Specific Process Knowledge/Thin film deposition/ALD2 (PEALD): Difference between revisions
(5 intermediate revisions by the same user not shown) | |||
Line 1: | Line 1: | ||
'''Feedback to this page''': '''[mailto:labadviser@danchip.dtu.dk?Subject=Feed%20back%20from%20page%20http://labadviser.danchip.dtu.dk/index.php/Specific_Process_Knowledge/Thin_film_deposition/ALD2_(PEALD) click here]''' | '''Feedback to this page''': '''[mailto:labadviser@danchip.dtu.dk?Subject=Feed%20back%20from%20page%20http://labadviser.danchip.dtu.dk/index.php/Specific_Process_Knowledge/Thin_film_deposition/ALD2_(PEALD) click here]''' | ||
''This page is written by DTU Nanolab internal'' | |||
=ALD 2 (PEALD)= | =ALD 2 (PEALD)= | ||
Line 10: | Line 12: | ||
[[image:ALD2.jpg|450x450px|right|thumb|ALD 2 (PEALD). Positioned in cleanroom F-2.]] | [[image:ALD2.jpg|450x450px|right|thumb|ALD 2 (PEALD). Positioned in cleanroom F-2.]] | ||
The ALD 2 (PEALD) is used to deposit very thin and uniform layers of different materials, by use of thermal ALD (Atomic Layer Deposition) or PEALD (Plasma Enhanced ALD). | The ALD 2 (PEALD) is used to deposit very thin and uniform layers of different materials, by use of thermal ALD (Atomic Layer Deposition) or PEALD (Plasma Enhanced ALD). Layers can be up to 100 nm thick, see the table below. | ||
The ALD deposition takes place in an ALD reactor chamber. In order to ensure that the temperature inside this reactor is the same everywhere, it has a dual chamber structure. The inner chamber is the reactor chamber, and the outer chamber is isolating the reactor chamber from room air. Both the inner and the outer chamber are under vacuum. The space between the two chambers is called an intermediate space (IMS), and the IMS is constantly purged with nitrogen. | The ALD deposition takes place in an ALD reactor chamber. In order to ensure that the temperature inside this reactor is the same everywhere, it has a dual chamber structure. The inner chamber is the reactor chamber, and the outer chamber is isolating the reactor chamber from room air. Both the inner and the outer chamber are under vacuum. The space between the two chambers is called an intermediate space (IMS), and the IMS is constantly purged with nitrogen. | ||
Line 46: | Line 48: | ||
[http://labmanager.dtu.dk/function.php?module=Machine&view=view&mach=365 ALD 2 (PEALD) info page in LabManager] | [http://labmanager.dtu.dk/function.php?module=Machine&view=view&mach=365 ALD 2 (PEALD) info page in LabManager] | ||
== Process information == | == Process information == | ||
Line 83: | Line 84: | ||
*Al<sub>2</sub>O<sub>3</sub> - Thermal Al<sub>2</sub>O<sub>3</sub> (mainly backup for ALD1) and Al<sub>2</sub>O<sub>3</sub> using plasma | *Al<sub>2</sub>O<sub>3</sub> - Thermal Al<sub>2</sub>O<sub>3</sub> (mainly backup for ALD1) and Al<sub>2</sub>O<sub>3</sub> using plasma | ||
*TiO<sub>2</sub> (amorphous or anatase) - Thermal TiO<sub>2</sub> (mainly backup for ALD1) and TiO<sub>2</sub> using plasma | *TiO<sub>2</sub> (amorphous or anatase) - Thermal TiO<sub>2</sub> (mainly backup for ALD1) and TiO<sub>2</sub> using plasma | ||
*HfO<sub>2</sub> - Thermal HfO<sub>2</sub> (mainly backup for ALD1) | *HfO<sub>2</sub> - Thermal HfO<sub>2</sub> (mainly backup for ALD1) | ||
*AlN - AlN using plasma | *AlN - AlN using plasma | ||
*TiN - Thermal TiN and TiN using plamsa | *TiN - Thermal TiN and TiN using plamsa | ||
Is is not possible to deposit oxides and nitrides at the same time | *ZnO | ||
*AZO | |||
All precursors might not be available at the same time. | |||
Is is not possible to deposit oxides and nitrides at the same time. | |||
|- | |- | ||
