Specific Process Knowledge/Etch/DRIE-Pegasus/FAQ/Bonding: Difference between revisions
New page: ; Question 1 : A user tried to etch through a wafer using a carrier and crystalbond as medium (see image below). Even though he ran the standard SPTS process (with 14 % etch load) at 0 deg... |
No edit summary |
||
Line 1: | Line 1: | ||
'''Feedback to this page: | |||
[mailto:plasma@danchip.dtu.dk?Subject=Feed%20back%20from%20page%20http://labadviser.danchip.dtu.dk/index.php/Specific_Process_Knowledge/Etch/DRIE-Pegasus/FAQ/Bonding click here]''' | |||
; Question 1 | ; Question 1 | ||
: A user tried to etch through a wafer using a carrier and crystalbond as medium (see image below). Even though he ran the standard SPTS process (with 14 % etch load) at 0 degrees, the wafer slid off the carrier. The crystalbond used melts at 65 degrees, is there any type with higher melting point? | : A user tried to etch through a wafer using a carrier and crystalbond as medium (see image below). Even though he ran the standard SPTS process (with 14 % etch load) at 0 degrees, the wafer slid off the carrier. The crystalbond used melts at 65 degrees, is there any type with higher melting point? |
Revision as of 11:07, 22 October 2013
Feedback to this page: click here
- Question 1
- A user tried to etch through a wafer using a carrier and crystalbond as medium (see image below). Even though he ran the standard SPTS process (with 14 % etch load) at 0 degrees, the wafer slid off the carrier. The crystalbond used melts at 65 degrees, is there any type with higher melting point?
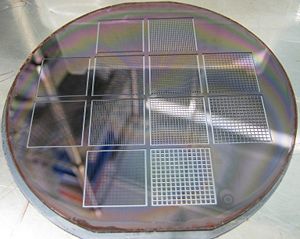
- Answer 1
- We usually use Crystalbond 555 or 555HMP, they have flow temps of ~55°C and 65°C respectively. Wafer temp during process can be in the range 77-80°C depending on etch rate, open area etc. but for most cases, the wax reflowing during process is not an issue as it is only a wafer piece which is bonded. Even if the wax reflows, I would expect any major slippage unless the chuck was very much off-level (VERY unlikely) or there was trapped air under the whole wafer which would result in the wafer lifting under vacuum; if the wax then reflows, there could be slippage as the wafer settles back down. I usually perform a check when the wafer is under vacuum in the loadlock; if it looks lifted, I remove it, back to the hotplate to reposition and try to work the trapped air out.
Source: Kerry Roberts, SPTS