Specific Process Knowledge/Characterization/Stress measurement: Difference between revisions
(26 intermediate revisions by 2 users not shown) | |||
Line 1: | Line 1: | ||
'''Feedback to this page''': '''[mailto:labadviser@ | '''Feedback to this page''': '''[mailto:labadviser@nanolab.dtu.dk?Subject=Feed%20back%20from%20page%20http://labadviser.danchip.dtu.dk/index.php/Specific_Process_Knowledge/Characterization/Stress_measurement click here]''' | ||
''All content by Nanolab staff unless otherwise noted'' | |||
Stress | =Stress measurement= | ||
The | The stress in a thin film can be quantified with a [http://labadviser.nanolab.dtu.dk/index.php/Specific_Process_Knowledge/Characterization/Profiler profilometer] by measuring the wafer bow before and after deposition of the film. If the thin film is deposited on both sides of the wafer, you can measure the bow after deposition and again after removing the film from one of the sides. | ||
== | If your thin film is crystalline, you can also measure stress using [[#Stress measurement using XRD|XRD]]. | ||
==Types of stress and their origin == | |||
A thin film can exhibit either compressive or tensile stress as illustrated by Figure 1: | |||
[[File:berit-film-stress-illustration-cropped.png|upright=3|alt=A rectangle illustrates a substrate without stress. A downward curving section of a sphere with a red band on top illustrates a substrate with compressive stress due to a thinfilm. An upward curving section of a sphere with a green band on top illustrates a substrate with tensile stress.|right|thumb|Figure 1: Compressive and tensile stress (figure by Berit Herstrøm).]] | |||
Examples of thin films that exhibit tensile stress include Cr, Pt, and Ni (evaporated or sputtered) as well as SiO2 made by LPCVD TEOS. SiN made by PECVD can exhibit either tensile or compressive stress. The same is true for sputtered Si. Thin films that exhibit compressive stress include e-beam evaporated Ti and Au. | |||
*Here you can read in general about [[Specific Process Knowledge/Characterization/Stress measurement/Stress origins|stress in thin metal films]]. | |||
*Here you can find some information about [[Specific Process Knowledge/Thin film deposition/Lesker/Stress dependence on sputter parameters in the Lesker sputter system|stress in sputtered films]] made at Nanolab. | |||
*Here you can find information about [[Specific Process Knowledge/Thin film deposition/Deposition of Nickel/Stress Wordentec Ni films|tensile stress in e-beam evaporated Ni films]]. | |||
*Here you can find a little information about [http://labadviser.nanolab.dtu.dk/index.php/Specific_Process_Knowledge/Thin_film_deposition/Deposition_of_NiFe tensile stress in Invar], a type of NiFe alloy. | |||
<br clear="all" /> | |||
==Stress measurement using a profilometer== | |||
Using a profilometer, the procedure is as follows: | |||
===When a thin film is deposited on one side of the wafer=== | |||
#Measure the thickness of the wafer | #Measure the thickness of the wafer | ||
#Make a pre-stress measurement. Measure the wafer bow on one of the stylus profilometers in the cleanroom, the ([[Specific Process Knowledge/Characterization/Profiler#Dektak XTA_new stylus profiler|Dektak XTA]] or [[Specific Process Knowledge/Characterization/Profiler#Stylus Profiler (Tencor P17)|P17 Stylus profiler]]). Save the measurement. It is a good idea to measure across most of the wafer (at least along 70% of the wafer diameter) in two directions perpendicular to each other. Using the P17 profiler you can measure a full radially resolved map of the wafer stress with up to 5° resolution. | |||
#Deposit the thin film | #Deposit the thin film | ||
#Measure the thickness of the thin film (ex. using the FilmTek or the Ellipsometer). | #Measure the thickness of the thin film (ex. using the FilmTek or the Ellipsometer). | ||
#Make a post-stress measurement | #Make a post-stress measurement: Measure the wafer bow again: | ||
#*On the same profilometer as used for the pre-measurement. | #*On the same profilometer as used for the pre-measurement. | ||
#*With the same recipe as used for the pre-mesurement. | #*With the same recipe as used for the pre-mesurement. | ||
Line 18: | Line 40: | ||
#*The profiler program asks for a substrate elasticity (choose the substrate type, e.g. Si(100)), substrate thickness, film thickness and the name of the pre-stress measurement. | #*The profiler program asks for a substrate elasticity (choose the substrate type, e.g. Si(100)), substrate thickness, film thickness and the name of the pre-stress measurement. | ||
==When a thin | ===When a thin film is deposited on both sides of the wafer=== | ||
