Specific Process Knowledge/Lithography/mrEBL6000: Difference between revisions
No edit summary |
No edit summary |
||
Line 32: | Line 32: | ||
== Process Flow == | |||
Test of Chemically Semi-Amplified Resist (CSAR); a positive e-beam resist from AllResist (AR-P 6200-2). | |||
{|border="1" cellspacing="0" cellpadding="3" style="text-align:left;" style="width: 60%;" | |||
|- | |||
|- | |||
|-style="background:Black; color:White" | |||
!Equipment | |||
!Process Parameters | |||
!Comments | |||
|- | |||
|- | |||
|-style="background:WhiteSmoke; color:black; text-align:center" | |||
!colspan="4"|Pretreatment | |||
|- | |||
|- | |||
|-style="background:LightGrey; color:black" | |||
|4" Si wafers | |||
|No Pretreatment | |||
| | |||
|- | |||
|- | |||
|-style="background:WhiteSmoke; color:black; text-align:center" | |||
!colspan="4"|Spin Coat | |||
|- | |||
|- | |||
|-style="background:LightGrey; color:black" | |||
|Spin Coater Manual, LabSpin, A-5 | |||
|AR-P 6200/2 AllResist E-beam resist | |||
60 sec at various spin speed. | |||
Acceleration 4000 s-2, | |||
softbake 1 - 5 min at 150 deg Celcius | |||
|Disposal pipette used; clean by N2-gun before use. Use approximately 1.5 ml per 4" wafer, never use a pipette twice. Softbake is not a crucial step, see e-mail correspondence with AllResist [[media:Softbake CSAR.pdf|here]]. | |||
|- | |||
|- | |||
|-style="background:WhiteSmoke; color:black; text-align:center" | |||
!colspan="4"|Characterization | |||
|- | |||
|- | |||
|-style="background:LightGrey; color:black" | |||
|Ellipsometer VASE B-1 | |||
|9 points measured on 100 mm wafer | |||
|ZEP program used; measured at 70 deg only | |||
|- | |||
|- | |||
|-style="background:WhiteSmoke; color:black; text-align:center" | |||
!colspan="4"|E-beam Exposure | |||
|- | |||
|- | |||
|-style="background:LightGrey; color:black" | |||
|JEOL 9500 E-beam writer, E-1 | |||
|Dosepattern 15nm - 100nm, | |||
dose 120-280 muC/cm2 | |||
|Virtual chip mark height detection (CHIPAL V1) used in corner of every dose array | |||
|- | |||
|- | |||
|-style="background:WhiteSmoke; color:black; text-align:center" | |||
!colspan="4"|Development | |||
|- | |||
|- | |||
|-style="background:LightGrey; color:black" | |||
|Fumehood, D-3 | |||
|60 sec in X AR 600-54/6, | |||
60 sec rinse in IPA, | |||
N2 Blow dry | |||
|Gentle agitation while developing. After developing, wafer is immersed in beaker with IPA, subsequently blow dried with N2 gun. | |||
|- | |||
|- | |||
|-style="background:WhiteSmoke; color:black; text-align:center" | |||
!colspan="4"|Characterization | |||
|- | |||
|- | |||
|-style="background:LightGrey; color:black" | |||
|Zeiss SEM Supra 60VP, D-3 | |||
|2-3 kV, shortest working distance possible, chip mounted with Al tape | |||
|The wafers are diced into smaller pieces and sputter coated with Pt at DTU CEN before SEM inspection; please contact [mailto:ramona.mateiu@cen.dtu.dk Ramona Valentina Mateiu] for further information. | |||
|- | |||
|} | |||
== Spin Curve == | |||
[[File:SpinCurveMrEBL6000.jpg|right|600px]] | [[File:SpinCurveMrEBL6000.jpg|right|600px]] | ||
Revision as of 12:47, 14 July 2014
Resist | Polarity | Manufacturer | Comments | Technical reports | Spinner | Developer | Rinse | Remover | Process flows (in docx-format) |
mr EBL 6000 | Positive | MicroResist | Standard negative resist | mrEBL6000 processing Guidelines.pdf | Manual Spinner 1 (Laurell), Spin Coater Labspin | mr DEV | IPA | Process_Flow_mrEBL6000.docx |
Process Flow
Test of Chemically Semi-Amplified Resist (CSAR); a positive e-beam resist from AllResist (AR-P 6200-2).
Equipment | Process Parameters | Comments | |
---|---|---|---|
Pretreatment | |||
4" Si wafers | No Pretreatment | ||
Spin Coat | |||
Spin Coater Manual, LabSpin, A-5 | AR-P 6200/2 AllResist E-beam resist
60 sec at various spin speed. Acceleration 4000 s-2, softbake 1 - 5 min at 150 deg Celcius |
Disposal pipette used; clean by N2-gun before use. Use approximately 1.5 ml per 4" wafer, never use a pipette twice. Softbake is not a crucial step, see e-mail correspondence with AllResist here. | |
Characterization | |||
Ellipsometer VASE B-1 | 9 points measured on 100 mm wafer | ZEP program used; measured at 70 deg only | |
E-beam Exposure | |||
JEOL 9500 E-beam writer, E-1 | Dosepattern 15nm - 100nm,
dose 120-280 muC/cm2 |
Virtual chip mark height detection (CHIPAL V1) used in corner of every dose array | |
Development | |||
Fumehood, D-3 | 60 sec in X AR 600-54/6,
60 sec rinse in IPA, N2 Blow dry |
Gentle agitation while developing. After developing, wafer is immersed in beaker with IPA, subsequently blow dried with N2 gun. | |
Characterization | |||
Zeiss SEM Supra 60VP, D-3 | 2-3 kV, shortest working distance possible, chip mounted with Al tape | The wafers are diced into smaller pieces and sputter coated with Pt at DTU CEN before SEM inspection; please contact Ramona Valentina Mateiu for further information. |
Spin Curve
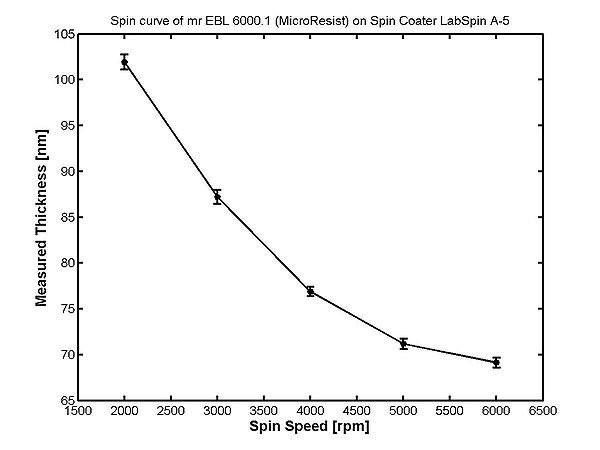
The thickness is measured on VASE Ellipsometer using a simple Cauchy model for a transparent polymer on Si. The measurements are performed at one incidence angle (70 degrees) only. 9 points on each 4" wafer has been measured; the standard deviation thus representing the homogeinity of the film on the 4" wafers.
MicroResist mr EBL 6000 spinning on Spin Coater: Manual LabSpin A-5, TIGRE, 14-07-2014. Softbake 3 min @ 110 degC. | ||||||
---|---|---|---|---|---|---|
Spin Speed [rpm] | Acceleration [1/s2] | Thickness [nm] | St Dev | |||
2000 | 2000 | |||||
3000 | 2000 | |||||
4000 | 2000 | |||||
5000 | 2000 | |||||
6000 | 2000 |