Specific Process Knowledge/Lithography/Baking: Difference between revisions
Line 225: | Line 225: | ||
<div align="left"> | <div align="left"> | ||
<gallery widths=" | <gallery widths="320px" heights="240px"> | ||
File:Benchtop C1.jpg|Benchtop hotplate located in C-1 | File:Benchtop C1.jpg|Benchtop hotplate located in C-1 | ||
File: | File:Labspin_2.JPG|Benchtop hotplates next to spin coater in E-5 | ||
</gallery> | </gallery> | ||
</div> | </div> |
Revision as of 14:47, 19 March 2020
Feedback to this page: click here
Comparing baking methods
Hotplate: 90-110C | Hotplate 1, 2, 3 and 4 (SU8) | Small benchtop hotplates | Gamma hotplates | Oven 90C | Oven: 110C - 250C | Oven 250C | |
---|---|---|---|---|---|---|---|
Purpose |
Programmable, contact bake
|
Programmable, ramped contact bake
|
Adjustable temperature, contact bake
|
Recipe dependent temperature, contact or proximity bake
|
Manual convection bake
|
Manual convection bake
|
Manual convection bake
|
Temperature |
Maximum 120°C |
Maximum 110°C |
Maximum temperature is hotplate dependent |
Fixed at various recipe dependent temperatures. |
Fixed at 90°C |
110 - 250°C Return to 110°C after use |
Fixed at 250°C |
Substrate size |
|
|
|
|
|
|
|
Allowed materials |
All substrates Film or pattern of all types |
Silicon, glass, and polymer substrates Film or pattern of all types except type IV |
Hotplate dependent. (All substrates and film or pattern of all types, unless otherwise noted on the hotplate) |
Silicon and glass substrates |
Silicon, glass, and polymer substrates Film or pattern of all types |
Silicon, glass, and high Tg polymer substrates Film or pattern of all types |
Silicon, glass, and high Tg polymer substrates Film or pattern of all types except resist| |
Restrictions (Not allowed) |
III-V, copper, steel substrates
Pb, Te films |
Hotplate dependent. Any restrictions will be noted on the hotplate. |
III-V, copper, steel substrates | III-V, low Tg polymer, copper, steel substrates | III-V, low Tg polymer, copper, steel substrates
Resist is not allowed | ||
QC |
https://labmanager.dtu.dk/view_binary.php?type=data&mach=336 |
Hotplate 1: Hotplate 2: Hotplate 3: Hotplate 4: |
Spincoater: Gamma UV: Developer: TMAH UV-lithography: Spincoater: Süss stepper: Developer: Stepper:
|
Hotplates
Feedback to this section: click here
Hotplate: 90-110C
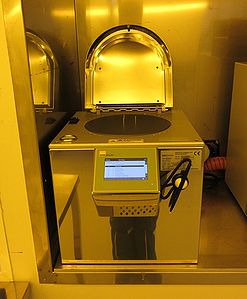
Hotplate: 90-110C is used for baking of 2" - 6" wafers. Do not exceed 120°C.
The user manual, and contact information can be found in LabManager: Hotplate: 90-110C
Hotplate 1 (SU8), Hotplate 2 (SU8), Hoplate 3(SU8) and Hotplate 4(SU8)
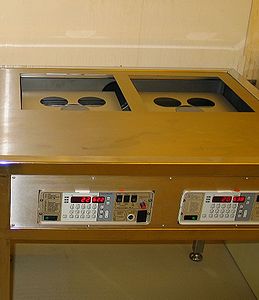
We have four dedicated SU-8 hotplates in C-1.
Users can control the ramp-time, the baking temperature, and the baking time. In order to avoid thermal curing of SU-8 residues on the hotplates, they are temperature limited to 110°C.
The user manual, and contact information can be found in LabManager: Hotplate 1 (SU8) Hotplate 2 (SU8) Hotplate 3 (SU8) Hotplate 4 (SU8)
Small benchtop hotplates
Model: Präzitherm PZ 28-2.
Contact bake only. Maximum temperature is hotplate dependent.
Most of these hotplates have been fitted with a top-plate in order to protect the original hotplate surface. With the top-plate, the set point of the controller must be adjusted in order to achieve the correct temperature during the bake:
Actual surface temperature = 0.9 * display value
Gamma hotplates

Hotplate temperatures are recipe dependent.
Information about the Süss MicroTec Gamma tools can be found in labadviser:
- Spin Coater: Süss Stepper
- Developer: TMAH Stepper
- Developer TMAH UV-lithography
- Spin Coater: Gamma UV
- Spin Coater: Gamma e-beam & UV
Ovens
Feedback to this section: click here
Oven 90C

The oven is mostly used for baking of several wafers at a time at 90 °C as a soft baking step after a spin coating of photoresist. For 1.5µm resist the baking time is 30 min. For most of the other resist thicknesses it is also 30 min.
The user manual, and contact information can be found in LabManager: Oven 90C
Oven: 110C - 250C
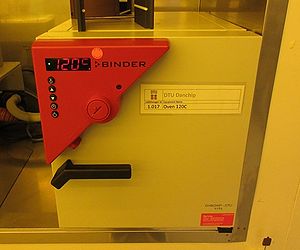
Variable temperature convection oven mostly used for baking of wafers as a hard baking step after development of photoresist.
The set-point can be varied, but should always be returned to 110°C after use.
The user manual, and contact information can be found in LabManager: Oven: 110C - 250C
Oven 250C for pretreatment
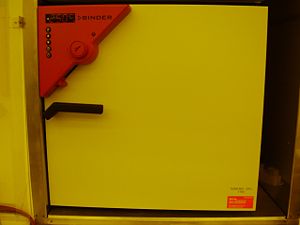
See Oven 250C