Specific Process Knowledge/Thin film deposition/Deposition of Alumina: Difference between revisions
Jump to navigation
Jump to search
THIS PAGE IS UNDER CONSTRUCTION
Line 11: | Line 11: | ||
*[[Specific Process Knowledge/Thin film deposition/Multisource PVD|Cryofox PVD co-sputter/evaporation]] | *[[Specific Process Knowledge/Thin film deposition/Multisource PVD|Cryofox PVD co-sputter/evaporation]] | ||
==Comparison of the methods for deposition of | ==Comparison of the methods for deposition of Alumium Oxide== | ||
{|border="1" cellspacing="1" cellpadding="3" style="text-align:left;" | {|border="1" cellspacing="1" cellpadding="3" style="text-align:left;" | ||
|- | |- |
Revision as of 11:14, 7 September 2015
THIS PAGE IS UNDER CONSTRUCTION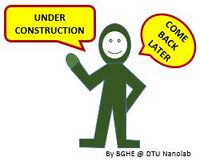
Feedback to this page: click here
Deposition of aluminium oxide
Aluminium oxide (Alumina, Al2O3 ) can be deposited by use of ALD (atomic layer deposition) or by a sputter technique in the Lesker Sputter System or the Cryofox PVD co-sputter/evaporation. During the sputter deposition oxygen is added to the chamber resulting in aluminium oxide on the sample
Comparison of the methods for deposition of Alumium Oxide
Sputter technique using IBE/IBSD Ionfab300 | Sputter System Lesker | III-V Dielectric evaporator | ALD Picosun 200 | |
---|---|---|---|---|
Generel description |
|
|
|
|
Stoichiometry |
|
|
|
|
Film Thickness |
|
|
|
|
Deposition rate |
|
|
|
|
Step coverage |
|
|
|
|
Process Temperature |
|
|
|
|
More info on TiO2 |
|
|
||
Substrate size |
|
|
|
|
Allowed materials |
|
|
|