:black" | |-style="background:WhiteSmoke; color:black" | ||
|'''Y''' | |'''Y''' | ||
| | | 100 ±50 | ||
| | | 120 ±50 | ||
|- | |- | ||
|-style="background:WhiteSmoke; color:black" | |-style="background:WhiteSmoke; color:black" | ||
|rowspan="2" align="center"|25 fields | |rowspan="2" align="center"|25 fields | ||
405 nm, high res camera | |||
(Taran Mar 2019) | (Taran Mar 2019) | ||
|'''X''' | |'''X''' | ||
| | | 100 ±75 | ||
| | | 108 ±75 | ||
|- | |- | ||
|-style="background:WhiteSmoke; color:black" | |-style="background:WhiteSmoke; color:black" | ||
|'''Y''' | |'''Y''' | ||
| | | 0 ±50 | ||
| | | 16 ±50 | ||
--> | |||
|} | |} | ||
<br clear="all" /> | <br clear="all" /> |
Latest revision as of 09:24, 7 March 2024
This section, including all images and pictures, is created by DTU Nanolab staff unless otherwise stated.
Feedback to this page: click here
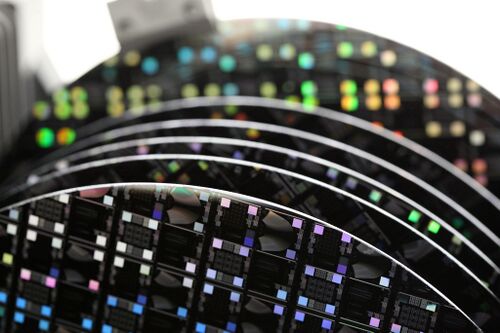
Exposure technology
Aligner: Maskless 02 is not a direct writer. In the maskless aligner, the exposure light is passed through a spatial light modulator, much like in a video projector, and projected onto the substrate, exposing a small area of the design at a time. The substrate is fully exposed by scanning the exposure field across the substrate in a succession of exposure stripes.
The light source is a laser diode (array) with a wavelength of 375 nm (2.8 W). The spatial light modulator is a digital micro-mirror device. The individual mirrors of the DMD are switched on and off in order to represent the design, and the laser is flashed on and off, in order to give the desired exposure dose. The exposure image is projected onto the substrate through a lens-system. The projected image has a pixel size of 500x500 nm on the substrate surface. The image is scanned across the substrate in stripes in order to expose the entire design. Each stripe is overlapping 2 or 5 times, depending on the chosen exposure mode), in order to reduce light-source non-uniformity effects and stitching errors. The address grid size is 250 nm or 100 nm for Fast and High Quality exposure mode, respectively.
The writing head of the Aligner: Maskless 02 moves only in the z-direction. Using the optical or pneumatic focusing system, the maskless aligner is able to do real-time dynamic autofocus. The defocus process parameter is used to offset the focusing mechanism, to optimize printing quality in different resists and resist thicknesses, as well as reflective or absorbing surfaces, and transparent or non-transparent substrates. The stage of the Aligner: Maskless 02 moves only in x and y. It has no theta-axis. All rotation during alignment is accomplished by digitally rotating the design to match the physical rotation of the substrate.
Process Parameters
The lithographic result of exposure on Aligner: Maskless 02 depends on a lot of factors, including the dose and defocus parameters, and the exposure mode used. The optimal dose and defocus depends on the type and thickness of the resist, as well as the optical properties of the substrate (e.g. reflective/absorbing/transparent). All of these factors influence the obtainable resolution, as well as the writing speed.
The correct way to determine the best dose-defocus settings is to generate a so-called Bossung plot (known from projection lithography), which plots the printed linewidth as a function of dose and defocus. From this, the most stable region of parameter space is chosen, i.e. the region where the linewidth changes the least when dose and defocus changes. Any deviation from the design linewidth may be corrected using the CD bias parameter. This typically involves SEM imaging of resist cross-sections, and quickly becomes time-consuming. However, in most cases, inspection of a dose-defocus matrix (easily generated using the series exposure function) in an optical microscope will get you most of the way.
Exposure dose and defocus
Information on UV exposure dose
Aligner: Maskless 02 offers two autofocus modes; optical or pneumatic. The autofocus mode is selected via the substrate template. The defocus process parameter is used to compensate for offsets between the autofocus mechanism and the focal point of the exposure light, and simultaneously optimize print quality in different resists and varying thicknesses.
Optical:
Works for substrates down to 3x3 mm.
Pneumatic:
Substrates must be at least 5x5 mm to be successfully loaded. The pneumatic AF freezes at a distance of 3 mm form the substrate edge, which means that in order to have any dynamic focusing, using the pneumatic AF, the substrate must be larger than 6x6 mm. When using the pneumatic autofocus, we recommend a substrate size of at least 20x20 mm.
