Specific Process Knowledge/Direct Structure Definition
Feedback to this page: click here
THIS PAGE IS UNDER CONSTRUCTION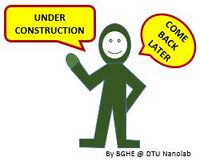
Direct Structure Definiton
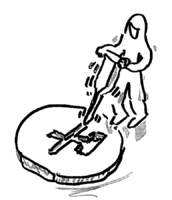
By direct structure definition we mean that you form the structures for you device directly in the material that the device consist of without any masking steps. Some of the techniques may require a master.
Choose method of structuring/equipment
- UV Lithography
- 2-Photon Polymerization Lithography
- Nano Imprint Lithography
- Polymer Injection Molder
- Laser Micromachining Tool/ablation
- Dicing saw
Comparison of equipment/material
UV Lithography | 2-Photon Polymerization Lithography | Nano Imprint Lithography | Polymer Injection Molder | Laser Micromachining Tool | Dicing saw | |
---|---|---|---|---|---|---|
General description | The device is typical made in a thick film (10-100µm thick) of a polymer (SU-8) that is spun on a carrier (silicon wafer). This film is exposed through a mask and then developed and possible cured to make the polymer harder. | The device is typical made in a thick film (1-10µm thick) of a polymer (SU-8) that is spun on a carrier (silicon wafer). This film is exposed by two intersecting laser beams in the system. Where the beams intersect the film polymerize and becomes less solvable. It is possible to form very small 3D structures | The device is typical made in a thick film (1-10µm thick) of a polymer that is spun on a carrier (silicon wafer). A master with the desired pattern is pressed into this film and the film is hardened by heating or UV-exposure. A residual layer has to be etched away by dry etching. It is possible to form very small 2½D structures over large areas relative fast. | The device is typical made in TOPAS or a similar polymer/plastic. A master disk of e.g. Nickel, called a shim, with the desired pattern is mounted in the tool of the machine and they form together a void where the melted plastic is injected into. It is possible to form small and large 2½D structures on the chosen shape (determined by the tool) relative fast. As an example Lego building blocks are made by polymer injection molding. | The device is made using a series of short, high intensity light pulses to engrave a pattern in almost any material. Since the light pulses are very short (100ns or 10ps) the heating of the sample can be minimized, and material can be removed without any further sample deformation/melting. | The dicing saw is mostly used to seperate a silicon/glass wafer into individual chips. It can however also be used to make straight channels in glass/fused silica for e.g. fluidic components. |
Typical used for | Optical waveguides, fluidic systems (master for PDMS/soft lithography) | Photonic bandgap structures | 3 | Fluidic devices, optical waveguides, surface modification. | Cutting Silicon and glass wafers in odd shapes, shim cutting, shim patterning, surface modification, hole drilling in glass/silicon etc. | Cutting Silicon and glass wafers in rectangular shapes, making straight channels in glass wafers. |
Processable materials |
|
|
|
|
|
|
Prerequisites | 1 | 2 | 3 | 4 | 5 | 6 |
Pattern generation | 1 | 2 | 3 | 4 | 5 | 6 |
Throughput | 1 | 2 | 3 | 4 | 5 | 6 |
Min/max featuresize | 1 | 2 | 3 | 4 | 5 | 6 |
Min/max aspect-ratio | 1 | 2 | 3 | 4 | 5 | 6 |
Post-treatment | 1 | 2 | 3 | 4 | 5 | 6 |
Patterning degree of freedom | 1 | 2 | 3 | 4 | 5 | 6 |
Sample sizes |
|
|
|
flat disk tool: , luer tool: |
|
|
Allowed materials | 1 | 2 | 3 | 4 | 5 | 6 |