Specific Process Knowledge/Lithography/Coaters/Spin Coater: Gamma UV processing: Difference between revisions
Line 196: | Line 196: | ||
|} | |} | ||
Spin coating of standard thicknesses (1.3 - 2.5 µm) of AZ MiR 701 (29cps) on Spin Coater: Gamma UV is divided into two or three steps: HMDS priming (optional), spin coating, and soft baking. The HMDS priming is equal to the ''HMDS fast'' process. Spin coating uses dynamic dispense of resist at 800 rpm, using a volume of 3 ml for 100mm substrates. The dispense is followed by spin-off at a thickness dependent spin speed for 30 seconds. The wafer is decelerated at 1000 rpm/s before stopping. Soft baking is done at 90°C for 60s. As MiR 701 has a tendency to produce "cotton candy" on the edges, soft baking is performed in 1 mm proximity. | <br>Spin coating of standard thicknesses (1.3 - 2.5 µm) of AZ MiR 701 (29cps) on Spin Coater: Gamma UV is divided into two or three steps: HMDS priming (optional), spin coating, and soft baking. The HMDS priming is equal to the ''HMDS fast'' process. Spin coating uses dynamic dispense of resist at 800 rpm, using a volume of 3 ml for 100mm substrates. The dispense is followed by spin-off at a thickness dependent spin speed for 30 seconds. The wafer is decelerated at 1000 rpm/s before stopping. Soft baking is done at 90°C for 60s. As MiR 701 has a tendency to produce "cotton candy" on the edges, soft baking is performed in 1 mm proximity. | ||
''Flow names, process parameters, and test results:'' | ''Flow names, process parameters, and test results:'' |
Revision as of 14:13, 20 May 2015
Feedback to this page: click here
THIS PAGE IS UNDER CONSTRUCTION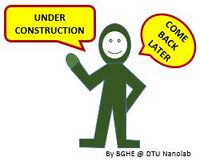
General Process Information
Processing using Spin Coater: Gamma UV is divided into three parts:
- HMDS priming
- Spin coating
- Soft baking
Features of Spin Coater: Gamma UV:
- Cassette-to-cassette wafer handling
- In-line HMDS priming
HMDS priming
The process of HMDS priming on Spin Coater: Gamma UV consists of five steps:
- Dehydration
- HMDS filling
- Reaction
- Purging
- Cooling
UPDATE: The wafer is first baked in contact with the hotplate in order to heat the wafer to the hotplate temperature. The hotplates of the priming modules are set to 50°C. Then the wafer is baked under a low vacuum (~0.5 bar) in order to dehydrate the wafer before HMDS application. The HMDS is applied to the wafer using nitrogen as a carrier gas. 15 liters per minute of dry nitrogen is bubbled through liquid HMDS before flowing across the wafer surface. After the priming, the chamber is pump-purged twice, using a 7s pump to ~0.5 bar and a 10s nitrogen purge at 40 liters per minute. Finally, the wafer is cooled on the priming module coolplate.
The contact angle after HMDS priming is a function of the priming temperature, the priming time, and the surface condition of the wafer. Tests have shown the contact angle to decrease with increasing hotplate temperature, while it increases as a function of priming time at constant temperature. At a priming temperature of 50°C, the contact angle resulting from priming an oxidized silicon wafer for t = 30 - 300s may be approximated by
The condition of the substrate surface is again a function of the substrate type, the substrate history, and the vacuum baking temperature and time. Since the vapor pressure of water at 50°C (0.123 bar) is lower than the vacuum bake pressure of 0.5 bar, the degree of dehydration will be a function of the vacuum baking time. Thus, for thick oxides, the standard of 30s vacuum bake may not be enough to dehydrate the surface sufficiently.
Spin coating
The process of spin coating on Spin Track 1 + 2 consists of a selection of the following steps:
- Acceleration to a low spin speed if dynamic dispense is used
- Resist dispense
- Resist spreading at low spin speed
- Spin-off
- Deceleration before stop or further process steps
- Edge-bead removal using PGMEA
- Backside rinse using PGMEA
The wafer is first centered on the spindle chuck and held in place by vacuum. If static dispense is specified in the process, the spindle remains static during the ensuing resist dispense. In the case of dynamic dispense, the spindle is accelerated to a low spin speed before the resist is dispensed. Using too high spin speed during dispense can cause surface wetting issues, while a too low spin speed causes the resist to flow onto the backside of the wafer. The resist is dispensed through the dispense arm, positioned over the center of the wafer. The resist pump administers a fixed volume of resist (4 ml), but multiple dispenses may be used. After dispense, a short spin at low spin speed may be used in order to spread the resist over the wafer surface before spin-off.
