Specific Process Knowledge/Etch/KOH Etch
KOH etch - Anisotropic silicon etch
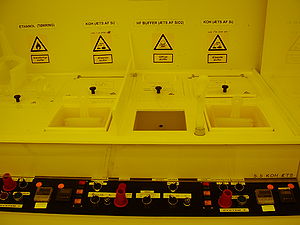
KOH belongs to the family of anisotropic Si-etchants based on aqueous alkaline solutions. The anisotropy stems from the different etch rates in different crystal directions. The {111}-planes are almost inert whereas the etch rates of e.g. {100}- and {110}-planes are several orders of magnitude faster.
KOH-etching is a highly versatile and cheap way to realize micro mechanical structures if you can live with the necessary SiN- or SiO-masking materials and the potassium contamination of the surface. The latter necessitates in most cases a wet post-clean ('7-up' or RCA-clean) if the wafer is to be processed further.
At Danchip we use as a standard a 28 wt% KOH. The etch rate - and the selectivity towards a SiO-mask - is depending on the temperature. We normally use T=80 oC but may choose to reduce this to e.g. 60 oC or 70 oC in case of a high-precision timed etch (e.g. defining a thin membrane). In some cases we recommend to saturate the standard 28 wt% KOH with IPA with an etch temperature at T=70 oC (reduce evaporation of IPA). One example is for boron etch-stop, where the selectivity towards the boron-doped silicon is improved compared to the standard etch. Key facts for the two solutions are resumed in the table:
KOH solutions
28 wt% KOH | 28 wt% KOH sat. with IPA | |
---|---|---|
General description |
|
|
Chemical solution |
|
|
Process temperature |
|
|
Possible masking materials |
|
|
Etch rate in Si |
|
|
Etch rate in SiO |
|
. |
Roughness |
|
|
Batch size |
|
|
Size of substrate |
|
|
Allowed materials |
|
|
Definition of structures
Due to the almost inert (111)-planes it is possible by KOH etching to realize high aspect ratio structures in sigle crytalline silicon using the (111)-planes as sidewalls. In Si(100) these sidewalls are inclined - 54.7o with respect to the (100) surface - whereas in Si(110) the sidewalls are vertical (see figures below).
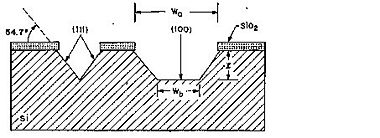
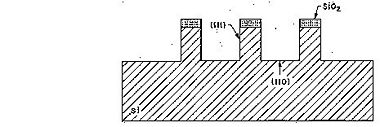
For Si(100), the relation between the width of the bottom of the etched groove (Wb) and the width of the opening (Wo) at the wafer surface in a groove etched to the depth l is given by:
Definition of <110> alignment structures
The etch rate dependence on the crystallographic planes can be used to determine the <110> crystal directions with high precision (better than +/- 0.05 o). A fast method for doing this, using the symmetric under-etching behavior around but not at the <110>-directions, was described by Vangbo and Bäcklund in J. Micromech. Microeng.6 (1996), 279-284. High-precision control of the <110>-direction during alignment can be necessary in order to control the dimensions of KOH-etched structures (e.g. precise control of V-groove dimensions). A dedicated mask (MASK NAME) has been designed for this purpose.
Etch rates: Empirical formula (Seidl et al)
The following empirical formula can be used for concentrations in the range of 10-60 wt%:
R = k0 [H2O]4 [KOH]0.25 e-Ea/kT,
where k0 = 2480 µm/hr (mol/l)-4.25, Ea = 0.595 eV for Si(100)
and k0 = 4500 µm/hr (mol/l)-4.25, Ea = 0.60 eV for Si(110)