Specific Process Knowledge/Thin film deposition/Deposition of Aluminium/Thermal deposition of Al
Feedback to this page: click here
All text on this page by DTU Nanolab staff
Thermal evaporation of Aluminum
Aluminum can be thermally evaporated in the Thermal Evaporator and the Wordentec. At DTU Nanolab, we recommend to use a thin layer of thermally evaporated aluminum on top of e-beam resist before the e-beam exposure. For deposition onto the unexposed e-beam resist, you need to use the thermal source.
Using the Thermal Evaporator
The Thermal Evaporator (Lesker) is easy to use and the quickest option if you only have a few samples or several small samples. It is also better suited for depositing rather thick layers, since you can add more material and the material use is more efficient than in the Wordentec. However, the deposited thickness will vary more across a large wafer than in the Wordentec because the throw distance is shorter (4-14 % variation across a 4" wafer for the Thermal Evaporator versus 3-6 % variation across a 4" wafer with the Wordentec).
See a few more details comparing the instruments including particle count and uniformity on 6" wafers here: File:thermal evap wtec vs lesker nano uniformity and particles.pdf
Notice that since this measurement was made we have implemented rotation in the machine, so it may be better now (June 2023).
As usual, you need a training session before using the instrument independently.
To deposit Al
- Vent the chamber (3 min)
- Load your sample(s) and add Al pellets to the crucible as necessary (you need approx. 1 pellet per 45 nm, note that there may also be some Al left in the crucible)
- Pump down (10 min)
- Run the process (soaking/ramping 7 minutes plus time for your deposition and about 1 minute for running down the power afterwards). The deposition rate is 1 Å/s.
For Al-deposition, you must activate source no. 1 and choose a process starting with "Al1". Follow the directions in the manual.
Quality control (QC) of Al evaporation on the thermal evaporator
Quality control (QC) for the Thermal evaporator | ||||||||||||||||||
Thicknesses are measured in 5 points with one of the stylus profilers. |
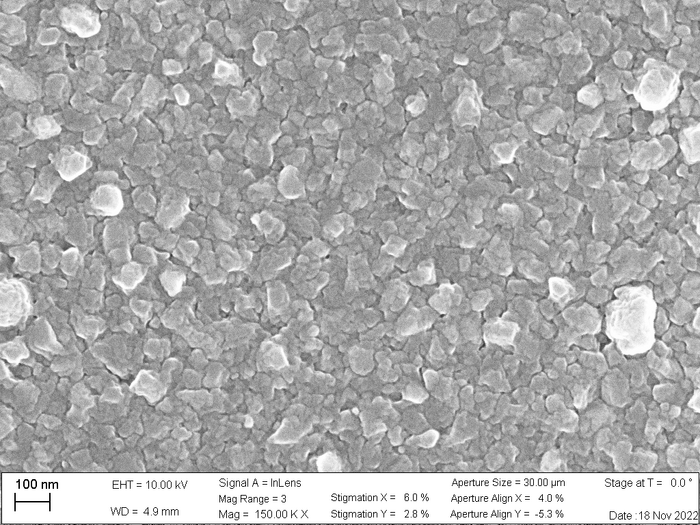
Using the Wordentec
The Wordentec is useful if you need to deposit a thin layer on more than three wafers: You can load up to six 6" wafers at a time, but you can only add 8 pellets at a time, which in the Wordentec gives a total of approx. 150 nm (or 20 nm per wafer on six wafers, as extra material is used up for each soaking step). The pumping time for the Wordentec is at least 1 hour, which means that this is much slower than the Thermal Evaporator unless you are depositing on many wafers.
Use process 9 in Wordentec to deposit thermal Aluminum. Follow the manual.
Observe that you need to get a special training to use the thermal deposition source.
Set-up
- Two "boats" of Tantalum are mounted (on top of each other) in the thermal source each time.
- We have also earlier seen that two boats give stable depositions, since the lower boat gets hot (and heat the top boat), even if there if a thick layer of aluminum all over the top boat.
- If the last deposition from the source was Aluminum, the same boats can be used, otherwise they should be changed.
- "Small" Al pellets (diameter 1/8", height 1/8") are used. Use these small pellets to get a more uniform deposition with stable deposition rate.
- The boat should be placed as horizontal as possible, so the Aluminum metal will be evenly distributed in the boat after it is melted. If it is a problem to mount the boats horizontal, contact equipment responsible persons.
Program settings
- The deposition rate is normally 1 or 2 Å/s.
The settings saved in the material file for thermal aluminum are these:
- Soak power 1: 5%
- Soak power 2: 7%
These are already saved in the process recipe.
Notes
This files contains some short notes regarding thermal Al evaporation: Short Tests thermal deposition of Al in Wordentec
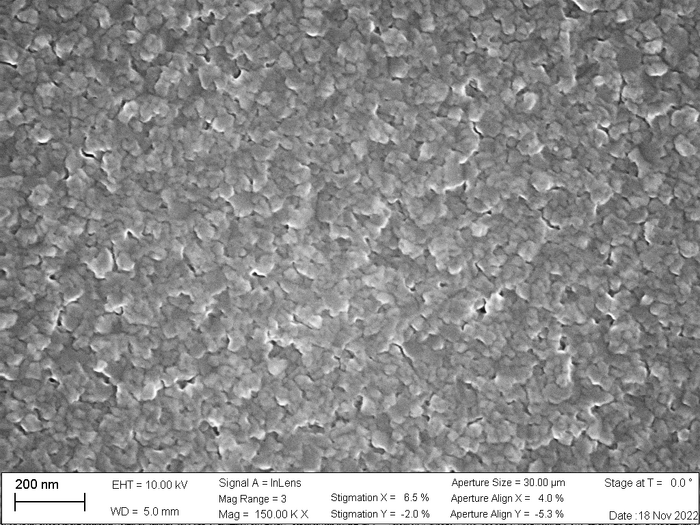