Specific Process Knowledge/Lithography/Pretreatment
Feedback to this page: click here
Pretreatment
All surfaces can be divided to hydrophilic or hydrophobic surfaces, where the oxidized surfaces such SiO2 or surface with native oxide formation on Si or Al substrates consider to be hydrophilic and have very bad wetting with hydrophobic resist.
Therefore it is very important to do the pretreatment step before the spinning. Here we will give an overview of treatments available at Danchip to promote photoresist adhesion.
Comparing pretreatment methods
HMDS | Buffered HF-Clean | Oven 250C | |
---|---|---|---|
Generel description |
Vapor priming |
Oxide strip |
Dehydration |
Chemical |
hexamethyldisilazane (HMDS) |
12%HF with Ammoniumflouride |
none |
Etch rate range |
|
|
|
Substrate size |
|
|
|
Allowed materials |
hmds |
|
|
Restrictions | None | Wafers with metal is not allowed | Resist is not allowed |
HMDS
Feedback to this section: click here
The chemical treatment with hexamethyldisilazane (HMDS) before the spin coating can be used to promote the adhesion for photoresist. HMDS treatment leaves a mono-layer of TMS (trimethylsilyl) on the Si or SiO2 surface.
The molecular formula for hexamethyldisilazane, or bis(trimethylsilyl)amine, is C6H19NSi2. Here is a schematic overview of HMDS treatment of silicon-oxide surface.
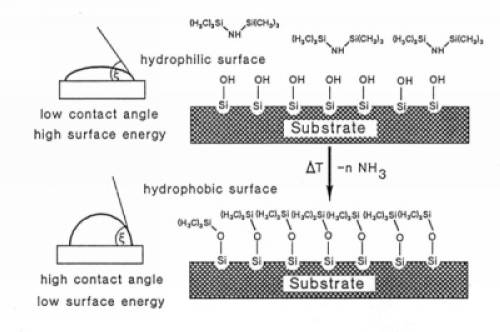
Comparing HMDS priming
Equipment | HMDS oven | Spin Track 1 + 2 | |
---|---|---|---|
Purpose |
|
| |
Priming chemical |
hexamethyldisilizane (HMDS) | ||
Performance | Contact angle |
standard recipe 82° (on SiO2) |
60° - 90°; standard recipe 82° (on SiO2) |
Process parameters | Process temperature |
150°C |
50°C |
Process time |
32.5 minutes |
3 min / wafer | |
Substrates | Substrate size |
|
100 mm wafers |
Allowed materials |
All cleanroom materials |
Silicon (with oxide, nitride, or metal films or patterning) Glass (borosilicate and quartz) | |
Batch |
1 - 25, multiple batches possible |
1 - 25 |
HMDS oven
At Danchip we use Star2000 model from IMTEC to do vapor deposition of hexamethyldisilizane (HMDS) under the special conditions: low pressure and high chamber temperature. The result of the dehydration bake and HMDS prime is that the wafers become hydrophobic after the treatment.
The user manual, user APV, and contact information can be found in LabManager:
Process information
- Recipe 4: baseline prime process with 5 min priming time
Baseline prime process description:
1. Vacuum, 2 min
2. Nitrogen pump, 3.5 min
3. Heat- up, 10 min
4. Vacuum, 4.5 min
5. HMDS prime, 5 min
6. Vacuum chamber exhaust, 3 min
7. Nitrogen back-fill, 3.5 min
Purpose |
Promotion of photoresist adhesion by hydrophobization | ||
---|---|---|---|
Chemical |
hexamethyldisilizane | ||
Performance | Contact angle |
82° (on SiO2) | |
Process parameters | Process temperature |
150 °C | |
Process time |
32.5 minutes | ||
Substrates | Substrate size |
| |
Allowed materials |
All cleanroom materials | ||
Batch |
1 - 25, multiple batches possible |
Buffered HF-Clean
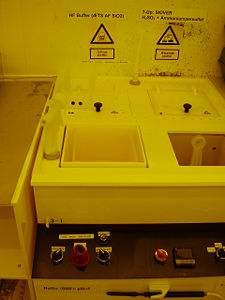
Another commonly used method to render the surface of silicon wafers hydrophobic is the dilute HF dip.
BHF is mostly used to do pretreatment step for new Si wafers. The native dioxide layer will be removed during 30 sec etching and in this way we will promote the resist adhesion on the Si substrates. We recommend to spin resist asap after the procedure.
Oven 250C
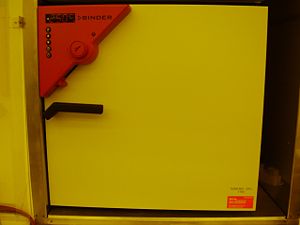
The oven is typically used for pretreatment (dehydration) of Si and glass substrates to promote the resist adhesion. We recommend to place the wafers in metal carrier in the oven at least for 4 hours, better during the night, and spin the resist on them asap.