Specific Process Knowledge/Lithography/CSAR
Resist | Polarity | Manufacturer | Comments | Technical reports | Spinner | Developer | Rinse | Remover | Process flows (in docx-format) |
CSAR | Positive | AllResist | Standard positive resist, very similar to ZEP520. | Allresist_CSAR62_English.pdf,, CSAR_62_Abstract_Allresist.pdf | Manual Spinner 1 (Laurell), Spin Coater Labspin | X AR 600-54/6, MIBK:IPA | IPA, H2O | 1165 Remover | Process_Flow_CSAR.docx |
Simple e-beam pattern in this resist has been tested, the results showed on this page. If you have questions to the process or wish to use this e-beam resist, please contact Tine Greibe at tigre@danchip.dtu.dk.
Process Flow
Test of Chemically Semi-Amplified Resist (CSAR); a positive e-beam resist from AllResist (AR-P 6200-2).
Equipment | Process Parameters | Comments | |
---|---|---|---|
Pretreatment | |||
4" Si wafers | No Pretreatment | ||
Spin Coat | |||
Spin Coater Manual, LabSpin, A-5 | AR-P 6200/2 AllResist E-beam resist
60 sec at various spin speed. Acceleration 4000 s-2, softbake 1 - 5 min at 150 deg Celcius |
Disposal pipette used; clean by N2-gun before use. Use approximately 1.5 ml per 4" wafer, never use a pipette twice. Softbake is not a crucial step, see e-mail correspondence with AllResist here. | |
Characterization | |||
Ellipsometer VASE B-1 | 9 points measured on 100 mm wafer | ZEP program used; measured at 70 deg only | |
E-beam Exposure | |||
JEOL 9500 E-beam writer, E-1 | Dosepattern 15nm - 100nm,
dose 120-280 muC/cm2 |
Virtual chip mark height detection (CHIPAL V1) used in corner of every dose array | |
Development | |||
Fumehood, D-3 | 60 sec in X AR 600-54/6,
60 sec rinse in IPA, N2 Blow dry |
Gentle agitation while developing. After developing, wafer is immersed in beaker with IPA, subsequently blow dried with N2 gun. | |
Characterization | |||
Zeiss SEM Supra 60VP, D-3 | 2-3 kV, shortest working distance possible, chip mounted with Al tape | The wafers are diced into smaller pieces and sputter coated with Pt at DTU CEN before SEM inspection; please contact Ramona Valentina Mateiu for further information. |
Spin Curves
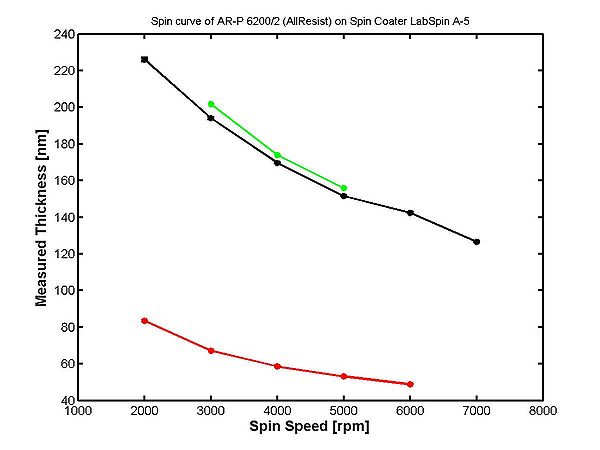
The thickness is measured on VASE Ellipsometer using a simple Cauchy model for a transparent polymer on Si. The measurements are performed at one incidence angle (70 degrees) only. 9 points on each 4" wafer has been measured; the standard deviation thus representing the homogeinity of the film on the 4" wafers.
Dosepattern has been e-beam exposured and SEM inspected on those wafers marked by silver gray.
AllResist AR-P 6200/2 spinning on Spin Coater: Manual LabSpin A-5, TIGRE, 09-04-2014. Softbake 5 min @ 150 degC. | ||||||
---|---|---|---|---|---|---|
Spin Speed [rpm] | Acceleration [1/s2] | Thickness [nm] | St Dev | |||
2000 | 4000 | 225.98 | 0.97 | |||
3000 | 4000 | 194.00 | 0.6 | |||
4000 | 4000 | 169.57 | 0.32 | |||
5000 | 4000 | 151.47 | 0.26 | |||
6000 | 4000 | 142.38 | 0.41 | |||
7000 | 4000 | 126.59 | 0.36 |
AllResist CSAR on Spin Coater: Manual LabSpin A-5, TIGRE, 16-06-2014. Softbake 2 min @ 150 degC. | ||||||
---|---|---|---|---|---|---|
Spin Speed [rpm] | Acceleration [1/s2] | Thickness [nm] | St Dev | |||
3000 | 4000 | 201.61 | 1.20 | |||
4000 | 4000 | 173.89 | 0.64 | |||
5000 | 4000 | 155.91 | 0.65 |
AllResist CSAR 1:1 in anisole, Spin Coater: Manual LabSpin A-5, TIGRE, 16-06-2014. Softbake 2 min @ 150 degC. | ||||||
---|---|---|---|---|---|---|
Spin Speed [rpm] | Acceleration [1/s2] | Thickness [nm] | St Dev | |||
2000 | 4000 | 83.48 | 0.49 | |||
3000 | 4000 | 67.12 | 0.41 | |||
4000 | 4000 | 58.64 | 0.44 | |||
5000 | 4000 | 53.13 | 0.39 | |||
6000 | 4000 | 48.76 | 0.38 |
SEM pictures of dosepatterns
wafer 6.13
Process | Equipment | Parameters | Date and initials |
---|---|---|---|
