Specific Process Knowledge/Etch/DRIE-Pegasus/Pegasus-2: Difference between revisions
No edit summary |
|||
(179 intermediate revisions by 4 users not shown) | |||
Line 1: | Line 1: | ||
'''Feedback to this page: | |||
[mailto:labadviser@nanolab.dtu.dk?Subject=Feed%20back%20from%20page%20http://labadviser.danchip.dtu.dk/index.php/Specific_Process_Knowledge/Etch/DRIE-Pegasus/Pegasus-2 click here]''' | |||
[[Category: Equipment |Etch DRIE]] | |||
[[Category: Etch (Dry) Equipment|DRIE]] | |||
= DRIE-Pegasus 2= | |||
{{Author-jmli1}} | |||
[[File:Pegasus 2 operator.jpg|right|400px|The DRIE-Pegasus 2 operator station and load lock in the DTU Nanolab cleanroom A-1. {{photo1}}]] | |||
'''The user manual(s), user APV(s), technical information and contact information can be found in LabManager:''' | |||
Equipment info in [http://labmanager.dtu.dk/function.php?module=Machine&view=view&mach=398| LabManager] | |||
==Restricted usage on a dedicated research tool == | |||
In general, the dry etch tools at DTU Nanolab are free to use for users with proper training. The users have freedom to etch the approved materials and substrates within the rules specified in manuals, LabAdviser and cross contamination sheets. At the same time, the instruments are set up to meet a wide range of etch demands in this way ensuring that most dry etch applications can be covered. Indeed, for most of the instruments there is a continuous tug of war between providing flexibility (for instance allowing mask materials that do not form any volatile etch products with the gas chemistry available in the process chamber) while ensuring process chamber cleanliness. | |||
Pegasus 2 stands out as it is a dedicated research tool where much fewer processes are allowed. As such, the instrument will not be released for general use for a wide range of applications. | |||
Whereas Pegasus 1 and 3 are intended to serve as stable platforms with limited or no changes in hardware, Pegasus 2 has been subject to experiments. For instance, as of the end of 2020 the instrument has been set up to run [[Specific_Process_Knowledge/Etch/DRIE-Pegasus/Pegasus-2#Publications_on_the_CORE_process|the CORE process]]. This means that comparing to [[Specific_Process_Knowledge/Etch/DRIE-Pegasus/Pegasus-1|DRIE-Pegasus 1]] and [[Specific_Process_Knowledge/Etch/DRIE-Pegasus/Pegasus-3|DRIE-Pegasus 3]], Pegasus 2 and its allowed usage have been modified (this list is not complete - see the complete list in the table below). For instance: | |||
# The C<sub>4</sub>F<sub>8</sub> MFC has been disconnected to maintain a carbon-free (carbon containing masks are allowed) chamber. | |||
|- | # The RF generator supplying the power to the coil has been disconnected thus allowing only processes driven by the platen generator. | ||
This kind of experiment will not be allowed on other dry etch tools as it is obvious that this is incompatible with running any of the usual Bosch processes. | |||
Therefore, you should always make sure that whatever process you may want to run on Pegasus 2 is allowed or even possible. The table below should provide this information. If you want to get access to the tool, then talk to the dry etch group. | |||
== Current setup and rules on Pegasus 2 == | |||
Click [[Specific Process Knowledge/Etch/DRIE-Pegasus/Pegasus-2/OldConfig | '''here''']] to access older configurations. | |||
The current configuration is set up for nanoscale etching using the CORE recipe. | |||
{{Template:Peg2configheader1 | |||
|TableHeader= 7: Currently valid from May 17 2023 onwards | |||
}} | |||
{{Template:Peg2configcontent1 | |||
|ItemName= Available gasses and gas chemistry | |||
|ItemConfiguration= '''Available gasses:''' | |||
* SF<sub>6</sub>-1: 1200 sccm | |||
* SF<sub>6</sub>-2: 50 sccm | |||
* O<sub>2</sub>: 50 sccm | |||
* Ar: 283 | |||
* N<sub>2</sub>: 500 sccm | |||
* He: 11 sccm | |||
'''Not available:''' | |||
* C<sub>4</sub>F<sub>8</sub> (H<sub>2</sub> currently fitted but closed) : 0 sccm | |||
* CO<sub>2</sub>: (It is not in the software) | |||
|ItemComment=Only SF<sub>6</sub> and O<sub>2</sub> are used for Si, PR, and Cr etch. The rest is only make-up | |||
}} | |||
{{Template:Peg2configcontent1 | |||
|ItemName= Plasma source heaters | |||
