Specific Process Knowledge/Thin film deposition/Furnace LPCVD PolySilicon: Difference between revisions
Line 42: | Line 42: | ||
*Amorphous polySi: 0-1000 nm | *Amorphous polySi: 0-1000 nm | ||
*Boron doped polySi: 0-1000 nm | *Boron doped polySi: 0-1000 nm | ||
4" furnace | 4" furnace: | ||
*Standard polySi: 0-2000 nm | *Standard polySi: 0-2000 nm | ||
*Amorphous polySi: 0-2000 nm | *Amorphous polySi: 0-2000 nm | ||
*Boron doped polySi: 0-2000 nm | *Boron doped polySi: 0-2000 nm | ||
*Phosphorus doped polySi: 0-1000 nm | *Phosphorus doped polySi: 0-1000 nm | ||
Thicker layers have to be deposited over more runs | |||
|- | |- | ||
|style="background:LightGrey; color:black"|Step coverage | |style="background:LightGrey; color:black"|Step coverage | ||
Line 52: | Line 53: | ||
*Good | *Good | ||
|- | |- | ||
|style="background:LightGrey; color:black"| | |style="background:LightGrey; color:black"|Film quality | ||
|style="background:WhiteSmoke; color:black"| | |style="background:WhiteSmoke; color:black"| | ||
*Good | *Deposition on both sides of the substrate | ||
*Good uniformity over the wafer | |||
|- | |- | ||
!style="background:silver; color:black" align="left" valign="top" rowspan="3"|Process parameter range | !style="background:silver; color:black" align="left" valign="top" rowspan="3"|Process parameter range | ||
Line 63: | Line 65: | ||
*Amorphous polySi: 560-580 <sup>o</sup>C | *Amorphous polySi: 560-580 <sup>o</sup>C | ||
*Boron doped polySi: 600-620 <sup>o</sup>C | *Boron doped polySi: 600-620 <sup>o</sup>C | ||
4" furnace: | 4" furnace: | ||
*Standard polySi: 620 <sup>o</sup>C | *Standard polySi: 620 <sup>o</sup>C | ||
Line 69: | Line 70: | ||
*Boron doped polySi: 620 <sup>o</sup>C | *Boron doped polySi: 620 <sup>o</sup>C | ||
*Phosphorus doped polySi: 620 <sup>o</sup>C | *Phosphorus doped polySi: 620 <sup>o</sup>C | ||
The process temperature | The process temperature vary over the furnace tube | ||
|- | |- | ||
|style="background:LightGrey; color:black"|Process pressure | |style="background:LightGrey; color:black"|Process pressure | ||
|style="background:WhiteSmoke; color:black"| | |style="background:WhiteSmoke; color:black"| | ||
*150-250 mTorr | 6" furnace: | ||
*150-220 mTorr | |||
4" furnace: | |||
*250 mTorr | |||
The process pressure depends on the actual process | The process pressure depends on the actual process | ||
|- | |- | ||
Line 81: | Line 85: | ||
*SiH<math>_4</math>: 50-70 sccm | *SiH<math>_4</math>: 50-70 sccm | ||
*BCl<math>_1</math>: 1 sccm | *BCl<math>_1</math>: 1 sccm | ||
4" furnace: | 4" furnace: | ||
*SiH<math>_4</math>: 80 sccm | *SiH<math>_4</math>: 80 sccm | ||
*B<math>_2</math>H<math>_6</math>: 7 sccm | *B<math>_2</math>H<math>_6</math>: 7 sccm | ||
*PH<math>_1</math>: 7 sccm | *PH<math>_1</math>: 7 sccm | ||
The silane (SiH<math>_4</math>) flow depends on the actual process | |||
|- | |- | ||
!style="background:silver; color:black" align="left" valign="top" rowspan="2"|Substrates | !style="background:silver; color:black" align="left" valign="top" rowspan="2"|Substrates | ||
Line 92: | Line 96: | ||
6" furnace: | 6" furnace: | ||
*1-25 4" wafers or 6" wafers per run | *1-25 4" wafers or 6" wafers per run | ||
4" furnace: | |||
*1-30 4" wafers per run | *1-30 4" wafers per run | ||
Deposition on both sides of the substrate | Deposition on both sides of the substrate | ||
Line 97: | Line 102: | ||
| style="background:LightGrey; color:black"|Substrate materials allowed | | style="background:LightGrey; color:black"|Substrate materials allowed | ||
|style="background:WhiteSmoke; color:black"| | |style="background:WhiteSmoke; color:black"| | ||
*Silicon wafers ( | *Silicon wafers (only clean wafers): | ||
**with layers of silicon oxide or silicon (oxy)nitride | **with layers of silicon oxide or silicon (oxy)nitride (RCA cleaned) | ||
**from furnaces in stack A or B in cleanroom 2 | |||
*Quartz wafers (RCA cleaned) | *Quartz wafers (RCA cleaned) | ||
|- | |- | ||
|} | |} |
Revision as of 10:56, 24 July 2012
This page has not been made yet - the information is not correct!!