Resist | Fumehood D-3 | AR-P 6200/2 AllResist E-beam resist diluted 1:1 in anisole | TIGRE |
Spin Coat | Spin Coater LabSpin A-5 | 1 min @ X000 rpm, 2000 1/s2, softbake X min @ 150 degC, thickness ~XXnm | TIGRE |
E-beam exposure | JEOL 9500 E-2 | 0.2 nA, aperture 5, dose 180-420 muC/cm2, Shot pitch 7-27 nm | TIGRE |
Develop | Fumehood D-3 | SX-AR 600-54/6 60 sec, 30 sec IPA rinse | TIGRE |
Sputter Coat | Cressington 208HR, DTU CEN | 3-5 nm Pt, sputtering | TIGRE |
Characterization | Zeiss SEM Supra 60VP, D-3 | 3 kV, WD below 4mm, conducting tape close to pattern | TIGRE |
Wafer 6.13, 100 nm exposed pattern, shot pitch 7 nm | |||||||
---|---|---|---|---|---|---|---|
300 [muC/cm2] | ![]() |
![]() |
![]() |
![]() |
![]() |
![]() |
ACHK NOT READY |
Wafer 6.13, 50 nm exposed pattern, shot pitch 7 nm | ||||||
---|---|---|---|---|---|---|
270 [muC/cm2] | ![]() |
![]() |
![]() |
![]() |
![]() |
ACHK NOT READY |
300 [muC/cm2] | ![]() |
![]() |
![]() |
![]() |
![]() |
ACHK NOT READY |
Wafer 6.13, 30 nm exposed pattern, shot pitch 7 nm | |||||
---|---|---|---|---|---|
240 [muC/cm2] | ![]() |
![]() |
ACHK NOT READY | ||
270 [muC/cm2] | ![]() |
![]() |
![]() |
![]() |
ACHK NOT READY |
300 [muC/cm2] | ![]() |
![]() |
![]() |
![]() |
ACHK NOT READY |
53 nm CSAR
The e-beam exposures presented here are written with 'SHOT A,10', i.e. a shot pitch of 5nm; this pitch works very well for large structures but not so well for 20nm or below. To illustrate this, ACHK screenshot are presented along with SEM inspection picures.
Process | Equipment | Parameters | Date and initials |
---|---|---|---|
Resist | Fumehood D-3 | AR-P 6200/2 AllResist E-beam resist diluted 1:1 in anisole | 16-06-2014 TIGRE |
Spin Coat | Spin Coater LabSpin A-5 | 1 min @ 5000 rpm, 4000 1/s2, softbake 2 min @ 150 degC, thickness ~53nm | 16-06-2014 TIGRE |
E-beam exposure | JEOL 9500 E-2 | 0.2 nA, aperture 5, dose 207-242 muC/cm2, SHOT A,10 | 02-07-2014 TIGRE |
Develop | Fumehood D-3 | SX-AR 600-54/6 60 sec, 60 sec IPA rinse | 08-07-2014 TIGRE |
Sputter Coat | Cressington 208HR, DTU CEN | 3-5 nm Pt, sputtering | 09-07-2014 TIGRE |
Characterization | Zeiss SEM Supra 60VP, D-3 | 3 kV, WD below 4mm, conducting tape close to pattern | 09-07-2014, TIGRE |
50nm
dose [muC/cm2] | 230 | 230 | 230 | 230 | 230 |
---|---|---|---|---|---|
![]() |
![]() |
![]() |
![]() |
![]() |
30nm
dose [muC/cm2] | 219 | 230 | 242 | ACHK |
---|---|---|---|---|
![]() |
![]() |
![]() |
||
![]() |
![]() |
![]() |
![]() |
20nm
dose [muC/cm2] | 207 | 219 | 230 | 242 | 253 | ACHK |
---|---|---|---|---|---|---|
![]() |
![]() |
![]() |
![]() |
![]() |
||
![]() |
![]() |
![]() |
![]() |
15nm
dose [muC/cm2] | 242 | 253 | 276 | ACHK |
---|---|---|---|---|
![]() |
![]() |
![]() |
||
![]() |
![]() |
![]() |
![]() |
140 nm CSAR
Process | Equipment | Parameters | Date and initials |
---|---|---|---|
Resist | Fumehood D-3 | AR-P 6200/2 AllResist E-beam resist | 2013 (bottle opened) |
Spin Coat | Spin Coater LabSpin A-5 | 1 min @ 6000 rpm, 4000 1/s2, softbake 5 min @ 150 degC, thickness ~143nm | 09-04-2014 TIGRE |
E-beam exposure | JEOL 9500 E-2 | 2 nA, aperture 5, dose 207-242 muC/cm2, SHOT A,10 | 10-04-2014 TIGRE |
Develop | Fumehood D-3 | SX-AR 600-54/6 60 sec, 60 sec IPA rinse | April/May-2014 TIGRE |
Sputter Coat | Cressington 208HR, DTU CEN | 2-3 nm Pt, sputtering | 22-05-2014 TIGRE |
Characterization | Zeiss SEM Supra 60VP, D-3 | 2 kV, WD below 4mm, conducting tape close to pattern | 06-06-2014, TIGRE |
50nm
dose [muC/cm2] | 207 | 219 | 230 | 242 |
---|---|---|---|---|
![]() |
![]() |
![]() |
![]() | |
![]() |
![]() |
![]() |
![]() |
30nm
dose [muC/cm2] | 207 | 219 | 230 | 242 |
---|---|---|---|---|
![]() |
![]() |
![]() |
![]() | |
![]() |
![]() |
![]() |
![]() |
20nm
dose [muC/cm2] | 230 | 242 | 253 |
---|---|---|---|
![]() |
![]() |
![]() |