|ItemConfiguration=The following heaters in the plasma source are off: | |||
* Plenum Heater | |||
* Inner Heater | |||
* Magnetic Confinement Heater | |||
* Chamber Heater | |||
|ItemComment= The temperature on the heaters in the plasma source are set to 20 degrees with a high tolerance. This essentially corresponds to powered off compared to default Pegasus temperatures which are in the 120-140 degrees range. The absence of fluorocarbons in the plasma makes it unnecessary to maintain a high temperature on the chamber walls in order to reduce polymer condensation (see below). | |||
Always make sure that the temperature settings in the recipes are ''not'' enabled. Click [[Specific Process Knowledge/Etch/DRIE-Pegasus/Pegasus-2/TemperatureSettings |'''here''']] to have more information. | |||
}} | |||
{{Template:Peg2configcontent1 | |||
|ItemName= Carbon free plasmas | |||
|ItemConfiguration= The process chamber does not have any carbon containing etch gasses. Therefore, polymer build-up on the chamber walls is not an issue. The 'carbon free' policy does not, however, apply to the choice of masking materials and CSAR, AZ and DUV resists are allowed. | |||
|ItemComment= | |||
}} | |||
{{Template:Peg2configcontent1 | |||
|ItemName= Chamber conditioning and cleaning | |||
|ItemConfiguration= Running long oxygen cleans is not necessary and must be avoided. Neither are shorter cleans between wafers. | |||
|ItemComment= The absence of carbon containing etch gasses ensures that the process chamber is kept clean. | |||
}} | |||
{{Template:Peg2configcontent1 | |||
|ItemName= Recipes | |||
|ItemConfiguration= Do ''not'' run any recipes from the folder called 'z-Archive'. | |||
|ItemComment= The configuration of Pegasus 2 has changed over time (hence this table) so there is a large number of recipes that are no longer working. Also, some inappropriate settings in the some recipes (mainly with respect to the pressure control) have been identified. This is why it was decided that all existing (by autumn 2022) recipes be relocated to the folder called 'z-Archive' from which they must serve ''only'' as backup. To run a recipe in the z-Archive folder, it must be verified by the dry etch group and copied to another folder (typically user\group\****). | |||
}} | |||
{{Template:Peg2configcontent1 | |||
|ItemName= Etch of chromium and silicon nitrides | |||
|ItemConfiguration= Recipes for etching chromium and silicon nitrides have been developed. | |||
|ItemComment= Etching the two materials is only allowed for processes in combination with other Pegasus 2 specific recipes such as the CORE recipe. '''Always consult with Nanolab staff.''' | |||
}} | |||
{{Template:Peg2configcontent1 | |||
|ItemName= Electrostatic clamping and helium backside cooling are again mandatory. | |||
|ItemConfiguration= The processes run in Pegasus 2 operate at such low powers that they do not require very efficient cooling. It has therefore been decided that the following options/procedures | |||
* Electrostatic clamping of carriers/substrates | |||
* The Helium backside cooling is kept at 5 Torr instead of the usual 10 Torr on the other Pegasus tools. | |||
* Using bonding procedures such as droplets of Galden oil to increase thermal contact between chips and carrier | |||
will no longer be required. | |||
|ItemComment= So far we have not seen any changes in the results but if you do, please contact Nanolab staff. | |||
}} | |||
{{Template:Peg2configcontent1 | |||
|ItemName= Background knowledge required for safe operation | |||
|ItemConfiguration= The users and supervisors of Pegasus-2 must carefully read the 4 papers listed in the comments in order to have a correct understanding of the etch process and experimental procedure and how it relates to the Bosch etch performance. | |||
|ItemComment= See the papers in the [[Specific_Process_Knowledge/Etch/DRIE-Pegasus/Pegasus-2#Publications_on_the_CORE_process |section below]]. | |||
}} | |||
|} | |} | ||
=== Publications on the CORE process === | |||
<span id="anchor_CORE1"></span> | |||
The CORE process is described in detail in the publications below: | |||
; Nguyen, V. T. et al.: On the formation of black silicon in SF6-O2 plasma: The clear, oxidize, remove, and etch (CORE) sequence and black silicon on demand | |||