LPCVD (Low Pressure Chemical Vapor Deposition) PolySilicon
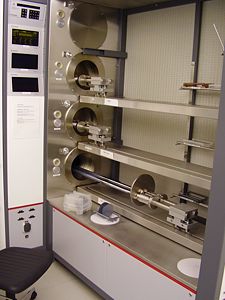
Danchip has two furnaces for deposition of LPCVD polysilicon: A new 6" furnace (installed in 2011) for deposition of standard polySi, amorphous polySi and boron doped polySi on 4" or 6" wafers and an older 4" furnace (installed in 1995) for deposition of standard polySi, amorphous polySi, boron- and phosphorous doped polySi on 4" wafers. In LabManager the two furnaces are named "Furnace: LPCVD Poly-Si" and "Furnace: LPCVD Poly-Silicon 6inch", respectively. Both furnaces are Tempress horizontal furnaces.
The LPCVD polysilicon deposition is a batch process, where polySi is deposited on a batch of 25 or 50 wafers (6" polySi furnace) or 30 wafers (4" polySi furnace). The polySi has a good step coverage, and especially for standard polySi the film thickness is very uniform over the wafers.
The reactive gas is silane (SiH4). The dopant for boron doped polySi is BCl3 (6" polySi furnace) or B2H6 (4" polySi furnace), and for phosphorous doped polySi the dopant is PH3. For standard polysilion the deposition takes place at a temperature of 620oC and a pressure of 200-250 MTorr. For amorphous polysilicon the deposition temperatures and thus the deposition rate are lower, and for boron and phosphorous doped polySi the deposition temperature is 600oC - 620oC depending on whether you use the 6" or the 4" polySi furnace. For phousphorous doped polySi the deposition rate is approximately ten times lower than for boron doped polySi. More process information about the process parameters can be found in the table below.
To get information on how to operate the furnaces please read the user manuals which are uploaded to the machine pages in LabManager or consult the Furnace group at Danchip (furnace@danchip.dtu.dk).
Process Knowledge
Please take a look at the process side for deposition of Silicon Nitride using LPCVD:
Deposition of Silicon Nitride using LPCVD
Purpose | Deposition of LPCVD polysilicon |
6" furnace:
4" furnace:
|
---|---|---|
Performance | Film thickness |
6" furnace:
4" furnace:
Thicker layers have to be deposited over more runs |
Step coverage |
| |
Film quality |
| |
Process parameter range | Process Temperature |
6" furnace:
4" furnace:
The process temperature vary over the furnace tube |
Process pressure |
6" furnace:
4" furnace:
The process pressure depends on the actual process | |
Gas flows |
6" furnace:
4" furnace:
The silane (SiH) flow depends on the actual process | |
Substrates | Batch size |
6" furnace:
4" furnace:
Deposition on both sides of the substrate |
Substrate materials allowed |
|