Specific Process Knowledge/Lithography/DUVStepperLithography
SÜSS Spinner-Stepper
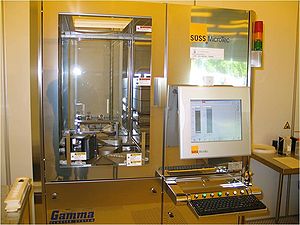
This spinner is dedicated for spinning DUV resists. The spinner is fully automatic and can run up to 25 substrates in a batch 4", 6", and 8" size. The machine is equipped with the 3 resist lines, an automatic syringe system and a solvent line for cleaning and back-side rinse.
The user manual(s), quality control procedure(s) and results and contact information can be found in LabManager: Equipment info in LabManager
Process information
The users are not allowed to use the spinner. In case you would like to do DUV lithography please contact Lithography team, who will consult your and run your wafers for you.
Information about resist can be found here:
- Bottom Anti Reflection Coating (BARC)DUV 42S-6 .
- Datasheet DUV42S-6.
- Positive DUV resist for spinning in 300-600nm thickness range KRF M230Y.
- Positive DUV resist for spinning in 1600-800nm thickness range KRF M35G.
- Negative DUV resist for spinning in 1400-800nm or diluted with EC Solvent in 1:1 in 400-200nm thickness range UVN2300-0.8.
DUV Stepper FPA-3000EX4 from Canon
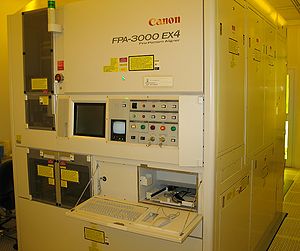
The FPA-3000EX4 is an advanced exposure system designed for mass-production of 6 and 8 inch large wafers/ devices. The largest applicable thickness of the wafers/ devices is 1,2 mm. Also 4" wafers/ devices can be processed with some restrictions concerning throughput, resolution, uniformity and maximum allowed wafer thickness. The system is equipped with a KrF Excimer laser from Cymer (wavelength 248 nm) leading to a specified resolution of 250 nm that is improved when well-defined pattern designs are used. The best resolution could be achieved with single line structures (line widths down to 160 nm) and multi-line structures (line widths down to 180 nm).
The user manual(s), quality control procedure(s) and results and contact information can be found in LabManager:
Equipment info in LabManager
Process information
1) A DUV reticle is needed that should be designed by the customer. Please note that the projection magnification of the stepper is 1:5, so that the dimensions of the pattern on the reticle are expanded by a factor 5 with respect to those printed on the wafer.
The whole reticle can be regarded as one chip that might be printed one time onto the wafer or repeatedly - step-by-step - in a two dimensional array. Alternatively, different chips can be placed onto the reticle, separated by frames. These chips can be printed individually onto the wafer either as one chip or as an array. Then the individual chips of the design have to be surrounded by frames. Additionally, the pattern of two different reticles can be combined on one wafer.
If the pattern of the reticle should be aligned to another one - that is already located on the wafer - the wafer needs to be equipped with several alignment marks. A guide for preparing reticle files for the Canon FPA-3000EX4 stepper, having the correct dimensions and positions of the individual patterns, frames and alignment marks can be found here: File:Canon Stepper Reticle Guide v0 03.pdf.
Usually the reticle is fabricated by an external company. It is recommended to send the mask design in GDS format to the Photolith group of Danchip, so that they can verify the mask design and order the mask.
2) The SÜSS Spinner-Stepper is dedicated for spinning DUV resists. Please note that a Bottom Anti-Reflective Coating (BARC) is necessary to guarantee high quality of both the resist film and the exposure. Please find the specification of the SÜSS Spinner-Stepper in the LabAdviser [[1]].
3) Usually, in order to guarantee the highest fidelity of the produced pattern on the wafer the best suitable exposure dose has to be evaluated for each individual pattern, resist type and resist thickness. Thus it is recommended to perform an exposure dose test as a first test, when a new reticle is used. After evaluation by SEM the identified dose - that leads to the most accurate pattern - can be applied in the DUV process for the required wafers.
4) The DUV process - including BARC and resist spinning, exposure, post exposure bake and development - will be performed by the Photolith group of Danchip. Any kind of inspection, evaluation and pre- and post-processing should be performed by the customer.
Overview of performance
Magnification | 1 : 5 |
NA | 0,6 |
Sigma | 0,65 (usual illumination mode) |
Illumination Intensity | 2800 W/m2 |
Illumination uniformity | 1,2 % |
Wavelength | 248 nm |
Chip size | 22 x 26 mm (maximum on wafer) |
Allignment accuracy | 3 sigma = 50 nm |