Specific Process Knowledge/Etch/Wet Silicon Oxide Etch (BHF)
Feedback to this page: click here
Wet Silicon Oxide Etch (BHF and SIO Etch (wetting agent))
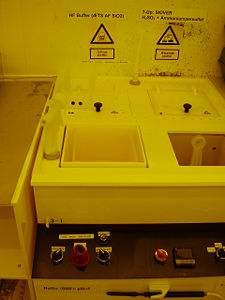
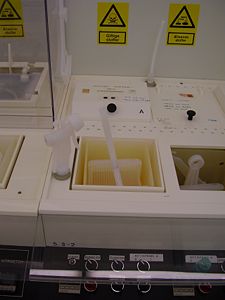
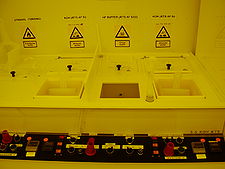
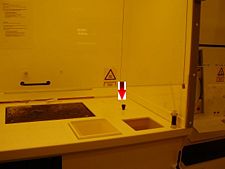
Silicon oxide can be etched using HF. At Danchip it is mainly used in a buffered version BHF (premixed). The BHF has a more stable etch rate and is more gentle to photoresist due to an almost pH neutral solution which makes photoresist a good masking material for the oxide etch.
SIO etch (BHF with wetting agent) can also be used for etching silicon oxide. This is mainly for etching small holes. If you have wetting problems in BHF try the SIO etch. It is also a good idea to wet the sample in water for a few minutes before etching.
Wafers with metals or other materials, not allowed in the dedicated oxide etch baths, can be etched in the PP-bath positioned in the fume hood in cleanroom 2 or in a plastic beaker.
Silicon oxide etch data
BHF | 5% HF | 40 % HF | SIO | |
---|---|---|---|---|
General description |
Etching of silicon oxide with a stable etch rate |
Mainly for removing native oxide |
Mainly for etching deep into borofloat or quartz wafers |
Etching of silicon oxide - especially for etching small holes |
Link to safety APV and KBA | see APV here | see APV here | see APV here | see APV here |
Chemical solution | BHF | 5% HF | 40% HF | BHF with wetting agent |
Process temperature | Room temperature | Room temperature | Room temperature | Room temperature |
Possible masking materials |
In RCA bench:
|
In plastic beaker or PP-bath in the fume hood in cleanroom 2:
In RCA bench:
|
In plastic beaker with magnetic stirrer in the fume hood in cleanroom 2:
|
|
Etch rate |
|
|
|
A little higher etch rates than BHF |
Life time of the photoresist | ~½ hour | ~½ hour | ~½ hour | ~½ hour |
Batch size |
Plastic beaker:
PP-bath:
BHF-bath in cleanroom 3:
BHF-bath in cleanroom 4:
BHF-bath in RCA bench:
|
Plastic beaker:
PP-bath:
HF-bath in RCA bench:
|
1-7 wafer of 4" at a time |
1-25 wafer of 4" at a time |
Size of substrate |
4"-6" wafers |
2"-6" wafers |
4" wafers |
4" wafers |
Allowed materials |
In plastic beaker or PP-bath in the fume hood in cleanroom 2:
BHF-bath in cleanroom 3:
BHF-bath in the RCA bench:
|
In plastic beaker or PP-bath in the fume hood in cleanroom 2:
HF-bath in RCA bench:
|
In plastic beaker in the fume hood in cleanroom 2:
|
|
Life time of the photoresist and blue film in BHF
Photoresist delaminates from the substrate in BHF. For standard photoresist this process starts after about or less than ½ hour but the time can vary with resist pattern. It starts by under etching the photoresist at the edges. The life time can be prolonged a little to ½ hour - 40 minutes if the photoresist is baked at 120oC.
Blue film also has a limited life time in BHF. Blue film is mainly used for back side protecting the wafer while etching on the front side. The life time of Blue film is also about ½ hour.