# | #Measure the thickness of the wafer | ||
#Make a pre-stress measurement. Measure the wafer bow on one of the profilometers ([[Specific Process Knowledge/Characterization/Profiler#Dektak XTA_new stylus profiler|Dektak | #Deposit the thin film | ||
#Make a pre-stress measurement. Measure the wafer bow on one of the profilometers ([[Specific Process Knowledge/Characterization/Profiler#Dektak XTA_new stylus profiler|Dektak XTA]] or [[Specific Process Knowledge/Characterization/Profiler#Stylus Profiler (Tencor P17)|P17 Stylus profiler]]). Save the measurement. It is a good idea to measure across most of the wafer (at least along 70% of the wafer length) in two directions perpendicular to each other. Using the P17 profiler you can also measure a radially resolved map of the wafer stress with up to 5° resolution. | |||
#Remove the thin film from one side of the wafer. If it is a single side polished wafer, then remove it on the non-polished side. | #Remove the thin film from one side of the wafer. If it is a single side polished wafer, then remove it on the non-polished side. | ||
#Make a post-stress measurement. Measure the wafer bow again: | #Make a post-stress measurement. Measure the wafer bow again: | ||
#*On the same profilometer as used for the pre-measurement. | #*On the same profilometer as used for the pre-measurement. | ||
#*With the same recipe as used for the pre-mesurement. | #*With the same recipe as used for the pre-mesurement. | ||
#*On the same position | #*On the same position(s) on the wafer as the pre-measurement. | ||
#Measure the thickness of the thin film (ex. using the FilmTek or the Ellipsometer). | #Measure the thickness of the thin film (ex. using the FilmTek or the Ellipsometer). | ||
#Use the program for stress measurement in the profilometer software. Use both the pre-stress measurement and the post-stress measurement. | #Use the program for stress measurement in the profilometer software. Use both the pre-stress measurement and the post-stress measurement. | ||
#*The profiler program asks for substrate elasticity (choose the substrate type, e.g. Si(100)), substrate thickness, film thickness and the name of the pre-stress measurement. | #*The profiler program asks for substrate elasticity (choose the substrate type, e.g. Si(100)), substrate thickness, film thickness and the name of the pre-stress measurement. | ||
==Stress measurement using XRD== | |||
After you make a [[Specific_Process_Knowledge/Characterization/XRD/Process_Info#Theta-2Theta|θ-2θ scan]] of a crystalline thin film, the peak positions can be used to calculate the lattice constant of the film. By comparing the calculated lattice constant to the theoretical one, you can calculate the amount of compressive or tensile stress. It is important to align the thin film carefully to the beam height, as you can in the [[Specific_Process_Knowledge/Characterization/XRD/XRD SmartLab|XRD Smartlab]]. You may use a standard measurement (e.g. of a crystalline Si sample) to be able to take into account the intrinsic peak broadening of the instrument. Use the Ni-filter to remove the K<sub>β</sub> side peaks and if you have enough signal you can also use the monochromator and analyzer crystals to remove the K<sub>α2</sub> contribution. | |||
Nanolab has the [[Specific_Process_Knowledge/Characterization/XRD/SLSII_analysis|SmartLab Studio software]] and the Malvern Panalytical HighScore software available for quantifying the stress (ask staff for details). There is a good summary of the principles of the strain calculation in the last section of the [https://labmanager.dtu.dk/view_binary.php?fileId=4247 associated help document] for the SmartLab Studio software. | |||
You may be able to measure the relaxed lattice directly rather than comparing to a theoretical lattice, but you would have to be able to release the film and measure it separately (if this means scraping the thin film off your sample mechanically, you could potentially measure it in the [[Specific_Process_Knowledge/Characterization/XRD/XRD Powder|XRD Powder]], but it would probably be difficult to get enough powder to get a good signal). |
Latest revision as of 11:27, 9 February 2024
Feedback to this page: click here
All content by Nanolab staff unless otherwise noted
Stress measurement
The stress in a thin film can be quantified with a profilometer by measuring the wafer bow before and after deposition of the film. If the thin film is deposited on both sides of the wafer, you can measure the bow after deposition and again after removing the film from one of the sides.
If your thin film is crystalline, you can also measure stress using XRD.
