Specific Process Knowledge/Back-end processing/Polymer Injection Molder/Dosing: Difference between revisions
Line 9: | Line 9: | ||
*'''Dosing speed''': Dosing speed is adjusted by pressing the left (green) '=' sign and entering a value. Alternatively the up/down arrow can be used or the points of the green graph may be edited directly. It is recommended not to increase the speed above ~0,34 m/s. For sensitive polymers it may be necessary to lower the speed. | *'''Dosing speed''': Dosing speed is adjusted by pressing the left (green) '=' sign and entering a value. Alternatively the up/down arrow can be used or the points of the green graph may be edited directly. It is recommended not to increase the speed above ~0,34 m/s. For sensitive polymers it may be necessary to lower the speed. | ||
*'''Back pressure''': The back pressure is adjusted by pressing the right (red) '=' sign and entering a value, using the arrows or editing the red curve points directly. During dosing the only thing that moves the screw backwards is polymer entering the cylinder and thus pressing the screw backwards. A back pressure is used to "press against" this motion. The higher the back pressure the harder 'kneading' of the polymer. Again, some sensitive polymers might require reduced back pressures to avoid thermal damage (decomposition) of the polymer. | *'''Back pressure''': The back pressure is adjusted by pressing the right (red) '=' sign and entering a value, using the arrows or editing the red curve points directly. During dosing the only thing that moves the screw backwards is polymer entering the cylinder and thus pressing the screw backwards. A back pressure is used to "press against" this motion. The higher the back pressure the harder 'kneading' of the polymer. Again, some sensitive polymers might require reduced back pressures to avoid thermal damage (decomposition) of the polymer. | ||
*''' | *'''Plasticizing time monitoring''': It is recommended to always keep this enabled (it '''must''' remain enabled if leaving the machine unattended) to make sure the machine stops in case of errors. Usually the maximum plasticizing time is set around 4-8 times the actual plasticizing time (which can be seen in the light blue field just above the setpoint after each shot). | ||
*''' | *'''Decompression''': To avoid problems with stress in the polymer melt it can be a good idea to enable decompression. A setpoint of 1 cm<sup>3</sup> work well for most cases. This means that after plasticizing the screw moves a little backwards to provide space for the polymer melt to relax. This is particularly beneficial when running at high back pressure. |
Revision as of 14:30, 6 February 2018
Dosing (Plasticizing)
Plasticizing is the process of dosing polymer pellets into the heating cylinder and press it forwards to melt and circulate (knead) the polymer melt inside the heating cylinder. A major part of the heat required to melt the polymer originates from friction energy during this kneading process. Some polymers are very sensitive to heat and thus most be dosed/plasticized gently to avoid decomposition. If samples turn out yellowish or brown it is likely to be caused to too harsh plasticizing settings. The problem can therefor often be solved by decreasing dosing speed and/or back pressure.
The dosing/plasticizing settings are found on the 'Plasticizing' screen:
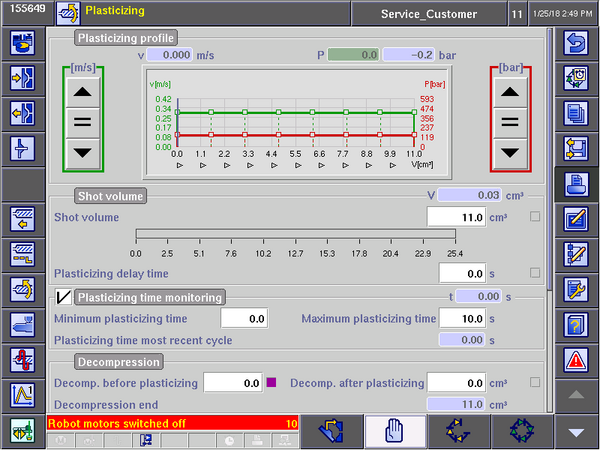
- Dosing speed: Dosing speed is adjusted by pressing the left (green) '=' sign and entering a value. Alternatively the up/down arrow can be used or the points of the green graph may be edited directly. It is recommended not to increase the speed above ~0,34 m/s. For sensitive polymers it may be necessary to lower the speed.
- Back pressure: The back pressure is adjusted by pressing the right (red) '=' sign and entering a value, using the arrows or editing the red curve points directly. During dosing the only thing that moves the screw backwards is polymer entering the cylinder and thus pressing the screw backwards. A back pressure is used to "press against" this motion. The higher the back pressure the harder 'kneading' of the polymer. Again, some sensitive polymers might require reduced back pressures to avoid thermal damage (decomposition) of the polymer.
- Plasticizing time monitoring: It is recommended to always keep this enabled (it must remain enabled if leaving the machine unattended) to make sure the machine stops in case of errors. Usually the maximum plasticizing time is set around 4-8 times the actual plasticizing time (which can be seen in the light blue field just above the setpoint after each shot).
- Decompression: To avoid problems with stress in the polymer melt it can be a good idea to enable decompression. A setpoint of 1 cm3 work well for most cases. This means that after plasticizing the screw moves a little backwards to provide space for the polymer melt to relax. This is particularly beneficial when running at high back pressure.