Specific Process Knowledge/Thin film deposition/Deposition of Gold: Difference between revisions
(29 intermediate revisions by 4 users not shown) | |||
Line 1: | Line 1: | ||
'''Feedback to this page''': '''[mailto:labadviser@nanolab.dtu.dk?Subject=Feed%20back%20from%20page%20http://labadviser.nanolab.dtu.dk/index.php/Specific_Process_Knowledge/Thin_film_deposition/Deposition_of_Gold click here]''' | |||
'''Feedback to this page''': '''[mailto:labadviser@ | |||
Gold can be deposited by e-beam evaporation or sputtering. In the chart below you can compare the different deposition equipment. | <i> Unless otherwise stated, this page is written by <b>DTU Nanolab internal</b></i> | ||
Gold can be deposited by e-beam evaporation or sputtering. In the chart below you can compare the different deposition equipment. We also describe the temperature rise on the wafer during gold deposition, the adhesion layers that can be used for gold deposition, the roughness of gold deposited in the Wordentec, and issues with particulates on the gold films in the Temescal and the Wordentec. | |||
== Au deposition == | == Au deposition == | ||
Line 11: | Line 12: | ||
|-style="background:silver; color:black" | |-style="background:silver; color:black" | ||
! | ! | ||
! E-beam evaporation ([[Specific Process Knowledge/Thin film deposition/Temescal|E-beam evaporator Temescal]]) | ! E-beam evaporation ([[Specific Process Knowledge/Thin film deposition/Temescal|E-beam evaporator (Temescal)]] and [[Specific Process Knowledge/Thin film deposition/10-pocket e-beam evaporator|E-beam evaporator (10-pockets)]]) | ||
! E-beam evaporation ([[Specific Process Knowledge/Thin film deposition/Wordentec|Wordentec]]) | ! E-beam evaporation ([[Specific Process Knowledge/Thin film deposition/Wordentec|Wordentec]]) | ||
! Resistive thermal evaporation ([[Specific Process Knowledge/Thin film deposition/thermalevaporator|Thermal Evaporator]]) | |||
! Sputter ([[Specific Process Knowledge/Thin film deposition/Lesker|Lesker]]) | ! Sputter ([[Specific Process Knowledge/Thin film deposition/Lesker|Lesker]]) | ||
! | ! Sputter ([[Specific Process Knowledge/Thin film deposition/Cluster-based multi-chamber high vacuum sputtering deposition system|Sputter-system Metal-Oxide (PC1) and Sputter-system Metal-Nitride (PC3)]]) | ||
! Sputter coater [[Specific Process Knowledge/Thin film deposition/Sputter coater#Sputter coater 03|(Sputter coater 03)]] | ! Sputter coater [[Specific Process Knowledge/Thin film deposition/Sputter coater#Sputter coater 03|(Sputter coater 03)]] | ||
! Sputter coater [[Specific Process Knowledge/Thin film deposition/Sputter coater#Sputter coater 04|(Sputter coater 04)]] | ! Sputter coater [[Specific Process Knowledge/Thin film deposition/Sputter coater#Sputter coater 04|(Sputter coater 04)]] | ||
Line 21: | Line 23: | ||
| E-beam deposition of Au | | E-beam deposition of Au | ||
| E-beam deposition of Au | | E-beam deposition of Au | ||
| Resistive thermal deposition of Au | |||
| Sputter deposition of Au | |||
| Sputter deposition of Au | | Sputter deposition of Au | ||
| Sputter deposition of Au | | Sputter deposition of Au | ||
| Sputter deposition of Au | | Sputter deposition of Au | ||
Line 28: | Line 31: | ||
|-style="background:LightGrey; color:black" | |-style="background:LightGrey; color:black" | ||
! Pre-clean | ! Pre-clean | ||
|Ar ion | |Ar ion etch (only in E-beam evaporator Temescal) | ||
| | |||
| | |||
|RF Ar clean | |RF Ar clean | ||
|RF Ar clean | |RF Ar clean | ||
| | | | ||
| | | | ||
|-style="background:WhiteSmoke; color:black" | |-style="background:WhiteSmoke; color:black" | ||
! Layer thickness | ! Layer thickness | ||
|10 Å to 1 µm* | |10 Å to 1 µm * | ||
|10 Å to | |10 Å to 1 µm * | ||
|10 Å to | |10 Å to 200 nm | ||
|10 Å to | |10 Å to 5000 Å ** | ||
| | |10 Å to 5000 Å ** | ||
| | | very thin, few nm range | ||
| very thin, few nm range | |||
|- | |- | ||
|-style="background:LightGrey; color:black" | |-style="background:LightGrey; color:black" | ||
! Deposition rate | ! Deposition rate | ||
|0.5 Å/s to 10 Å/s | |0.5-10 Å/s (in 10-pocket machine only up to 5 Å/s as material is deposited from a liner) | ||