Types of stress and their origin
A thin film can exhibit either compressive or tensile stress as illustrated by Figure 1:
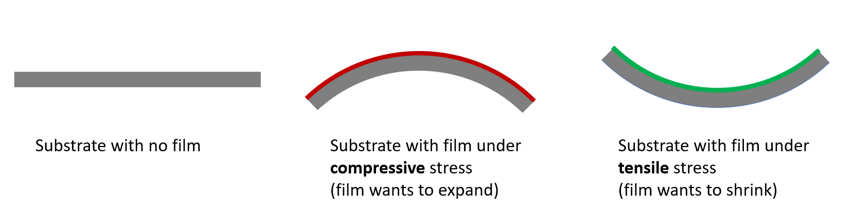
Examples of thin films that exhibit tensile stress include Cr, Pt, and Ni (evaporated or sputtered) as well as SiO2 made by LPCVD TEOS. SiN made by PECVD can exhibit either tensile or compressive stress. The same is true for sputtered Si. Thin films that exhibit compressive stress include e-beam evaporated Ti and Au.
- Here you can read in general about stress in thin metal films.
- Here you can find some information about stress in sputtered films made at Nanolab.
- Here you can find information about tensile stress in e-beam evaporated Ni films.
- Here you can find a little information about tensile stress in Invar, a type of NiFe alloy.
Stress measurement using a profilometer
Using a profilometer, the procedure is as follows:
When a thin film is deposited on one side of the wafer
- Measure the thickness of the wafer
- Make a pre-stress measurement. Measure the wafer bow on one of the stylus profilometers in the cleanroom, the (Dektak XTA or P17 Stylus profiler). Save the measurement. It is a good idea to measure across most of the wafer (at least along 70% of the wafer diameter) in two directions perpendicular to each other. Using the P17 profiler you can measure a full radially resolved map of the wafer stress with up to 5° resolution.
- Deposit the thin film
- Measure the thickness of the thin film (ex. using the FilmTek or the Ellipsometer).
- Make a post-stress measurement: Measure the wafer bow again:
- On the same profilometer as used for the pre-measurement.
- With the same recipe as used for the pre-mesurement.
- On the same position(s) on the wafer as the pre-measurement.
- Use the program for stress measurement in the profilometer software. Use both the pre-stress measurement and the post-stress measurement.
- The profiler program asks for a substrate elasticity (choose the substrate type, e.g. Si(100)), substrate thickness, film thickness and the name of the pre-stress measurement.
When a thin film is deposited on both sides of the wafer
- Measure the thickness of the wafer
- Deposit the thin film
- Make a pre-stress measurement. Measure the wafer bow on one of the profilometers (Dektak XTA or P17 Stylus profiler). Save the measurement. It is a good idea to measure across most of the wafer (at least along 70% of the wafer length) in two directions perpendicular to each other. Using the P17 profiler you can also measure a radially resolved map of the wafer stress with up to 5° resolution.
- Remove the thin film from one side of the wafer. If it is a single side polished wafer, then remove it on the non-polished side.
- Make a post-stress measurement. Measure the wafer bow again:
- On the same profilometer as used for the pre-measurement.
- With the same recipe as used for the pre-mesurement.
- On the same position(s) on the wafer as the pre-measurement.
- Measure the thickness of the thin film (ex. using the FilmTek or the Ellipsometer).
- Use the program for stress measurement in the profilometer software. Use both the pre-stress measurement and the post-stress measurement.
- The profiler program asks for substrate elasticity (choose the substrate type, e.g. Si(100)), substrate thickness, film thickness and the name of the pre-stress measurement.
Stress measurement using XRD
After you make a θ-2θ scan of a crystalline thin film, the peak positions can be used to calculate the lattice constant of the film. By comparing the calculated lattice constant to the theoretical one, you can calculate the amount of compressive or tensile stress. It is important to align the thin film carefully to the beam height, as you can in the XRD Smartlab. You may use a standard measurement (e.g. of a crystalline Si sample) to be able to take into account the intrinsic peak broadening of the instrument. Use the Ni-filter to remove the Kβ side peaks and if you have enough signal you can also use the monochromator and analyzer crystals to remove the Kα2 contribution.
Nanolab has the SmartLab Studio software and the Malvern Panalytical HighScore software available for quantifying the stress (ask staff for details). There is a good summary of the principles of the strain calculation in the last section of the associated help document for the SmartLab Studio software.
You may be able to measure the relaxed lattice directly rather than comparing to a theoretical lattice, but you would have to be able to release the film and measure it separately (if this means scraping the thin film off your sample mechanically, you could potentially measure it in the XRD Powder, but it would probably be difficult to get enough powder to get a good signal).