Exposure mode
Aligner: Maskless 02 offers two exposure modes. The exposure mode is selected during design conversion.
High quality:
High quality mode is used for minimum stitching effects.
In the high quality mode, an area of the pattern is exposed by 5 stripes, each 500 µm wide and exposing a fifth of the dose. At the same time, sub-pixel interpolation is applied, giving an address grid size of 100 nm.
Fast:
Fast mode is used for maximum exposure speed.
In the fast mode, each area of the pattern is exposed by 2 stripes only. This effectively reduces the exposure time by 60%, but also increases the size of the address grid in the X-direction to 250 nm. Due to less averaging of non-uniformities, stitching effects will be more prominent in this mode.
Writing speed
(This section was updated 05-09-2023 by taran@nanolab)
According to specs (after being converted to write mode 2), the writing speed of Aligner: Maskless 02 is 500 mm2/min in fast mode. Using the high quality exposure mode cuts the expected speed by 2.5, to approximately 200 mm2/min. The writing speed of the machine for a 100x100 mm2 area measured after being modified to write mode 2 (2023-03-21) was ~1200 mm2/min at 100 mJ/cm2.
When the exposure is started on the maskless aligner, the software starts converting the design to the image files needed for the exposure. When sufficient data has been generated, the hardware starts exposing the sample, while more image data is being generated in the background. This simultaneous data conversion and exposure is called Online conversion. Once a design has been converted (and/or exposed) the data may be reused for repeated exposures. Due to no time lost waiting for data conversion, offline exposure may be several tens of % faster than online. However, the converted data can only be reused if no alignment is needed, including flat alignment ("Expose with substrate angle"/"Expose with Global Angle").
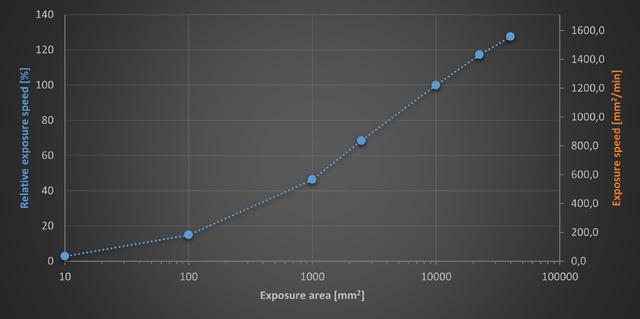
Speed vs. area:
During exposure of a stripe the stage moves at a constant speed. Each stripe thus includes a certain movement overhead for acceleration and deceleration. As the stripes get shorter, this overhead becomes more significant, and the normal writing speed is no longer achieved. For smaller samples, the writing speed of Aligner: Maskless 02 drops below the specified writing speed for a full 100 x 100 mm substrate.
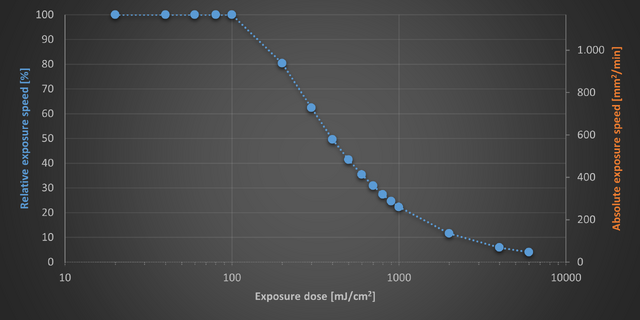
Speed vs. dose:
The writing speed is constant up to a dose of 100 mJ/cm2, then drops with increasing dose. At 500 mJ/cm2, the writing speed is approximately the nominal speed of 500 mm2/min. As a rule of thumb, the writing time doubles every time the dose is doubled.
Speed vs. design:
Depending on the complexity and density of the pattern, the conversion process may slow down the exposure significantly. A 100 mm wafer exposed with a pattern consisting of 200 million 5 µm circles took more than 16 minutes (600 mm2/min), compared to the expected 8-9 minutes (1200 mm2/min). It took 6.5 minutes before the first stripe was exposed, and there were several pauses during the print (waiting for data from conversion). Even a simple 100 x 100 mm square takes 1.5 minutes to start printing, lowering the effective writing speed to 1000 mm2/min.
The maskless aligner exposes the design in north-south oriented stripes (perpendicular to the flat). The stripes all have the same length, set by the height of the design, and only completely empty stripes are skipped. The writing speed may thus be affected by the layout of the design, as shown below.
Features
Substrate centring and flat alignment
During substrate detection, the sample is scanned along the X- and Y-axes, as well as diagonally. From these measurements, the size (diameter) of the substrate is calculated, as well as the stage position matching the center of the substrate. This stage position will be the default origin for the subsequent exposure.
