Specific Process Knowledge/Thermal Process/Resist Pyrolysis Furnace: Difference between revisions
No edit summary |
No edit summary |
||
(18 intermediate revisions by 2 users not shown) | |||
Line 1: | Line 1: | ||
'''Feedback to this page''': '''[mailto:thinfilm@danchip.dtu.dk?Subject=Feed%20back%20from%20page%20http://labadviser.danchip.dtu.dk/index.php/Specific_Process_Knowledge/Thermal_Process/Resist_Pyrolysis_Furnace click here]''' | |||
''This page is written by DTU Nanolab internal'' | |||
===<span style="color:Red">EXPIRED! | |||
The Resist Pyrolysis furnace has been removed from the cleanroom August 2019. Use the Multipurpose Anneal furnace instead.</span>=== | |||
[[Category: Equipment |Thermal Resist Pyrolysis]] | |||
[[Category: Thermal process|Resist Pyrolysis]] | |||
[[Category: Furnaces|Resist Pyrolysis]] | |||
== Resist Pyrolysis Furnace == | == Resist Pyrolysis Furnace == | ||
[[image:Resist_Pyrolysis_Furnace.jpg|500x500px|right|thumb|The Resist Pyrolysis furnace located in cleanroom area A-5]] | |||
The Resist Pyrolysis Furnace is used for resist pyrolysis, where samples with different resist layers are heated up to maximum 1000 <sup>o</sup>C in a nitrogen atmosphere. At high temperatures carbon is formed by pyrolysis of the resist. In this way conductive structures can be made from a resist patterned sample. | The Resist Pyrolysis Furnace is used for resist pyrolysis, where samples with different resist layers are heated up to maximum 1000 <sup>o</sup>C in a nitrogen atmosphere. At high temperatures carbon is formed by pyrolysis of the resist. In this way conductive structures can be made from a resist patterned sample. | ||
Line 8: | Line 19: | ||
If oxygen from the air or from outgassing of the resist is present in the furnace, the resist layer will be removed. Thus, for each process it is important to include a step with a high nitrogen flow at a lower temperature, before a high temperature for resist pyrolysis is obtained. Pyrolysis of a large amount of resist may also be a problem due to resist outgassing. | If oxygen from the air or from outgassing of the resist is present in the furnace, the resist layer will be removed. Thus, for each process it is important to include a step with a high nitrogen flow at a lower temperature, before a high temperature for resist pyrolysis is obtained. Pyrolysis of a large amount of resist may also be a problem due to resist outgassing. | ||
During processing the furnace is rapidly heated by use of six long heating lamps situated around the furnace tube, and | During processing the furnace is rapidly heated by use of six long heating lamps situated around the furnace tube. The furnace is not heated in the ends, and this affects the temperature uniformity in the furnace. Cooling is done (rather slowly) by use of cooling fans. | ||
The furnace is purged with a controlable nitrogen flow. | |||
There is no vacuum on the furnace. | |||
'''The user manual, user APV and contact information can be found in LabManager:''' | |||
[http://www.labmanager.danchip.dtu.dk/function.php?module=Machine&view=view&mach=294 Resist Pyrolysis Furnace] | [http://www.labmanager.danchip.dtu.dk/function.php?module=Machine&view=view&mach=294 Resist Pyrolysis Furnace] | ||
Line 19: | Line 33: | ||
There are no standard processes on the furnace. | There are no standard processes on the furnace. | ||
==Equipment performance and process related parameters== | ==Equipment performance and process related parameters== | ||
Line 27: | Line 39: | ||
!colspan="2" border="none" style="background:silver; color:black;" align="center"|Equipment | !colspan="2" border="none" style="background:silver; color:black;" align="center"|Equipment | ||
|style="background:WhiteSmoke; color:black"|<b> | |style="background:WhiteSmoke; color:black"|<b>Reist Pyrolysis Furnace</b> | ||
|- | |- | ||