!style="background:silver; color:black" align="center" valign="center" rowspan="2"|Performance | !style="background:silver; color:black" align="center" valign="center" rowspan="2"|Performance | ||
Line 97: | Line 100: | ||
|style="background:LightGrey; color:black"|Thickness | |style="background:LightGrey; color:black"|Thickness | ||
|style="background:WhiteSmoke; color:black"| | |style="background:WhiteSmoke; color:black"| | ||
*Al<sub>2</sub>O<sub>3</sub>, TiO<sub>2</sub>, HfO<sub>2</sub>: | *Oxides: Al<sub>2</sub>O<sub>3</sub>, TiO<sub>2</sub>, HfO<sub>2</sub>, ZnO, AZO: 0-100 nm | ||
*SiO<sub>2</sub>, AlN, TiN: | *Nitrides: SiO<sub>2</sub>, AlN, TiN: 0-100 nm | ||
<i>As the purpose of ALD 2 is to deposit very thin and uniform layers, the allowed deposition thickness is limited to 100 nm, and it is not allowed to do more depositions on the same sample(s) to deposit thicker layers than 100 nm. Deposition of thicker layers is not allowed, because this will occupy the machine for long time and thus make it available for less users. Long depositions also cause issues and with flakes and particles, which means that the chamber and the pump line will have to be cleaned or changed quite often. Furthermore, the delivery time on precursors is usually quite long. So when you make a sample design, you should avoid steps, where you need to deposit thicker layers than 100 nm with ALD, or you can consider, if the same material can be deposited using other machines in the cleanroom.</i> | |||
|- | |- | ||
!style="background:silver; color:black" align="center" valign="center" rowspan="3"|Process parameter | !style="background:silver; color:black" align="center" valign="center" rowspan="3"|Process parameter |
Latest revision as of 14:41, 15 August 2023
Feedback to this page: click here
This page is written by DTU Nanolab internal
ALD 2 (PEALD)
Thermal ALD and PEALD
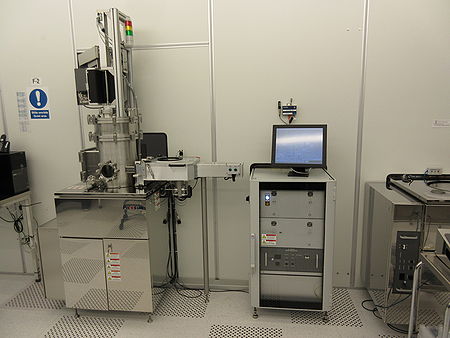
The ALD 2 (PEALD) is used to deposit very thin and uniform layers of different materials, by use of thermal ALD (Atomic Layer Deposition) or PEALD (Plasma Enhanced ALD). Layers can be up to 100 nm thick, see the table below.
The ALD deposition takes place in an ALD reactor chamber. In order to ensure that the temperature inside this reactor is the same everywhere, it has a dual chamber structure. The inner chamber is the reactor chamber, and the outer chamber is isolating the reactor chamber from room air. Both the inner and the outer chamber are under vacuum. The space between the two chambers is called an intermediate space (IMS), and the IMS is constantly purged with nitrogen.
When a sample is loaded into the reactor chamber, it will take some time before it reaches the desired temperature. Thus, it is important to include a temperature stabilization time in the deposition recipes.
The ALD depositions take place under vacuum, thus a vacuum pump is connected to the bottom of the ALD reactor chamber. The pump is located in the basement.
Different precursor lines are connected to the reactor chamber through separate precursor inlets. At the moment the available precursors here are TMA, TiCl4, SAM24, TEMAHf, H2O and NH3, and soon O3 will also be available. These precursor lines are all purged with a constant flow of nitrogen.
The liquid precursor sources TMA, TiCl4 and H2O are stored in bottles located in a side cabinet on the left side of the machine. When the TMA and TiCl4 precursors are not in use, a manual valve on each bottle has to be closed. The powder precursors SAM24 and TEMAHf are stored in bottles located in a big cabinet below the ALD chamber. These precursors are heated by heating jackets, and users should not open and close the manual valves. O3 is generated by use of an ozone generator that is located in the E-rack at the right side of the machine.