: 2020 Journal of Vacuum Science & Technology. A. Vacuum, Surfaces, and Films, 38(4), [043004]. | |||
: https://doi.org/10.1116/6.0000196 | |||
; Vy Thi Hoang Nguyen et al.: The CORE Sequence: A Nanoscale Fluorocarbon-Free Silicon Plasma Etch Process Based on SF6/O2 Cycles with Excellent 3D Profile Control at Room Temperature | |||
: 2020 ECS J. Solid State Sci. Technol. 9 024002 | |||
: https://doi.org/10.1149/2162-8777/ab61ed | |||
; Vy Thi Hoang Nguyen et al.: Ultrahigh aspect ratio etching of silicon in SF<sub>6</sub>-O<sub>2</sub> plasma: The clear-oxidize-remove etch (CORE) sequence and chromium mask | |||
: 2020 Journal of Vacuum Science & Technology. A. Vacuum, Surfaces, and Films, 38(5), [053002] | |||
: https://doi.org/10.1116/6.0000357 | |||
; Vy Thi Hoang Nguyen et al.: Cr and CrO<sub>x</sub> etching using SF<sub>6</sub> and O2 plasma | |||
: 2021 Journal of Vacuum Science and Technology B: Nanotechnology and Microelectronics, 39(3), [032201] | |||
: https://doi.org/10.1116/6.0000922 | |||
== Process information == | |||
New recipes are being developed all the time and the total number of recipes on the tool is huge. However, as the configuration of the instrument changes over time a vast majority of the recipes may no longer be safe to run. Unless you have specific permission to run other recipes, the only recipes that you can safely run are the ones in the 'std' folder as shown above in the table. If you have your own recipe folder, always verify that the recipe you want to run is present in the 'std' folder. | |||
=== Previous work on Pegasus 2 === | |||
|- | * [[Specific Process Knowledge/Etch/DRIE-Pegasus/Pegasus-2/Nanoscale silicon etching with SF6 and O2|Nanoscale silicon etching with SF6 and O2 (the CORE process)]] | ||
| | * [[Specific Process Knowledge/Etch/DRIE-Pegasus/Pegasus-2/Black silicon on Demand|Black silicon on Demand]] | ||
* [[/ORE with Al2O3 mask|The ORE process with Al2O3 mask]] | |||
*[[/Nanoscale silicon nitride etch with SF6|Nanoscale silicon nitride etch with SF6]] |
Latest revision as of 08:14, 30 July 2024
Feedback to this page: click here
DRIE-Pegasus 2
Unless otherwise stated, all content on this page was created by Jonas Michael-Lindhard, DTU Nanolab
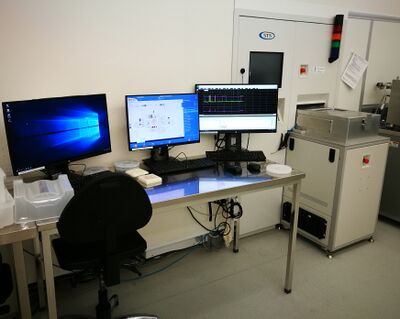
The user manual(s), user APV(s), technical information and contact information can be found in LabManager:
Equipment info in LabManager
Restricted usage on a dedicated research tool
In general, the dry etch tools at DTU Nanolab are free to use for users with proper training. The users have freedom to etch the approved materials and substrates within the rules specified in manuals, LabAdviser and cross contamination sheets. At the same time, the instruments are set up to meet a wide range of etch demands in this way ensuring that most dry etch applications can be covered. Indeed, for most of the instruments there is a continuous tug of war between providing flexibility (for instance allowing mask materials that do not form any volatile etch products with the gas chemistry available in the process chamber) while ensuring process chamber cleanliness.
Pegasus 2 stands out as it is a dedicated research tool where much fewer processes are allowed. As such, the instrument will not be released for general use for a wide range of applications.
Whereas Pegasus 1 and 3 are intended to serve as stable platforms with limited or no changes in hardware, Pegasus 2 has been subject to experiments. For instance, as of the end of 2020 the instrument has been set up to run the CORE process. This means that comparing to DRIE-Pegasus 1 and DRIE-Pegasus 3, Pegasus 2 and its allowed usage have been modified (this list is not complete - see the complete list in the table below). For instance:
- The C4F8 MFC has been disconnected to maintain a carbon-free (carbon containing masks are allowed) chamber.
- The RF generator supplying the power to the coil has been disconnected thus allowing only processes driven by the platen generator.
This kind of experiment will not be allowed on other dry etch tools as it is obvious that this is incompatible with running any of the usual Bosch processes.