The spin-off cycle determines the thickness of the resist coating. The thickness is primarily a function of the spin-off speed and the spin-off time, both following an inverse power-law (y=k*x^-a). The acceleration to the spin-off speed also influences the thickness, but the effect is dependent on previous steps. The spin-off is usually a simple spin at one speed, but it may be comprised of several steps at different spin speeds. After spin-off, the wafer is decelerated.
During spin coating, resist builds up at the edge of the wafer due to the change in surface tension at the edge. This phenomenon is called an edge-bead. Dependent on spin coating parameters, the coating may be several times thicker at the edge than in the central area. In a subsequent hard contact exposure step, this edge-bead induces an undesired proximity gap which reduces the lateral resolution, and may even cause the wafer to stick to the mask. In an edge-bead removal step, solvent administered through a nozzle positioned at the edge of the wafer while spinning at low or medium spin speed dissolves the resist and washes it away. After the removal, a short spin at medium spin speed dries the wafer before the soft bake. Dependent on the viscosity (solvent content) of the resist at the point of edge-bead removal, this drying spin may cause the resist to re-flow and create a secondary edge-bead. In some cases, it may be necessary to (partially) soft bake the resist before edge-bead removal.
Dependent on the spin speeds used in the various steps of the spin coating, resist may creep over the edge of the wafer and onto the backside. Also, some resists tend to leave fine strings of resist protruding from the edge of the wafer, or folded onto the backside, an effect sometimes referred to as "cotton candy". This resist will contaminate the soft bake hotplate, and thus subsequent wafers with resist. In a backside rinse step, solvent administered through a nozzle to the backside of the wafer while spinning at low or medium spin speed dissolves the resist and washes it away. After the rinse, a short spin at medium spin speed dries the wafer before the soft bake. During the backside rinse solvent inevitably creeps onto the front side of the wafer. This effect may be used to dissolve and subsequently remove an edge-bead, but it may also leave the rim of the wafer exposed. As an alternative to backside rinse, a wafer which is left dirty on the backside by the spin coat process may be soft baked in proximity in order to protect the hotplate from contamination. This leaves front side coating intact, but also leaves the backside dirty.
Soft baking
After spin coating the solvent in the resist formulation must be evaporated in a baking step in order to solidify the resist. This soft bake can be carried out as a contact bake or a proximity bake. In a contact bake, the wafer is held in close contact to the hotplate surface by vacuum during the bake. In a proximity bake, the wafer is first moved into close proximity, e.g. 1mm, of the hotplate surface, then held there for the duration of the bake. The hotplate temperatures of the baking modules of Spin Track 1 and 2 are fixed at temperatures relevant to the resist used, i.e. 90°C and 110°C, respectively. After baking, the wafer is cooled for 5 seconds on the coolplate.
Standard Processes
HMDS priming
The standard HMDS priming process has been developed to mimic the behavior of the IMTEC Star2000 HMDS oven. It produces a contact angle of 81-82° on an oxidized silicon surface. General information on HMDS priming can be found here.
Flow names, process parameters, and test results:
- HMDS Standard
Process parameters: 10s contact bake, 30s vacuum bake, 72s HMDS priming, 5s cooling.
Test results:
Substrate | Contact angle | Test date | Tester initials | Comments |
---|---|---|---|---|
110 nm oxide | 82.0° | 7/5 2013 | taran | average of three measurements on one sample |
Si with native oxide | 73.3° | 7/5 2013 | taran | average of nine measurements (three measurements on three different samples) |
Borofloat (glass) | 65.6° | 7/5 2013 | taran | average of three measurements on one sample |
- HMDS fast
Process parameters: 10s contact bake, 30s vacuum bake, 72s HMDS priming, 5s cooling.