|1 Å/s to | |1-10 Å/s | ||
| | |1 Å/s (can be adjusted to around 5Å/s) | ||
|Depends on process parameters, 1-10 Å/s | |||
|Depends on process parameters | |||
|Not measured | |Not measured | ||
|Not measured | |Not measured | ||
Line 66: | Line 71: | ||
*6x4" wafers or | *6x4" wafers or | ||
*6x6" wafers | *6x6" wafers | ||
| | |||
*4x2" wafers or | |||
*3x4" wafers or | |||
*1x6" wafer | |||
*1x8" wafer | |||
*many smaller pieces | |||
| | | | ||
*Pieces or | *Pieces or | ||
Line 71: | Line 82: | ||
*1x6" wafer | *1x6" wafer | ||
| | | | ||
* | *Up to 10x6" or 4" wafers | ||
*Many small pieces | |||
* | |||
| | | | ||
*Several smaller samples | *Several smaller samples | ||
Line 87: | Line 97: | ||
| | | | ||
*See the [http://labmanager.dtu.dk/function.php?module=XcMachineaction&view=edit&MachID=429 cross-contamination sheet] | |||
*See | |||
| | | | ||
* Silicon oxide | * Silicon oxide | ||
Line 103: | Line 107: | ||
* SU-8 | * SU-8 | ||
* Metals | * Metals | ||
| | |||
* Almost any as long as it does not outgas - see cross-contamination sheets in Labmanager | |||
| | | | ||
* Silicon | * Silicon | ||
Line 115: | Line 121: | ||
* Carbon | * Carbon | ||
| | | | ||
* | * Almost any as long as it does not outgas - see cross-contamination sheets in Labmanager | ||
| | | | ||
* All samples allowed in the SEM Supra 1 | * All samples allowed in the SEM Supra 1 | ||
Line 128: | Line 131: | ||
| | | | ||
* For thicknesses above 600 nm permission is required | * For thicknesses above 600 nm permission is required | ||
* Takes approx. 20 min to pump down. | * Takes approx. 20 min to pump down. | ||
| | | | ||
* Takes approx. 1 hour to pump down. | * Takes approx. 1 hour to pump down. | ||
| | | | ||
*Make sure that all pellets are melted beforehand | |||
| | |||
*Takes approx. 10 minutes to load and transfer sample | |||
| | | | ||
* | * Takes approx. 12 minutes to load and transfer samples | ||
| | | | ||
* Used for gold sputter coating of samples before SEM inspection | * Used for gold sputter coating of samples before SEM inspection | ||
Line 149: | Line 150: | ||
'''*''' ''For thicknesses above 600 nm write to metal@ | '''*''' ''For thicknesses above 600 nm write to metal@nanolab.dtu.dk to ensure that there will be enough material in the machine.'' | ||
'''**''' ''For thicknesses above 200 nm write to metal@ | '''**''' ''For thicknesses above 200 nm write to metal@nanolab.dtu.dk to ensure that there will be enough material in the machine.'' | ||
== Studies of Au deposition processes in the Wordentec== | == Studies of Au deposition processes in the Wordentec== | ||
[[/Roughness of Au|Roughness of Au layers]] - ''Roughness of Au layers deposited | [[/Roughness of Au|Roughness of Au layers]] - ''Roughness of Au layers deposited in the Wordentec'' | ||
===Wafer temperature=== | ===Wafer temperature=== | ||
Line 183: | Line 184: | ||
The temperatures are accurate within approximately +/- 3C and probably underestimating the actual wafer temperature slightly. It is observed that the wafer temperature increases with each wafer, thus if wafer temperature is of concern it is advised to reduce the number of wafers per run. | The temperatures are accurate within approximately +/- 3C and probably underestimating the actual wafer temperature slightly. It is observed that the wafer temperature increases with each wafer, thus if wafer temperature is of concern it is advised to reduce the number of wafers per run. | ||
== Resistive thermal evaporation of Au == | |||
* [[Specific Process Knowledge/Thin film deposition/Deposition of Gold/Resistive thermal evaporation of Au in Thermal Evaporator|Resistive thermal evaporation of Au in Thermal Evaporator]] | |||
== Adhesion of Au on Si == | == Adhesion of Au on Si == | ||