!style="background:silver; color:black;" align="center"|Purpose | !style="background:silver; color:black;" align="center"|Purpose | ||
Line 34: | Line 46: | ||
*Pyrolysis of different resist layers to form conductive structures | *Pyrolysis of different resist layers to form conductive structures | ||
|- | |- | ||
!style="background:silver; color:black" align="center" valign="center" rowspan=" | !style="background:silver; color:black" align="center" valign="center" rowspan="4"|Process parameter range | ||
|style="background:LightGrey; color:black"|Temperature | |style="background:LightGrey; color:black"|Temperature | ||
|style="background:WhiteSmoke; color:black"| | |style="background:WhiteSmoke; color:black"| | ||
* | *Max 1000 <sup>o</sup>C | ||
*Temperature ramp-up rate: Max 10<sup>o</sup>C/min | *Temperature ramp-up rate: Max 10 <sup>o</sup>C/min | ||
*Temperature ramp-down rate: Relative slow (depending on the furnace temperature) | *Temperature ramp-down rate: Relative slow (depending on the furnace temperature) | ||
|- | |||
|style="background:LightGrey; color:black"|Process gasses | |||
|style="background:WhiteSmoke; color:black"| | |||
*N<sub>2</sub> | |||
|- | |||
|style="background:LightGrey; color:black"|Vacuum | |||
|style="background:WhiteSmoke; color:black"| | |||
*No | |||
|- | |- | ||
|style="background:LightGrey; color:black"|Nitrogen flows | |style="background:LightGrey; color:black"|Nitrogen flows | ||
Line 49: | Line 69: | ||
|style="background:LightGrey; color:black"|Batch size | |style="background:LightGrey; color:black"|Batch size | ||
|style="background:WhiteSmoke; color:black"| | |style="background:WhiteSmoke; color:black"| | ||
* | *1-4 50 mm wafers (placed on Si carrier wafers) | ||
* | *1-5 100 mm wafers (place on Si carrier wafers or in a horizontal wafer boat) | ||
* | *Several smaller samples if these are placed on a support wafer | ||
|- | |- | ||
| style="background:LightGrey; color:black"|Allowed materials | | style="background:LightGrey; color:black"|Allowed materials | ||
Line 62: | Line 82: | ||
*AZ resist (prebaked) | *AZ resist (prebaked) | ||
*SU-8 (prebaked) | *SU-8 (prebaked) | ||
*Other resist - Permission required | |||
|- | |- | ||
|} | |} |
Latest revision as of 14:08, 6 February 2023
Feedback to this page: click here
This page is written by DTU Nanolab internal
===EXPIRED! The Resist Pyrolysis furnace has been removed from the cleanroom August 2019. Use the Multipurpose Anneal furnace instead.===
Resist Pyrolysis Furnace
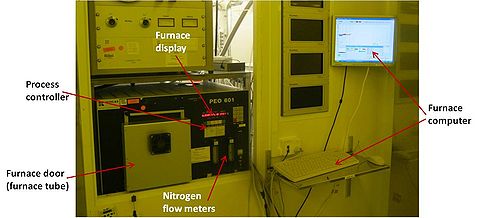
The Resist Pyrolysis Furnace is used for resist pyrolysis, where samples with different resist layers are heated up to maximum 1000 oC in a nitrogen atmosphere. At high temperatures carbon is formed by pyrolysis of the resist. In this way conductive structures can be made from a resist patterned sample.
If oxygen from the air or from outgassing of the resist is present in the furnace, the resist layer will be removed. Thus, for each process it is important to include a step with a high nitrogen flow at a lower temperature, before a high temperature for resist pyrolysis is obtained. Pyrolysis of a large amount of resist may also be a problem due to resist outgassing.
During processing the furnace is rapidly heated by use of six long heating lamps situated around the furnace tube. The furnace is not heated in the ends, and this affects the temperature uniformity in the furnace. Cooling is done (rather slowly) by use of cooling fans.
The furnace is purged with a controlable nitrogen flow.
There is no vacuum on the furnace.
The user manual, user APV and contact information can be found in LabManager:
Process information
There are no standard processes on the furnace.
Equipment | Reist Pyrolysis Furnace | |
---|---|---|
Purpose |
| |
Process parameter range | Temperature |
|
Process gasses |
| |
Vacuum |
| |
Nitrogen flows |
| |
Substrates | Batch size |
|
Allowed materials |
|