Test results:
Substrate | Contact angle | Test date | Tester initials | Comments |
---|---|---|---|---|
110 nm oxide | 82.0° | 7/5 2013 | taran | average of three measurements on one sample |
Si with native oxide | 73.3° | 7/5 2013 | taran | average of nine measurements (three measurements on three different samples) |
Borofloat (glass) | 65.6° | 7/5 2013 | taran | average of three measurements on one sample |
AZ MiR 701 (29cps) coating
Spin coating of standard thicknesses (1.3 - 2.5 µm) of AZ MiR 701 (29cps) on Spin Coater: Gamma UV is divided into two or three steps: HMDS priming (optional), spin coating, and soft baking. The HMDS priming is equal to the HMDS fast process. Spin coating uses dynamic dispense of resist at 800 rpm, using a volume of 3 ml for 100mm substrates. The dispense is followed by spin-off at a thickness dependent spin speed for 30 seconds. The wafer is decelerated at 1000 rpm/s before stopping. Soft baking is done at 90°C for 60s. As MiR 701 has a tendency to produce "cotton candy" on the edges, soft baking is performed in 1 mm proximity.
Flow names, process parameters, and test results:
- (1410) DCH 100mm MiR 701 1.5um
- (1411) DCH 100mm MiR 701 1.5um HMDS
- (1610) DCH 150mm MiR 701 1.5um
- (1611) DCH 150mm MiR 701 1.5um HMDS
Spin-off: 4600 rpm.
Substrate | Thickness | Uniformity (+/-) | Test date | Tester initials | Comments |
---|---|---|---|---|---|
Silicon with native oxide | 1.513 | 0.6% | 26/3 2015 | taran | 4" wafer, no HMDS. 9 points on one wafer, exclusion zone 5mm |
- (1420) DCH 100mm MiR 701 2um
- (1421) DCH 100mm MiR 701 2um HMDS
- (1620) DCH 150mm MiR 701 2um
- (1621) DCH 150mm MiR 701 2um HMDS
Spin-off: 2600 rpm.
Substrate | Thickness | Uniformity (+/-) | Test date | Tester initials | Comments |
---|---|---|---|---|---|
Silicon with native oxide | 2.019 µm | 1.5% | 26/3 2015 | taran | 4" wafer, no HMDS. 9 points on one wafer, exclusion zone 5mm |
Spin coating of standard thicknesses (1.3 - 2.5 µm) of AZ MiR 701 (29cps) on Spin Coater: Gamma UV is divided into two or three steps: HMDS priming (optional), spin coating, and soft baking. The HMDS priming is equal to the HMDS fast process. Spin coating uses dynamic dispense of resist at 800 rpm, using a volume of 3 ml for 100mm substrates. The dispense is followed by spin-off at a thickness dependent spin speed for 30 seconds. The wafer is decelerated at 1000 rpm/s before stopping. Soft baking is done at 90°C for 60s. As MiR 701 has a tendency to produce "cotton candy" on the edges, soft baking is performed in 1 mm proximity.
Flow names, process parameters, and test results:
- (1440) DCH 100mm MiR 701 4um
- (1441) DCH 100mm MiR 701 4um HMDS
- (1640) DCH 150mm MiR 701 4um
- (1641) DCH 150mm MiR 701 4um HMDS
Waiting: 75s @ 600 rpm. Spin-off: 10s @ 3000 rpm.
Substrate | Thickness | Uniformity (+/-) | Test date | Tester initials | Comments |
---|---|---|---|---|---|
Silicon with native oxide | 3.992 µm | 0.7% | 26/3 2015 | taran | 4" wafer, no HMDS. 9 points on one wafer, exclusion zone 5mm |
AZ nLOF 2020 coating
Spin coating of AZ nLOF 2020 on Spin Track 2 is divided into two or three steps: HMDS priming (optional), spin coating, and soft baking. At the moment, the HMDS priming is equal to the standard priming, but this may be subject to change as our process knowledge grows. Spin coating uses dynamic dispence of 4 ml resist at 1000 rpm, followed by spin-of at a thickness dependent spin speed for a thickness dependent time. The wafer is deaccelerated at 1000 rpm/s for 5 seconds before stopping. Soft baking is done at 110°C for 60s, normally as a contact bake. In order to enable double-sided coating of nLOF, recipes have been created witch use a 1mm proximity bake for the softbake (prox SB).
