Specific Process Knowledge/Etch/KOH Etch: Difference between revisions
Line 4: | Line 4: | ||
At Danchip we use as a standard a 28 wt% KOH. | At Danchip we use as a standard a 28 wt% KOH. | ||
Wet etching of aluminium is done with two different solutions: | |||
# H<math>_2</math>O:H<math>_3</math>PO<math>_4</math> 1:2 at 50 <sup>o</sup>C | |||
# Pre-mixed etch solution: PES 77-19-04 at 20 <sup>o</sup>C | |||
Both solutions are used in the Aluminium etch bath shown to the right. I must be written on which one is in. Solution no. 1 is the most used solution for etchning oure aluminium. Solution no. 2 is primarily for etching aluminium mixed with a small percentage of silicon. | |||
<br clear="all" /> | |||
===Comparing the two solutions=== | |||
{| border="1" cellspacing="0" cellpadding="4" align="left" | |||
! | |||
! Aluminium Etch 1 | |||
! Aluminium Etch 2 | |||
|- | |||
|General description | |||
| | |||
Etch of pure aluminium | |||
| | |||
Etch of aluminium + 1.5% Si | |||
|- | |||
|Chemical solution | |||
|H<math>_2</math>O:H<math>_3</math>PO<math>_4</math> 1:2 | |||
|PES 77-19-04 | |||
|- | |||
|Process temperature | |||
|50 <sup>o</sup>C | |||
|20 <sup>o</sup>C | |||
|- | |||
|Possible masking materials: | |||
| | |||
Photoresist (1.5 µm AZ5214E) | |||
| | |||
Photoresist (1.5 µm AZ5214E) | |||
|- | |||
|Etch rate | |||
| | |||
~100 nm/min (Pure Al) | |||
| | |||
~60(??) nm/min | |||
|- | |||
|Batch size | |||
| | |||
1-25 wafers at a time | |||
| | |||
1-25 wafer at a time | |||
|- | |||
|Size of substrate | |||
| | |||
4" wafers | |||
| | |||
4" wafers | |||
|- | |||
|Allowed materials | |||
| | |||
*Aluminium | |||
*Silicon | |||
*Silicon Oxide | |||
*Silicon Nitride | |||
*Silicon Oxynitride | |||
*Photoresist | |||
*E-beam resist | |||
| | |||
*Aluminium | |||
*Silicon | |||
*Silicon Oxide | |||
*Silicon Nitride | |||
*Silicon Oxynitride | |||
*Photoresist | |||
*E-beam resist | |||
|- | |||
|} |
Revision as of 11:33, 28 January 2008
KOH etch - Anisotropic silicon etch
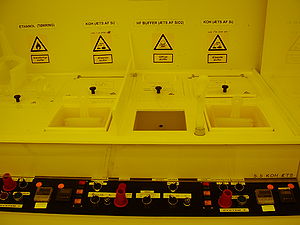
KOH belongs to the family of anisotropic Si-etchants based on aqueous alkaline solutions. The anisotropy stems from the different etch rates in different crystal directions. The {111}-planes are almost inert whereas the etch rates of e.g. {100}- and {110}-planes are several orders of magnitude faster.
At Danchip we use as a standard a 28 wt% KOH.
Wet etching of aluminium is done with two different solutions:
- HO:HPO 1:2 at 50 oC
- Pre-mixed etch solution: PES 77-19-04 at 20 oC
Both solutions are used in the Aluminium etch bath shown to the right. I must be written on which one is in. Solution no. 1 is the most used solution for etchning oure aluminium. Solution no. 2 is primarily for etching aluminium mixed with a small percentage of silicon.
Comparing the two solutions
Aluminium Etch 1 | Aluminium Etch 2 | |
---|---|---|
General description |
Etch of pure aluminium |
Etch of aluminium + 1.5% Si |
Chemical solution | HO:HPO 1:2 | PES 77-19-04 |
Process temperature | 50 oC | 20 oC |
Possible masking materials: |
Photoresist (1.5 µm AZ5214E) |
Photoresist (1.5 µm AZ5214E) |
Etch rate |
~100 nm/min (Pure Al) |
~60(??) nm/min |
Batch size |
1-25 wafers at a time |
1-25 wafer at a time |
Size of substrate |
4" wafers |
4" wafers |
Allowed materials |
|
|