At the end of substrate detection, the sample is scanned twice along the bottom edge (flat), in order to determine the substrate rotation. This angle will be presented in the exposure panel along with the option to expose the design rotated in order to compensate for this angle, i.e. aligned to the flat/edge of the substrate.
Result of using "Expose with substrate angle" ("Expose with Global Angle"):
- Rotation: 0 ±0.2°
- Centring:
- X 0 ±100µm
- Y 0 ±100µm
Taran Sep 2023, average of 3 4" wafers.
Result of loading the same substrate ~10 times without removing it from the stage:
Average | Range | |
---|---|---|
Optical autofocus | -4.7 mRad | ±1.4 mRad
(±0.08°) |
Pneumatic autofocus | -2.8 mRad | ±1.4 mRad
(±0.08°) |
Measured after conversion to write mode 2 in 2023 by Taran Sep 2023.
Labeling
The conversion manager software allows for inclusion of labels during the design conversion process. The labels are configured in a .lbl tab-delimited ASCII file with a special header in the first row, which must be located in the 'HIMT\Designs_conversion_PC\Labels' folder. When used, the labels defined in the label file will be merged with the pattern in the source file, and the result can be inspected in the viewer. The X and Y positions of the labels should be given in design coordinates, and will be subject to any offsets/shifts applied to the design. Note, that if the label file is changed, the job file will not update automatically.
Example of a label file:
X | Y | UNIT | HEIGHT | UNIT | TITLE
-16000 | -46000 | um | 2000 | um | TARAN DTU Nanolab 20190320
This produces a 2 mm high, approximately 32 mm long, wafer ID at the flat of a 100 mm wafer. Some special characters are not allowed (eg. ';').
Large defocus range
The standard range for the defocus parameter is -10 to 10, but a special feature allows to extend this range to -25 to 25. The large defocus range feature is set in the resist template, and can only be accessed by choosing the 'Special - Large defoc range' resist template during the job setup. The dose must be set manually, as this is an otherwise empty resist template. This feature works with both pneumatic and optical autofocus, in the full range for both.
It is possible to combine this feature with other features, such as high aspect ratio mode.
High Aspect Ratio (DOF) mode
New specs after the new writehead has been installed - section will be updated soon.
Aligner: Maskless 02 is configured with the so-called "Write Mode I", which uses a higher demagnification, higher NA lens system to achieve higher resolution. This reduces the depth of focus (technically depth of field), making it more difficult to achieve good lithographic results in thicker resist coatings. The theoretical DOF of Aligner: Maskless 02 is 0.3µm, compared to 1µm for Aligner: Maskless 01 and Aligner: Maskless 03. In order to improve processing of thick resists, the Aligner: Maskless 02 has been configured with the High Aspect Ratio Mode, which uses a variable aperture in the optical path to decrease the (illumination) NA of the system, thus increasing the DOF at the expense of intensity and resolution limit.
The aperture size is controlled via a parameter in the resist template. The high AR parameter can be Standard (aperture fully open; 800 motor steps), Large (100 steps), or X-Large (60 steps).
- Standard: No resist template or any normal resist template
- Large: 'NLAB High AR mode Large'
- X-Large: 'NLAB High AR mode XL'
Assuming a linear relation between motor steps and aperture diameter, Large corresponds to a relative aperture area of 1.6%, while X-Large corresponds to 0.6% aperture area. Intensity measurements show a relative intensity of approximately 25%, and 6%, respectively. The effective dose can be corrected by increasing the nominal dose in the exposure, either by a fixed machine parameter, or by the user setting a higher dose themselves. At the moment, the user will be required to increase the nominal dose.
Decreasing the aperture size significantly reduces the amount of light that reaches the sample, and thus the effective dose, as can be seen in the graph to the right, and the table below. The resolution limit, however, seem to be much less affected. Tests using 1.5µm MiR resist suggest that using the X-Large setting (60 steps) reduces the achievable resolution from 1µm at Standard setting to 3µm for exposure at 375nm, but only to 1.75µm for exposure at 405nm.