Flow names, process parameters, and test results:
- T2 nLOF 2020 1,5um no HMDS
- T2 nLOF 2020 1,5um prox SB no HMDS
- T2 nLOF 2020 1,5um with HMDS
Spin-of: 30 s at 6700 rpm.
Substrate | Thickness | Uniformity (+/-) | Test date | Tester initials | Comments |
---|---|---|---|---|---|
Silicon with native oxide | 1.483 | 0.48% | 5/9 2013 | taran | with HMDS. Average of 3 wafers |
- T2 nLOF 2020 2um no HMDS
- T2 nLOF 2020 2um prox SB no HMDS
- T2 nLOF 2020 2um with HMDS
Spin-of: 30 s at 3800 rpm.
Substrate | Thickness | Uniformity (+/-) | Test date | Tester initials | Comments |
---|---|---|---|---|---|
Silicon with native oxide | 1.947 | 0.56% | 5/9 2013 | taran | with HMDS. Average of 3 wafers |
Silicon with native oxide | 1.910 | 0.4% | 17/02 2015 | chasil | with HMDS. Average of 3 wafers |
Silicon with native oxide | 1.868 | 0.5% | 1/04 2015 | chasil | with HMDS. Average of 3 wafers |
- T2 nLOF 2020 3um no HMDS
- T2 nLOF 2020 3um prox SB no HMDS
- T2 nLOF 2020 3um with HMDS
Spin-of: 30 s at 1700 rpm.
Substrate | Thickness | Uniformity (+/-) | Test date | Tester initials | Comments |
---|---|---|---|---|---|
Silicon with native oxide | 2.948 | 0.62% | 5/9 2013 | taran | with HMDS. Average of 3 wafers |
AZ 5214E coating
Spin coating of AZ nLOF 2020 on Spin Track 2 is divided into two or three steps: HMDS priming (optional), spin coating, and soft baking. At the moment, the HMDS priming is equal to the standard priming, but this may be subject to change as our process knowledge grows. Spin coating uses dynamic dispence of 4 ml resist at 1000 rpm, followed by spin-of at a thickness dependent spin speed for a thickness dependent time. The wafer is deaccelerated at 1000 rpm/s for 5 seconds before stopping. Soft baking is done at 110°C for 60s, normally as a contact bake. In order to enable double-sided coating of nLOF, recipes have been created witch use a 1mm proximity bake for the softbake (prox SB).
Flow names, process parameters, and test results:
- T2 nLOF 2020 1,5um no HMDS
- T2 nLOF 2020 1,5um prox SB no HMDS
- T2 nLOF 2020 1,5um with HMDS
Spin-of: 30 s at 6700 rpm.
Substrate | Thickness | Uniformity (+/-) | Test date | Tester initials | Comments |
---|---|---|---|---|---|
Silicon with native oxide | 1.483 | 0.48% | 5/9 2013 | taran | with HMDS. Average of 3 wafers |
- T2 nLOF 2020 2um no HMDS
- T2 nLOF 2020 2um prox SB no HMDS
- T2 nLOF 2020 2um with HMDS
Spin-of: 30 s at 3800 rpm.
Substrate | Thickness | Uniformity (+/-) | Test date | Tester initials | Comments |
---|---|---|---|---|---|
Silicon with native oxide | 1.947 | 0.56% | 5/9 2013 | taran | with HMDS. Average of 3 wafers |
Silicon with native oxide | 1.910 | 0.4% | 17/02 2015 | chasil | with HMDS. Average of 3 wafers |
Silicon with native oxide | 1.868 | 0.5% | 1/04 2015 | chasil | with HMDS. Average of 3 wafers |
- T2 nLOF 2020 3um no HMDS
- T2 nLOF 2020 3um prox SB no HMDS
- T2 nLOF 2020 3um with HMDS
Spin-of: 30 s at 1700 rpm.
Substrate | Thickness | Uniformity (+/-) | Test date | Tester initials | Comments |
---|---|---|---|---|---|
Silicon with native oxide | 2.948 | 0.62% | 5/9 2013 | taran | with HMDS. Average of 3 wafers |