Specific Process Knowledge/Direct Structure Definition: Difference between revisions
No edit summary |
|||
Line 19: | Line 19: | ||
== Choose method of structuring/equipment == | == Choose method of structuring/equipment == | ||
*[[Specific Process Knowledge/ | ** [[Specific Process Knowledge/Lithography/3DLithography|2-Photon Polymerization Lithography]] | ||
*[[Specific Process Knowledge/ | ** [[Specific Process Knowledge/Back-end processing/Polymer Injection Molder|Polymer Injection Molder]] | ||
*[[Specific Process Knowledge/ | ** [[Specific Process Knowledge/Lithography/NanoImprintLithography|Nano Imprint Lithography]] | ||
*[[Specific Process Knowledge/Back-end processing/ | ** [[Specific Process Knowledge/Back-end processing/Laser Micromachining Tool|Laser Micromachining Tool/ablation]] | ||
** Dicing saw | |||
== Materials for structuring == | == Materials for structuring == | ||
Line 30: | Line 31: | ||
** Topas | ** Topas | ||
*** [[Specific Process Knowledge/Back-end processing/Polymer Injection Molder|Polymer Injection Molder]] | *** [[Specific Process Knowledge/Back-end processing/Polymer Injection Molder|Polymer Injection Molder]] | ||
*** | *** [[Specific Process Knowledge/Lithography/NanoImprintLithography|Nano Imprint Lithography]] | ||
*** [[Specific Process Knowledge/Back-end processing/Laser Micromachining Tool|Laser ablation]] | |||
** PMMA | ** PMMA | ||
*** | *** [[Specific Process Knowledge/Lithography/NanoImprintLithography|Nano Imprint Lithography]] | ||
*** [[Specific Process Knowledge/Back-end processing/Laser Micromachining Tool|Laser ablation]] | |||
** AZ resists | ** AZ resists | ||
*** [[Specific Process Knowledge/Lithography/3DLithography|2-Photon Polymerization Lithography]] | *** [[Specific Process Knowledge/Lithography/3DLithography|2-Photon Polymerization Lithography]] | ||
** ... | ** ... | ||
*Metals | *Metals/Silicon/Graphene | ||
**[[Specific Process Knowledge/Back-end processing/Laser Micromachining Tool|Laser ablation]] | **[[Specific Process Knowledge/Back-end processing/Laser Micromachining Tool|Laser ablation]] | ||
*Glass | *Glass | ||
Line 44: | Line 45: | ||
** dicing saw | ** dicing saw | ||
**[[/Sandblasting|Sandblasting (at DTU Nanotech).]] | **[[/Sandblasting|Sandblasting (at DTU Nanotech).]] | ||
== Comparison of equipment/material == | == Comparison of equipment/material == |
Revision as of 13:48, 6 October 2014
Feedback to this page: click here
Direct Structure Definiton
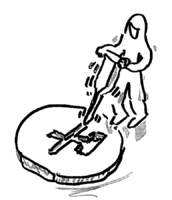
By direct structure definition we mean that you form the structures for you device directly in the material that the device consist of without any masking steps.
Advantages of direct structure definition may be ..
- Quicker process because no need for masking steps
- In some cases the structure is defined directly by a computer, so changes in the design can be made very quickly.
Dis-advantages could be
- Limited choice of materials
- Limited resolution
lakdfjasdfien dfjnsdk djfhk ueuhnndkjnf kjdhf jn uafhisf
Choose method of structuring/equipment
Materials for structuring
- Polymers
- Metals/Silicon/Graphene
- Glass
- Laser ablation
- dicing saw
- Sandblasting (at DTU Nanotech).
Comparison of equipment/material
Polymers | Nano Imprint Lithography | 2-Photon Polymerization Lithography | Polymer Injection Molder | Laser Micromachining Tool |
---|---|---|---|---|
Generel description | Low Pressure Chemical Vapour Deposition (LPCVD furnace process) | Plasma Enhanced Chemical Vapour Deposition (PECVD process) | Reactive sputtering | |
Allowed materials |
Processed wafers have to be RCA cleaned |
|
Any |
Metals/Silicon/Glass | Nano Imprint Lithography | 2-Photon Polymerization Lithography | Polymer Injection Molder | Laser Micromachining Tool |
---|---|---|---|---|
Generel description | Low Pressure Chemical Vapour Deposition (LPCVD furnace process) | Plasma Enhanced Chemical Vapour Deposition (PECVD process) | Reactive sputtering | |
Allowed materials |
Processed wafers have to be RCA cleaned |
|
Any |