The adhesion of gold on Silicon or Silicon with native oxide is not very good. The Si substrate is often deposited an adhesion layer before the gold deposition. A few nm of Chromium or Titanium works well and they react with the Oxygen of Silicon oxide and present a metallic bond with gold. 5 nm to 10 nm thick of Cr or Ti is commonly used and it is important to deposit Cr or Ti and then immediately Au. If the vacuum chamber is opened in between, the surface of Cr or Ti will get oxidized and that will give a poor adhesion. If a gold layer needs to be deposited directly on Silicon, then native oxide has to be removed by deep in diluted HF and immediately load the evaporation chamber. And after the deposition, the wafer has to be heated op to get some Au-Si diffusion which improves the adhesion. | The adhesion of gold on Silicon or Silicon with native oxide is not very good. The Si substrate is often deposited an adhesion layer before the gold deposition. A few nm of Chromium or Titanium works well and they react with the Oxygen of Silicon oxide and present a metallic bond with gold. You can also use polymer or organosilane adhesion layers as exemplified by the work in the next section. | ||
For Cr and Ti adhesion layers, a 5 nm to 10 nm thick layer of Cr or Ti is commonly used and it is important to deposit Cr or Ti and then immediately Au. If the vacuum chamber is opened in between, the surface of Cr or Ti will get oxidized and that will give a poor adhesion. If a gold layer needs to be deposited directly on Silicon, then native oxide has to be removed by deep in diluted HF and immediately load the evaporation chamber. And after the deposition, the wafer has to be heated op to get some Au-Si diffusion which improves the adhesion. | |||
*[[/Adhesion layers|Read more about Ti and Cr adhesion layers]]. | *[[/Adhesion layers|Read more about Ti and Cr adhesion layers]]. | ||
Line 191: | Line 197: | ||
Below you can read about using an organosilane adhesion layer. | Below you can read about using an organosilane adhesion layer. | ||
== Thin Au layer | == Thin Au layer using APTMS adhesion layer and sputter system Lesker == | ||
For depositing very thin, down to 6nm continuous Au layers on Si/SiO<sub>2</sub> substrates. Works also with ALD deposited Al<sub>2</sub>O<sub>3</sub> and TiO<sub>2</sub> as substrate. | For depositing very thin, down to 6nm continuous Au layers on Si/SiO<sub>2</sub> substrates. Works also with ALD deposited Al<sub>2</sub>O<sub>3</sub> and TiO<sub>2</sub> as substrate. | ||
Line 239: | Line 245: | ||
''NOTE: After depositing 10 layers of 10nm each, one on top of each other, the roughness increased to 0.8nm RMS'' | ''NOTE: After depositing 10 layers of 10nm each, one on top of each other, the roughness increased to 0.8nm RMS'' | ||
Work done by Johneph Sukham (@ DTU Fotonik) and Radu Malureanu (@ DTU Fotonik and DTU | Work done by Johneph Sukham (@ DTU Fotonik) and Radu Malureanu (@ DTU Fotonik and DTU Nanolab) in 2016-2017. | ||
==Particulates in e-beam evaporated films== | |||
[[File:particulates au film.png|right|thumb|upright=2|Alt=SEM image of a film with droplets ranging in size from a few hundred nanometers to about 1.5 microns.|Au droplets on an Au film (image by Evgeniy Shkondin, Au identified by EDX).]] | |||
We have found that the amount of particulates on the e-beam evaporated films depends on the deposition parameters. Specifically for gold it is hard to avoid tiny gold droplets on the films, but they can be minimized with careful attention to the sweep parameters, cleanliness of the target, etc. | |||
The droplets appear to be inconsequential for many users, for instance if the Au layer is simply used as an electrical contact. However, for some users it is very important, for instance when the exact resistivity of the Au layer is critical. | |||
You can read more about this issue [[Specific_Process_Knowledge/Thin_film deposition/Temescal/Particulates_in_Temescal_Au_films|here]]. | |||
<br clear="all" /> | |||
==Quality control of e-beam evaporated TiAu films== | |||
{| border="1" cellspacing="2" cellpadding="2" colspan="3" | |||
|bgcolor="#98FB98" |'''Quality control (QC) for the Temescal''' | |||
|- | |||
| | |||
*[http://labmanager.dtu.dk/d4Show.php?id=5862&mach=429 QC procedure for the Temescal]<br> | |||
*[https://labmanager.dtu.dk/view_binary.php?type=data&mach=429 The newest QC data for the Temescal]<br> | |||
{| {{table}} | |||