A remote plasma generator is connected to the upper part of the reactor chamber. Different precursor gases are connected to this plasma generator through the same gas inlet. At the moment the available plasma precursor gases are N2, O2, NH3 and H2. The plasma gas inlet is constantly purged with argon. The plasma gases can also be used as precursors for thermal ALD if the power to the plasma generator is not turned on. When H2 is being used, the pump line constantly has to be purged with 1.9 SLM nitrogen, and this has to be enabled manually.
The plasma generator is separated from the reactor chamber by a plasma cone (or chamber lid). The argon flow through the plasma gas inlet ensures that the plasma cone remains clean.
The plasma cone is not heated, and thus is will affect the temperature uniformity in the reactor chamber, and it will affect the gas flows and increase the necessary purge time. For that reason it is possible to mount a thermal lid between the plasma cone and the reactor chamber. However, it is quite time consuming to install the thermal lid as it requires that the machine is cooled to room temperature and vented. Furthermore, it is not possible to run plasma processes with the thermal lid installed.
The precursor pulse time is controlled by special ALD valves that allow very short precursor pulses to be introduced into the ALD reactor chamber and at the same time allow a constant nitrogen or argon flow. Thus, nitrogen and argon are always flowing through the ALD valves into the chamber, independent on whether a precursor pulse is introduced or not.
At the moment it is possible to deposit Al2O3, TiO2, HfO2, SiO2, AlN and TiN in the ALD. In order to deposit good quality nitride layers with low sheet resistance, the amount of oxygen has to be very low. Thus, the ALD reactor chamber has to be passivated for about three days, before nitride depositions can be done, and oxides and nitrides cannot be deposited at same time.
Samples are loaded through a load lock. 6" and 8" wafers can be loaded directly in the load lock, while 4" wafers and smaller samples have to be placed on a 6" carrier plate or a 6" silicon dummy wafer with an etched recess. It is only possible to load one wafer or carrier plate at a time by use of the load lock.
The plasma cone is opened and closed, when samples are transferred between the load lock and the reactor chamber. Two buttons on the load lock are used to insert and retract the load lock arm from the reactor chamber. A window on the front side of the machine makes it possible to keep an eye on the reactor chamber and the sample during loading and unloading.
It is also possible to load a minibatch directly holder into ALD through a door on the left side of the reactor chamber. However, a training is needed in order to use the minibatch holder, and for nitride depositions the minibatch holder cannot be used as it requires that the machine is vented, and thus a possible nitride passivation will be ruined. Furthermore, the minibatch holder is not useful for plasma process, as the ALD material will only be deposited on the top sample.
The ALD is controlled by use of a computer with a touch screen that is situated next to the machine.
The ALD 2 (PEALD) is a Picosun R-200 Advanced Plasma ALD manufactured by Picosun, and it was installed in the cleanroom in 2016.
The user manual, the user APV and contact information can be found in LabManager:
ALD 2 (PEALD) info page in LabManager
Process information
Standard recipes on ALD 2 (PEALD):
Available processes:
Equipment | ALD 2 (PEALD) | |
---|---|---|
Purpose | Thermal ALD or PEALD deposition |
All precursors might not be available at the same time. Is is not possible to deposit oxides and nitrides at the same time. |
Performance | Deposition rates |
Depending on the deposited materials and temperature. More information can be found on the pages under "Process information" |
Thickness |
As the purpose of ALD 2 is to deposit very thin and uniform layers, the allowed deposition thickness is limited to 100 nm, and it is not allowed to do more depositions on the same sample(s) to deposit thicker layers than 100 nm. Deposition of thicker layers is not allowed, because this will occupy the machine for long time and thus make it available for less users. Long depositions also cause issues and with flakes and particles, which means that the chamber and the pump line will have to be cleaned or changed quite often. Furthermore, the delivery time on precursors is usually quite long. So when you make a sample design, you should avoid steps, where you need to deposit thicker layers than 100 nm with ALD, or you can consider, if the same material can be deposited using other machines in the cleanroom. | |
Process parameter | Deposition temperature |
Maximum 500 oC |
Thermal precursors |
| |
Plasma precursors |
| |
Substrates | Batch size |
|
Allowed materials |
|