Specific Process Knowledge/Back-end processing/Polymer Injection Molder/Demolding: Difference between revisions
Created page with "== Demolding == Demolding is the process of opening the mold and thereby pulling the sample off the shim. Many of the previously mentioned parameter will influence the demold..." |
|||
Line 1: | Line 1: | ||
== Demolding == | == Demolding == | ||
Demolding is the process of opening the mold and thereby pulling the sample off the shim. Many of the previously mentioned parameter will influence the demolding process. Generally, the higher mold temperature, faster injection speed and higher | Demolding is the process of opening the mold and thereby pulling the sample off the shim. Many of the previously mentioned parameter will influence the demolding process. Generally, the higher the mold temperature, faster injection speed and higher switchover/after pressure, the more difficult it can be to demold the sample. | ||
The | The demolding settings are can be found on the 'Mold open' screen: | ||
[[File:06-demold.png|600px|thumb|left|Parameters for opening the mold is found on the 'Mold Open' screen.]] | [[File:06-demold.png|600px|thumb|left|Parameters for opening the mold is found on the 'Mold Open' screen.]] | ||
<br><br> | |||
*''' | *'''Opening profile''': Dosing speed is adjusted by pressing the left (green) ''''='''' sign and entering a value. Alternatively the up/down arrow can be used or the points of the green graph may be edited directly. It is recommended not to increase the speed above ~0,34 m/s. For sensitive polymers it may be necessary to lower the speed. | ||
*''' | *'''Mold stroke position''': The back pressure is adjusted by pressing the right (red) ''''='''' sign and entering a value, using the arrows or editing the red curve points directly. During dosing the only thing that moves the screw backwards is polymer entering the cylinder and thus pushing the screw backwards. A back pressure is used to "press against" this motion. The higher the back pressure the harder 'kneading' of the polymer. Again, some sensitive polymers might require reduced back pressures to avoid thermal damage (decomposition) of the polymer. It is usually sufficient to keep the back pressure at 120 bars or below, but in some cases (e.g. when using pigments) a higher back pressure can give better mixing of pigment and polymer. But be aware of the risks involved regarding decomposition of the polymer. | ||
*''' | *'''Sequence settings''': This is the setpoint for the amount of polymer that is loaded into the heating cylinder. Note that this number is '''in no way''' linked to the amount of polymer injected into the mold cavity. This is defined on the "Switchover" screen mentioned earlier. | ||
Revision as of 09:38, 8 February 2018
Demolding
Demolding is the process of opening the mold and thereby pulling the sample off the shim. Many of the previously mentioned parameter will influence the demolding process. Generally, the higher the mold temperature, faster injection speed and higher switchover/after pressure, the more difficult it can be to demold the sample.
The demolding settings are can be found on the 'Mold open' screen:
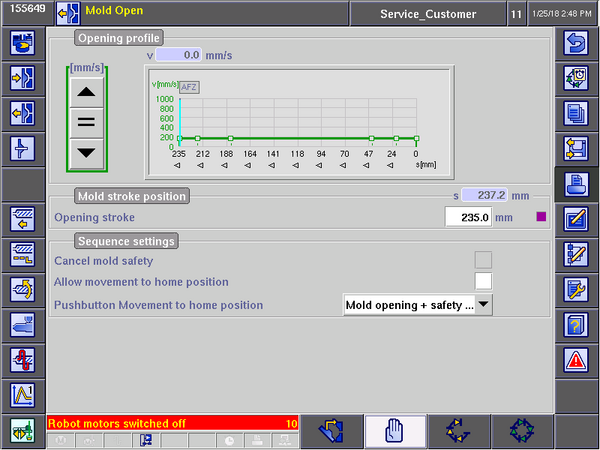
- Opening profile: Dosing speed is adjusted by pressing the left (green) '=' sign and entering a value. Alternatively the up/down arrow can be used or the points of the green graph may be edited directly. It is recommended not to increase the speed above ~0,34 m/s. For sensitive polymers it may be necessary to lower the speed.
- Mold stroke position: The back pressure is adjusted by pressing the right (red) '=' sign and entering a value, using the arrows or editing the red curve points directly. During dosing the only thing that moves the screw backwards is polymer entering the cylinder and thus pushing the screw backwards. A back pressure is used to "press against" this motion. The higher the back pressure the harder 'kneading' of the polymer. Again, some sensitive polymers might require reduced back pressures to avoid thermal damage (decomposition) of the polymer. It is usually sufficient to keep the back pressure at 120 bars or below, but in some cases (e.g. when using pigments) a higher back pressure can give better mixing of pigment and polymer. But be aware of the risks involved regarding decomposition of the polymer.
- Sequence settings: This is the setpoint for the amount of polymer that is loaded into the heating cylinder. Note that this number is in no way linked to the amount of polymer injected into the mold cavity. This is defined on the "Switchover" screen mentioned earlier.