| align="center" | | |||
{| border="1" cellspacing="1" cellpadding="2" align="center" style="width:400px" | |||
! QC Recipe: | |||
! Standard recipes/TiAu or Cr/Au | |||
|- | |||
|Deposition rate | |||
|was at 10 Å/s (change to 2 Å/s from October 2022 as it gives less particles) | |||
|- | |||
|Thickness | |||
|10 nm / 90 nm | |||
|- | |||
|Pressure | |||
|Below 1*10<sup>-6</sup> mbar | |||
|- | |||
|} | |||
| align="center" valign="top"| | |||
{| border="2" cellspacing="1" cellpadding="2" align="center" style="width:440px" | |||
!QC limits | |||
!Temescal | |||
|- | |||
|Deposition rate deviation | |||
|± 20 % | |||
|- | |||
|Measured average thickness | |||
|± 10 % | |||
|- | |||
|Thickness deviation across a 4" wafer | |||
|± 5 % | |||
|- | |||
|} | |||
|- | |||
|} | |||
Thickness is measured in 5 points with a stylus profiler. <br> | |||
Additionally we examine the newly deposited films for particles using the particle scanner (if available, otherwise we use the Jenatech microscope in darkfield mode) and we monitor the sheet resistance of the Ti/Au or Cr/Au films. | |||
|} | |||
{| border="1" cellspacing="2" cellpadding="2" colspan="3" | |||
|bgcolor="#98FB98" |'''Quality control (QC) for Wordentec''' | |||
|- | |||
| | |||
*[http://labmanager.dtu.dk/d4Show.php?id=3736&mach=167 QC procedure for Wordentec]<br> | |||
*[https://labmanager.dtu.dk/view_binary.php?type=data&mach=167 The newest QC data for Wordentec]<br> | |||
{| {{table}} | |||
| align="center" | | |||
{| border="1" cellspacing="1" cellpadding="2" align="center" style="width:300px" | |||
! QC Recipe: | |||
! Process 13 | |||
|- | |||
|Deposition rate | |||
|10 Å/s | |||
|- | |||
|Thickness | |||
|10 nm / 90 nm | |||
|- | |||
|Pressure | |||
|Below 4*10<sup>-6</sup> mbar | |||
|- | |||
|} | |||
| align="center" valign="top"| | |||
{| border="2" cellspacing="1" cellpadding="2" align="center" style="width:440px" | |||
!QC limits | |||
!Wordentec | |||
|- | |||
|Measured average thickness (Å) | |||
|± 10 % | |||
|- | |||
|Lowest accepted deposition rate (Å/s) | |||
|6 Å/s | |||
|- | |||
|} | |||
|- | |||
|} | |||
Thickness is measured in 5 points with a stylus profiler. | |||
|} |
Latest revision as of 16:35, 7 February 2024
Feedback to this page: click here
Unless otherwise stated, this page is written by DTU Nanolab internal
Gold can be deposited by e-beam evaporation or sputtering. In the chart below you can compare the different deposition equipment. We also describe the temperature rise on the wafer during gold deposition, the adhesion layers that can be used for gold deposition, the roughness of gold deposited in the Wordentec, and issues with particulates on the gold films in the Temescal and the Wordentec.
Au deposition
Below you can compare the different equipment that allows Au deposition.
E-beam evaporation (E-beam evaporator (Temescal) and E-beam evaporator (10-pockets)) | E-beam evaporation (Wordentec) | Resistive thermal evaporation (Thermal Evaporator) | Sputter (Lesker) | Sputter (Sputter-system Metal-Oxide (PC1) and Sputter-system Metal-Nitride (PC3)) | Sputter coater (Sputter coater 03) | Sputter coater (Sputter coater 04) | |
---|---|---|---|---|---|---|---|
General description | E-beam deposition of Au | E-beam deposition of Au | Resistive thermal deposition of Au | Sputter deposition of Au | Sputter deposition of Au | Sputter deposition of Au | Sputter deposition of Au |
Pre-clean | Ar ion etch (only in E-beam evaporator Temescal) | RF Ar clean | RF Ar clean | ||||
Layer thickness | 10 Å to 1 µm * | 10 Å to 1 µm * | 10 Å to 200 nm | 10 Å to 5000 Å ** | 10 Å to 5000 Å ** | very thin, few nm range | very thin, few nm range |
Deposition rate | 0.5-10 Å/s (in 10-pocket machine only up to 5 Å/s as material is deposited from a liner) | 1-10 Å/s | 1 Å/s (can be adjusted to around 5Å/s) | Depends on process parameters, 1-10 Å/s | Depends on process parameters | Not measured | Not measured |
Batch size |
|
|
|
|
|
|
|
Allowed materials |
|
|
|
|
|
|
|
Comment |
|
|
|
|
|
|
|
* For thicknesses above 600 nm write to metal@nanolab.dtu.dk to ensure that there will be enough material in the machine.