Therefore, you should always make sure that whatever process you may want to run on Pegasus 2 is allowed or even possible. The table below should provide this information. If you want to get access to the tool, then talk to the dry etch group.
Current setup and rules on Pegasus 2
Click here to access older configurations.
The current configuration is set up for nanoscale etching using the CORE recipe.
Item | The currently applied modification | Comments |
---|---|---|
Available gasses and gas chemistry | Available gasses:
Not available:
|
Only SF6 and O2 are used for Si, PR, and Cr etch. The rest is only make-up |
Plasma source heaters | The following heaters in the plasma source are off:
|
The temperature on the heaters in the plasma source are set to 20 degrees with a high tolerance. This essentially corresponds to powered off compared to default Pegasus temperatures which are in the 120-140 degrees range. The absence of fluorocarbons in the plasma makes it unnecessary to maintain a high temperature on the chamber walls in order to reduce polymer condensation (see below).
Always make sure that the temperature settings in the recipes are not enabled. Click here to have more information. |
Carbon free plasmas | The process chamber does not have any carbon containing etch gasses. Therefore, polymer build-up on the chamber walls is not an issue. The 'carbon free' policy does not, however, apply to the choice of masking materials and CSAR, AZ and DUV resists are allowed. | |
Chamber conditioning and cleaning | Running long oxygen cleans is not necessary and must be avoided. Neither are shorter cleans between wafers. | The absence of carbon containing etch gasses ensures that the process chamber is kept clean. |
Recipes | Do not run any recipes from the folder called 'z-Archive'. | The configuration of Pegasus 2 has changed over time (hence this table) so there is a large number of recipes that are no longer working. Also, some inappropriate settings in the some recipes (mainly with respect to the pressure control) have been identified. This is why it was decided that all existing (by autumn 2022) recipes be relocated to the folder called 'z-Archive' from which they must serve only as backup. To run a recipe in the z-Archive folder, it must be verified by the dry etch group and copied to another folder (typically user\group\****). |
Etch of chromium and silicon nitrides | Recipes for etching chromium and silicon nitrides have been developed. | Etching the two materials is only allowed for processes in combination with other Pegasus 2 specific recipes such as the CORE recipe. Always consult with Nanolab staff. |
Electrostatic clamping and helium backside cooling are again mandatory. | The processes run in Pegasus 2 operate at such low powers that they do not require very efficient cooling. It has therefore been decided that the following options/procedures
will no longer be required. |
So far we have not seen any changes in the results but if you do, please contact Nanolab staff. |
Background knowledge required for safe operation | The users and supervisors of Pegasus-2 must carefully read the 4 papers listed in the comments in order to have a correct understanding of the etch process and experimental procedure and how it relates to the Bosch etch performance. | See the papers in the section below. |
Publications on the CORE process
The CORE process is described in detail in the publications below:
- Nguyen, V. T. et al.
- On the formation of black silicon in SF6-O2 plasma: The clear, oxidize, remove, and etch (CORE) sequence and black silicon on demand
- 2020 Journal of Vacuum Science & Technology. A. Vacuum, Surfaces, and Films, 38(4), [043004].
- https://doi.org/10.1116/6.0000196
- Vy Thi Hoang Nguyen et al.
- The CORE Sequence: A Nanoscale Fluorocarbon-Free Silicon Plasma Etch Process Based on SF6/O2 Cycles with Excellent 3D Profile Control at Room Temperature
- 2020 ECS J. Solid State Sci. Technol. 9 024002
- https://doi.org/10.1149/2162-8777/ab61ed
- Vy Thi Hoang Nguyen et al.
- Ultrahigh aspect ratio etching of silicon in SF6-O2 plasma: The clear-oxidize-remove etch (CORE) sequence and chromium mask
- 2020 Journal of Vacuum Science & Technology. A. Vacuum, Surfaces, and Films, 38(5), [053002]
- https://doi.org/10.1116/6.0000357
- Vy Thi Hoang Nguyen et al.
- Cr and CrOx etching using SF6 and O2 plasma
- 2021 Journal of Vacuum Science and Technology B: Nanotechnology and Microelectronics, 39(3), [032201]
- https://doi.org/10.1116/6.0000922
Process information
New recipes are being developed all the time and the total number of recipes on the tool is huge. However, as the configuration of the instrument changes over time a vast majority of the recipes may no longer be safe to run. Unless you have specific permission to run other recipes, the only recipes that you can safely run are the ones in the 'std' folder as shown above in the table. If you have your own recipe folder, always verify that the recipe you want to run is present in the 'std' folder.