Dose factor for different wavelengths and aperture settings:
375nm | 405nm | |||
---|---|---|---|---|
Large (100) | X-Large (60) | Large (100) | X-Large (60) | |
Intensity measurements | 3.3 | 17.4 | 5.7 | 14.6 |
150µm SU-8 acceptance test | ~3 | ~10 | NA | NA |
1.5µm AZ MiR 701 dose test | 7.5 | 20.8 | 6.7 | 18.0 |
10µm AZ 4562 dose test | ? | ? | ? | ? |
Results from acceptance test on 150µm thick SU-8:
Pillars | Rings | |
---|---|---|
Standard (800)
6000 mJ/cm2 |
![]() |
![]() |
Large (100)
16500 mJ/cm2 |
![]() |
![]() |
X-Large (60)
55000 mJ/cm2 |
![]() |
![]() |
Alignment
Important information regarding alignment:
After alignment to the specified alignment marks, the Aligner: Maskless 02 will automatically compensate for the translation (shift) and rotation detected during the alignment. However, the translation is set using only the first alignment mark. This means that if there is any run-out (gain) in the wafer, the alignment will be perfect at the first alignment position, while the second alignment position will be off by the run-out error. The central part of the print will be misaligned by half the run-out error. This is different compared to alignment in a mask aligner, where the user usually splits the run-out error between the two sides, resulting in good alignment in the center. In Aligner: Maskless 02, run-out may be compensated by activating the scaling function, which only becomes available when using 3 or more alignment positions. To help assess whether the measured scaling or shearing is significant, 10 ppm (scaling = 1.000010 or 0.999990; shearing = ±0.010 mRad) corresponds to a difference of 1µm from one edge to the other on a 4" wafer.
In order to get good alignment, it is advised to use four alignment marks for alignment, and to activate scaling (possibly also shearing) before starting the exposure. Optical or pneumatic auto-focus should not affect the result, but it is recommended to use the "High Res" camera for the final alignment of each mark in order to achieve the best overlay accuracy. Exposure using the fast mode decreases the overlay accuracy, since the address grid size is increased to 250 nm.
Top Side Alignment
Overlay accuracy (spec): ±0.5 µm
Camera field of view (W x H):
High Res 190 µm x 140 µm
Low Res 640 µm x 480 µm
Overview 12 mm x 9 mm
Accessible stage coordinates:
High/Low Res X = ±108mm; Y = ±108mm
Overview X = ±108mm; Y = +39mm to -180mm
In order to be sure the Overview camera can be used to locate the first alignment mark, it is advised to use a mark in the bottom left portion (3rd quadrant) of the design as mark 1.
Alignment test (unless otherwise stated, these tests use 375nm laser, High Res camera, and Quality exposure)
MLA-MLA | Scaling [ppm] | Shearing [mRad] | Misalignment [µm] | Run-out [ppm] | Rotation [ppm] | |
---|---|---|---|---|---|---|
4 alignment marks
(Taran Apr 2023) |
X | 6 | 0.004 | -0.5±0.08 | -0.3±1.7 | 0.6±1.2 |
Y | 9 | -0.3±0.08 | 1.1±1.7 | -1.1±1.2 | ||
4 alignment marks
Low Res camera (Taran Apr 2023) |
X | 5 | 0.004 | -0.95±0.13 | -1.1±2.5 | -0.8±1.3 |
Y | 7 | 0.1±0.1 | -1.1±1.7 | -0.8±2.5 | ||
4 alignment marks
Fast exposure (Taran Apr 2023) |
X | 7 | 0.003 | -0.65±0.05 | -0.6±1.7 | 0.3±1.2 |
Y | 8 | -0.25±0.05 | 0.3±1.7 | -0.3±1.2 | ||
2 alignment marks
(Taran Apr 2023) |
X | NA | NA | -0.75±0.3 | -8.9±1.7 | -1.4±2.5 |
Y | NA | -0.55±0.28 | -6.1±2.5 | -0.8±1.2 |
Back Side Alignment
Overlay accuracy (spec): ±1 µm
BSA windows: along the X and Y axes, 10 mm wide x 46 mm long, starting 14.5 mm from the center.
Camera field of view (W x H): 640 µm x 480 µm
The alignment marks must be placed within the BSA windows. The Overview camera only shows the top side of the substrate, and cannot be used to locate the BSA marks.
Backside alignment test:
Misalignment [µm] | Comment | ||
---|---|---|---|
Align - flip 180° - align 3 point average |
X | -0.625 ±0.125 | 0.5 µm verniers
Taran May 2019 |
Y | -0.75 ±0.125 |
Advanced Field alignment (TSA)
Overlay accuracy (spec): 0.25 µm (5x5 mm2 area)
Shift, rotation, scaling, and shearing is determined and set by global alignment marks. The shift is corrected locally by automatic alignment to one mark in each field (chip).
Advanced field alignment test:
Median [nm] | Average [nm] | ||
---|---|---|---|
25 fields
375 nm, high res camera (Taran Sept 2023) |
X | -450 ±75 | -438 ±75 |
Y | -200 ±50 | -212 ±50 | |
25 fields
375 nm, high res camera (Taran Mar 2019) |
X | 50 ±75 | 70 ±75 |
Y | 150 ±50 | 128 ±50 |