** For thicknesses above 200 nm write to metal@nanolab.dtu.dk to ensure that there will be enough material in the machine.
Studies of Au deposition processes in the Wordentec
Roughness of Au layers - Roughness of Au layers deposited in the Wordentec
Wafer temperature
The wafer temperature during e-beam deposition of 200 nm Au on six wafers has been measured using thermal labels on the backside of the wafers. The following results were obtained:
Wafer | Temperature [C] |
---|---|
1 | 48 |
2 | 60 |
3 | 65 |
4 | 71 |
5 | 71 |
6 | 77 |
The temperatures are accurate within approximately +/- 3C and probably underestimating the actual wafer temperature slightly. It is observed that the wafer temperature increases with each wafer, thus if wafer temperature is of concern it is advised to reduce the number of wafers per run.
Resistive thermal evaporation of Au
Adhesion of Au on Si
The adhesion of gold on Silicon or Silicon with native oxide is not very good. The Si substrate is often deposited an adhesion layer before the gold deposition. A few nm of Chromium or Titanium works well and they react with the Oxygen of Silicon oxide and present a metallic bond with gold. You can also use polymer or organosilane adhesion layers as exemplified by the work in the next section.
For Cr and Ti adhesion layers, a 5 nm to 10 nm thick layer of Cr or Ti is commonly used and it is important to deposit Cr or Ti and then immediately Au. If the vacuum chamber is opened in between, the surface of Cr or Ti will get oxidized and that will give a poor adhesion. If a gold layer needs to be deposited directly on Silicon, then native oxide has to be removed by deep in diluted HF and immediately load the evaporation chamber. And after the deposition, the wafer has to be heated op to get some Au-Si diffusion which improves the adhesion.
Below you can read about using an organosilane adhesion layer.
Thin Au layer using APTMS adhesion layer and sputter system Lesker
For depositing very thin, down to 6nm continuous Au layers on Si/SiO2 substrates. Works also with ALD deposited Al2O3 and TiO2 as substrate.
Adhesion promoter: aminopropyltrimethoxysilane (APTMS). MSDS here.
Adhesion promoter deposition: 3h immersion in 95%IPA, 2.5% H2O, 2.5% APTMS.
NOTE: the APTMS layer is degrading quickly in atmosphere, so deposit it as close to the Au deposition as possible.
Lesker deposition parameters:
Gun # | Power [W] | Ramp rate [W/s] | Pressure [mtorr] | Atmosphere | Deposition rate [nm/s] |
---|---|---|---|---|---|
2 | 300 | 5 | 3 | Ar | 1 |
NOTE: As a general rule, the lower the pressure and higher the power (i.e. higher the deposition rate), the better.
Film characteristics (5-10 wafers for each thickness):
Thickness [nm] | Roughness min [nm] | Roughness max [nm] |
---|---|---|
6 | 0.25 | 0.4 |
10 | 0.3 | 0.5 |
24 | 0.3 | 0.5 |
NOTE: After depositing 10 layers of 10nm each, one on top of each other, the roughness increased to 0.8nm RMS
Work done by Johneph Sukham (@ DTU Fotonik) and Radu Malureanu (@ DTU Fotonik and DTU Nanolab) in 2016-2017.
Particulates in e-beam evaporated films
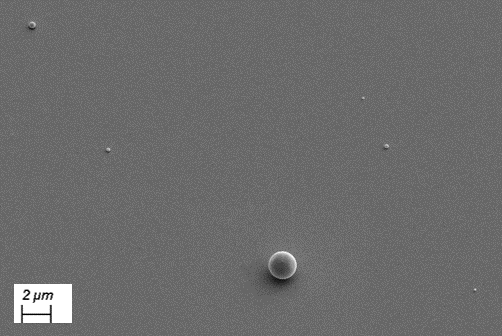
We have found that the amount of particulates on the e-beam evaporated films depends on the deposition parameters. Specifically for gold it is hard to avoid tiny gold droplets on the films, but they can be minimized with careful attention to the sweep parameters, cleanliness of the target, etc.
The droplets appear to be inconsequential for many users, for instance if the Au layer is simply used as an electrical contact. However, for some users it is very important, for instance when the exact resistivity of the Au layer is critical.
You can read more about this issue here.
Quality control of e-beam evaporated TiAu films
Quality control (QC) for the Temescal | ||||||||||||||||||
Thickness is measured in 5 points with a stylus profiler. |
Quality control (QC) for Wordentec | ||||||||||||||||
Thickness is measured in 5 points with a stylus profiler. |